Biocarbonfasern ziehen gleich
Ein neues Ultrahochtemperatur-Verfahren macht die Hightech-Fasern aus nachwachsenden Rohstoffen zu einer echten Alternative zu ihrem Erdölpendant.
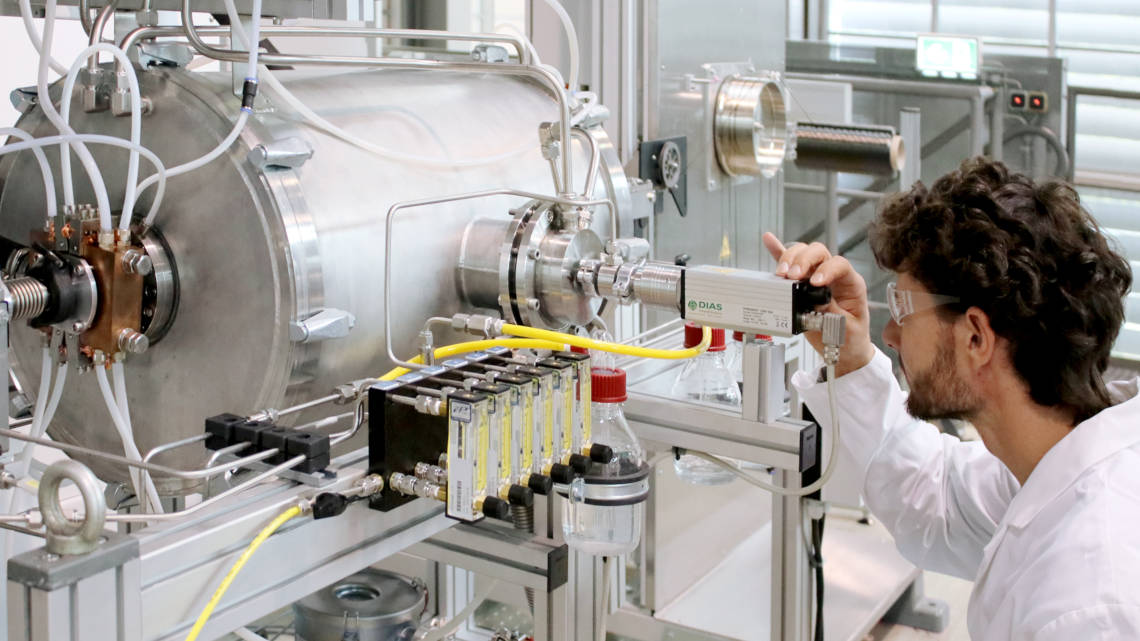
Jetzt werden sie konkurrenzfähig: Schon länger ist es möglich, den wichtigen Hightech-Werkstoff Carbonfaser auch aus nachwachsenden Rohstoffen anstelle von Erdöl zu erzeugen. Doch die mechanischen Eigenschaften waren bislang dem Erdölpendant unterlegen. Dank eines Ultrahochtemperaturofens dürfte sich das nun ändern, wie Faserspezialisten des Potsdamer Fraunhofer-Instituts für Angewandte Polymerforschung (IAP) jetzt berichten. Auf der Kunststoffmesse K in Düsseldorf wollen die Forscher vom 16. bis 23. Oktober 2019 erste Produkte und Vorstufen vorstellen.
Bislang unzulängliche Steifigkeit und Festigkeit
„Die Herstellung von Carbonfasern aus Präkursoren, die auf nachwachsenden Rohstoffen wie Cellulose, Lignin oder Hemicellulose basieren, war bisher zwar prinzipiell möglich, jedoch sind bei den üblichen Pyrolysetemperaturen von bis zu 1600 °C die mechanischen Eigenschaften Steifigkeit und Festigkeit sehr beschränkt“, erläutert Jens Erdmann vom IAP das Problem. Die sogenannten Präkursoren sind als Zwischenprodukt unumgänglich, da sich aus reinem Kohlenstoff nicht direkt Fasern herstellen lassen.
Ultrahochtemperaturofen verbessert die Faserstruktur
Chemisch erklärt sich die bisherige Unterlegenheit der Biocarbonfasern durch einen geringen Anteil geordneter Kohlenstoffstrukturen in der Carbonfaser und der nicht der Faserrichtung entsprechenden Orientierung vieler Kohlenstoffstrukturen. Für diese beiden Probleme haben die Fraunhofer-Forscher nun eine Lösung entwickelt, schildert Erdmann: „Dafür haben wir einen speziellen Ultrahochtemperaturofen anfertigen lassen, in dem die biobasierten Carbonfasern zusätzlich für wenige Sekunden bei Temperaturen zwischen 2.700 und 2.900 °C thermisch nachbehandelt werden. In diesem Temperaturbereich lassen sich die Kohlenstoffstrukturen in der Faser durch Verstrecken so anordnen, dass sie in Richtung der Faserachse orientiert sind.“ Das mache die Fasern deutlich fester und steifer und sie erhielten mechanische Eigenschaften, die das Niveau erdölbasierter Carbonfasern erreichen. „Wir erhalten sogenannte High-Modulus-Fasern“, resümiert Erdmann.
Kooperationspartner gesucht
Mit dem Ultrahochtemperaturofen eröffnen sich für das Fraunhofer IAP und dessen Kooperationspartner viele Möglichkeiten, um leichte und stabile Materialien zu entwickeln. „Der Ofen ist ideal, um mit wenig Fasermaterial innerhalb kurzer Zeit viele Variationen von Parametern zu testen“, wirbt Erdmann um weitere Industriepartner. So werden Carbonfasern im Leichtbau von Fahrzeugen und Flugzeugen genutzt, sie dienen als Carbonbeton dem Bau und der Sanierung von Brücken und sie bringen als Werkstoffe für Windkraftanlagen und Wasserstofftanks die Energiewende voran.
bl