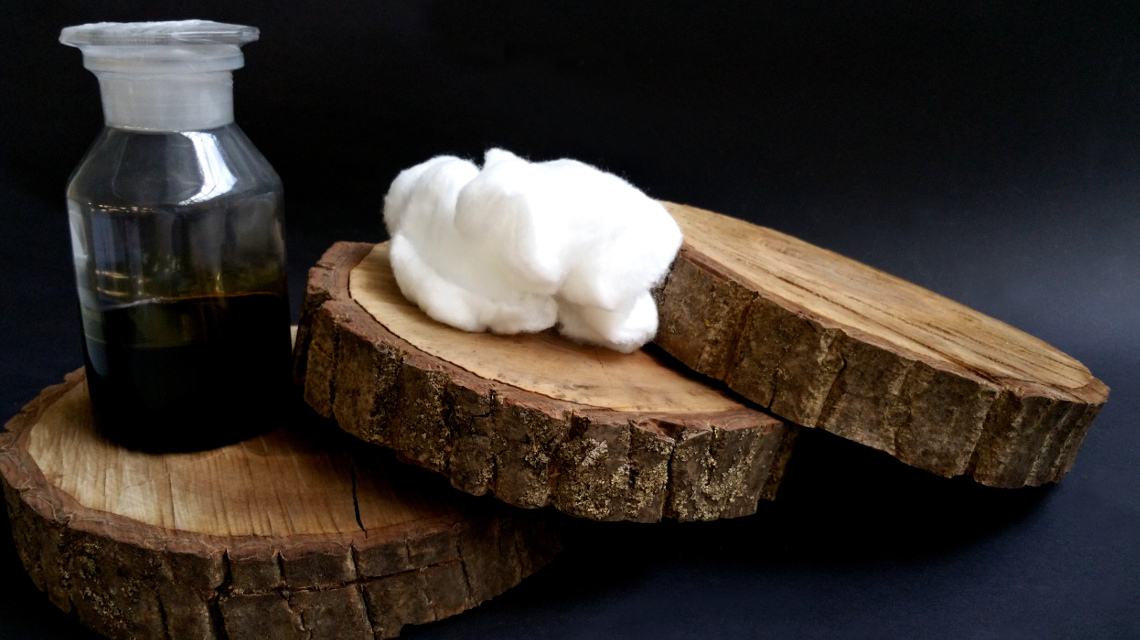
Ob in Schutzhelmen, Bremsbelägen oder der Autokarosserie: Duroplaste – also nach dem Aushärten nicht mehr verformbare Kunststoffe – sind besonders da gefragt, wo extreme Bedingungen herrschen. Sie basieren meist immer noch auf dem fossilen Rohstoff Erdöl. Im Verbundprojekt „BioDuroZell“ ist ein Konsortium um den Binger Naturstoffexperten Oliver Türk seit 2014 dabei, die Palette biogener Bindemittel für Duroplaste zu erweitern. Dabei muss berücksichtigt werden, dass die Rohstoffe für die neuen biobasierten Harze nicht für die Nahrungsmittelproduktion geeignet sind. Denn eine Konkurrenz will man künftig vermeiden. „Die früheren biobasierte Verbundwerkstoffe basieren auf Nahrungsmitteln wie epoxidiertes Leinöl oder Soja. Perspektivisch will man aber von Nahrungsmitteln als Rohstoff weg. Das erwartet auch die Industrie von uns“, betont Türk. Der Experte für nachwachsende Rohstoffe und Biokunststoffe der Fachhochschule Bingen weiß aus Erfahrung, dass vor allem Automobilhersteller solch hochwertige Lebensmittel wie Leinöl für Türinnenverkleidungen ablehnen.
Reste der Zellstoffverarbeitung nutzen
Mit der Entwicklung neuer biogener duroplastischer Harze betreten die Forscher jedoch Neuland. Denn die Biokunststoff-Branche ist bisher auf Bio-Thermoplaste fokussiert. Joghurtbecher als Polymilchsäure (PLA) sind nur ein Beispiel dafür. „Wenn ich ein Duroplast herstellen möchte, brauche ich reaktive Systeme, die miteinander chemisch wechselwirken. Davon gibt es in der Natur nicht so viele Stoffe“, erklärt Türk. Im Vorhaben „BioDuroZell“, das vom Bundesministerium für Bildung und Forschung (BMBF) im Rahmen der Förderinitiative „Neue Produkte für die Bioökonomie“ noch bis 2018 mit insgesamt knapp 300.000 Euro gefördert wird, konzentrieren sich die Wissenschaftler daher auf Reststoffe, die bei der Herstellung von Zellstoff anfallen. Am Projekt beteiligt sind neben der Fachhochschule Bingen, die Transferstelle Bingen (TSB), die Johannes Gutenberg-Universität Mainz sowie der Zellstoffhersteller ZPR, die Marktexperten der Angewandte Innovative Materialien (AIM) und der Automobilzulieferer Polytec als Wirtschaftspartner.
Zellstoffreste modifiziert
Erste Erfolge haben die Verbundpartner bereits vorzuweisen. Im Rahmen der bis 2015 laufenden und mit knapp 50.000 Euro geförderten Sondierungsphase gelang es ihnen, ein Verbundwerkteil, bestehend aus dem in Zellstoffresten gefundenen biogenem Harz zuzüglich petrochemischen Härter und Naturstofffasern herzustellen. „Wir haben es geschafft, aus den ersten kleinen Harzmengen ein Tablett herzustellen“, so der Projektleiter. Bei dem biogenen Harz handelt es sich um Tallöl-Komponenten, die im Holz als Reststoff bei der Zellstoffherstellung anfallen. „Die Mainzer Kollegen haben diese Reststoffe chemisch und elektrochemisch so modifiziert, dass sie als duroplastisches Bindemittel funktionieren“, erklärt Türk.
Dieses Tablett wurde als Probestück aus dem neuen biogenen Bindemittel und Naturstofffasern gefertigt.
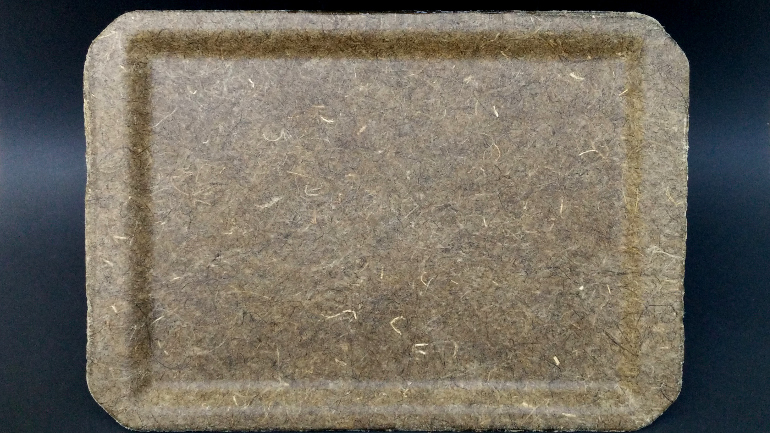
Weniger geruchsintensiv und CO2-neutral
Hinsichtlich ihrer mechanischen Eigenschaften sowie der thermischen Belastbarkeit könnte das neue biogene Harz mit der erdölbasierten Version mithalten, wenn die Vernetzung optimiert wird. „Im Vergleich zur petrochemischen Variante entstehen bei unseren biobasierten Duroplasten prinzipiell nur sehr wenige organische Emissionen, sodass sie weniger riechen und so für den Automobilbau prädestiniert sind. Außerdem sind die Bio-Verbundwerkstoffe in erster Näherung auch CO2-neutral.“
Nach dem Erfolg in der Sondierungsphase gilt es nun zu beweisen, dass das biogene Bindemittel auch den Anforderungen der Industrie gewachsen ist. In der sogenannten Machbarkeitsphase, die mit weiteren 250.000 Euro vom BMBF gefördert wird, muss der einst im kleinen Maßstab geglückte Prozess nun reproduziert werden, damit ausreichende Mengen des neuen Harzes hergestellt werden können. „Wir haben noch ein paar chemische Herausforderungen zu meistern, damit ein industrietaugliches Produkt daraus wird,“ sagt Türk. Man habe zwar ein Reaktivharzsystem gefunden. Das muss aber eine entsprechende Netzwerkdichte, Härte und Reaktionsgeschwindigkeit aufweisen, um mit den petrochemischen Vergleichsprodukten mitzuhalten. Daran haben wir noch ganz schön zu knabbern“, berichtet Türk.
Energetische Nutzung von biobasierten Harzen
Bis zu einer industriellen Anwendung in Fahrzeugbau und Elektrik ist es also noch ein weiter Weg. Parallel dazu arbeiten die Binger Forscher um Türk bereits an einem biobasierten Härter für Duroplaste, um den Kunststoff noch nachhaltiger zu machen. Bisher können duroplastische Verbundstoffe nur schwer wiederverwendet werden. Für Naturstoffexperten Oliver Türk gibt es daher nur ein Ziel: „Die biobasierten Duroplaste können am stofflichen Lebensende dann noch einer energetischen Nutzung zugeführt werden. Diese doppelte Verwertung ist durchaus sinnvoll und darüber hinaus in erster Näherung CO2-neutral.“
Autorin: Beatrix Boldt