Energy
Bioenergy from renewable resources remains an important element in the energy mix of the future. Agricultural farms can use biogas plants to produce electricity and heat. Even in a future electric mobility system, biofuels will still be needed for shipping and aviation.
Examples of bioeconomy:
Wood pellet heating systems,
Biogas, biodiesel, bioethanol,
synthetic biofuel
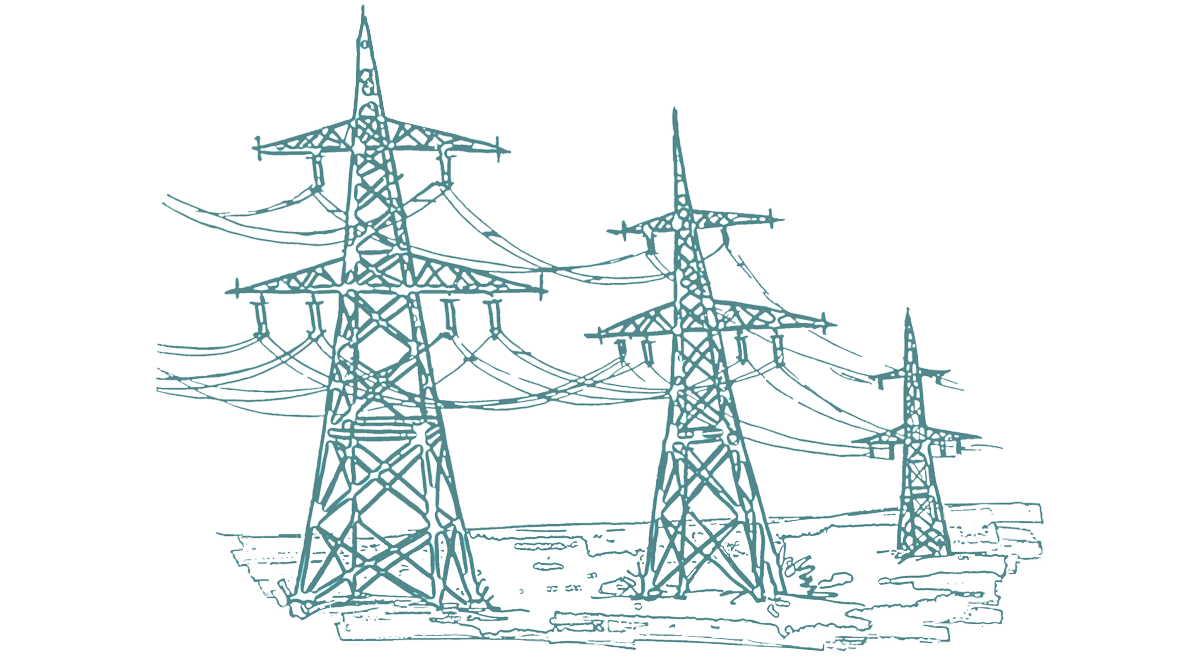
With the energy transition, the German Federal Government intends to considerably increase the share of renewable sources of energy. To ensure that the energy supply continues to be reliable, secure and affordable, the Federal Government has set up the Energy and Climate Fund (EKF). The programme supports projects on renewable energies, national and international climate and environmental protection, electromobility and investments into boosting energy efficiency (including building refurbishment).
Bioenergy is a renewable energy, and one of the important building blocks in the energy mix of the future. Biomass, i.e. plants as well as plant and animal residues and waste, is considered a versatile source of bioenergy. It can be used to generate heat, electricity and fuels. On top of that it can be easily stored and bioenergy plants can be flexibly controlled. Biomass plants have the potential to compensate for fluctuations in the availability of other renewable energy sources, such as wind or solar power. According to the Federal Environment Agency, the largest share (47%) of renewable energies used in Germany in 2024 came from biomass. However, the available technologies are controversial because they do not yet meet all sustainability criteria. The first-generation biofuels such as biodiesel or bioethanol, for instance, are produced from oil- and sugar-containing plant crops that are also used for food production. This has created competition between “food, feed and fuel”.
In Europe – and particularly in Germany – the use cases of bioenergy have been reassessed in recent years and the framework conditions have been modified. In the National Bioeconomy Strategy and elsewhere, the Federal Government emphasises the priority of a secure global food supply over material and energy use. In future, biomass for energy generation should mainly come from organic residues and waste materials. Second-generation biofuels are produced from non-edible plant parts, i.e. residues and lignified plant parts such as straw or wood chips.
Wood is an important fuel. In 2020, around 60 million cubic metres of wood were used for energy production in Germany (approximately 50% of the total wood raw material volume), 45.7% were burnt by private households. This means that a little over half of the wood used for energy is burned in biomass plants. 27% of the wood used for energy is solid forest wood (this is predominantly non-coniferous wood which is burned in private households). 24.7% of wood energy comes from sawmill residues and 22.5% from used wood, which is mainly incinerated in large combustion plants (> 1 MW).
The remainder is other types of wood such as landscape conservation wood. About 90% of renewable heat is generated from biomass. Modern, fully automatic pellet heating systems significantly reduce the emission of air pollutants such as particulate matter and carbon monoxide. The Agency for Renewable Resources (FNR) operates a website offering comprehensive information on heating with wood (heizen.fnr.de).
Biogas plants convert plants, animal excrement such as manure and other residual materials into biogas. Microorganisms ferment the biomass in airtight containers called digester. The result is a gas mixture which mainly consists of methane and CO2. The biogas is then combusted in gas engines to produce electricity or heat. The residual material left after fermentation can be used as a fertiliser. Some plants convert biogas into biomethane by increasing the methane content and improving the quality of the gas until it is suitable for feeding into the natural gas grid.
According to the German Biogas Association, there were around 10,000 plants in Germany in 2023, generating more than 5,900 megawatts of electricity. There is still much room for improvement in process technology for biogas plants. Through the NextGenBiogas project, the BMEL is promoting the development of a new generation of flexible biogas plants (see Mechanical engineering). The choice of energy crops is important, and the most common crop used today is corn silage. The Renewable Energy Sources Act (EEG) of 2021 aims to reduce the substrate share of maize and cereal grain to 40%. Attention is now shifting to perennial plants such as the sturdy miscanthus grass or the cup plant. The Berlin-based start-up SOLAGA takes a different approach: Microalgae film is used to produce biogas in small plants that can be installed in private households.
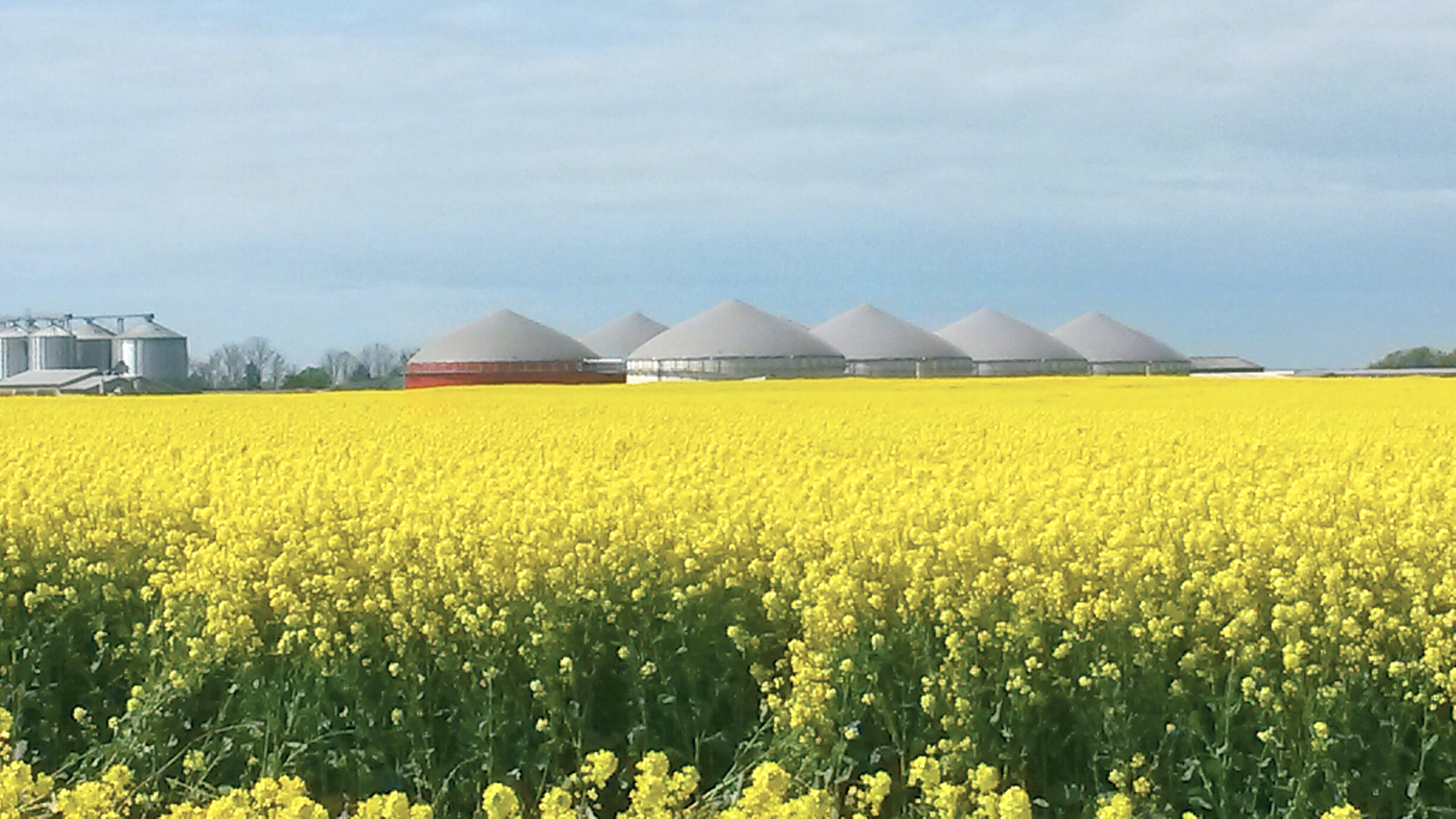
As we strive for climate neutrality and switch to electricity and hydrogen power, there are some areas, such as heavy goods transport and shipping, where liquid fuels will remain important. Biodiesel is produced from vegetable oils or animal fats. In Europe, the largest share of biodiesel comes from rapeseed, which is suitable for the production of biodiesel because its contains up to 45% fat. Biodiesel from residual materials, such as used cooking oil and frying fat, is gaining in importance. According to the FNR, around 3 million tonnes of biodiesel from vegetable oil and used cooking oil were used in Germany in 2020.
Next-generation biofuels
Biomass from agricultural residues such as cereal and corn straw, miscanthus and wood is in high demand for the production of biogas as well as other forms of bioenergy. However, lignocellulose, a substance contained in the cell walls, makes the efficient and complete use of plant residues, straw and wood difficult. There are different approaches to split up lignocellulose. Clariant, a chemical company, operates a demonstration biorefinery in Straubing in Bavaria, where straw is split up into its components and then converted to cellulosic ethanol through a biotechnological process. The bioethanol produced with the “sunliquid” process can then be added to petrol for combustion engines. At the end of 2021, the construction of a commercial biorefinery plant in Romania was completed with EU funding.
Usually, the soluble alcohol has to be separated from the water – a process which consumes much energy – before bioethanol can be produced. To overcome this challenge, recent research efforts have been looking into converting lignocellulose into a biofuel that does not dissolve in water easily. Alternatives include the long-chain alcohol butanol, which has different physical and chemical properties that make it insoluble in water, and which also offers higher fuel efficiency than ethanol. Processes for producing butanol from plants or plant residues are currently being developed. Global Bioenergies, a French company, has come up with a biotechnical process in which bacteria produce a gaseous hydrocarbon called isobutene. At its site in Leuna, Global Bioenergies produces isobutene, which can be converted into isooctane. The bio-based fuel is being tested by Audi to establish its suitability for standard use as part of a cooperation project.
Other sources of biofuel which are enjoying rising popularity include microalgae and cyanobacteria. These microorganisms perform photosynthesis, meaning they use the sun’s energy to produce energy-rich sugar molecules from CO2. In a subsequent step, microbial metabolisms can convert the sugars into lipids or oils, which in turn are processed into fuels. Experts refer to fuels which are obtained from photosynthetic organisms and CO2 as a carbon source as third-generation biofuels. The AlgaeTec facility on the Bölkow Campus of the Technical University of Munich is a state-of-the-art algae research laboratory. Since 2016, research has been ongoing into the potential of algae of (mostly) marine origin to produce fatty oils, which are suitable for the production of aviation fuels and other industrial chemicals at extreme salt concentrations. The AlgaeTec facility was funded by the Federal State and by the Airbus Group. At the Algae Science Centre at Forschungszentrum Jülich, sustainable kerosene from algae oil is being investigated.
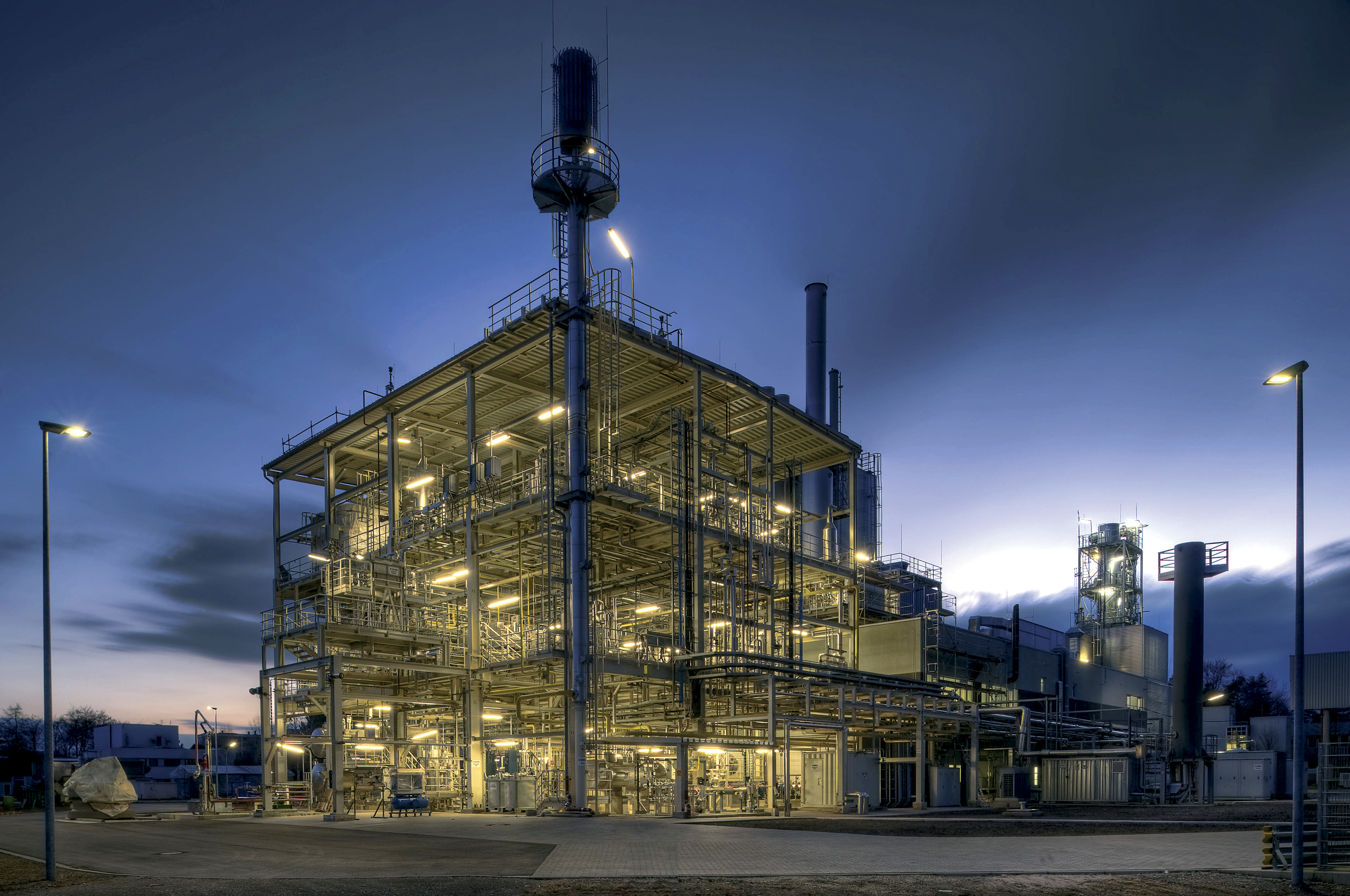
Synthetic biofuels
Biomass-to-Liquid (BtL) fuels are produced by thermochemical conversion. The complex molecules of the biomass are converted into a syngas (carbon monoxide and hydrogen) at high temperature. The syngas is then converted into liquid hydrocarbons – the desired fuel – using the Fischer-Tropsch synthesis, a principle which has been around for decades. Any elements contained in the biomass, such as nitrogen or sulphur, are separated. The synthetic fuel is free from foreign substances and has the same combustion properties as conventional diesel, for example. The fact that, potentially, the entire plant can be utilised, is a bonus and means that straw or woodchips are suitable for processing into BtL fuels. While the technology is not yet commercially used, BtL fuels are the subject of intensive research. At at pilot plant at the Karlsruhe Institute of Technology (KIT), the “bioliq” process, a production method for synthetic fuels, is being developed.
Hydrogen is considered the energy carrier of the future because of its low-carbon production and use. Green hydrogen is currently mainly produced by water electrolysis, a process which uses large amounts of electricity from renewable sources. However, there are some bio-based methods to produce green hydrogen, such as the photosynthesis of green algae or bacteria. As part of this process, water molecules are split up into oxygen, protons (i.e. hydrogen ions) and electrons with the help of light energy and enzyme catalysis. Certain enzymes, known as hydrogenases, then help to produce hydrogen molecules. A research team from Kassel has managed to convert cyanobacteria into biological hydrogen factories using molecular tools. Under specific conditions, microorganisms can also convert biomass into hydrogen and CO2 in biogas plants. This is referred to as dark fermentation. Both methods for the production of biohydrogen are being explored intensively.
Almost all common batteries contain metal compounds based on lithium, lead or vanadium, which are difficult to extract and to recycle, and often associated with environmental problems. The BMEL is currently funding the development of a plant-based alternative. The project is aimed at stationary redox flow batteries, which are able to store energy on an industrial scale. This requires electrolytes that are to be extracted from lignin, a wood component. Biogas plants can also be used as a flexible element of the electricity sector by serving as chemical energy carriers and storage. A project funded by the BMEL is looking into ways in which biogas plants can be combined with battery storage in order to open up new marketing channels.