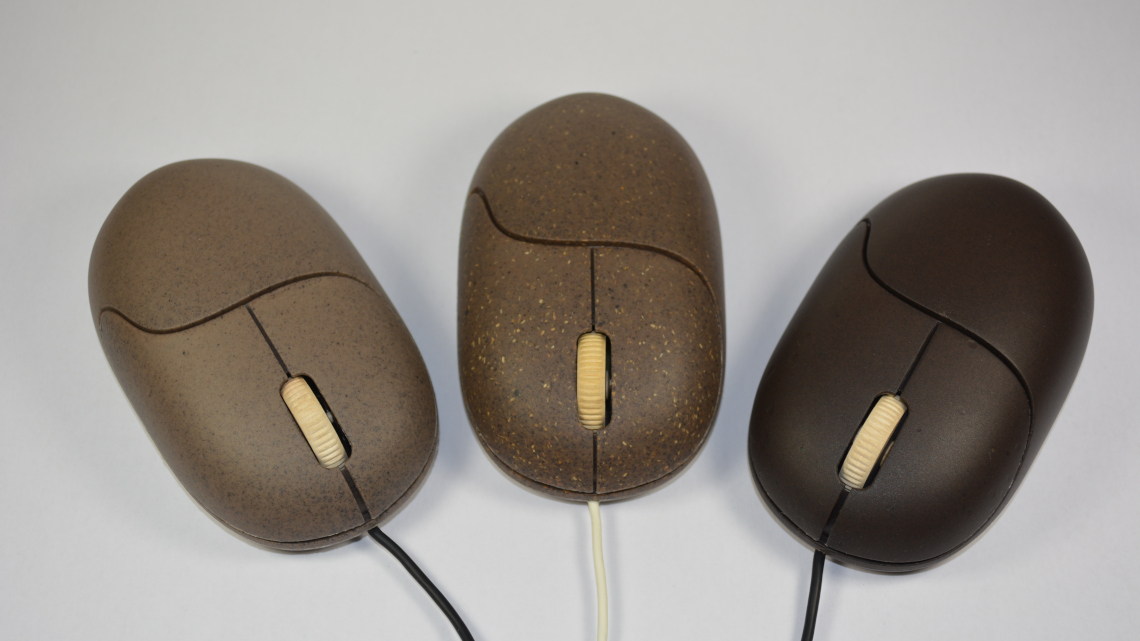
For breakfast, after dinner or just in between: coffee is the most popular hot drink in Germany. For 72% of Germans, the energizing brown drink is part of everyday life. As a result, the average person consumes 165 litres of coffee per year. However, the leftover coffee grounds usually end up in the waste. Using this waste material as a resource for new bio-based materials and products has become an exciting field of research.
That is also how BioKaVe's focus on development of high-quality bio-based composites based on coffee grounds came about. The project was coordinated by abc GmbH in Cologne and funded by the Federal Ministry of Education and Research (BMBF) with about 675,700 euros from June 2017 to December 2019 as part of the "New products for the bioeconomy" ideas competition. The four project partners provided the same amount of funding for the project.
Replacing petroleum polymers with coffee grounds
In recent years, the team around abc managing director and project coordinator Alexander Schank has developed a processing method to recycle coffee grounds and make them usable for a wide range of composite materials. "Plastics are quite expensive, so we wanted to replace parts of conventional petroleum polymers with something less expensive and bio-based," says Schank. Therefore, the focus was on the development of fillers and colorants that could reduce the proportion of fossil-based plastics in the composite material.
As wide as the range of coffees, as wide was the range of coffee grounds that were available as a resource to the project team. "Espresso, filter or instant coffee: there was no need to differentiate between the different types of coffee," says Schank. Both residues left over from coffee house chains and from a large instant coffee producer were used.
From inhomogeneous residues to homogeneous industrial material
The coffee grounds could not be processed without further ado. "The challenge was to process this inhomogeneous waste material in a way that a homogeneous industrial material was created from it," says Schank. Therefore, the team first had to eliminate ingredients from the coffee grounds that could hinder subsequent processing. These included, for instance, oils that give coffee its aroma. "The oils interfere with processing of plastics by preventing the correct binding between the plastic matrix polymer and the coffee grounds as filler and colorant," explains Schank. To make matters even more difficult, the oil content of the individual types of coffee such as Arabica or Robusta varies depending on their origin. According to Schank, it was therefore hardly possible to use standardized and steady process parameters for the preparation aggregates.
Tension rods made from granulated coffee grounds
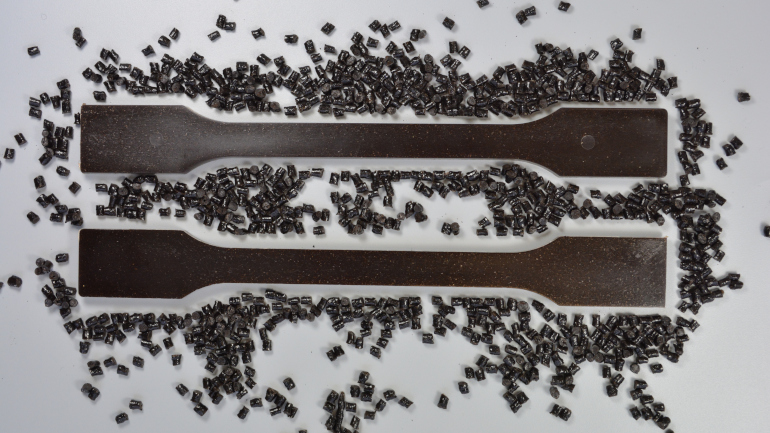
Processing in several stages
The perishability of coffee grounds poses a further difficulty. After a few days only, mould develops. "If you work with very small quantities like we do, every single mould spore has consequences. The challenge was therefore to find a process that would still be economically viable in a very small capacity range," says Schank. The main goal here was to find an energy-efficient solution for drying the residues in order to prevent mould growth.
Mixing coffee grounds with plastics
Using a multi-stage process, the team was able to filter out the impure ingredients. "In a first step, the residue was both thermally and biologically stabilized, so that in the next step it could be further processed mechanically," explains Schrank. With reference to possible property rights, detailed information on the new process can currently not be provided. However, the result is a filler in powder form. Finally, using both conventional and bio-based plastics such as Bio-PE, PLA, PLLA and Bio-PA, the recycled coffee grounds were processed into plastic granulate by the project partner IfBB - Institute for Bioplastics and Biocomposites.
"As a result, we now have a pattern chart that helps us identifying which plastic goes with which mixing ratio of coffee grounds," says Schank. This is because the amount of coffee grounds incorporated into a composite material is determined by the type of main plastic and the subsequent application of the bioplastics component. Whether Bio-PA or PLLA is used depends on the product to be made and the material requirements of the clients.
Wide range of products
Using numerous prototypes - from computer mice, pens, serving trays and water dispensers to terrace decks and coffee house floors - the BioKaVe team showed that with their new processing method coffee grounds can be used for a variety of composite materials. "We are only now entering the phase where we’re examining whether this is also realisable on a large scale," said Schank. To achieve this, discussions with industrial partners are currently being held. In addition to the companies already involved in the project, BeoPlast Besgen GmbH in Langenfeld and Maschinenfabrik Reinartz in Neuss, other interested parties are on board in order to start practical testing on an industrial scale this year and to establish supplier relations. "Whether this can still be achieved with Corona and co. is of course questionable. But if the talks continue as they have so far, it definitely is a realistic goal," says Schank.
Author: Beatrix Boldt