Consumer goods
Whether cosmetics, dishwashing and washing detergents or household appliances – a wide range of bio-based processes are already used in the production of everyday products. They enable the development of innovative consumer products with new features. Bio-based packaging solutions are also becoming increasingly popular.
Examples of bioeconomy:
Bio-based surfactants,
bioactive ingredients for cosmetics
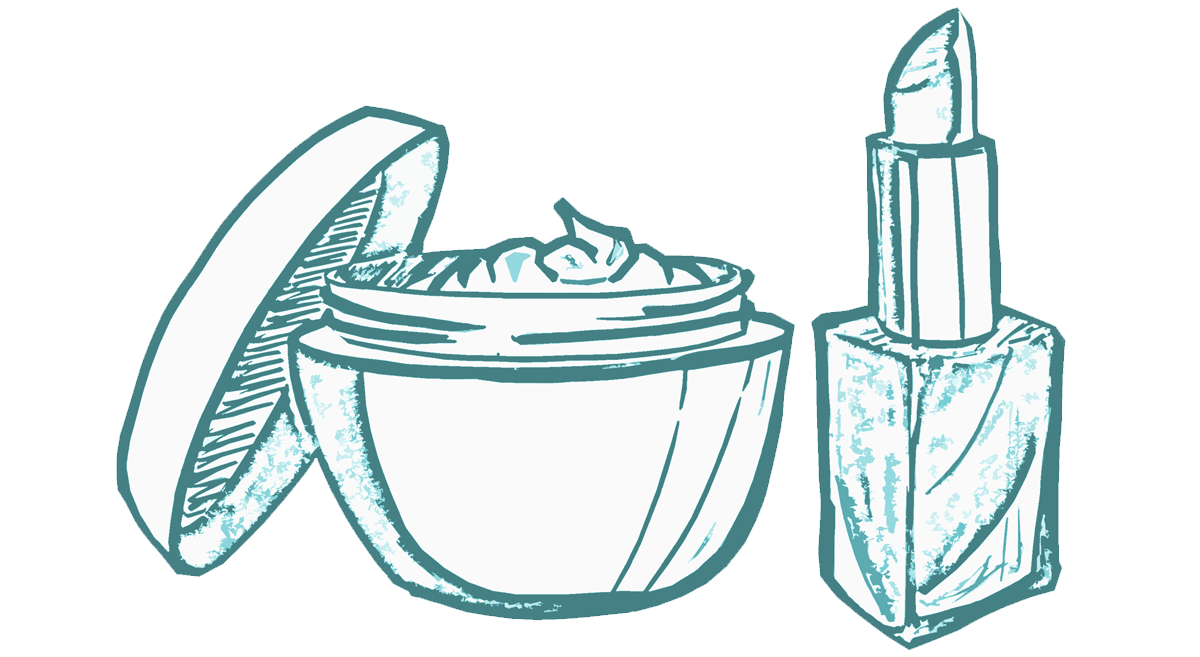
According to the Federal Statistical Office, private consumption in Germany amounts to around 31,000 euros per household. With around 14 billion euros, clothing and food as well as personal care and hygiene products accounted for the largest shares of private consumption in Germany in 2020. Around 4.6 billion euros were spent on detergents and cleaning products. The bioeconomy has been an intrinsic part of the consumer goods industry for some time. Many industrial manufacturing processes rely on natural raw materials or bio-based processes.
The latter are already particularly prevalent in the production of detergents, care products and cleaning agents, with more than one third of all ingredients (total of 525,000 tonnes) having been fully, or partially, bio-based in 2019 (IKW Sustainability Report). These ingredients include surfactants, alcoholic solvents, enzymes and citric acid. The entire production of citric acid today is already based on fermentation using moulds with molasses, a by-product of sugar beet -processing, as the substrate.
Surfactants are indispensable components of cleaning agents, detergents and cleaning products that are produced either from petrochemical, or from renewable raw materials. Mixed surfactant systems consist of both petrochemical and bio-based raw materials, mainly vegetable oils and animal fats (see chart p. 74). Most surfactants produced through chemical synthesis are based on palm kernel or coconut oil. According to the digital platform Forum Waschen, the amount of coconut oil used in the production of surfactants for detergents, care products and cleaning agents in Germany was estimated at 14,000 tonnes in 2017. The share of palm kernel oil reported by the Forum for Sustainable Palm Oil was 75,000 tonnes in 2019. To reduce the impact on the environment, German producers have been turning to European oil crops such as rapeseed, olive, linseed and sunflower, or to sustainably produced tropical oils.
Biosurfactants are surfactant molecules that are biotechnologically produced using microorganisms or enzymes. While there are only a few products containing biosurfactants on the market, their potential is thought to be considerable. Specialty chemicals group Evonik is among the pioneers in the field of rhamnolipids, a type of biosurfactant naturally produced by bacteria. Biotensidion is a start-up based in Karlsruhe which develops biosurfactants. The strategic Innovation Alliance for Functionally Optimised Biosurfactants aims to promote the biotechnological production of biosurfactants from domestic renewable raw materials. The BMBF has been funding the alliance since 2018 as part of the Innovation Initiative Industrial Biotechnology with 6.4 million euros over a period of six years. Research institutions and companies have joined forces to cover the entire value chain of biosurfactant production.
The consortium includes BASF, Henkel, Festo and Analyticon Discovery and is coordinated by Dalli-Werke, a cleaning products and cosmetics manufacturer. The alliance is looking to develop a wide portfolio of different biosurfactants for many application areas (such as detergents and cleaning agents, cosmetics, crop protection and food), and to boost productivity and make the process scalable.
Enzymes are essential ingredients of detergents and cleaning agents. This segment of the consumer goods industry accounts for the largest market share (40%) of industrial enzymes. The use of these biocatalysts in detergents over many years has certainly helped to save water and energy, making laundry management much more environmentally friendly. Since enzymes are often active at moderate temperatures, it has become possible to reduce the average washing temperature to 46 °C from 63 °C in 1972.
Today only 7% of all washes are at 90 °C, compared to about 40% more than 40 years ago. Biocatalysts have also increased the efficiency of detergents: While in the past 220 grams were needed for a 5-kilogram wash, today 75 grams are sufficient. According to the German Cosmetic, Toiletry, Perfumery and Detergent Association, around 7,100 tonnes of enzymes were used as ingredients in detergents and cleaning products in 2019, compared to only half that amount in 1994.
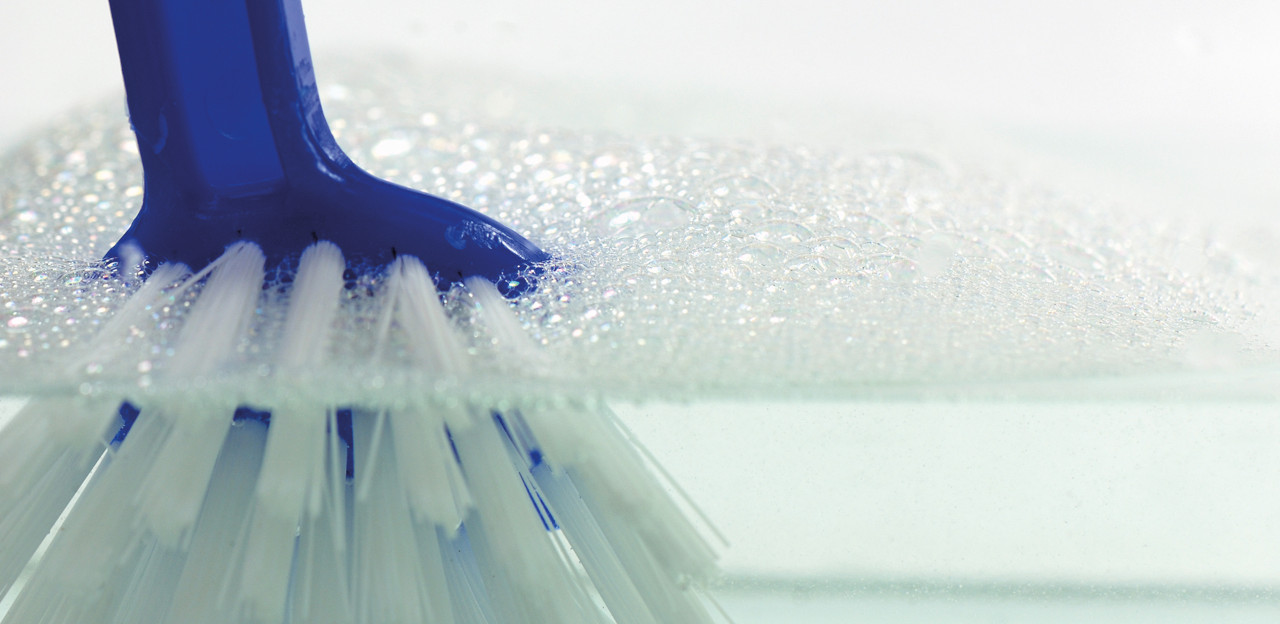
In response to a growing demand for natural cosmetics, manufacturers have been using special bioactive ingredients in personal care products for some time now. According to the Federal Statistical Office, 34% of Germans much prefer natural personal care products without chemical additives, which is why more and more cosmetics producers are using natural and sustainable raw materials and active ingredients.
Microorganisms or cells are used as living biofactories in biotechnical production. Bioactive ingredients that are biotechnologically produced include peptides, lipids, vitamins and sugars or enzymes. Brain, a biotechnology company from Zwingenberg, uses bacteria to produce the preservative perillic acid from terpene derived from orange peel. In 2018, fragrance and flavour manufacturer Symrise from Holzminden introduced a pentylene glycol which is derived from bagasse, a by-product of sugar cane processing. The green alternative is the result of a collaboration with the Leibniz Institute for Catalysis at the University of Rostock. Another strategic alliance funded by the BMBF develops bio-based cosmetics: GOBI - Good Bacteria and Bioactives in Industry bundles research findings on the health-promoting effects of living micro¬organisms and makes the information accessible for industrial application. The network is coordinated by the biotechnology company Novozymes Berlin (formerly Organobalance).
Plastics are key materials for the consumer goods industry. However, plastic waste mountains and microplastics in the food chain have brought us to the realisation that plastic products and packaging are actually a global challenge. This is why bio-based and biodegradable alternatives are receiving more and more interest (see chapter Chemical industry). The range of products for which these alternatives are being investigated goes from electrical goods to office supplies to sports equipment. Tecnaro, a Fraunhofer spin-off, specialises in plastics made from renewable raw materials. With the support of the BMBF, amongst others, the company has developed a thermoplastic bioplastic, ARBOFORM. This “liquid wood” can be used to produce a wide variety of products, including toy figures or storage boxes. In another project funded by the BMEL, FKuR Kunststoff has joined forces with several research institutions to develop new bio-based hard-soft composite materials that can be processed using multi-component injection moulding to make office equipment, personal care items and sports equipment as well as handles and housings. The hard phase of the new material consists of cellulose acetate (CA) and polylactic acid (polylactide - PLA), while the soft phase is based on termoplastic elastomers (Bio-TPE) and bio-based ethylene propylene diene monomer rubber (Bio-EPDM).
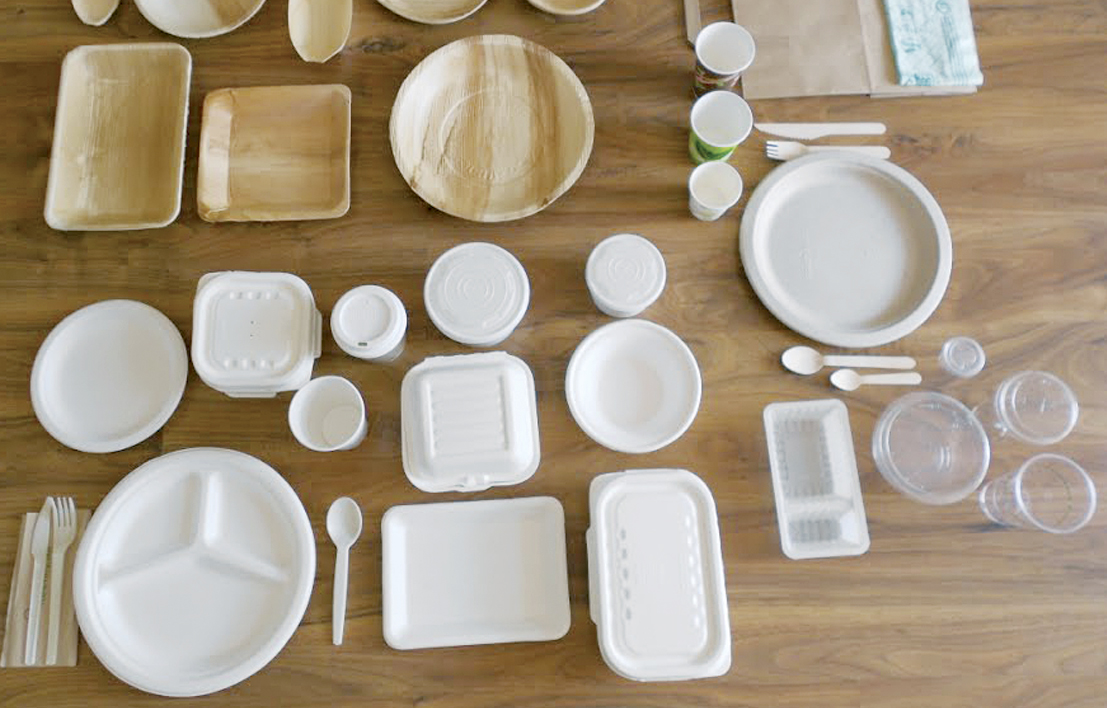
New EU plastics directives and corresponding national laws as well as consumer pressure are forcing companies to optimise packaging materials in terms of recycling, recyclability and sustainability. In the food and pharmaceutical sectors in particular, the requirements for packaging are very high because they need to be robust and protect the contents from dirt, moisture and microbial contamination, while preferably also being recyclable. For bio-based plastics to meet these requirements, the BMEL is funding several application-oriented research approaches. The BioPrima project by Südzucker AG and its partners is developing a starch-based shrink film that is suitable for freezing. The Fraunhofer Institute for Process Engineering and Packaging IVV and the Albstadt-Sigmaringen University are working on a bio-based and recyclable packaging concept for sensitive food that is packaged in a protective gas atmosphere. The Fraunhofer Institute for Silicate Research ISC is working with industry partners to develop bio-based high-performance barrier films that are 95 to 100% bio-based and recyclable.
Industry demand for paper-based packaging is also high. Two projects funded under the BMBF ideas competition New Products for the Bioeconomy are developing innovative solutions for this. One of the projects is the BioBox, made entirely of innovative wrapped paper with the required barrier properties for protecting the content. Another project is testing thermoformable paper materials to produce three-dimensional structures. There are some companies that have started making paper from grass fibre, as an alternative to wood. Agricultural residues can also be used as a source of fibre. The cleantech start-up BIO-LUTIONS from Hamburg is working with Zelfo Technology GmbH to develop a mechanical process for the extraction of fibre from wheat straw, rapeseed straw, reeds and vegetable stalks. The resulting fibre pulp can be pressed into a variety of shapes, for example for packaging and tableware. A production facility is currently being built in Schwedt, Brandenburg.