Automotive sector
The car will continue to be an important component of mobility in the future. Alternative drive technologies are on the rise in response to climate targets and international competition. Manufacturers are turning to bioplastics and biocomposites to build ever lighter vehicles, conserve resources and implement a circular economy.
Examples of bioeconomy:
Natural fibre-reinforced body parts,
interior panelling made from bioplastics,
tyres made from natural rubber from dandelions
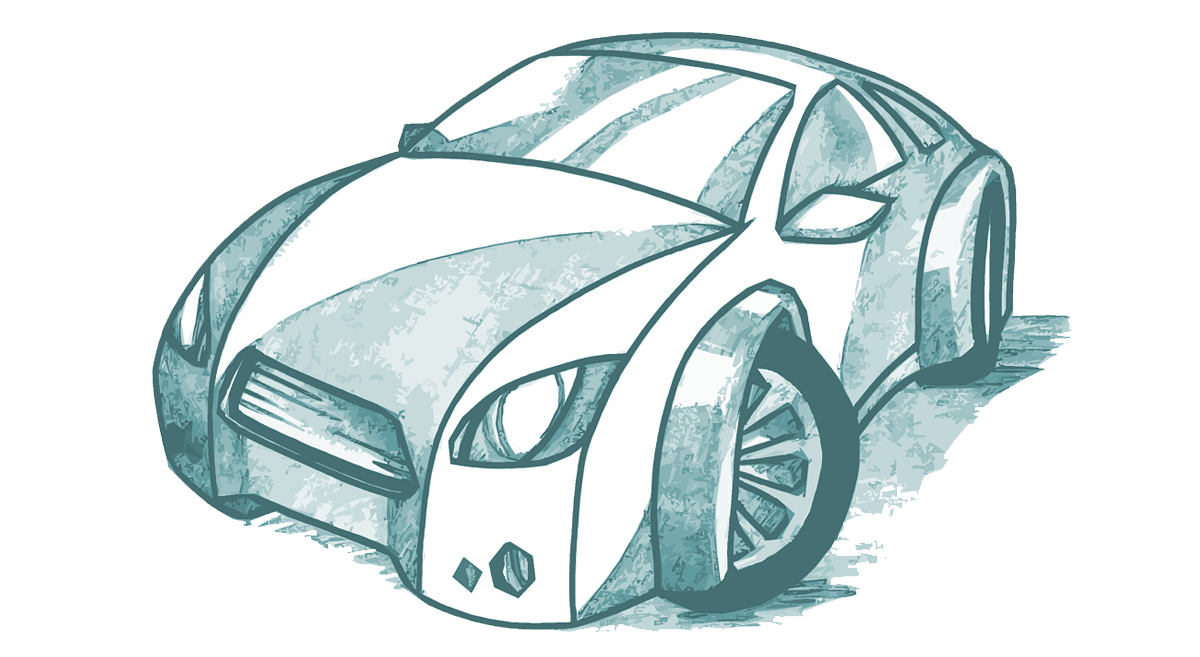
The transport sector causes about one fifth of Germany’s greenhouse gas emissions, with more than 95% due to road traffic. As we move towards climate neutrality, the mobility sector is facing a fundamental transformation, with the car at its centre. According to the Kraftfahrt-Bundesamt, there were more than 49 million registered cars in Germany in 2023. The number of e-cars is still low. Their share of the passenger car population is 2.1 %.
One of the most important drivers of structural change in the automotive industry is the shift to alternative drive technologies. The industry’s focus is clearly on electric motors powered either by batteries or hydrogen technology (fuel cells). The combustion engine will continue to play a role in the future, however – at least for some types of vehicles, such as commercial vehicles that require a long range or off-road vehicles, such as agricultural vehicles. Green fuels include biofuels and synthetic fuels (see Energy).
Petroleum is not just used in the form of petrol, diesel or lubricants. It is also the material from which many car parts are made: from paint to large interior parts, electronic components and displays. Around 10% of the German annual plastic production volume is used in the automotive industry. The main reason for the popularity of plastic is that it is light, easy to shape and has good thermal and sound insulation properties. Hybrid parts made of a combination of metal and plastic are also used. Some plastics are even robust enough to substitute metal.
The automotive industry is very much concerned with resource efficiency, lightweight construction and the circular economy. Carmakers are increasingly looking towards bio-based alternatives with a view to designing more resource-efficient vehicles and to making the production processes more sustainable. Plant fibres, bio-based plastics and natural fibre-reinforced composites for lightweight construction are used in the interior and body.
Actually, natural fibres have long been used in arm rests, luggage compartment floors and insulation. Fibres from coconut, beet or coffee grounds can be used as fillers. Natural fibre is also a popular material for reinforcing lightweight components such as the dashboard or the internal panelling of the car boot and doors, as well as in the car body. Materials made of flax, sisal or similar do not splinter easily, which is an advantage during processing and when accidents occur. Biocomposites contain plant fibres which are embedded in a petroleum- or bio-based plastic matrix.
According to the nova-Institute, around 150,000 tonnes of biocomposites were used by the European automotive sector in 2018. Volkswagen’s subsidiary Seat, for instance, is running a pilot project using Oryzite, a biocomposite made from rice husk, polyurethane and polypropylene. The material is to be used in tailgates, in the load floor and in the roof lining.
Car manufacturers are also turning to bioplastics. These are either so-called drop-in solutions or novel and biodegradable bioplastics (see chapter Chemistry). Bio-based polyamide made from castor oil is used in high-performance components, polylactic acid (PLA) in interior door panels, soy-based foams in seat cushions and armrests. One of the challenges when using bioplastics in automotive construction lies in their processability. This is why research and development often focus on how existing injection moulding processes can be adapted for the production of bio-based car parts. In addition, there is rising research interest in the recyclability of bioplastics.
The Institute for Bioplastics and Biocomposites (IfBB) of the Hochschule Hannover - University of Applied Sciences and Arts is working with all the major car manufacturers and companies along the value chain to pave the way for the development and industrial-scale production of bio-based materials. One example is a new project funded by the BMEL, which investigates the suitability of bioplastics for parts that are exposed to high temperatures and stress.
Self-repairing corn-based lacquer
Nanotechnology researchers have been working on self-repairing lacquers for more than a decade. In a project funded by the BMBF, researchers from the Leibniz Institute for New Materials in Saarbrücken and Saarland University developed a self-repairing vehicle lacquer using ring-shaped derivatives of corn starch, so-called cyclodextrins, which are threaded – like pearls – onto plastic molecules with long synthetic chains. When heated, the pearls become mobile and can compensate for gaps in the material, thus repairing superficial scratches. Paderborn University, in collaboration with PPG Hemmelrath Lackfabrik, has also been researching a bio-based, scratch-resistant and self-repairing lacquer with funding from the BMEL.
Bioconcept Car is an unusual alliance of a racing team, sports car manufacturers and material researchers. This project of the Reutlingen-based Four Motors racing team, which includes singer Smudo from the band Die Fantastischen Vier, has been around for more than 15 years. The goal is to design and test racing cars that are mostly built from biomaterials and run on biofuels.
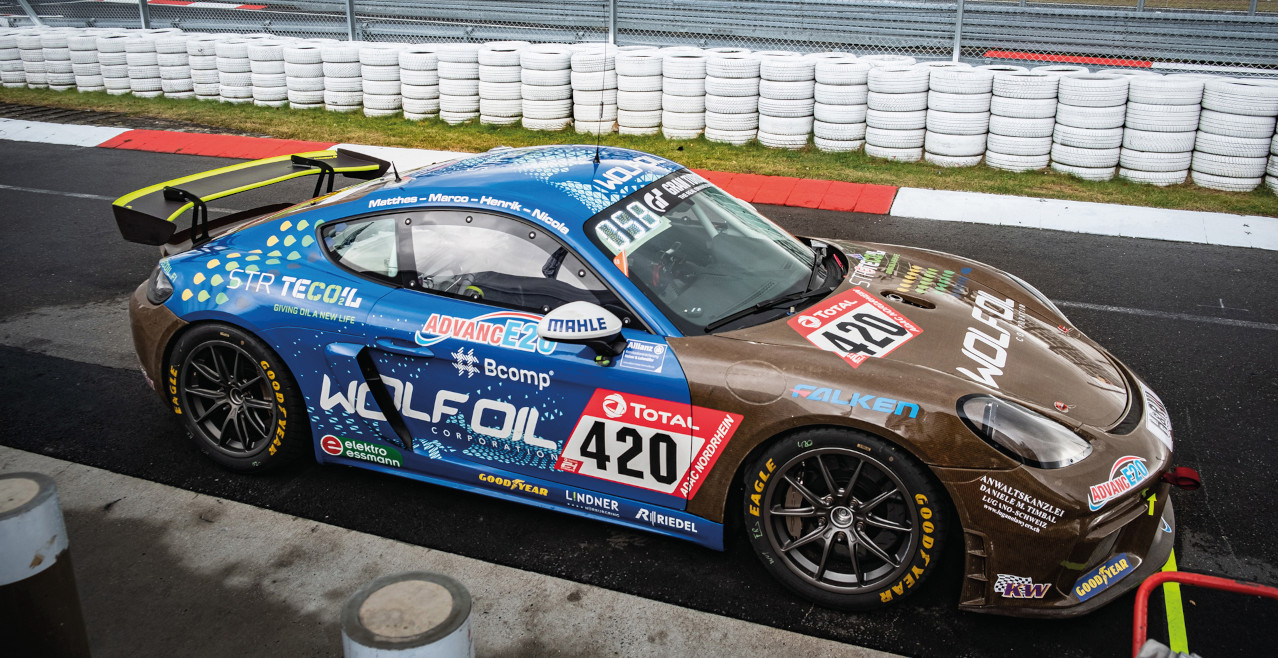
Funded by the BMEL, the project has produced seven concept cars since 2003, which today regularly drive on the test track at the Nürburgring. Four Motors currently races Porsche cars. The Stuttgart-based car manufacturer has already been using natural fibre-reinforced plastics in a small series of the Cayman GT4 Clubsport since 2019. Biocomposites with a 30 to 70% share of renewable raw materials and bioplastic parts have been designed, manufactured and assembled as body and interior components for Bioconcept Cars. In addition to making the cars more eco-friendly, the flax-based natural fibres bring an added benefit: They are lighter than glass fibre and cheaper than carbon fibres. A research network which includes the Fraunhofer Institute for Wood Research (WKI) has developed biohybrid lightweight components for the Bioconcept Car. In a next step, the group comprising Fraunhofer researchers, Hobum Oleochemicals GmbH, Porsche Motorsport and Four Motors wants to develop a vehicle door with 85% of biogenic materials using a resin and lacquer composite.
Rubber is in great demand and can be produced either petrochemically or on the basis of natural rubber. The latter is obtained from the milky sap of the rubber tree (Hevea brasiliensis), which mainly grows in plantations in Southeast Asia. Natural rubber remains elastic even at low temperatures, which makes it the ideal material for winter tyres. However, forests have to be destroyed to make way for rubber plantations, and long transport routes make for high consumption of resources and CO2 emissions.
Russian dandelion (Taraxacum koksaghyz) is a possible alternative source material which also grows in our moderate climate. The rubber from the milky sap of dandelion roots has the same molecular weight and elasticity as that from the rubber tree, and can be processed in exactly the same way. For many years, researchers from industry and science have been working on how to process dandelion rubber at industrial scale. Plant researchers from the University of Münster, the Fraunhofer IME and the tyre company Continental are leading the project.
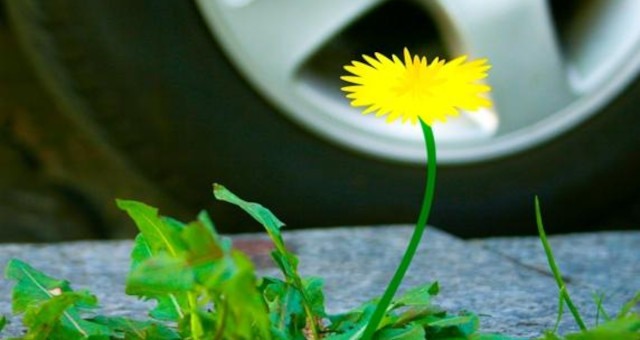
Both the BMBF and the BMEL, as well as the European Union and the state of Mecklenburg-Antepomerania, have provided extensive funding for research and development into the industrial use of dandelion rubber. Their efforts cover the entire value chain: Modern precision breeding methods are intended to produce significantly higher-yielding and more robust plants. The alliance also wants to make the processing steps and the extraction of the plant raw materials more efficient and more sustainable.
For Continental, natural rubber from dandelions has become an important part of its sustainability strategy. The first Taraxagum test tyres for passenger cars were manufactured and tested in 2014, followed by the first dandelion HGV tyres two years later. In 2018, Continental opened its Taraxagum Lab, a research and development laboratory in Anklam / Mecklenburg-Antepomerania, Germany. This is where the first commercially available product was developed: a bicycle tyre, which has been on the market since 2019.