Construction
Whether as a building material, for insulation or interior finishing: Renewable raw materials boast good material properties, improve the eco-balance and are often better for human health. However, even for conventional construction products such as concrete, bio-based, sustainable strategies are now available.
Examples of bioeconomy:
Timber construction,
natural-fibre-reinforced composites,
dowels
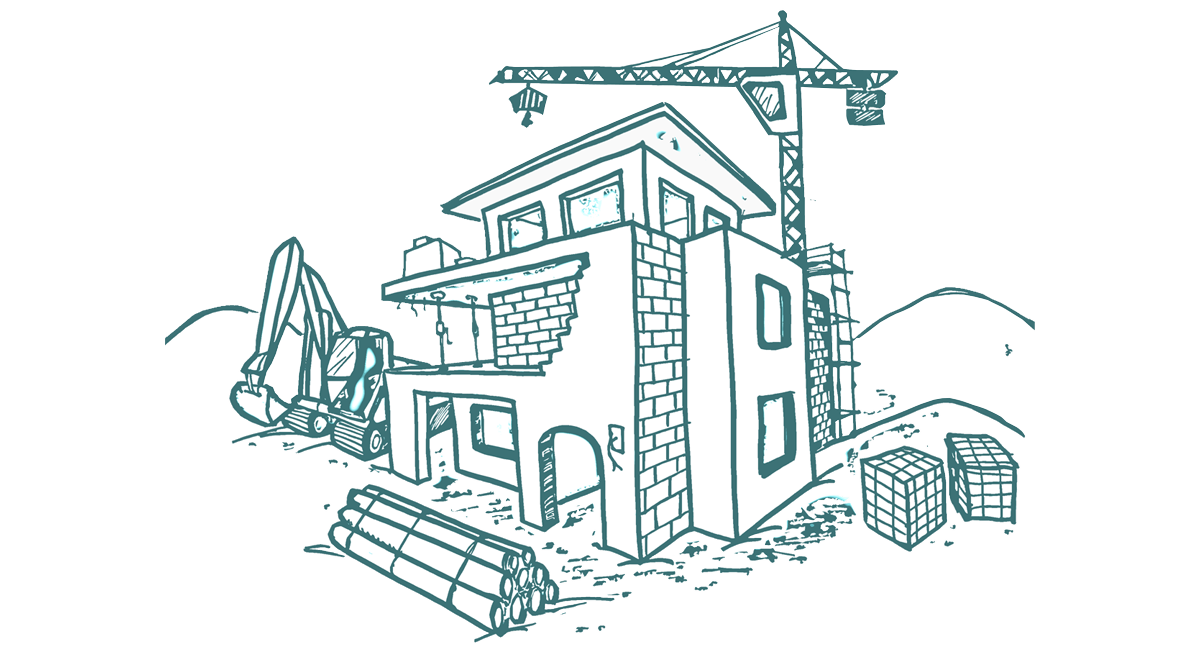
Construction is one of the most resource-intensive sectors in Germany. 90% of mineral raw materials are used for the production of building materials and products, and the building sector accounts for about 40% of total greenhouse gas emissions in Germany. Three quarters of these emissions are caused by the use and operation of buildings, while the rest is caused by the construction materials industry and construction activities themselves. This is shown by the environmental footprint of buildings determined by the Federal Institute for Research on Building, Urban Affairs and Spatial Development (BBSR). With increased attention being paid to climate neutrality and sustainability, bio-based materials are increasingly coming into focus.
This means that the 325,000 businesses of the main construction industry and the finishing trade, which employed 2 million people in 2019, are of great importance for the bioeconomy in this country. At 277 billion euros, the sector generates about 6% of the total value added in Germany. According to the German Construction Confederation (ZDB), the timber construction sector alone accounted for 71,561 employees in 11,864 companies in 2020 and had a total turnover of 8.3 billion euros.
Wood is the most important renewable building and construction material there is, either in the traditional form of sawn timber produced by sawmills, or in the form of wood-based materials. In the production of chipboard, for example, wood chips are glued together and pressed into boards. Wood boasts excellent structural properties: Not only is it flexible, light and easy to work with, but also load-bearing, pressure-resistant and – after processing – it is extremely resistant to bending. What’s more, wood is good for the climate: As they grow, trees store CO2 by absorbing carbon dioxide and locking the carbon into their wood biomass. As a rule, less fossil energy is required for the production and disposal of building materials made of wood than for materials based on finite, mineral raw materials.
Wood creates a good indoor climate thanks to its pleasant surface temperature and its ability to regulate humidity inside buildings. Wood can be used for designs for new buildings, but also for urban densification or adding storeys to existing buildings. Timber structures can be efficiently prefabricated with high accuracy, which reduces construction time.
Digital planning and manufacturing
According to the German Timber Construction Association (Holzbau Deutschland), the timber construction rate was 22% in 2023. The number of employees in the field of timber construction increased by 28% in the space of ten years. The working group on timber construction in urban and rural areas under the umbrella of the Charter for Wood 2.0 – a programme initiated by the BMEL – brings together players from industry, science and administration in order to promote timber construction.
More and more architects are opting for wood as a load-bearing structure. The BMEL’s national HolzbauPlus competition awards prizes for outstanding timber construction projects. One particularly impressive example of a modern, high-tech wooden building is the German National Garden Show pavilion designed by the University of Stuttgart for the National Garden Show 2019: The pavilion’s load-bearing structure was inspired by the plate skeleton of a sea urchin and is made exclusively of fibre composites. The lightweight construction was designed digitally and manufactured in a robot-assisted process. In 2020, the design received a HolzbauPlus award. The Technical University of Munich is heading a BMEL-funded digitalisation project for the adaptation of Building Information Modelling (BIM) to timber construction. BIM, a 3D structural engineering planning method, supports all the digital workflows within the planning and construction process.
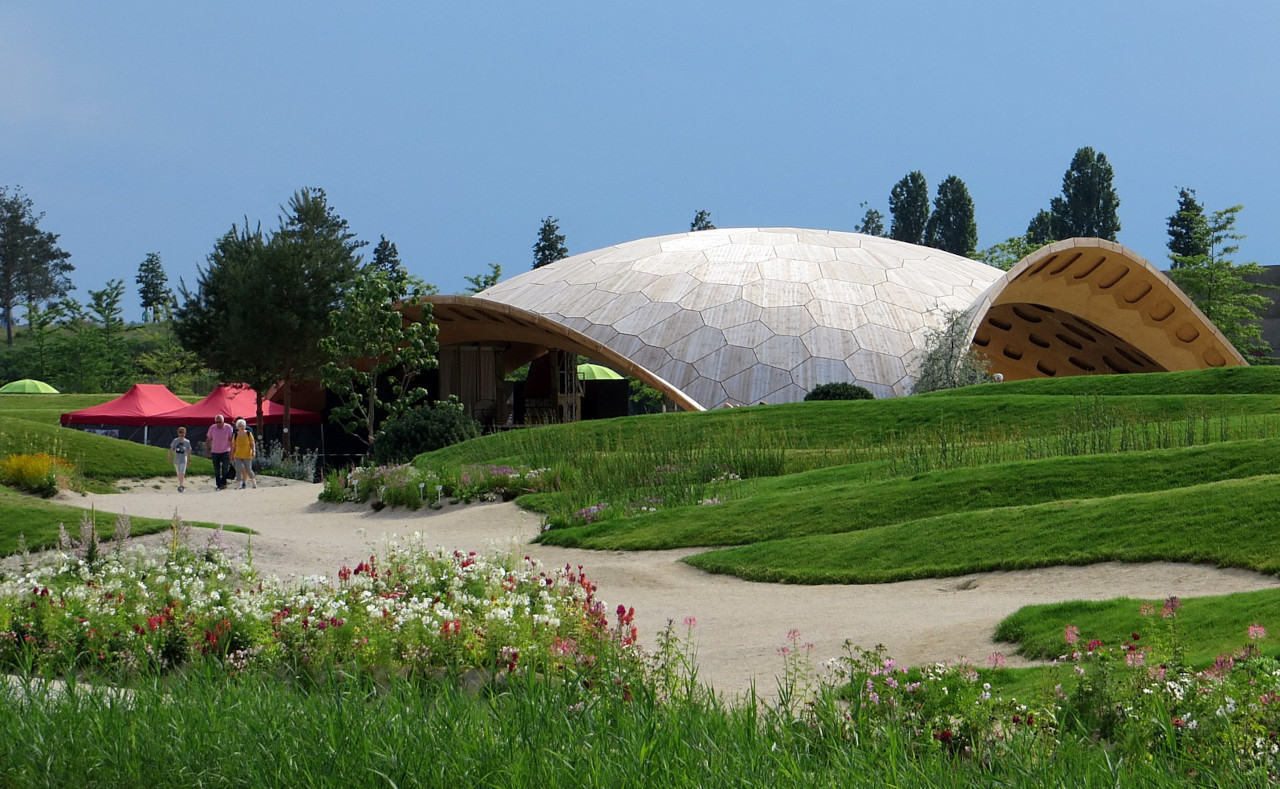
Unlocking the potential of non-coniferous wood
Traditionally, load-bearing components in timber construction have been made of coniferous wood such as spruce. But the attention of research and development in the construction industry is increasingly turning to non-coniferous wood. This is partly due to the fact that in our native forests, which are being converted to mixed forests in response to climate change, beech wood is already abundant and expected to become even more so. Currently, most of the non-coniferous wood is used for energy production, but modern bonding technologies are expanding its potential: The Pollmeier sawmill, a specialist in beech wood processing, has developed a product called BauBuche, for example. This new type of material is produced by peeling wood off the beech trunk and then gluing it together in layers.
The resulting laminated veneer is a high-tech material that is suitable for structural timber design. Thanks to its great density, the load-bearing characteristics of laminated veneer lumber are close to those of steel. The SWG screw factory in Waldenburg is a case in point: At a size of 97 by 114 metres, the factory’s roof truss is the word’s largest roof made of BauBuche. The Thünen Institute for Wood Research analyses the structural properties of construction beech.
The German Federal Government and Federal State governments are supporting several innovative programmes for the application of non-coniferous woods such as beech and oak for the construction and other sectors. One such initiative is the Technikum Laubholz (Hardwood Technical Centre) in Baden-Württemberg. The BMEL also supports research initiatives to increase the material use of non-coniferous wood, such as the Charter for Wood 2.0.
Building with wood is not the only way to reduce CO2 emissions in the building materials industry. The steel and cement industries have great potential to reduce the vast amounts of CO2 they emit. As shown by the Fraunhofer Institute for Wood Research (WKI) in Braunschweig, there are ways of replacing steel in concrete with a fabric made from flax fibres. Flax fibre-reinforced concrete only requires half the thickness of steel-reinforced concrete in a bridge. There are a number of research projects that aim at improving the CO2 footprint of concrete by employing bio-based raw materials, raising recycling rates and other approaches. Researchers in Berlin, for example, have developed a bio-concrete based on cassava peel ash.
A team at Hochschule München University of Applied Sciences is experimenting with adding bacteria to the concrete mix. If cracks appear and moisture penetrates, the microorganisms form limestone and repair the crack, which could extend the life of a building. Last but not least, wood and concrete can be combined to form hybrid materials. A BMEL-funded research initiative uses an innovative wet-on-wet adhesive bonding technology in which fresh concrete is poured onto a still-wet adhesive layer on a wooden support. Wood-concrete composite (WCC) floors bonded using this technique have a higher load-bearing capacity than conventional WCC floors, saving two thirds of the concrete and four fifths of the reinforcing steel compared with conventional construction methods. This reduces CO2 emissions to one third.
Researchers at TU Berlin are working with fungi that can transform renewable raw materials into innovative building materials. Basidiomycota mushrooms, which may be edible varieties such as oyster mushrooms or inedible polypores such as tinder fungus, are best suited for the production of composites. The fungal mycelia convert plant residues into a stable and very light composite material. The big advantage of this material is that it can be easily composted. Experts in sustainable building at the Karlsruhe Institute of Technology (KIT) are researching “cultivated” building materials from fungal mycelia and how to combine them with digital manufacturing techniques.
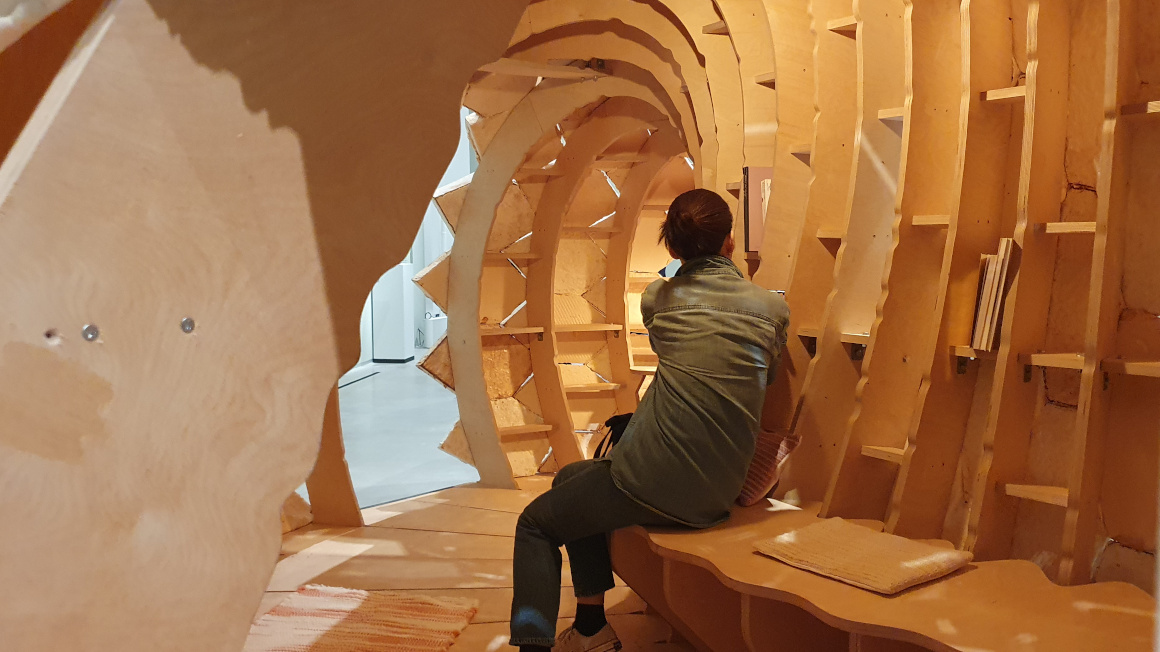
In this age of energy-efficient construction and renovation, natural insulation materials are becoming increasingly important. Their production is less energy-intensive and they have a positive effect on the indoor climate. These materials absorb large amounts of moisture and are often better for allergy sufferers. In 2019, the market share of insulation materials made from renewable raw materials was approximately 9%. With 58%, wood fibre insulation materials account for the largest share within this segment. Cellulose from shredded waste paper is also used as a raw material and makes up 32% of bio-based insulation materials, while hemp, flax, meadow grass, straw and sheep’s wool account for smaller shares. As a research project funded by the BMBF has shown, agricultural residues can also be used as a basis for insulation material. The project team developed insulation materials for filling and blowing from corncobs. Corncobs are the central core of an ear of corn that is left over once grain maize has been harvested. In 2018, natural paints had a market share of 5%. Unlike conventional chemical products, natural paints are made from natural mineral or plant sources and require far smaller amounts of solvents. The most frequently used natural paint products are wall paints, wood stains, natural resin varnishes, oils and waxes. Floor coverings made from renewable raw materials provide the basis for wooden floors such as parquet, planks and laminate, as well as for cork and sisal floors. Linoleum consists of linseed oil, cork and wood flour, lime flour and pigments as well as jute fabric as a backing.
As we move towards a circular economy, recycling is becoming an important topic for the construction industry. ReMatBuilt, a German-Chinese research project funded by the BMBF, aims to improve resource efficiency in construction by recycling agricultural and forestry waste as well as construction and demolition waste. The goal of the project is to develop environmentally friendly hybrid building products, such as insulation panels made from rice or wheat straw.