Pharmaceuticals
Medicinal herbs have been used against illnesses for thousands of years. Today, medicines are more and more often produced using biotechnological processes. Biopharmaceuticals, which include active ingredients such as antibodies, enzymes and vaccines, account for about one third of the pharmaceutical market – and their share is growing rapidly.
Examples of bioeconomy:
Biopharmaceuticals
- antibodies
- vaccines
- enzymes
Medical plants
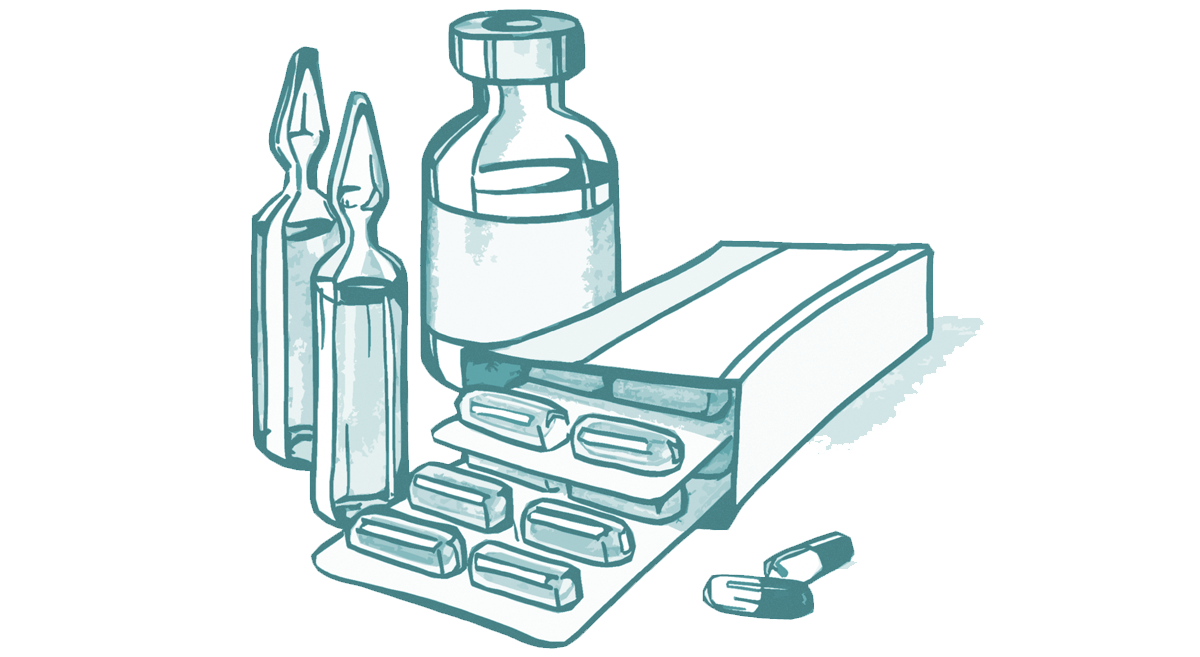
Pharmaceutical companies are increasingly resorting to knowledge about biology for the production of medicines. Although chemically synthesised active ingredients still make up the largest share of the German pharmaceutical market, so-called biopharmaceuticals are catching up. Biopharmaceuticals are biomolecules that are too large to be produced chemically, or at least their production would not be efficient. This is where modern biotechnology comes in by using molecular genetic processes that turn living microorganisms and cells of higher living organisms into miniature factories for drugs.
According to an industry report published by the Boston Consulting Group and vfa bio, at the end of 2023, 417 biopharmaceuticals had been approved in Germany. This pushed the market share of these biotechnologically produced medicines to 34,5%. In 2023, a total of 19.2 billion euros was generated with biopharmaceuticals in Germany, including antibodies against cancer or autoimmune diseases such as rheumatism or multiple sclerosis, hormones such as insulin for the treatment of diabetes or enzymes against metabolic diseases.
Genetically engineered drugs for humans and animals are widely accepted by society. In 2020 alone, 25 more biopharmaceuticals were approved. The largest players are the former Hoechst site in Frankfurt, which is now part of the French company Sanofi, and the Swiss pharmaceutical company Roche, which has established extensive production capacities for biotech drugs at its Penzberg site. In addition, some German companies have large-scale production facilities, for example Bayer in Leverkusen, Merck in Darmstadt and Boehringer Ingelheim in Biberach. A number of small and medium-sized biotechnology companies have specialised in taking over bio-based production as service providers or in helping to develop and implement processes that meet market requirements. In 2020, the total production capacity for biopharmaceuticals in Germany was estimated to be 380,000 litres. Germany ranks fifth worldwide behind the USA, South Korea, Ireland and Switzerland. When it comes to the biotechnological production of active pharmaceutical ingredients, Germany is one of the world leaders.
Among biopharmaceuticals, antibodies in particular have come into focus. These complex protein molecules are considered the “sentry guns” and guided weapons within the human immune system. Each specific antibody will attach to a specific molecule only, such as the surface protein of a virus or the toxin of a bacterium. Antibodies bind to their target molecule, marking it for degradation. Antibodies are produced using cell cultures. At the end of 2020, 107 antibody-based medicines had been approved, which is 32% of all approved biopharmaceuticals. Especially the treatment of cancer and autoimmune diseases has seen considerable improvement since the advent of antibody therapy. The sales of antibody drugs in Germany were at 10 billion euros.
Peptides are small protein molecules composed of up to 100 amino acids. The pharmaceutical and cosmetics industries use peptides as active ingredients or bioactive ingredients for creams and ointments. Numaferm, a company based in Düsseldorf, has developed a biotechnical process for the large-scale production of peptides with the help of microorganisms. The start-up was funded by the BMBF on several occasions.
Other classes of drugs, such as antibiotics and vaccines, are also usually produced with biotechnology. German vaccine production focuses on influenza, tick-borne encephalitis (TBE), diphtheria, whooping cough, rabies, Ebola and, since 2020, COVID-19.
The COVID-19 pandemic has given a boost to vaccine research and production. Mainz-based company BioNTech has commissioned an innovative facility for the production of mRNA vaccines against COVID-19 in Marburg. The production of mRNA vaccines is cell-free, meaning that no living cells are used for production. The biomolecules and all necessary components are synthesised in a reaction vessel.
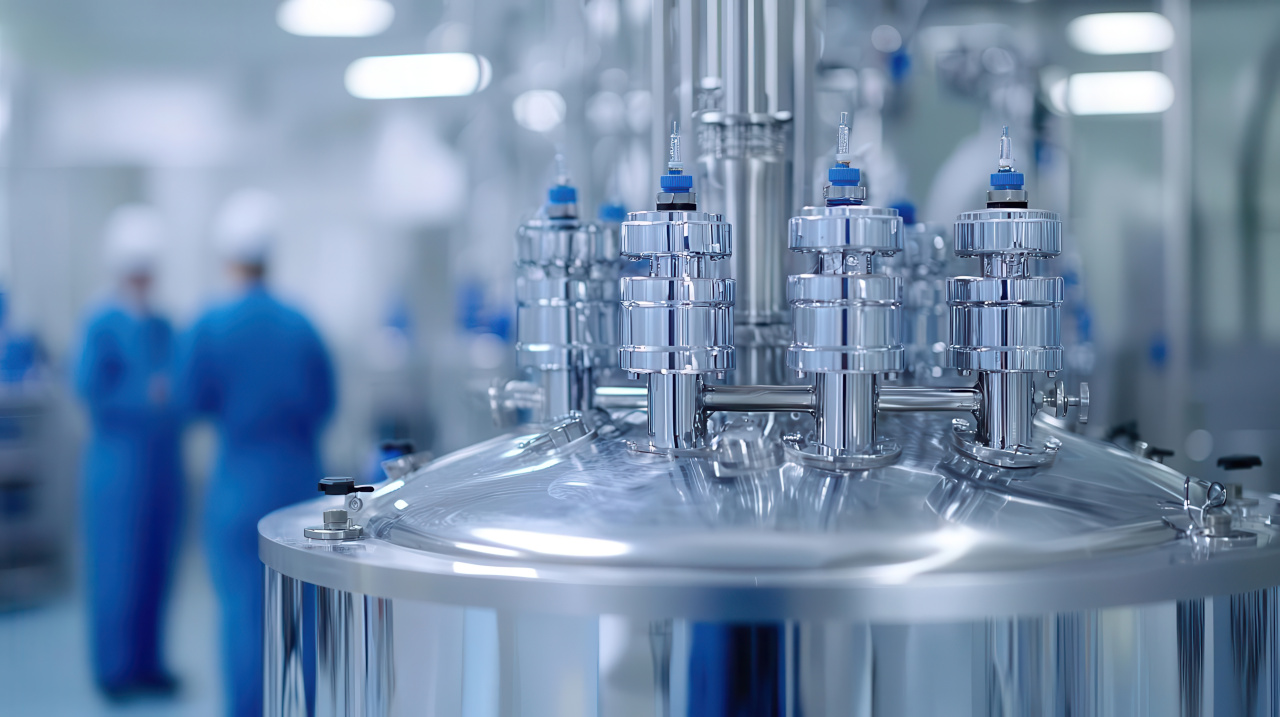
We need intelligent bioprocess technology for the efficient production of all these medicines in the required quantities (see chapter Mechanical engineering). Thanks to Germany’s technical expertise, the country is a leader in bioprocess engineering. The BMBF is supporting companies so they can continue to overcome challenges in this field, such as the need for optimised process control based on intelligent sensor technology. Around 20 partners of the strategic alliance “Knowledge-based Process Intelligence” have developed a sensor and software platform that combines novel measurement principles with modern data evaluation. Another central issue which receives funding from the BMBF is the continuous improvement of purification for biotechnologically produced medicines.
Suitable production organisms are also an important research focus. While in the early days, biotechnology mainly concentrated on working with bacteria – as in the case of insulin – the focus has now shifted to mammalian cells, such as CHO cells (originally from hamsters), or human cell lines. Unlike bacteria, these cells are able to produce certain molecules that determine the effect of drugs. A BMBF funding initiative is looking to establish new microbial biofactories for the industrial bioeconomy, especially for active pharmaceutical ingredients such as terpenes or isoprenoids.
The digitalised biotech laboratory
The collaborative project DigInBio aims to highlight the opportunities presented by digitalisation, automation and miniaturisation for industrial biotechnology, and to make use of them. The partners in this BMBF-funded project work across three digitalised bioprocess laboratories that are connected through a central data management system. The focus is on various steps in bioprocess development. From intelligent software components to knowledge-based experiment planning, to sequence control of real-time simultaneous laboratory experiments, to online data evaluation, in order to be able to drastically shorten bioprocess development in the future. The project partners of DigInBio are Forschungszentrum Jülich, the Technical University of Munich and Leibniz University Hanover.
Today, biological drugs are also made from unconventional organisms. There is increasing interest in using plants to produce innovative active substances. Back in 2012, the US Food and Drug Administration (FDA) approved an enzyme produced in carrot cells for the treatment of Gaucher disease. In Germany, too, research is being conducted into so-called molecular farming as an approach to plant biotechnology.
Scientists at the Fraunhofer-Institute for Molecular Biology and Applied Ecology in Aachen use tobacco plants as green pharmaceutical factories, using an automated production plant. From sowing, cultivation in a high rack system with controllable lighting, irrigation and fertilisation, to harvesting and biotechnological production, practically every step is automated. Based on a process developed by the Halle-based biotech company Icon Genetics, a new plant-based cancer vaccine against lymphoma is to be produced under controlled conditions in the greenhouse. Research carried out by plant researchers at the University of Freiburg is providing the basis for a production process for drugs based on the spreading earthmoss Physcomitrium patens that is being developed by Eleva (formerly Greenovation), a biotech company.
Some plants contain potentially interesting medically active substances, such as paclitaxel, a substance derived from the Pacific yew (Taxus brevifolia), which is used as a cancer drug. Since the population of the Pacific yew is small and the concentration of active substance is low, the global demand for paclitaxel could not be met using traditional methods.
To meet demand, a semisynthetical process from certain plant-based sourcing materials was used for many years. In 2002, the British pharmaceutical company Bristol-Myers Squibb developed a process in which the active substance was isolated from yew cells cultivated on nutrient media in digestors. Biotechnological production takes place at Phyton Biotech GmbH in Ahrensburg, Schleswig-Holstein, which has one of the world’s largest plant cell-based digestor capacities.
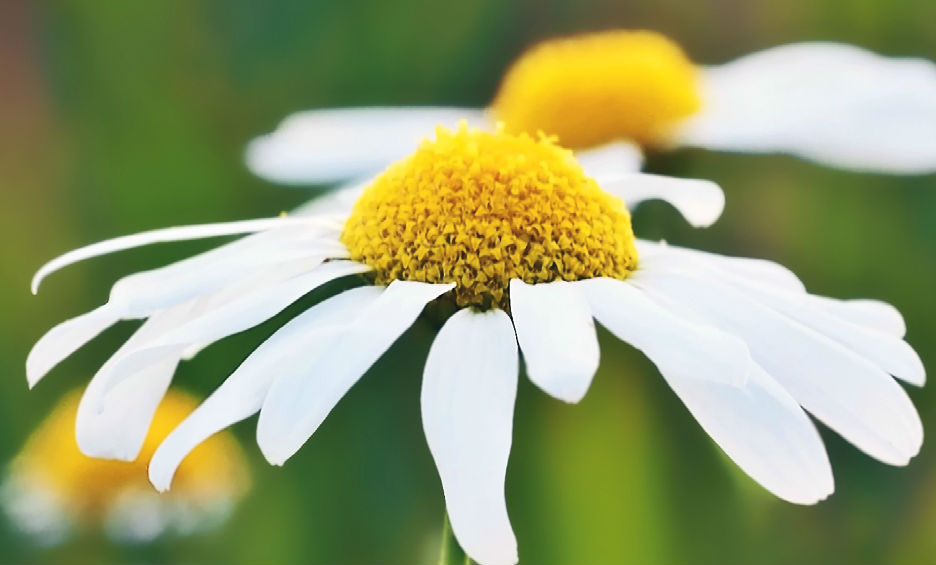
pharmaceuticals, traditional medicinal plants still play an important role today. The cultivation of medicinal herbs has a long history in Germany, which has 440 native medicinal plants. About 75 of them are grown commercially on an area of about 12,000 hectares, mainly in Thuringia, Bavaria, Hesse and Lower Saxony, and account for more than 70% of domestic medicinal plant cultivation. Chamomile has the largest share (more than 1,000 hectares), followed by linseed, milk thistle, peppermint and sea-buckthorn (500 to 1,000 hectares each). However, domestic cultivation is only a niche, because around 85% of medicinal plants processed in Germany are imported.
Plants for which demand is low or that do not grow in Germany are collected in their natural habitat through wild harvesting. Unlike in commercially cultivated plants, these plants may vary in terms of quality and quantity of their compounds. This is why there are growing attempts to cultivate plants that are still only found in the wild. However, this is not easy. The time it takes before harvesting is possible is long – at least five years for herbs, and even longer for some woody plants. For this reason, the BMEL supports research work on the cultivation of medicinal plants.