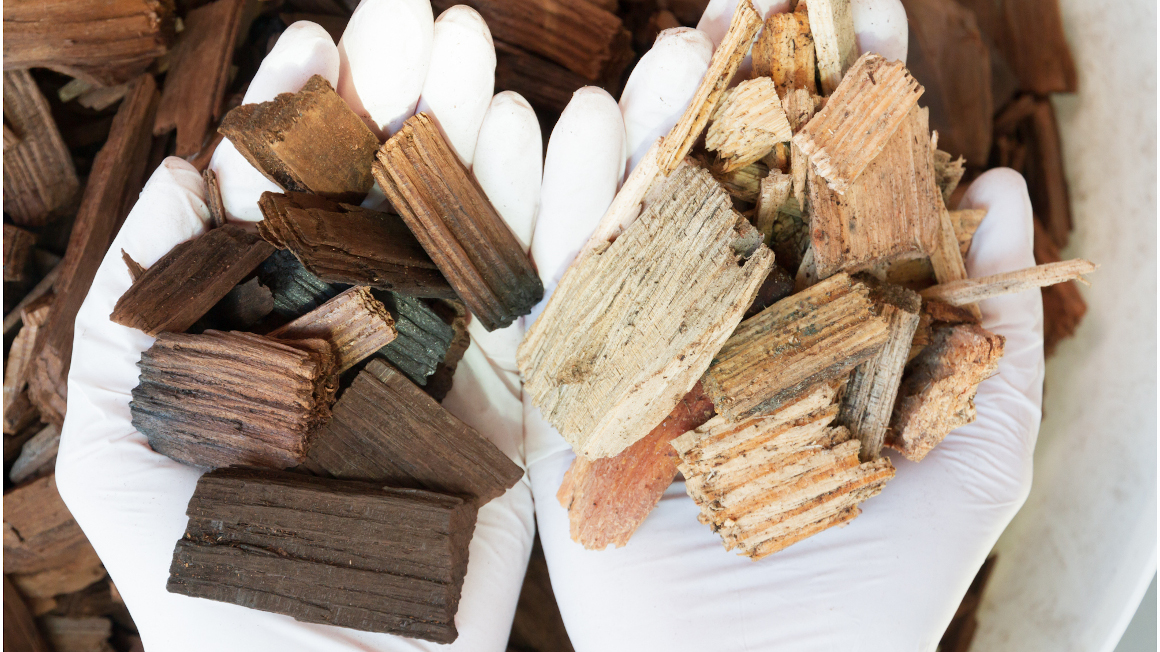
Agriculture and forestry produce enormous quantities of residual materials such as hay, straw, wood or plant residues. The bioeconomy strives for the efficient and sustainable utilization of such raw materials in order to close cycles and thus conserve resources and the environment. Some of these valuable by-products of agricultural and forestry production are already being used to generate energy and materials for the production of new biobased products. However, neither the material nor the energy potential has been sufficiently exploited. The project "The new biorefinery - valorization of condensate streams from the torrefaction of biomass - VALORKON" starts here.
In the joint project "The new biorefinery - valorization of condensate streams from the torrefaction of biomass", researchers have developed a new biorefinery concept that makes better use of residues from agriculture and forestry - especially wood residues. "We wanted to develop a process that is as flexible as possible, can treat many residues, and generates many products," explains project leader Antoine Dalibard of the Fraunhofer Institute for Interfacial Engineering and Biotechnology (IGB). The project was funded by the German Federal Ministry of Education and Research (BMBF) from 2019 to 2022 as part of the Biorefineries Technology Initiative with around 474,000 euros. In addition to the IGB, researchers from Reutlingen University and Heckmann Metall- und Maschinenbau GmbH as a practical partner were also involved.
Thermochemical decomposition instead of fermentation
Biomass is usually recovered for energy in biogas plants in fermenters with the aid of microorganisms. However, the project team chose a different approach: superheated steam was used as a process gas to treat the lignocellulosic biomass. This fermentation-free method had already been developed by researchers from the IGB together with industrial partner Heckmann in previous projects.
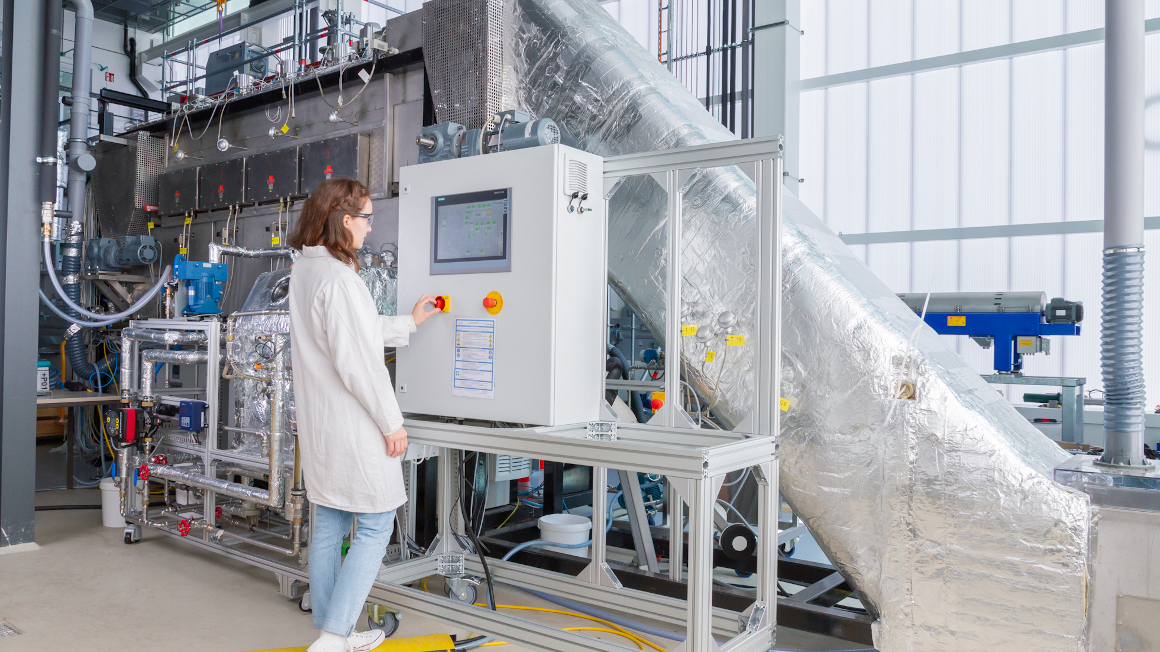
The biomass is heated to between 200 and 300 degrees Celsius with superheated steam in the absence of oxygen and thus torrefied, i.e. thermochemically decomposed. "First, however, the solid matter must be dried in advance of torrefaction. This drying is carried out using the same process and superheated steam," the researcher explains. Drying and torrefaction thus take place in a single plant and each with steam.
Recovery of water during drying and torrefaction
The advantage: during drying, the water bound in the biomass evaporates and can then be completely recovered by condensation. "This allows us to recover the energy we use in the process," Dalibard explains. "Volatiles are also produced in the subsequent torrefaction of the dried biomass as it decomposes, and we condense them as well. This condensate in turn contains valuable materials that we can separate and sell as a product - specifically, basic chemicals."
Platform chemicals obtained with high quality
The recyclables are valuable basic chemicals such as acetic or formic acid, methanol or furfural. The aim of the project was to generate as many of these platform chemicals as possible and to do so in high quality. Using distillation, extraction and electrodialysis, Dalibard's team eventually recovered furfural and methanol from the condensate. "In the extraction of furfural, we were able to achieve a purity level of 90 to 95%," the engineer recounts.
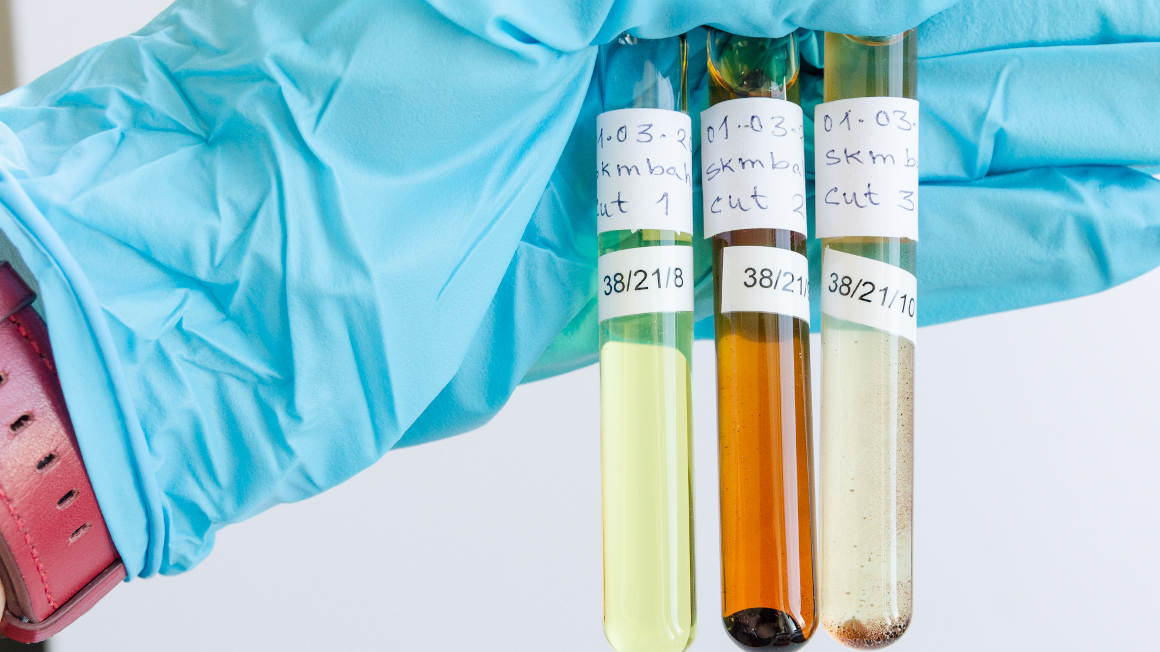
Dried biomass suitable for use as a raw material
Besides the basic chemicals, the torrefied biomass can also be used energetically as a fuel - for example, by burning it in power plants to generate electricity and heat - as well as materially. "There is the possibility of using this torrefied biomass as an input for further processes, for example to produce bioplastics or adsorbents - to remove contaminants from gas streams - or high-value fuels such as biokerosene. But it can also replace coal in the iron industry."
As a result, the project team was able to generate two products from wood residues with the help of the newly developed process - torrefied biomass and basic chemicals. In addition, the water produced during drying can be recycled. With the fermentation-free process, the researchers have also developed a method that can be flexibly adapted to different lignocellulosic residues.
Positive carbon footprint for new biorefinery process chain
The project partners' aim is to bring the combined process for drying and torrefaction of biomass onto the market. The project therefore also investigated whether the process is ecological and economical. Researchers at Reutlingen University have come to the conclusion here that the entire biorefinery process chain already has a consistently positive CO2 balance. Accordingly, the economic potential is also promising.
According to Dalibard, there is certainly no shortage of interested parties. "Since the energy crisis, the number of industrial inquiries has increased significantly," says the researcher. For example, the new process is already being used by a start-up in Estonia. "In February, a prototype of the plant for drying and torrefaction of biomass was put into operation. We licensed the know-how to the start-up."
The researchers are currently in the process of separating organic acids such as acetic and formic acid from the condensate. If further public funding becomes available, a demonstration plant will be built.
Author: Beatrix Boldt