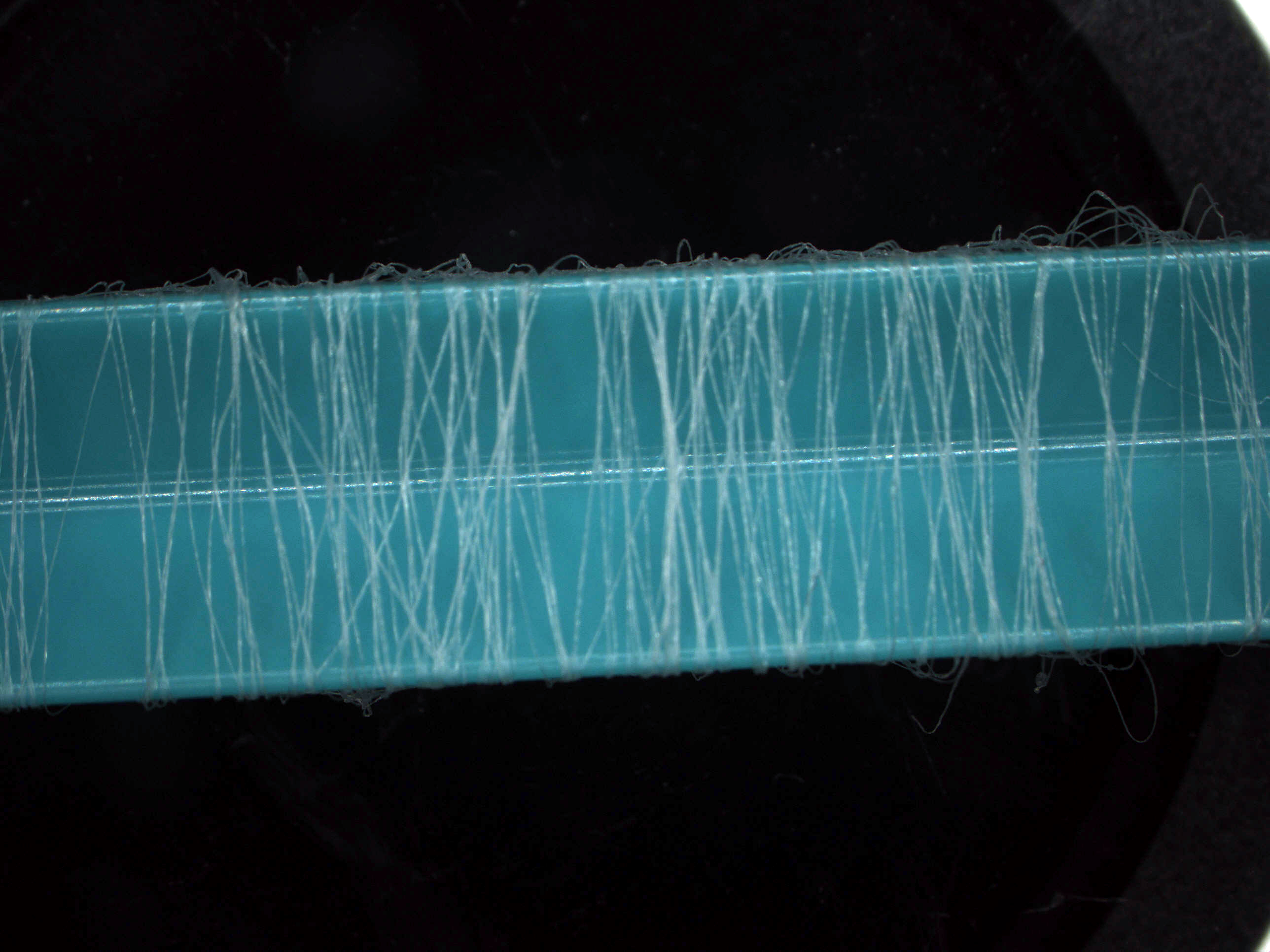
Alginates act like a sponge. The biopolymer, which is obtained from brown algae, can absorb huge amounts of germs and liquid. Because of its gelling properties, it is in great demand for medical wound dressings. However, the quality of algae-based alginates varies, as they are highly sensitive to environmental influences. As part of the AlBioTex joint project, researchers at the Hohenstein Institute for Textile Innovation in Germany liaised with industry partners and managed to find a biotechnological process of producing polysaccharides using Azotobacter vinelandii. The obtained powder was spun into fibres and later processed into wound dressings. The development of these bacteria-based algae-fibres was supported with €546,000 by the German Federal Ministry of Education and Research (BMBF).
Because of the countless minerals they contain Algae are not only healthy. Some kinds of green algae are able to act ascellbased factory to generate biofuels. The biopolymer alginate produced from brown algae is highly biocompatible and therefore suitable for the use in medical and pharmaceutical products. For many years, it has been used for wound dressings. The reason: The biopolymer is able to absorb liquids weighing more than double itself and in doing so, it literally sucks germs right out of a wound. But that's not all. "When the alginate comes into contact with wound secretion or blood, it gels. That keeps the wound moist and sealed, so that it doesn't stick to the dressing," explains molecular biologist Eva Glink from the Hohenstein Institute for Textile Innovation in Baden-Wuerttemberg.
To guarantee biocompatibility
Producing the biocompatible alginates with a consistent degree of quality used to be quite a challenge in the past, as the alginate's quality varied depending on the origin of the brown algae. "The composition of algae changes, depending on their location and the seasons," Eva Glink continues. However, the purity and composition of alginate biopolymers should be on a constant level to be officially approved for the use in medical products such as wound dressings.
Researchers working on the AlBioTex joint project successfully used biotechnology to generate alginates from Azotobacter vinelandii soil bacteria, which have a natural capacity for forming alginate. Besides the Hohenstein Institute other partners such as the biotechnology company Brain AG, and fibre-maker Kelheim Fibres GmbH were also part of the BBMF-funded project.
Tailor-made alginate
The main aim of project: to biotechnologically generate reproducible and chemically standardised alginate for use in fibre-based materials such as wound dressings. "We managed to produce tailor-made alginate of a consistent quality. To receive certain properties of the alginate, we genetically modified the bacteria," reports Glink.
First, the researchers had to turn the soil bacteria into efficient alginate factories. The advantage of this approach: unlike brown algae, Azotobacter vinelandii releases the biopolymer into the culture medium. "We grew bacteria in a nutrient solution and subsequently separated the alginate that they had released. We isolated the alginate in multiple precipitation steps and freeze-dried it to alginate powder," explains Glink. From the alginate the researchers spun either pure alginate fibres or, alternatively, Kelheim Fibres GmbH made alginate viscose fibres. In the final step, the textile experts at the Hohenstein Institute processed wound dressings out of them.
Meanwhile, industrial biotech specialist Brain AG was responsible for optimizing the alginate biosynthesis. In Zwingenberg, the bacterial strains were genetically modified to improve the material’s properties. The bacterial alginate was finally produced through fermentation.
"We succeeded in depicting a typical biotechnological production and manufacturing process, from obtaining the bacterial alginate and generating the fibre through to producing the textile coverings," says Glink and adds, that the bacterial alginate obtained has a defined chemical make-up and is reproducible at any time. However, bacterial alginates cannot yet compete economically with the biopolymer extracted from brown algae, as the total yield achieved is still too small and its purity does not yet reach 100%, says Glink. "Genetically modifying the bacteria to improve their yield affected their growth. Moreover, bacterial alginates contain toxins, and filtering them out in additional purification steps still reduces the alginate yield," she explains.
Making bacterial alginate competitive
The next step is therefore to make the bacterial alginate competitive - the advantages of obtaining alginate using biotechnology are self-evident when compared with the traditional methods. Glink: "The properties of the material can be fine-tuned to each application area. Alginate can be produced anywhere in closed systems irrespective of climatic and environmental influences — and cheaper than extracting it from algae."
Autorin: Beatrix Boldt