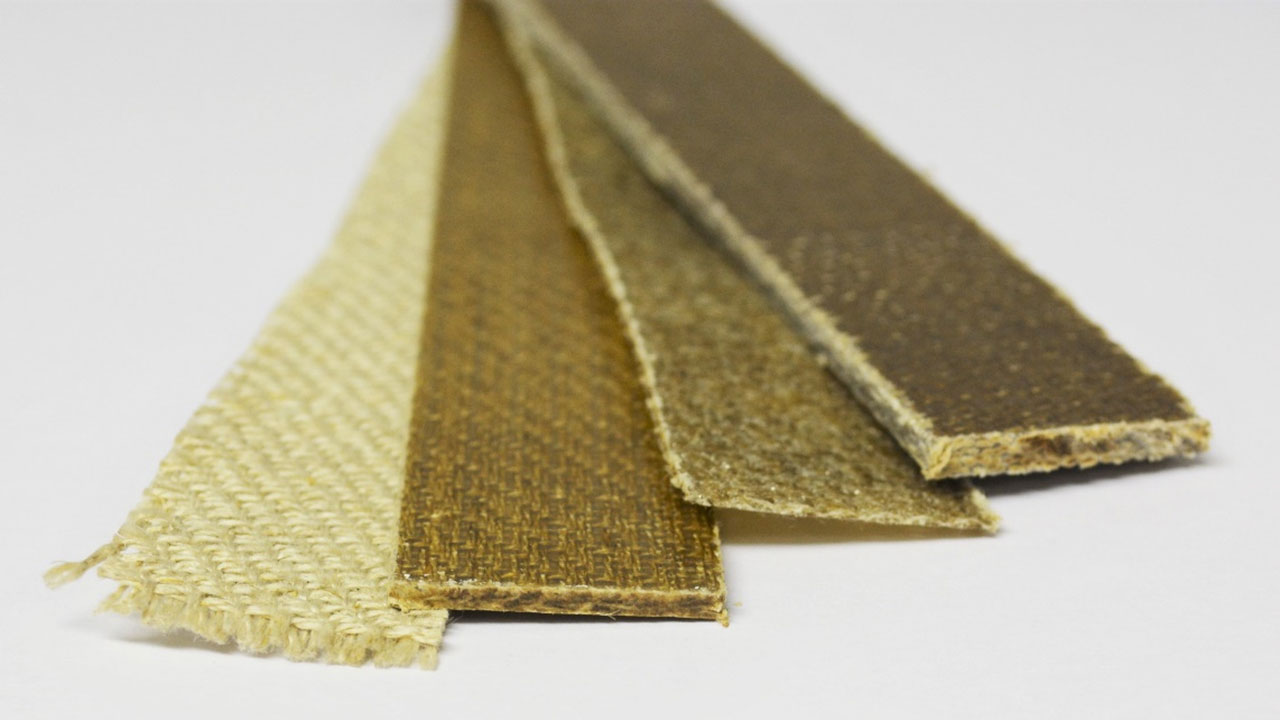
The plastics industry is changing: The abandonment of petroleum as a raw material and the move toward bio-based raw materials requires research into new processes and materials, but also promises potential for new types of applications. One of the challenges involved relates to engineering thermoplastics: Their melting temperature in the hot press is often over 200°C. However, since natural fibers are generally only heat-resistant up to a maximum of 200°C, it has been virtually impossible to process them this way. The "DeFiCoat" research project has now developed an initial approach to solving this problem.
High-performance and biobased
The project acronym "DeFiCoat" stands for "Development of specially coated fibers for manufacture of novel biocomposites from engineering thermoplastic". From November 2017 to December 2019, the Fraunhofer Institute for Wood Research (Wilhelm-Klauditz-Institut; WKI), together with the Canadian University of Guelph, has taken on the challenge of making natural fibers more stable thermally, mechanically and in terms of moisture absorption. The research team received funding of around 500,000 euros from the German Federal Ministry of Education and Research through the "Bioeconomy International 2016" program.
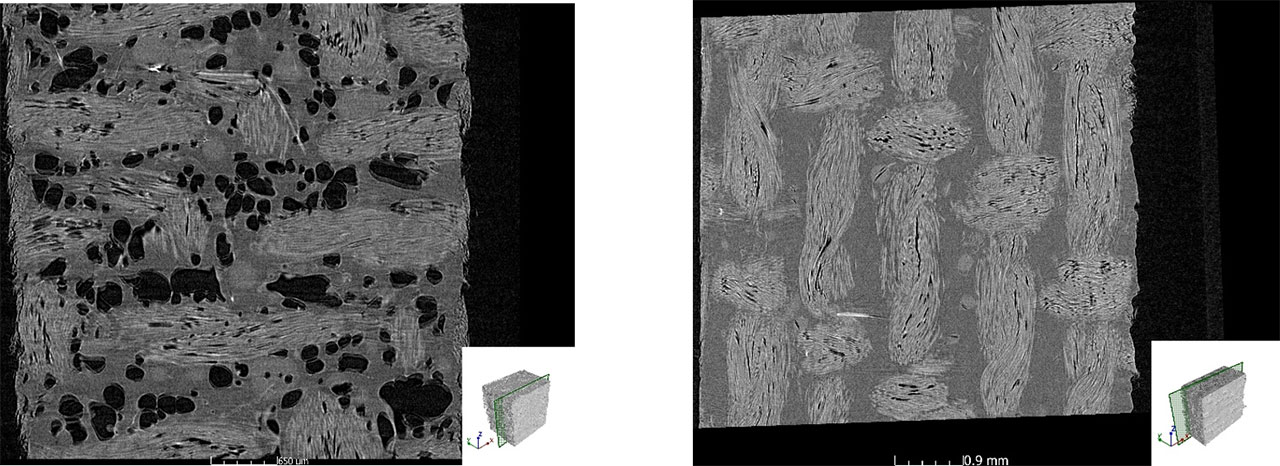
"How can natural fibers be thermally stabilized - by means of a coating?" was the question with which the project began, recalls Natalie Vellguth of the Fraunhofer WKI. The materials and nanochemist had taken over the project management from Hans-Josef Endres after he had moved from Fraunhofer HOFZET to Leibniz University Hannover. Alternatively, it would be possible to lower the melting temperature of the thermoplastics through additives, but that would worsen the material properties.
Coating flax with resin
Vellguth reports that experience with natural fibers has already been gained with duromers, which cure at a maximum of 120°C and can no longer be molded afterwards, for example as biocomposites for car doors. Thermoplastics, on the other hand, can be repeatedly reshaped within a certain temperature range and are therefore of interest for a wide range of applications and industries.
The decision was finally made in favor of the approach of coating the fibers with a thermosetting resin. This protects the natural fibers when they are subsequently incorporated into thermoplastics during hot pressing. The research team chose flax as the fiber raw material - because of its good mechanical properties and easy availability in Germany. "In the Asian region, other fibers would certainly have been chosen," says Vellguth. Hemp or jute could also be used, but the project results would not be easily transferable due to the different fiber structures. In the case of the resin, a partially biobased system provided the best material flexibility. A non-biobased polyamide matrix was used as the thermoplastic component.
Several hardener systems tested
In order to apply the resin well, the experts tested different resin hardener systems. Spraying the resin on both sides proved best in order to obtain a flexible and well coated material. The originally planned coating process by immersion failed due to the late availability of the corresponding machine. But even so, the project manager was pleased to note: "We were able to achieve significantly higher mechanical characteristic values than without coating."
The project was primarily concerned with studying the material, not with producing specific components: It was tested how the biocomposite material made of resin-coated flax fiber and polyamide performs in comparison to uncoated fiber composites. Using computed tomography and scanning electron microscopy, the experts examined the homogeneity of the structure and coating, and conducted accelerated aging tests. The latter resulted in the resin post-curing and further increased mechanical parameters. "Composites with ceramic or even glass fibers can be replicated with flax for applications with less stringent mechanical requirements," Vellguth sums up. The biocomposite material is even better to process, she says, because glass fibers, for example, are porous and break more easily.
Ready for industry in five years?
"We have achieved the milestones of the project well," Vellguth concluded. Future challenges will now be to establish a process for continuous coating, where previously manual work was carried out. Among other things, this requires further optimization of the resin system. In addition, the material components are to be modified in such a way that easier recycling is possible - another important sustainability factor. Perhaps in five years, such a material could then be ready for industrial use.
Author: Björn Lohmann