Textiles
The textile industry has always used renewable raw materials, from plant fibres such as linen or cotton to animal products such as wool, silk or leather. With the increasing drive towards more sustainability, bio-based innovations are on the rise. Examples include biotech silk, vegan leather and vegetable tanning and dyeing agents.
Examples of bioeconomy:
High-tech fibres made from spider silk,
microalgae as a raw material for synthetic yarns,
textile coating with chitosan,
leather substitute made from mushroom mycelium,
plant tanning agents
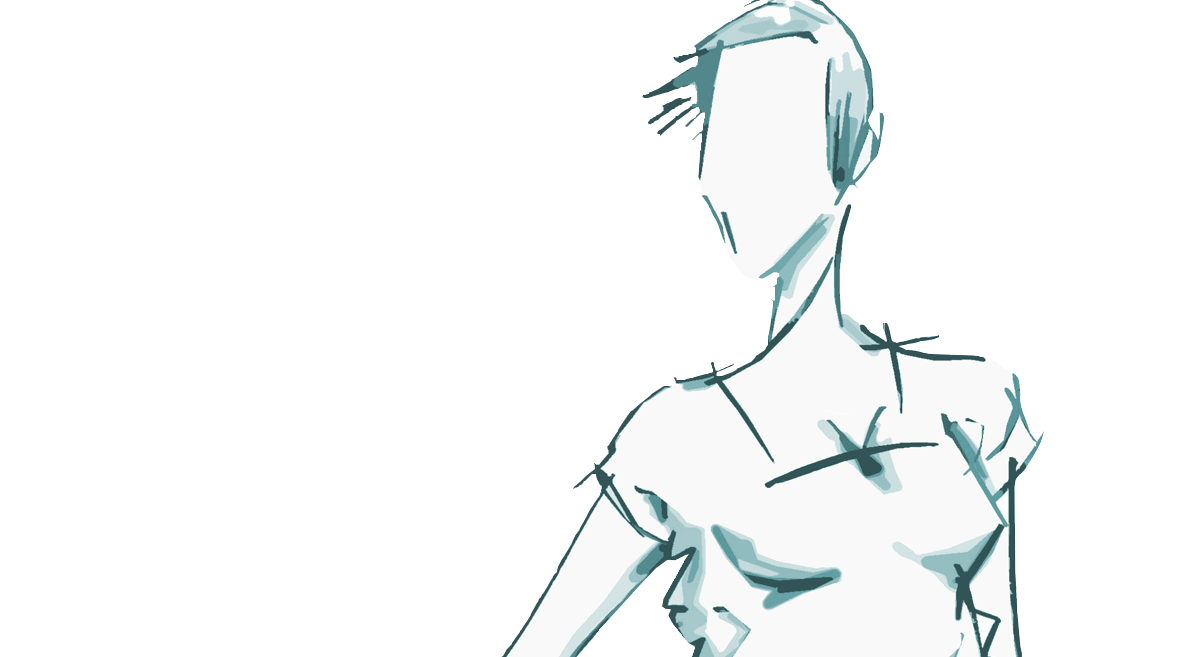
Clothing has been produced from natural products for thousands of years. The manufacture of linen fabrics from flax fibres goes back as far as the ancient Egyptians and Romans. Inexpensive, petroleum-based synthetic fibres have only become established in recent decades. According to the Industrievereinigung Chemiefaser e.V. (Industrial Association Synthetic Fibres), around 108 million tonnes of textile fibres were produced worldwide in 2020. Natural fibres account for 25%, while synthetic fibres make up 75% of global production.
Cotton is by far the most commonly used natural fibre for home and clothing textiles. The entire plant can be utilised: seed fibres for making textiles, cotton oil for cosmetics and plant residues as green manure. Unlike other textile plants such as flax, hemp or jute, the stalks of cotton plants are also processed. However, global production of these bast fibres is much lower, at around 2 million tonnes per year each. Although they can be processed like cotton, they are mainly used for so-called technical textiles in industrial applications rather than the production of clothing. The huge global demand for fabric can no longer be met by cotton. In 1990, the worldwide availability of cotton was 19 million tonnes, which is 49% of the total fibre market. According to the Industrievereinigung Chemiefaser (Industrial Association Synthetic Fibres), the 26 million tonnes of cotton produced in 2020 covered just under 24% of total fibre production worldwide.
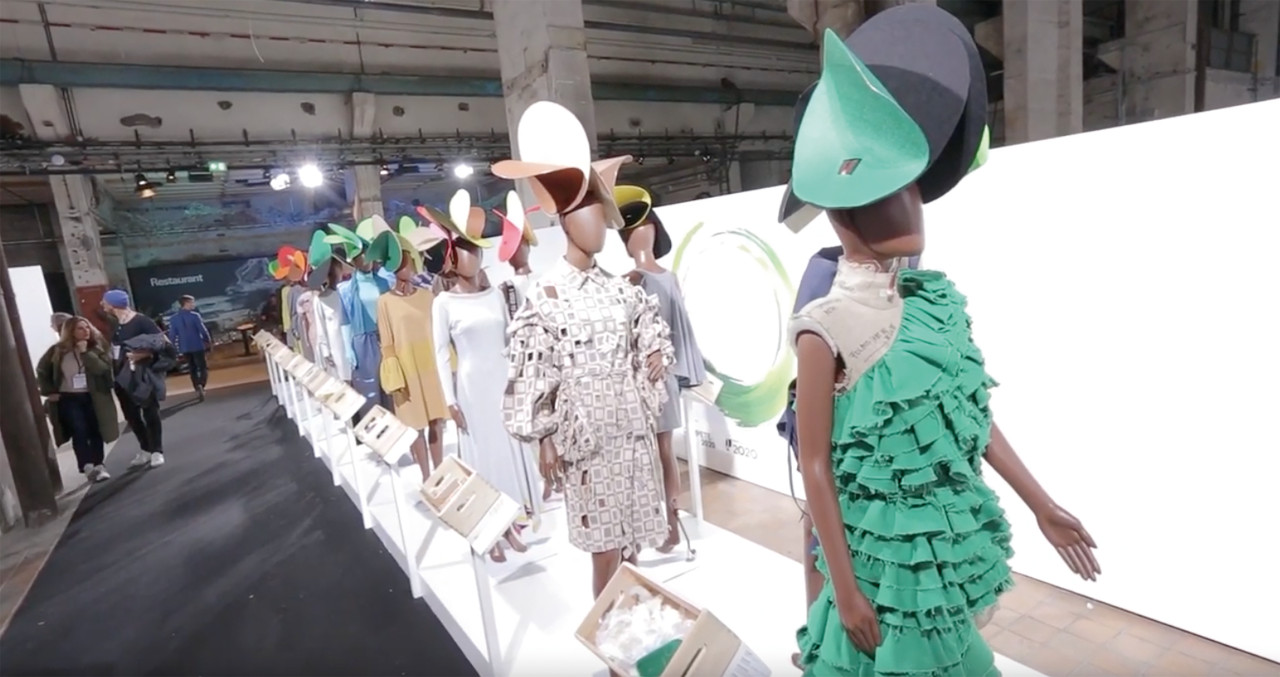
Textile production is resource-intensive and not yet very sustainable, no matter whether it uses natural or synthetic fibres. While synthetic fibres are largely petroleum-based and not easily biodegradable, cotton production consumes large amounts of water and uses massive amounts of pesticides. But textiles use up a lot of resources and damage the environment during their entire life cycle, as the life cycle assessment of a T-shirt carried out by researchers at the TU Berlin reveals. In addition to production, distribution and disposal, washing has the biggest impact on the footprint and uses large amounts of energy and water.
There are synthetic fibres that are based on a renewable raw material – wood. Cellulose regenerated fibres are obtained from cellulose, which is then chemically modified, such as viscose. Even though viscose is chemically identical to cotton fibres, viscose fibres have a wider range of possible fibre geometries (length, crimp, fineness, cross-sectional shape) and can thus be applied more widely. While the production and processing of viscose consumes less energy and water than cotton, it produces toxins such as hydrogen sulphide (H2S) and carbon disulphide (CS2) that are harmful to human beings and the environment.
There are other synthetic fibres made from cellulose whose production is less environmentally harmful, such as lyocell. The direct dissolving process relies on a non-toxic solvent and works within a closed material cycle. The cellulose for lyocell fibres is harvested from eucalyptus or beech wood. These plants grow faster than cotton and have a high yield per area, which gives them a better environmental footprint. Recent research has also shown that flax, hemp, bamboo, banana and soya are also suitable for cellulose pulp.
Bio-based innovation for the textile industry – the BIOTEXFUTURE innovation space
The BIOTEXFUTURE innovation space aims to make the entire value chain of the textile industry more sustainable. To this end, the innovation space provides a network for 75 companies, research institutions and universities. With up to 20 million euros funding from the BMBF, numerous projects are dedicated to the production of bio-based textiles based on sustainable raw material cycles. Project partners include the sporting goods manufacturer adidas, Fraunhofer IGB, RWTH Aachen University and the University of Bayreuth. The Algaetex project uses microalgae as a raw
material for plastic yarns that could potentially be used to make T-shirts and knitted shoe uppers (see photo). Another project is developing a bio-based coating that is water-repellent, antimicrobial and dries faster. The BIOBASE project has set itself the goal of replacing one petroleum-based product with a product made from biopolymers in each of the following areas: automotive, sportswear, interior design and technical textiles. The close ties between the project partners are intended to contribute to consolidating all options along the entire value chain.
The German Institutes of Textile and Fiber Research Denkendorf (DITF) have developed an innovative material made of pure cellulose named purcell. Both the matrix and the reinforcing fibre embedded in this one-component composite material are made of cellulose. This enables an eco-friendly recycling concept with a low environmental impact and carbon footprint. Purcell is manufactured using a novel technology based on ionic liquids. The Federal Ministry for Economic Affairs and Climate Action has supported the DITF researchers. Even waste from the food industry can now be used for textile production. Hanover-based Qmilk Deutschland, for example, produces a biopolymer consisting of the milk protein casein from non-marketable raw milk. The fibres are produced without chemical additives and can be used to make clothing or technical textiles for medical devices or the automotive industry.
Spider silk threads are marvels of nature; they are only a tenth as thick as a human hair, yet twenty times stronger than steel and more elastic than rubber. The natural material is extremely suitable for high-tech textiles. The Martinsried-based company AMSilk has developed a biotechnological process to produce spider silk protein on an industrial scale. The company, founded in 2008 as a spin-off from the TUM in Munich, has converted bacteria into cell factories for spider silk protein. The final step of the bioprocess is a white protein powder that can be spun into fibres by machines (see photo on p. 79). Textiles made from these vegan silk biopolymers are not only particularly hard-wearing and skin-friendly, but also completely biodegradable. Sports clothing company adidas has joined forces with AMSilk and produced a sneaker prototype whose upper material consists of Biosteel fibres (see photo p.78). These biotech textiles have also been used in straps by watch manufacturer Omega.
Finishing textiles with enzymes and biopolymers
Enzymes are used as bio-catalysts for processing or finishing fabrics, for example for bleaching or for achieving the stonewashed effect in denim. Textiles made of synthetic fibres are a challenge for manufacturers, as they form unwelcome pilling on the textile surface after repeated washing. During the FuPol project funded by the BMBF, a strategic alliance including detergent manufacturer Henkel conducted research on how to reduce pilling. The enzyme cutinase was able to reduce pilling and improve the dyeing result at the same time. Not only enzymes, but also biopolymers are being considered for finishing textiles. The ChitoTex research project, led by Fraunhofer IGB and supported by the BMBF, has found a way to coat textile fibres with chitosan in order to make them water-repellent (photo). The biopolymer was extracted from insect skins and could replace previously used chemicals.
Leather is a durable and versatile material that is used for many everyday objects, such as furniture and clothing. However, leather made from tanned animal hides causes pollution and is viewed with increasing scepticism. Consumers are turning to imitation leather made from pineapple fibre, apple pomace or cactus leather, which are considered to be more sustainable. However, these materials always contain some petroleum-based plastics, such as polyvinyl chloride or polyurethane. Another new alternative are leather substitutes made from fungi which are cultivated on residues from agriculture and forestry, such as sawdust or molasses. The growing fungal network, the mycelium, creates fungal biomass, which can be processed into a material that looks and feels almost exactly like leather. Some biotechnology companies have already started marketing the materials obtained from fungi. adidas for example has produced a prototype of a vegan sports shoe using a fungal mycelium material called Mylo instead of leather. It is manufactured by the US company Bolt Threads from California. The Leipzig-based start-up ScobyTec has also developed a biotechnical process in which microorganisms produce bacterial nanocellulose (BNC), a nonwoven fabric that can be used instead of leather.
There are also some bio-based innovations in leather tanning. Chromium salts, which are harmful to the environment and health, are increasingly being replaced by plant-based tanning processes. One example is Rhubarb Technology, a start-up that has extracted a substance suitable as a tanning agent from the roots of rhubarb plants. wet-green, a company from Reutlingen, makes a tanning agent from olive leaves, which was developed in collaboration with N-Zyme BioTec. Textile dyeing is also turning to plant-based raw materials, using traditional plant dyes in order to make textile dyeing more sustainable. Dyeing plants such as madder, reseda, bluewood, gardenia and jasmine flowers have proven to provide effective dyes. In a project funded by the BMEL, two vegetable dyes for printing on silk and modal fabrics were developed. The spring 2019 collection of hessnatur already featured two silk blouses that had been printed using the colour pastes developed in the project.
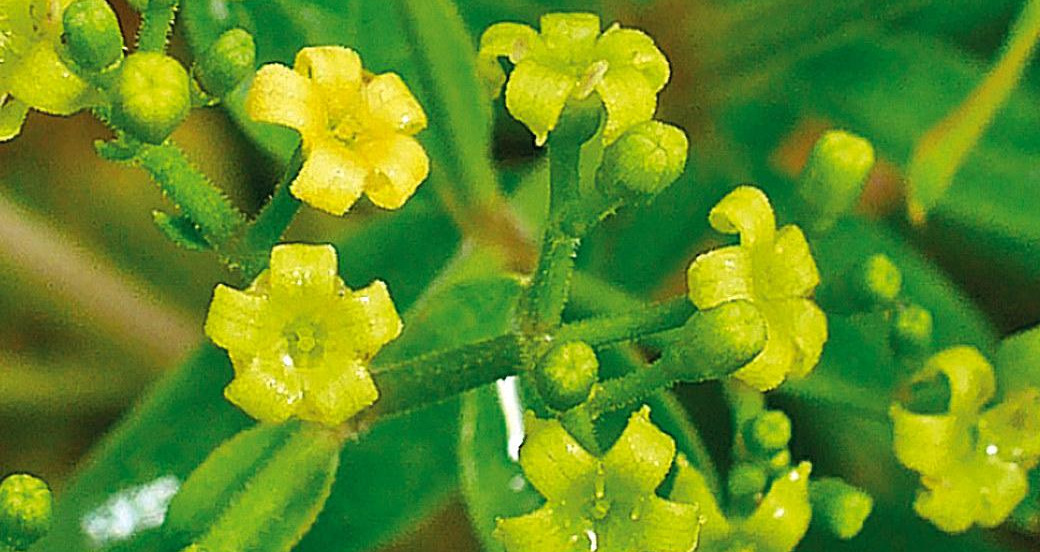
According to the Bundesverband Sekundärrohstoffe und Entsorgung e. V. (BVSE - German Association for Secondary Raw Materials and Waste Disposal), approximately one million tonnes of clothing end up in clothing banks every year. Clothes that are no longer wearable are usually turned into cleaning rags or painter’s fleece. However, a sustainable circular economy in which textile fibres are recycled has not yet been created. Researchers at Fraunhofer IAP have found a way to produce a high-quality fibre from used cotton textiles. This had previously not been technically feasible because most clothes are made of mixed fibres. The researchers have developed a process for filtering cellulose from the cotton to create a viscose filament yarn consisting of 100% cellulose. The quality of these recycled fibres is comparable to wood-based cellulose regenerated fibres and has the same quality as viscose fibres.
Knowing each type of fibre and understanding the fibre composition is a prerequisite for recycling textiles. The DiTex project is testing the quality, resources and sustainability of workwear and towels made from recycled fibres as part of a pilot project funded by the BMBF. For this purpose, the textiles were equipped with an intelligent label that stores parameters such as material mix, fibre origin as well as washing and recycling cycles. This allows tracking and analysing the complete life cycle of the textiles, including all environmental aspects.