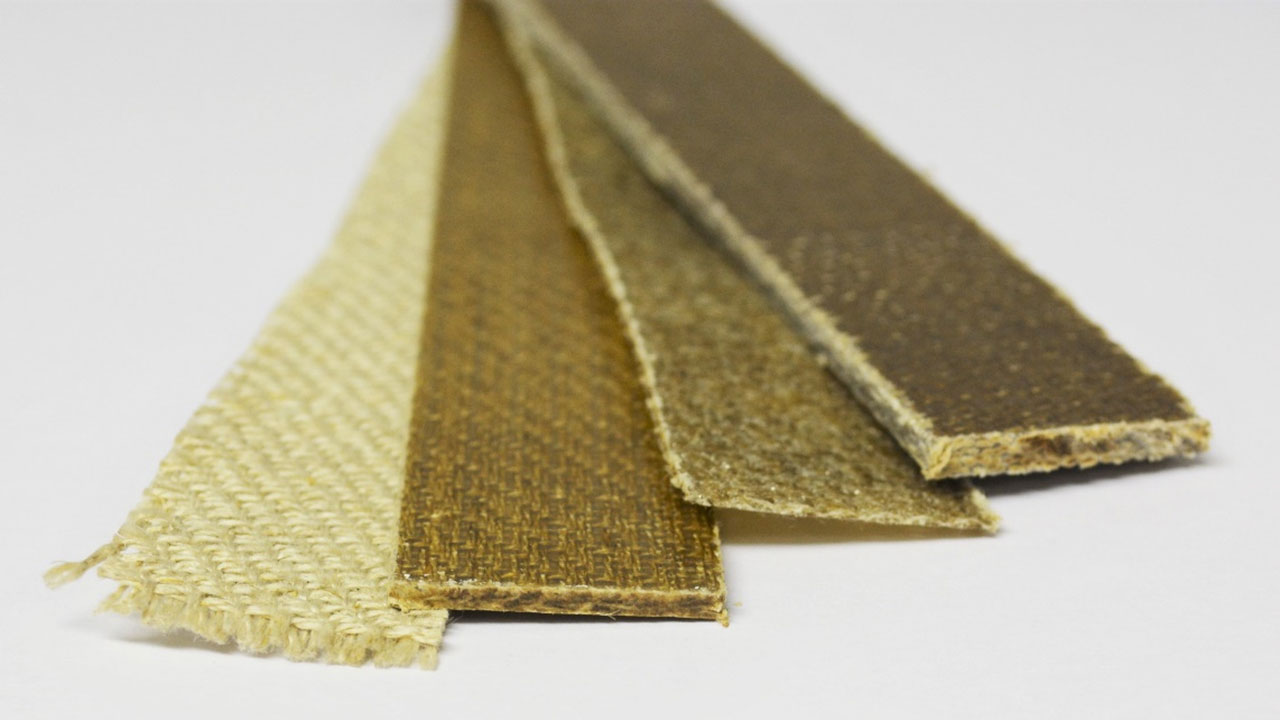
Die Kunststoffindustrie ist im Wandel: Die mittelfristige Abkehr vom Erdöl als Rohstoff und die Zuwendung hin zu biobasierten Rohstoffen verlangt, neue Prozesse und Materialien zu erforschen, verspricht aber auch Potenziale für neuartige Anwendungen. Eine dieser Herausforderungen, die es zu meistern gilt, betrifft technische Thermoplaste: Deren Schmelztemperatur in der Heißpresse liegt häufig oberhalb von 200° C. Das machte es bisher kaum möglich, darin Naturfasern zu verarbeiten, da diese meist bis maximal 200° C hitzebeständig sind. Das Forschungsprojekt „DeFiCoat“ hat dafür nun einen ersten Lösungsansatz entwickelt.
Leistungsfähig und biobasiert
Das Projekt-Akronym „DeFiCoat“ steht für „Development of specially coated fibers for manufacture of novel biocomposites from engineering thermoplastic“, also die Entwicklung speziell beschichteter Naturfasern zur Herstellung von neuartigen Bioverbundwerkstoffen aus technischen Thermoplasten. Gemeinsam mit der kanadischen Universität Guelph hat sich das Fraunhofer-Institut für Holzforschung, Wilhelm-Klauditz-Institut WKI, von November 2017 bis Dezember 2019 der Herausforderung gestellt, Naturfasern thermisch, mechanisch und hinsichtlich der Feuchtigkeitsaufnahme stabiler zu machen. Gefördert wurde das Forschungsteam dabei vom Bundesministerium für Bildung und Forschung über das Programm „Bioökonomie International 2016“ mit rund 500.000 Euro.
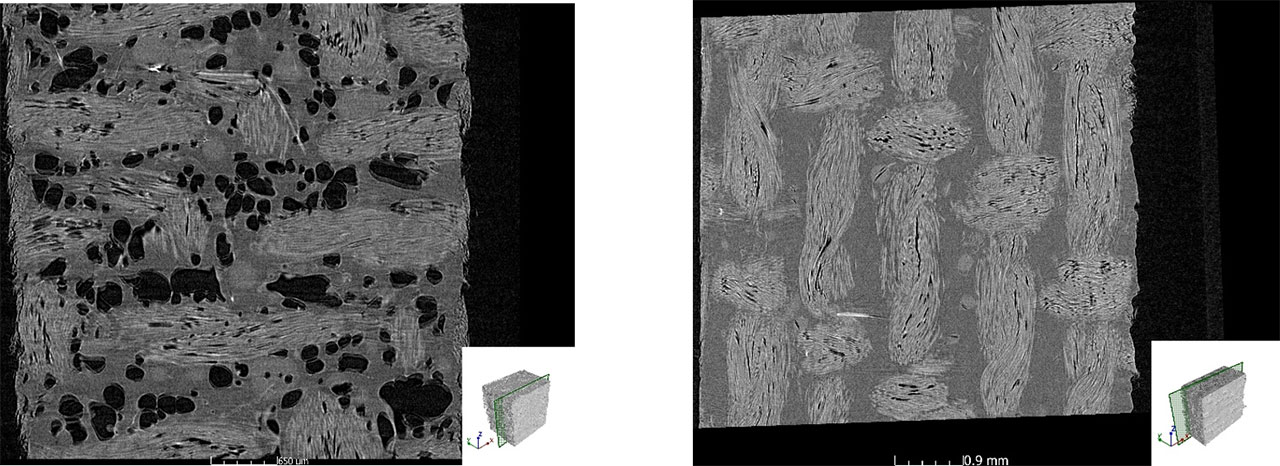
„Wie lassen sich Naturfasern thermisch überhaupt stabilisieren? Durch eine Beschichtung?“, das sei die erste Frage im Projekt gewesen, erinnert sich Natalie Vellguth vom Fraunhofer WKI. Die Material- und Nanochemikerin hatte die Projektleitung von Hans-Josef Endres übernommen, nachdem dieser vom Fraunhofer HOFZET an die Leibniz-Universität Hannover gewechselt war. Möglich wäre es alternativ, die Schmelztemperatur der Thermoplaste durch Zusätze abzusenken, doch das würde die Materialeigenschaften verschlechtern.
Flachs mit Harz beschichten
Erfahrungen mit Naturfasern habe es bereits mit Duromeren gegeben, die bei maximal 120° C aushärten und danach auch nicht mehr formbar sind, beispielsweise als Bioverbundwerkstoffe für Autotüren, berichtet Vellguth. Thermoplaste hingegen lassen sich innerhalb eines bestimmten Temperaturbereichs immer wieder aufs Neue verformen und sind daher für eine Vielzahl von Anwendungen und Branchen interessant.
Die Entscheidung fiel schließlich für den Ansatz, die Fasern mit einem duroplastischen Harz zu beschichten. Das schützt die Naturfasern temporär, wenn sie beim anschließenden Heißpressen in Thermoplaste eingebunden werden. Als Faserrohstoff wählte das Forschungsteam Flachs – wegen der guten mechanischen Eigenschaften und der guten Verfügbarkeit in Deutschland. „Im asiatischen Raum hätte man sicher andere Fasern gewählt“, sagt Vellguth. Auch Hanf oder Jute seien im Übrigen möglich, die Projektergebnisse aufgrund der unterschiedlichen Faserstrukturen aber nicht einfach übertragbar. Beim Harz lieferte ein teilbiobasiertes System die beste Materialflexibilität. Als Thermoplastkomponente wurde eine nicht biobasierte Polyamidmatrix eingesetzt.
Mehrere Härtersysteme erprobt
Um das Harz gut aufzutragen, testeten die Fachleute unterschiedliche Harz-Härtersysteme. Am besten bewährte sich außerdem das beidseitige Aufsprühen des Harzes, um ein flexibles und gut beschichtetes Material zu erhalten. Die ursprünglich geplante Beschichtung im Tauchverfahren scheiterte an der verspäteten Verfügbarkeit der entsprechenden Maschine. Doch auch so konnte die Projektleiterin erfreut feststellen: „Wir konnten deutlich höhere mechanische Kennwerte erzielen als ohne Beschichtung.“
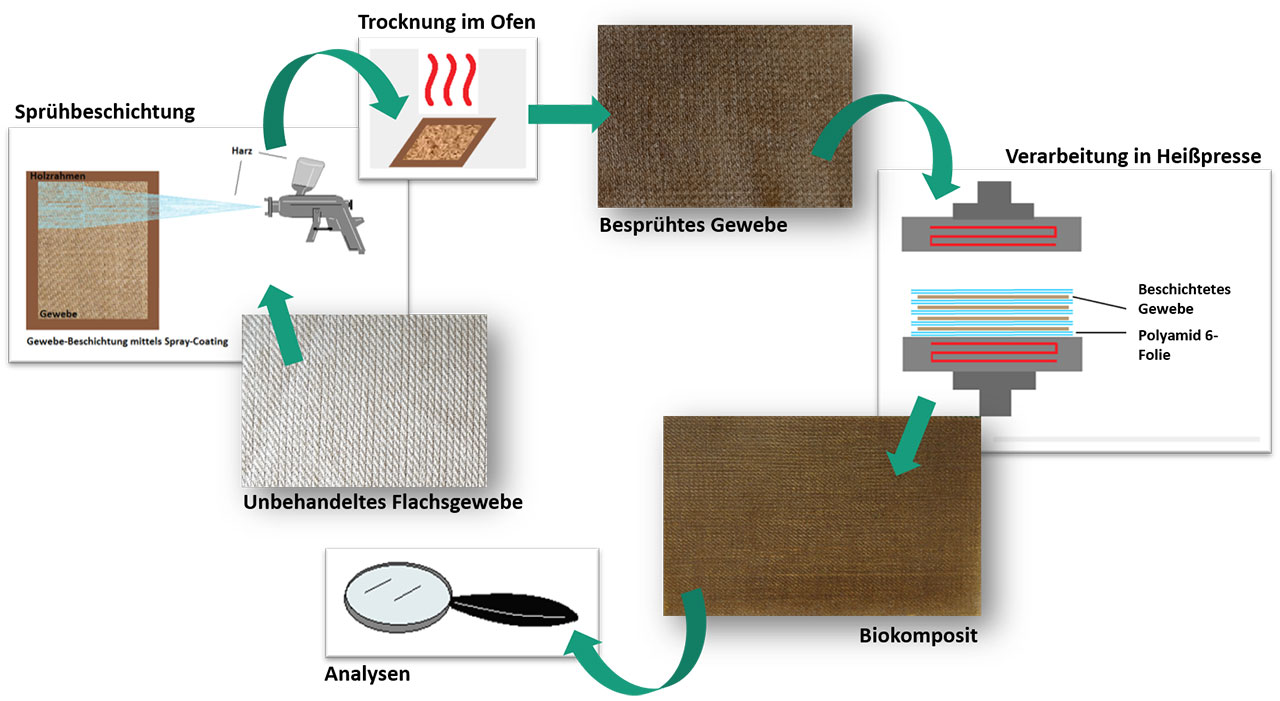
Im Projekt ging es vorrangig um eine Materialstudie, nicht darum, bestimmte Bauteile herzustellen. Daher erzeugten die Projektbeteiligten einfache Plattengeometrien, um zu testen, wie sich der Bioverbundwerkstoff aus harzbeschichteter Flachsfaser und Polyamid im Vergleich zu unbeschichteten Faserverbundwerkstoffen schlägt. Mittels Computertomografie und Rasterelektronenmikroskopie untersuchten die Fachleute die Homogenität von Struktur und Beschichtung und führten beschleunigte Alterungsversuche durch. Letztere führten dazu, dass das Harz nachhärtete und sich die mechanischen Kennwerte noch weiter erhöhten. „Verbundwerkstoffe mit keramischen Fasern und auch Glasfasern sind mit Flachs für Anwendungen mit weniger hohen mechanischen Anforderungen nachstellbar“, resümiert Vellguth zufrieden, der Bioverbundwerkstoff sei sogar besser zu verarbeiten, da zum Beispiel Glasfasern porös sind und leichter brechen.
In fünf Jahren reif für die Industrie?
„Die Meilensteine des Projekts haben wir gut erreicht“, resümiert Vellguth. Künftige Herausforderungen bestünden nun darin, einen Prozess für die kontinuierliche Beschichtung zu etablieren, wo bisher manuell gearbeitet wurde. Das erfordere unter anderem weitere Optimierungen des Harzsystems. Außerdem sollen die Materialkomponenten so verändert werden, dass ein einfacheres Recycling möglich wird – denn auch das ist ein wichtiger Nachhaltigkeitsfaktor. In vielleicht fünf Jahren könnte ein solcher Werkstoff dann bereit sein für den Einsatz im industriellen Maßstab.
Autor: Björn Lohmann