Mechanical engineering
Germany is a global leader in mechanical engineering. Modern machinery, devices and processes can help make production sustainable and efficient in any industrial or economic sector. This is why innovation in mechanical engineering is an important driver of the bioeconomy.
Examples of bioeconomy:
Bioprocess technology, agricultural technology,
measurement and control technology
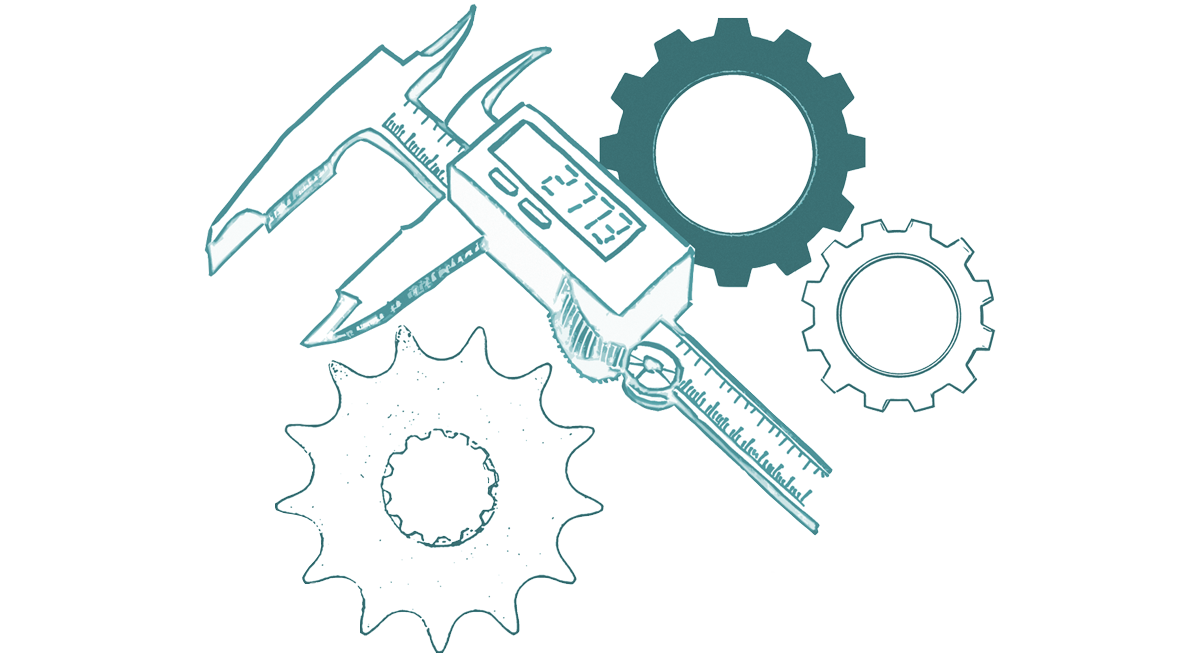
Mechanical and process plant engineering has always been one of the mainstays of the German economy. In a bio-based economy, technical systems, machines and process technology are essential for resource-efficient and sustainable management. The particular engineering challenge lies in having to reconciliate technical and biological requirements. Depending on the specification, biological materials require dedicated machines, plants or processes. Digitalisation and automation – such as robotic solutions – drive innovation in mechanical engineering and combine mechanical engineering and machines in smart networks.
Biotechnological production processes rely on living cells to make chemicals, medicines, food additives and cosmetic ingredients. Conditions have to be very particular in order to ensure the optimal performance and reproduction of these sensitive cell factories. Bioreactors – or digestors – are the heart of every biotechnological production plant. Developing these plants, operating them at industrial scale and optimising the processes requires sophisticated bioprocess technology. This is where the art of engineering and knowledge about biology meet, with the level of knowledge of industrial biotechnology at German universities, research institutions and in industry being outstanding. Today, new findings in bioprocess engineering provide the basis for designing particularly efficient plants that are characterised by low energy requirements or high efficiency, for example. In addition, there are special requirements resulting from new production strains and organisms, such as algae.
Biorefineries are the major industrial factories of the bioeconomy. In these complex technical facilities, plant biomass is broken down into its components and utilised – analogous to a petroleum refinery. The biorefinery concept is being researched and developed at several locations across Germany.
One such research initiative is the BMEL-funded research association EthaNa, which has developed a holistic concept for rapeseed utilisation – from peeling the rapeseed to breaking down the rapeseed kernels to the fractionated extraction of oil, proteins and other ingredients. With this process, reusable rapeseed-based materials can be used for technical or cosmetic products. The process can be integrated both in conventional oil mills and in vegetable oil biorefineries.
The key challenges facing bioprocess technology are the continuous monitoring of the bio-based production process and the purification step at the end of the process chain. The industry is also lookingto improve resource efficiency in order to cut costs. These are the kinds of issues investigated by a strategic alliance for knowledge-based process intelligence which is being funded by the BMBF and coordinated by Sartorius Lab Instruments GmbH & Co. KG in Göttingen for the creation of a novel sensor and software platform. Another BMBF-funded project is DigInBio, a joint project of Forschungszentrum Jülich, the Technical University of Munich and Leibniz University Hanover for the establishment of digital and automated processes in the biotechnology laboratory (see Pharmaceuticals).
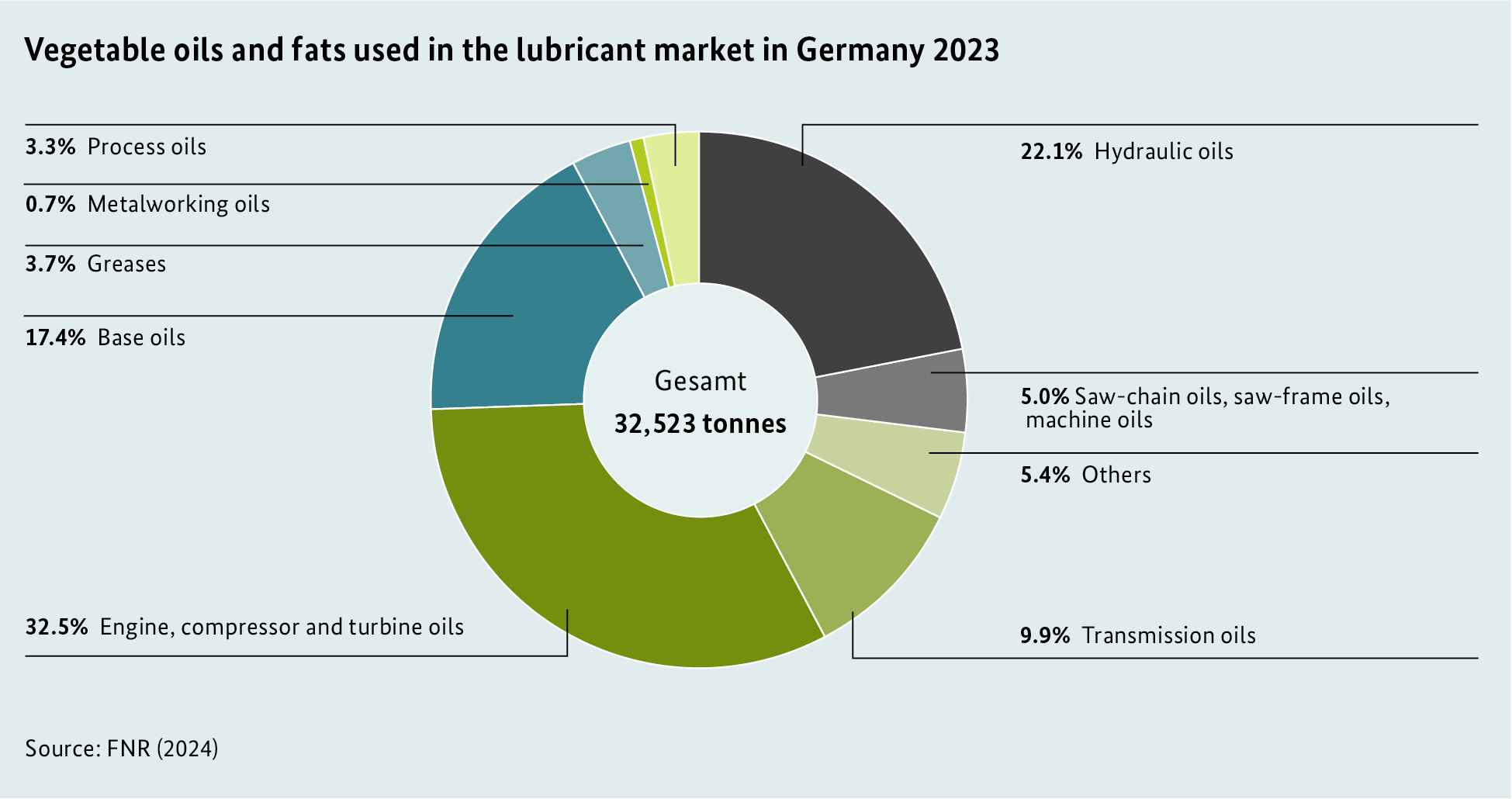
Today, there are products made from renewable raw materials for all lubrication and pressure transmission applications (see chapter Chemical industry). These products are biodegradable, environmentally friendly and have excellent performance data. In 2023, production in Germany amounted to 32,500 tonnes, with the main raw materials being palm oil, palm kernel oil and rapeseed oil, followed by animal fats. Sunflower oil and residues such as used frying fat are currently playing less of a role, but their share is growing. The BMBF-funded project ZeroCarbFP investigated ways of using enzymes to break down used frying fat from the catering industry for the production of lubricant additives. Another BMBF-funded project, PHAt, has come up with biodegradable thickeners and binding agents for lubricants and lubricating varnish from polyhydroxyalkanoates, which are naturally produced by various bacteria. The BMEL, too, launched a funding initiative in 2019 to further bio-based lubricants and hydraulic oils, which provides 6 million euros to eight collaborative projects covering 31 individual projects. The goal is to develop components and additives for cooling lubricants used in metal cutting and forming, as well as thermally resilient plant-based greases for roller bearings and stationary or mobile hydraulic systems.
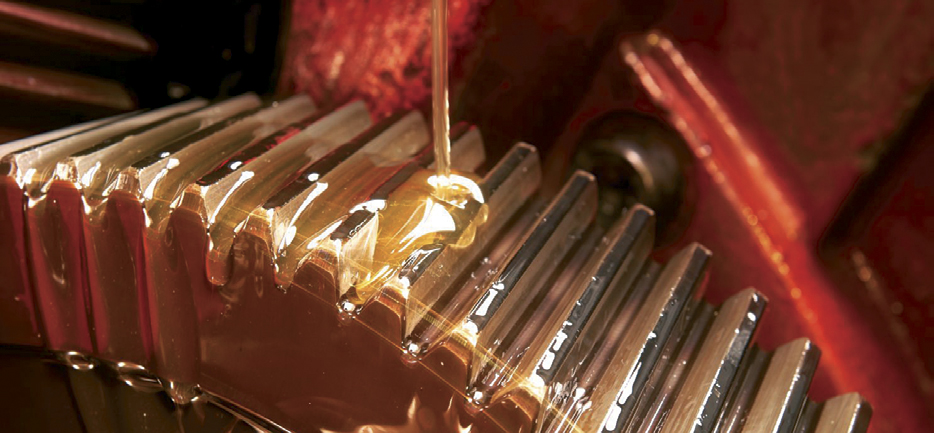
To meet the growing demand for bio-based plastics and (partially) bio-based composites, production technology has responded to the new requirements by adapting compression moulding and injection moulding processes. Forming multidimensional components presents a major challenge because wood and natural fibres have a lower density than the mineral fillers or reinforcement materials traditionally used. The BMEL-funded Biopolymernetzwerk (Biopolymer Network) responded to these challenges by investigating how the sandwich injection moulding process can be adapted to working with partially bio-based composites.
The Biopolymer Network was succeeded by the Zukunftsnetzwerk biobasierte Polymere (BioFoN) which provides a knowledge-sharing network for experts with the long-term goal of creating a fully bio-based plastics industry. Network partners work together on projects such as the development of new production processes for bio-based packaging, or for violin bows made from natural fibre composites. 3D printing is also growing in popularity across industries and is increasingly switching from traditional plastics to bio-based raw materials. One example is the production of 3-D printed wooden furniture as part of a BMEL-funded project. The construction industry is also benefitting from these new developments: For example, lightweight components made of wood or flax can be designed on a computer and manufactured by robots (see construction).
Process plant engineering and process engineering are not the only parts of the mechanical engineering industry that could contribute to the bioeconomy. The digitalisation of all economic sectors goes hand in hand with increasing automation and intelligent networking of systems.
In the agricultural industry for example, precision agriculture has become much more important in recent years (see chapter Agriculture and forestry). Mechanical engineering provides innovations in measurement and control technology as well as in automation processes that can help make agricultural processes more sustainable – both in crop cultivation and in animal husbandry. This also includes robotics solutions such as field robots, which could be used for heavy and monotonous work in particular, or when precise work is required over a long period of time – such as fertilising or sowing. There are also some promising approaches in the cultivation of fruit and vegetables, such as watering and harvesting robots. Even delicate fruits such as strawberries or gherkins can now be picked by robots. Animal husbandry is also looking to automated solutions such as milking robots or automatic feeding systems. The machines help to use resources more efficiently, especially in large agricultural operations.
High-tech equipment can be the basis for sustainable agricultural production in greenhouses or indoor farming systems for urban farming. In indoor farming systems for example, hydroponics is combined with modern LED lighting technology, heating and ventilation systems, sensor technology and intelligent information technology in order to be able to use resources as effectively as possible (see Agriculture and forestry).
Food processing also relies on engineering expertise to become more resource-efficient and sustainable, with smart automation processes being in particular demand. The German Institute of Food Technologies is working on developing hygienic gripping techniques that can be used for a variety of applications. Process analytics also has an important role to play. It records and determines the quality of finished products or supplied goods and provides a system for process tracking and control, data analysis and simulation of process operations, ranging from the identification of ingredients, the recording of physical and functional properties to the tracking and tracing of food products and product evaluation by consumers.
A sustainable bioeconomy works with closed material cycles which use resources more efficiently and minimise waste and emissions. Innovative, smart process technology is needed at every step of the value chain, such as product design, production and cascade use of bio-based resources (see chapter Circular bioproduction). Recycling of agricultural residues and industrial waste streams has become possible through innovations in mechanical and plant engineering. The CocoaFruit project funded by the BMBF where researchers are trying to utilise the pulp and shell of the cocoa fruit, illustrates this. High-quality recycling or upcycling depends on the upstream separation and reprocessing of recyclable materials. Examples include the recovery of phosphates from sewage sludge, of building materials from demolition waste, or of balsa wood from wind turbine rotor blades.