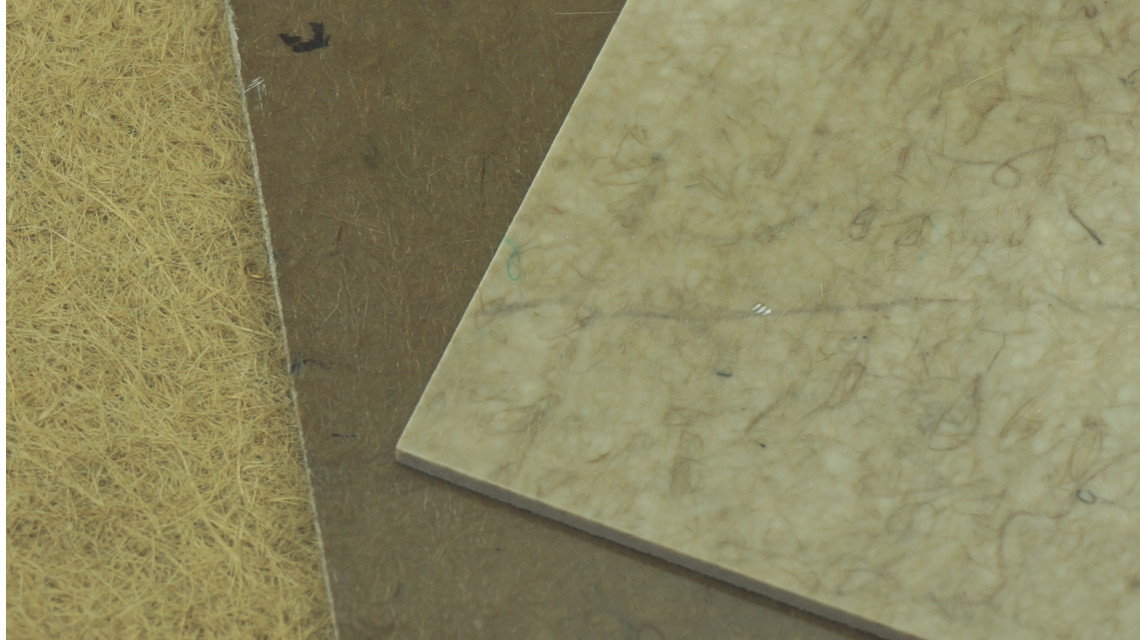
Be it in the household, at sports or in the car: objects made of fiber composites are ubiquitous without us being aware of them. The combination of two components, such as a plastic matrix with fibers, creates a high-strength and lightweight material that meets a wide range of requirements. The range of applications extends from skateboards and leg prostheses to aircraft fuselages. So far, glass fibers have dominated such materials, but natural fibers are making up ground: Hemp or flax can keep up in terms of stiffness and strength and are many times cheaper to manufacture. Natural fiber-based composites are a real alternative to non-structural components, especially in automotive engineering.
Jute fiber components
In the international joint project Jute Bio-Comp, German and Indian researchers and partners from industry have now taken a close look at jute fibers for composite materials. The aim is to develop jute fiber-based composites for a wide range of industrial applications that can be produced cost-effectively. The project was coordinated by the Karlsruhe Institute of Technology (KIT) and funded by the German Federal Ministry of Education and Research with around 400,000 euros from 2015 to 2018 as part of the "Bioeconomy International" funding measure. "We wanted to transfer our standardized processes for handling fiber composites to jute fibers and show how they are processed into corresponding components," explains project manager Julian Hüttl from KIT.
India is one of the main producers of jute. Jute plants were used there for many years to produce packaging. But the market is in a slump because plastic packaging is becoming cheaper and cheaper. "This was a political motivation for the project: the processors in India were looking for new areas of application for their product," explains project employee Patrick Griesbaum. At the Fraunhofer Institute for Chemical Technology (ICT), he was responsible for process development for the production of jute fiber-based composites.
Jute fibers as good as glass fibers
Before processing, the jute fiber first had to be characterized and examined for its capabilities. The bar was high: the natural material from the subcontinent should offer nothing less than the properties of the glass fiber in order to be considered as a composite candidate. The decisive factors here were tensile strength, elasticity and density. "The first thing we noticed was that the properties of the jute fiber were very similar to those of the glass fiber, especially with regard to how the fiber could be integrated into the matrix. At 1.3 grams per cubic centimeter, the density is much lower than that of glass fiber," reports Hüttl. The jute fiber is therefore even lighter than its competitor - an advantage that could make it attractive for lightweight construction.
In general, fibers in composites provide the necessary strength. The decisive factor in the project was whether jute fibers could also withstand the considerable forces in the manufacturing process. The researchers are testing the processability in three processes, known as process routes, which are already used to manufacture fiber composites: wet pressing, resin transfer molding (RTM), and sheet molding compounds (SMC).
Jute fibres drying (Bangladesh)
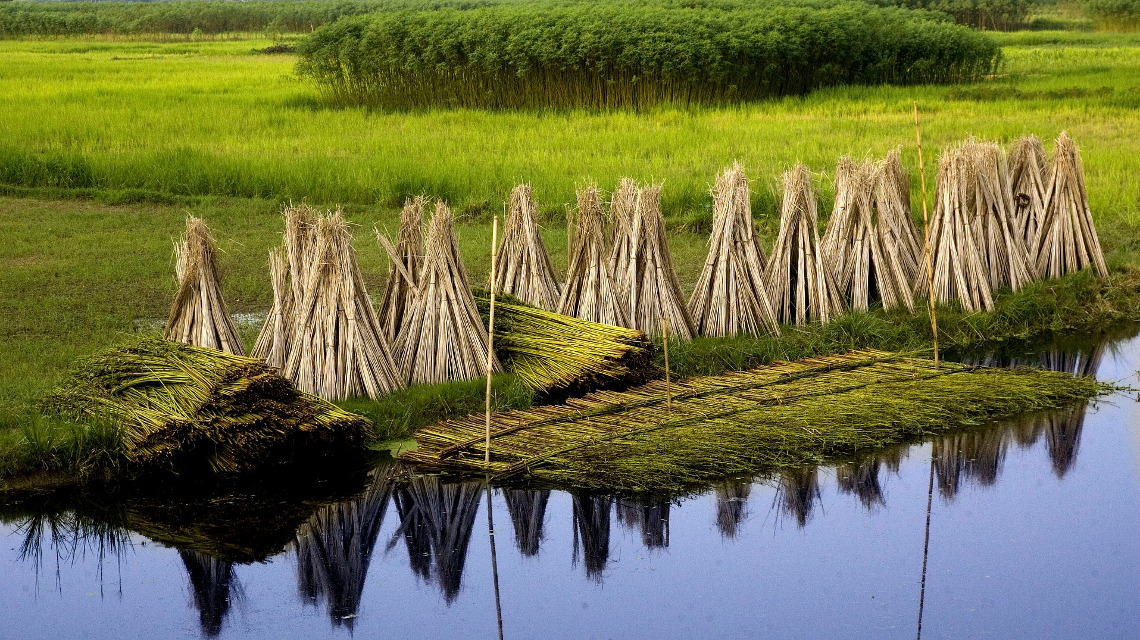
The drawbacks of natural fibers
But natural substances have their drawbacks that the researchers had to come to terms with in the project. In the case of jute fibers, it was the high affinity to water and the polar fiber surface. Both of these factors hinder the optimal binding of the fiber to the duromer matrix. The difficulty: As a natural raw material, the jute fiber draws water from the air even after harvesting. The researchers have solved this problem by drying in an oven at 80 degrees Celsius. " However, the fibers had to be processed immediately, because as soon as they are exposed to the ambient air again, they draw water once more. So the time window was very short," reports Hüttl.
The polarity of the surface results from organic residues found on the natural raw material. Hüttl reports that a method developed by the Indian partners came to the rescue here. "The organic residues were removed with hydrogen peroxide, i.e. by chemical bleaching. Afterwards, the adhesion was measurably better."
Nonwoven fabric of jute fibers processed in duromer matrix
The Jute BioComp team also had to overcome a number of hurdles when it came to processability. In the SMC process, the fibers are usually embedded in a liquid film of plastic resin. The fibers have a certain cut length and thus can flow with the matrix. The initially honey-like mass finally becomes a leather-like material in the process that can be cut to size. "With the jute fiber, we wanted to produce a similar material. But we could not process the fibers into cut fibers on the existing lines," reports Griesbaum, who was responsible for the SMC tests. The solution: The jute fibers were processed into a nonwoven fabric by an Indian partner. This could then easily be introduced into the liquid duromer matrix in the existing plants at the ICT and processed into a fiber composite material.
However, one problem remains: the quality of the jute fibers depends on climatic and soil conditions and is therefore not consistent. "It is a natural fiber that will always have fluctuations. There's not much you can do about that", says Griesbaum. "One option would be to mix the fibers from different vintages in order to balance out the differences."
Principle transferable to other natural fibres
As a result, the researchers were able to show that jute fibers have similarly good composite properties as glass fibers and can be processed into composite materials in existing processes. "The project has taught us how to process natural fibers in our processes. This principle can also be applied to other natural fibers such as hemp or flax," emphasizes Griesbaum. The researchers also learned another lesson: "It is a natural product, and you have to work differently than with conventional fibers. You have to explain this to the people," said Hüttl.
Whether in the automotive industry, in the construction industry or in the play and leisure industry: composite materials made from jute or other natural materials undoubtedly have great potential and the researchers around Hüttl and Griesbaum want to explore this further.
Author: Beatrix Boldt