Chemistry
While the chemical industry is still predominantly based on petroleum, a fossil raw material, it is increasingly tapping into biomass, a complex and versatile raw material. More and more companies are turning to green chemical production based on renewable raw materials and biotechnical processes.
Examples of bioeconomy:
Bioplastics, bio-based platform chemicals,
biolubricants
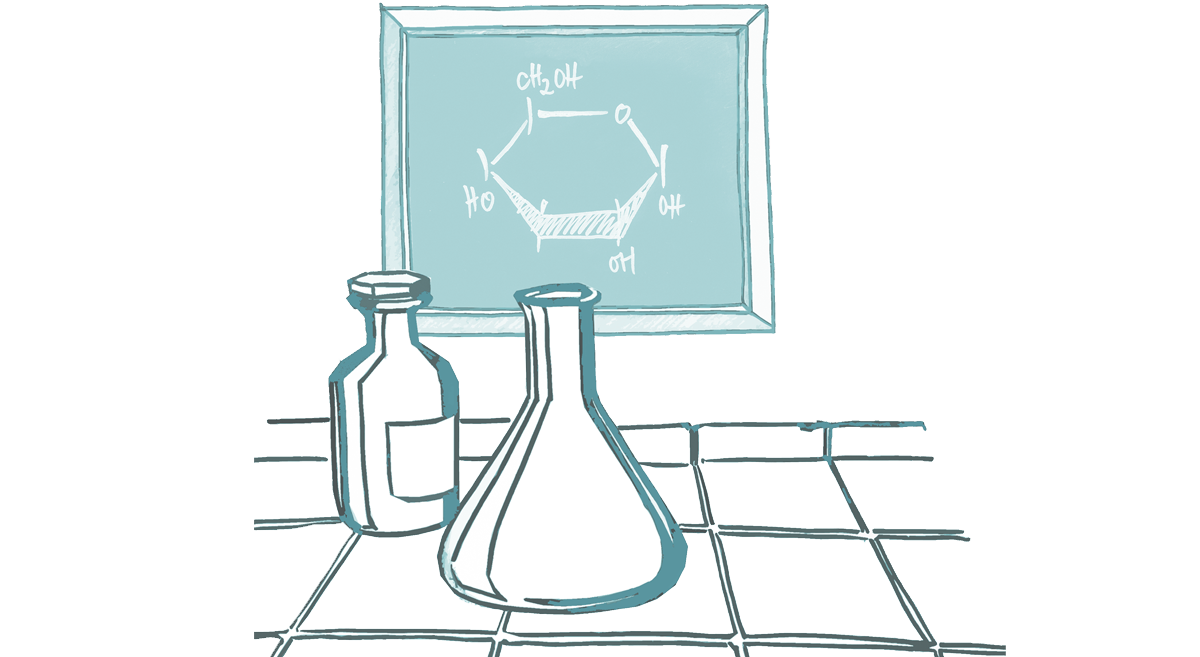
With around 2,100 companies, the chemical industry is one of the most important sectors of the German economy. In 2023, the number of people working in the chemical industry was more than 479,500. Major international corporations such as BASF and Evonik have their headquarters in Germany. These key players generate the bulk of the chemical sector’s annual turnover (2023: 225.5 billion euros). The chemical industry produces and sells a staggering 30,000 or more different products. Key clients include the plastics processing, the automotive, the packaging and the construction industries. Currently, petroleum and natural gas are by far the most important raw materials used by the chemical industry. In 2022, the consumption of fossil resources by the German chemical industry was around 16.4 million tonnes, from which basic chemical building blocks were obtained. These formed the basis of more complex compounds such as plastics, adhesives, varnishes and paints.
Biomass is a versatile mixture of carbohydrates, fats, oils and proteins, which makes it suitable as a raw material for the production of chemicals. In 2019, the chemical industry processed 2.6 million tonnes of renewable raw materials (see chart p.38). Most renewable raw materials used in the chemical industry today are vegetable oils obtained from palm fruits, rapeseed and soya, as well as animal fats. The oils and fats are then processed using chemical synthesis steps to generate bio-based surfactants, which are used in cleaning products, detergents and in cosmetic products (see Consumer goods).
Biotechnical processes also use renewable raw materials. After having been optimised for industrial production, microorganisms use sugar from beet, sugar cane, wood, straw and plant residues to power their cell growth and metabolism. This process is known as fermentation, and the microorganisms produce basic building blocks that can be used for more advanced chemical synthesis or even high-quality end products. Biomass can be the basic material for the production of organic acids, amino acids, alcohols, peptides, therapeutic proteins, enzymes and other biopolymers.
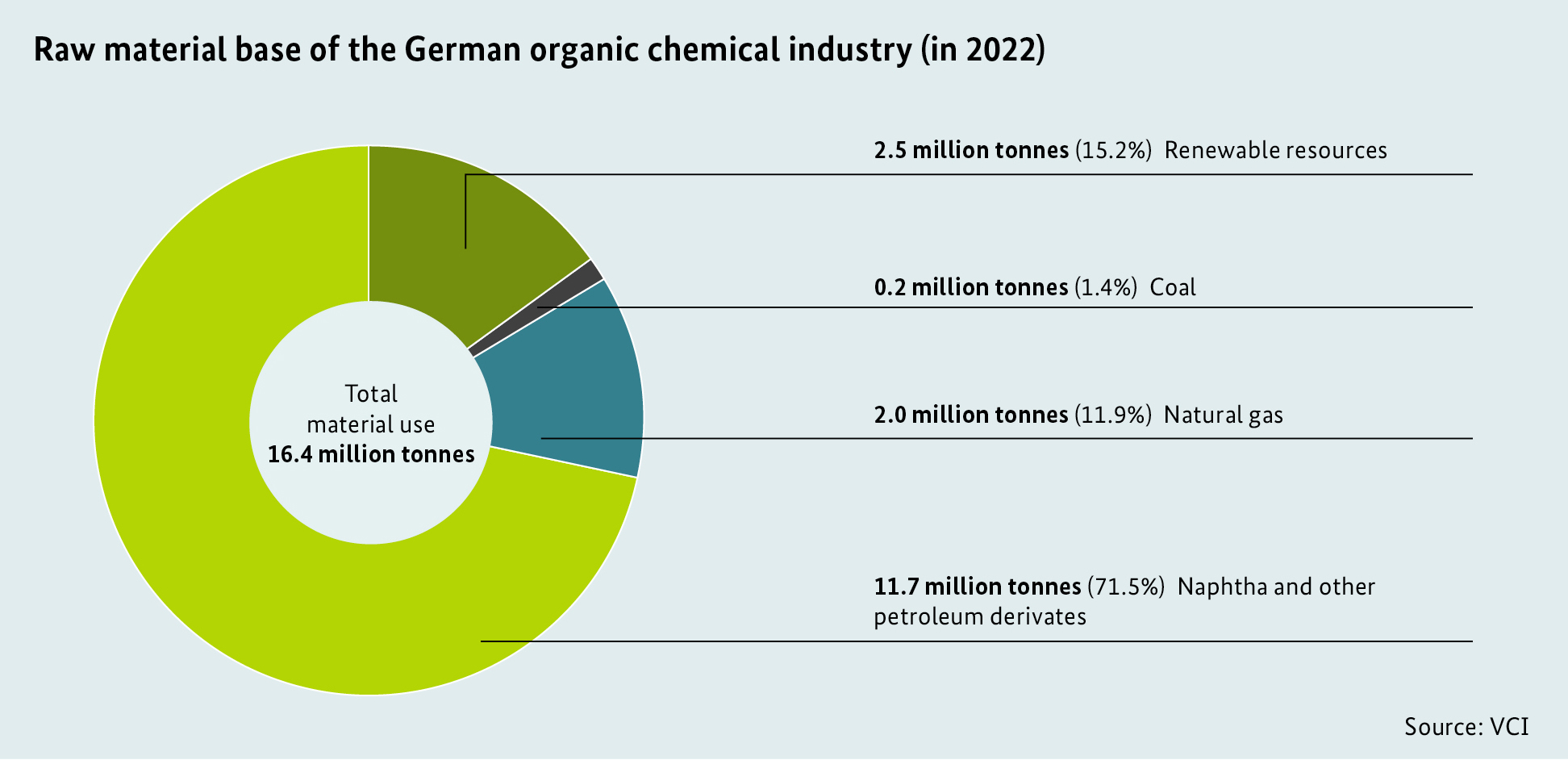
Compared with chemical synthesis, biotechnological production is often the more sustainable strategy because, unlike petroleum-based processes, microbial processes usually require an aqueous solution, and take place at room temperature and under normal pressure. What’s more, microbial processes can produce substances which are difficult to produce using traditional methods. Examples include complex and large protein molecules such as enzymes, hormones or antibodies. This is the core business of industrial biotechnology.
After fine and speciality chemicals, plastics are the second most important product segment for the chemical industry. Plastics are polymers produced from monomers, basic chemical building blocks, that are linked to form macromolecules during synthesis. Increasingly, manufacturers are turning to bio-based alternatives. Currently, about 1% of the plastics produced globally are based on renewable raw materials. According to figures by the European Bioplastics association and nova-Institute, the total volume was around 2.1 million tonnes in 2020.
There are two different types of bioplastics: Firstly, there are biodegradable plastics – but these are not necessarily made from renewable raw materials; some petroleum-based plastics are biodegradable. Bio-based plastics, however, consist of synthetic building blocks derived from biomass. We have to bear in mind that not all bio-based plastics are also biodegradable, though.
Bio-based plastics are mainly used in packaging and bottles, as well as in technical applications such as automotive construction or in the catering and agricultural sectors. Starch and cellulose in particular are important precursors for the production of bioplastics. While the first bioplastics were made from starchy fruits such as corn or potatoes, today, research is focusing on renewable resources that do not compete with food production, such as chitin, chitosan from crustaceans and insects, as well as lignin from woody biomass. These substances are waste products from other industries that have not yet been put to use much. Residues from agriculture and waste streams from the food industry include casein from non-marketable milk, animal fats from slaughterhouse waste and proteins from rapeseed processing.
Drop-in solutions dominate
The world market for bio-based plastics is currently dominated by drop-in solutions. This means that bio-based basic chemicals, which have almost the same structure as the petroleum-based version, are integrated into the chemical synthesis. However, the resulting plastics, such as bio-polyethylene terephthalate (PET) or bio-polyethylene (PE), are not biodegradable. Evonik, a specialty chemicals company, sells PA610, PA1010 and PA1012 polyamides, which are completely or partly produced from castor oil, and which are used in a wide range of applications from the automotive to the textile industry. Covestro, a polymer manufacturer, has managed to produce aniline, an important precursor for many plastics, from plant-based raw materials. A project funded by the BMEL paved the way for bringing the process to industrial scale. In a biotechnological process, microorganisms use chemical catalysis to convert sugar from corn, straw or wood to an intermediate product and then to aniline. Covestro then uses aniline for the production of polyurethane foam for mattresses, insulation materials and car interiors. Plastics additives have also been receiving increasing attention from manufacturing companies. In a project funded by the BMBF, BASF is working with academic research partners from Hamburg and Bielefeld to develop bio-based plasticisers for the sustainable production of PVC. To make the process even more environmentally friendly, special enzymes are used to reduce the energy consumption and prevent the formation of harmful or environmentally damaging by-products.
Is the switch to bio-based processes worth it?
How much sense does it make for a company to switch to bio-based chemical production? The EvaChem research initiative developed a system for finding the ideal production process for bio-based chemicals based on multiple criteria. The system can also be used to assess when a move away from fossil raw materials makes financial sense. Innovation-driven companies should be able to use the system to answer questions about the best possible combination of raw material, synthesis route and target molecule, for example. The aim of the new solution is to provide a reliable scientific basis and a manageable tool for small and medium-sized enterprises. The system was developed by the nova-Institute, Dechema and Leuphania Lüneburg, and was funded by the BMEL.
In addition to drop-in solutions, novel bio-based plastics are on the rise, such as polylactic acid (polylactide, PLA). This bioplastic is obtained from linking lactic acid molecules, a platform chemical produced by microbes. PLA is both bio-based and biodegradable, and is mainly used in films and packaging. A German-Chinese research cooperation funded by the BMBF has established rice bran as a precursor for PLA. The use of this residual material (residual materials from starch or sugar factories are also conceivable) is set to be a decisive factor in making this plastic competitive. Through its ThyssenKrupp Uhde business unit, the ThyssenKrupp Group is currently building its second large-scale PLA production plant in China. The new plant is expected to produce 30,000 tonnes per year.
Even though the fact that bio-based plastics are made from renewable raw material is positive, their recyclability and disposal remain major challenges. Material recycling of bio-based plastics is technically possible, but due to very small quantities of this material being on the market, recycling it is currently not economically viable. As a result, bio-based plastics are being incinerated. The carbon they are made of comes from biomass – not fossil resources –, so the process does not produce any additional CO2, but does require renewable heat and electricity. While German law does not allow the industrial composting of biodegradable plastics, products labelled as “home compostable” may be put on the garden compost.
To establish a recycling system, adjustments in waste management are necessary. Experts emphasise the importance of multiple use, meaning that bio-based plastics should be reused as often as possible before being recycled and finally incinerated. In view of massive plastic waste pollution and microplastics in the soil and groundwater, the creation of plastic cycles remains the major challenge for the industry. In addition to mechanical and chemical recycling, there are now promising approaches using plastic-degrading enzymes for biotechnological recycling.
In 2016 in Japan, a bacterium was first discovered that grows on PET and also feeds on it. Researchers found out that the microbial enzyme PETase, among others, is responsible for the degradation of PET. The enzyme breaks down the plastic into smaller building blocks, while other enzymes split the plastic into its basic components. This ground-breaking discovery gave rise to numerous international and national research projects, such as the research consortium MIX-UP with the involvement of several German partners, which is funded by the EU and coordinated by RWTH Aachen University. The consortium develops processes using molecular-biologically optimised enzymes that efficiently break down PET plastic into its individual building blocks. Microorganisms will then use these components to produce higher-value chemical compounds in a value-added upcycling process.
Biorefineries are the industrial factories of the bioeconomy. Similarly to a petroleum refinery, they break down biomass into its individual chemical components and utilise them as efficiently as possible (see chapter Circular bioproduction). As a rule, material ecycling and energy recovery are coupled with each other to create a wide range of new materials or bio-based chemicals. Different biorefinery concepts are being investigated and developed for commercial use across several German sites.
The Cluster BioEconomy in central Germany is one such example. At the Leuna chemical site, the Fraunhofer Centre for Chemical-Biotechnological Processes (CBP), which was set up with federal and state funding, is testing wood as a raw material in particular. CBP is attracting more and more companies, such as Global Bioenergies, a French company that is looking into new methods for the biotechnological production of so-called light olefins, such as isobutene, propylene and butadiene. The BMBF contributed around 5.7 million euros to the construction of a pilot plant which is designed to produce up to 100 tonnes of isobutene for the production of plastics, elastomers and fuels, for example.
The Finnish forestry and paper company UPM is building the world’s first large-scale biorefinery for the chemical processing of beech wood in Leuna. The refinery, which costs 550 million euros, will break down waste from sawmills and forestry work into its components, sugar and lignin. UPM uses the sugar to extract ethylene glycol, which in turn is used to produce polyester and PET, among other things. Renewable fillers are made from the lignin, which could be interesting for the production of tyres.
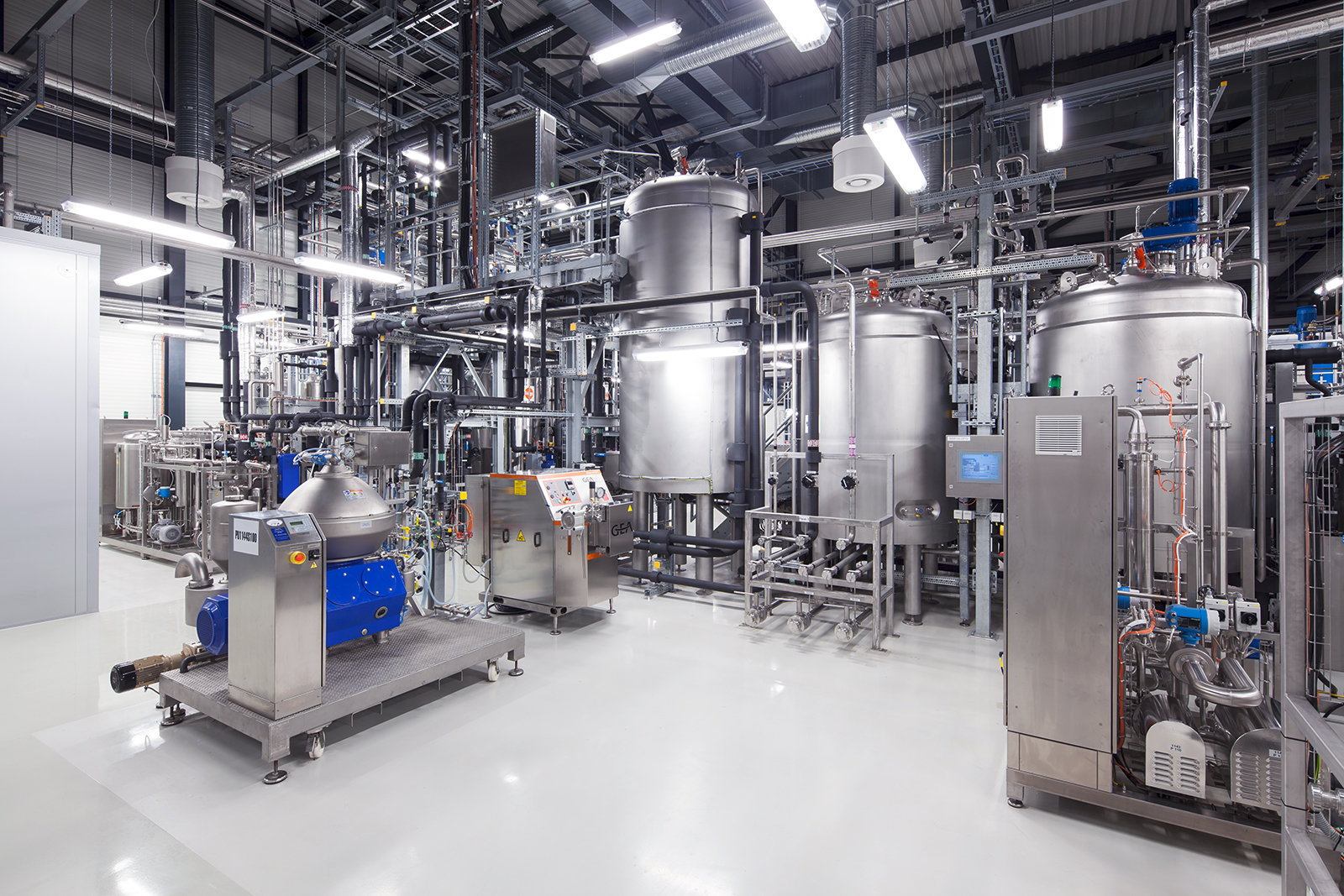
The German chemical industry has been producing approximately 2.5 million tonnes of lubricants annually for many years, and domestic sales in 2020 amounted to around 0.8 million tonnes. The market share of biolubricants is just over 4%. Currently, the most important applications for biolubricants are as hydraulic oils, turbine or engine oils and base oils. Most biolubricants are made from palm oil or palm kernel oil, followed by rapeseed oil, but sunflower oil is also increasingly used. Eight research associations funded by the BMEL are working on improving biolubricants for industrial applications in order to extend their scope of application. These include bio-cooling lubricants with corrosion protection, bio-hydraulic oils based on chitosan and bio-based thickeners for lubricating greases.
Bio-based alternatives for adhesives are also becoming established. One advantage is that they are healthier than petroleum-based products, which may make them suitable for medical applications. Another plus is that they are mostly biodegradable. Last but not least, they often offer new functionalities. According to the German Adhesives Association, the market share of adhesives made from renewable raw materials was as much as 15% in 2017, and may well be higher for some classes of adhesives. The Leibniz Institute for Catalysis in Rostock and Henkel AG are collaborating in a BMEL-funded joint project to develop a new generation of adhesives by 2023. The resulting industrial and consumer adhesives are intended for assembly in the electronics and automotive sectors.
Electricity-driven chemical production
Electrochemical processes can be combined with chemical or biotechnological synthesis processes. It is possible to produce interesting chemical compounds from green electricity and renewable raw materials by electrosynthesis. The BMEL and BMBF’s National Bioeconomy Strategy promotes the development of green chemical production processes. The BMEL has launched a call for funding for “Novel Paths to Electricity-based Conversion of Biogenic Raw Materials and Electrochemical Manufacturing of Biobased Products (Electrosynthesis)”. The German Research Foundation also promotes electro-biotechnology by combining microbial and electrochemical material conversion. Fields of application range from wastewater treatment and soil remediation to the synthesis of chemicals and energy carriers.