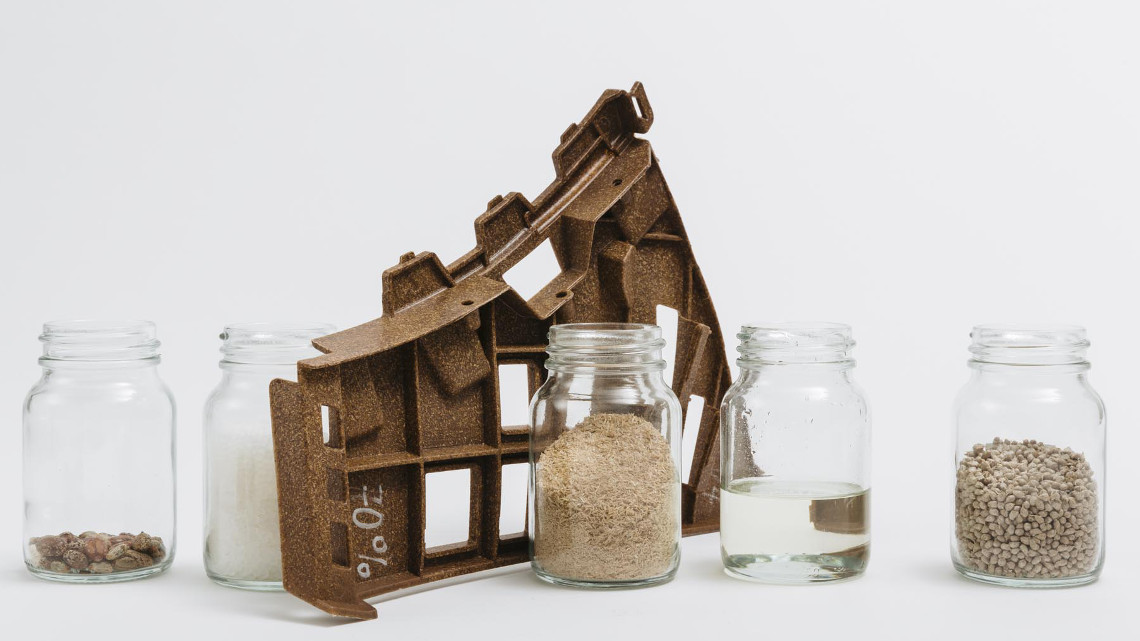
Sei es im Lebensmittelbereich, bei Möbeln oder Baumaterial: Viele Kunden achten immer mehr auf Nachhaltigkeit bei neuen Produkten. Und tatsächlich stehen biobasierte Materialien den Eigenschaften erdölbasierter Kunststoffe in kaum noch etwas nach. Dafür sorgen unter anderem Patrick Hirsch und Kollegen am Fraunhofer-Institut für Mikrostruktur von Werkstoffen und Systemen IMWS in Halle. Zusammen mit weiteren Kooperationspartnern aus Forschung und Industrie haben sie ein auf Buchenholz basierendes Biopolymer entwickelt, das sowohl in der Automobilindustrie als auch bei Kinderspielzeug zum Einsatz kommen könnte.
Kiefer und Fichte werden durch Buche ersetzt
Das IMWS in Halle ist Teil des Spitzenclusters „BioEconomy“ und ist hier für das Verbundprojekt „Polymere Materialien und Bauteile aus Biomasse“ zuständig. Das Großprojekt wurde zwischen September 2012 und Juni 2016 mit insgesamt knapp 754.000 Euro vom Bundesministerium für Bildung und Forschung (BMBF) gefördert. Der promovierte Wirtschaftsingenieur Patrick Hirsch leitete dabei das Teilprojekt BioWPC. Das Kürzel WPC steht für wood plastic composites – Verbundwerkstoffe aus Holz und Kunststoffen. Als Rohstoff diente den Forschern das Holz der Buche. Der Laubbaum ist in den deutschen Wäldern auf dem Vormarsch und löst zunehmend die Fichte ab. „In unserem Teilprojekt wollten wir die molekulare Ebene erkunden und herausfinden, wie man Lignin und Cellulose der Buche nutzen und daraus möglicherweise sogar neue Werkstoffe kreieren kann“, sagt Hirsch.
Neues Co-Biopolymer senkt Schmelztemperatur
Tatsächlich wird Holz schon seit vielen Jahren als Verstärkung in Kunststoffmaterialien eingesetzt, und auch viele Biopolymere wurden bereits aus sogenanntem Matrixmaterial hergestellt. „Der Vorteil von Biopolymeren ist, dass sie eine sehr gute Bindung mit den Verstärkungsfasern eingehen und dadurch für bessere mechanische Eigenschaften im Endprodukt sorgen“, erklärt Hirsch. Allerdings lag genau hier auch einer der Knackpunkte des Projekts: „Die Schmelztemperaturen und Verarbeitungstemperaturen der von uns favorisierten Biopolymere liegen bei etwa 240 bis 250 Grad Celsius. Bei diesen hohen Temperaturen degradieren jedoch die meisten eingesetzten Holzfasern.“
In Kooperation mit dem Fraunhofer-Institut für Angewandte Polymerforschung IAP in Potsdam kreierten die Hallenser Forscher ein völlig neues und komplett biobasiertes Co-Polymer aus zwei verschiedenen Biopolyamiden. „Dadurch konnte die Verarbeitungstemperatur gesenkt werden und in die niedrigschmelzenden Bio-Polyamide konnten dann die Holzfasern eingebaut werden, ohne dass diese durch die Hitze geschädigt wurden“, erklärt Hirsch.
Biobasiert, aber nicht biologisch abbaubar
Zwar lag der Fokus des Projektes auf der biobasierten Herkunft des Materials, nicht aber auf einer biologischen Abbaubarkeit der Produkte. Hirsch und seine Kooperationspartner arbeiteten anfangs eng mit der Automobilindustrie zusammen. Seitens der Autobauer bestand großes Interesse, Teile des Innenraums, der Türen oder der Sitzstrukturen aus Biokunststoff zu fertigen, denn die biobasierten Bauteile sind oft wesentlich leichter. Für potenzielle Kunden ist es jedoch enorm wichtig, dass der Autoinnenraum auch nach mehreren Jahren noch „wie neu“ aussieht und funktioniert, und sich nicht etwa nach 10 bis 15 Jahren selbst abbaut.
Ohne Hemicellulose steigt thermische Beständigkeit
In einem weiteren Teilprojekt haben Hirsch und seine Kollegen zudem untersucht, warum die Buchenholzfasern so anfällig für Hitze sind, und welche Bestandteile am empfindlichsten reagieren. „Wir haben die Mikrostrukturen der Fasern chemisch und molekularbiologisch sehr genau untersucht und konnten gut zeigen, dass es an der Hemicellulose, also dem Kleber zwischen Lignin und Cellulose, liegt.“
Anschließend haben die Wissenschaftler chemische Prozesse entwickelt, wie man diese Hemicellulose-Bestandteile an der Oberfläche und einige Mikrometer darunter entfernen, und somit die thermische Beständigkeit verbessern kann. „Durch diese Problemlösung von zwei Seiten – mit niedrigerem Schmelzpunkt und weniger Hemicellulose – konnten wir das Prozessfenster für unsere neuen Biopolymere immer mehr vergrößern“, sagt Hirsch. Diese könnten jetzt mit Standardmaschinen und herkömmlichen Spritzgussmaschinen verarbeitet werden, so der Wirtschaftsingenieur.
Industriereife Produktion
Tatsächlich gab es im Projekt auch eine Großproduktionsphase, in der die Partner an einem Tag etwa 500 Kilogramm Material hergestellt haben. Dabei wurden pro Stunde 80 bis 90 Kilogramm Material zu Granulat verarbeitet, aus dem sich dann mittels herkömmlicher Spritzgussverfahren Bauteile fertigen ließen.
Prozessseitig stünde einer großflächigen Anwendung also nichts mehr im Weg. „Allerdings sind die fertigen biobasierten Stücke noch immer teurer als herkömmlich produzierte Materialien.“ So liegen Biopolyamide derzeit bei etwa 8 bis 10 Euro pro Kilogramm, während erdölbasierte Kunststoffe nur mit etwa 2 bis 3 Euro pro Kilogramm zu Buche schlagen. „Die Kosten können vermutlich nie ganz angeglichen werden“, so Hirsch. „Vielmehr muss bei den Verbrauchern der Wille und die Einsicht entstehen, dass biobasierte Materialien mehr wert sind, weil sie hochwertiger sind, durch bessere Eigenschaften lange halten und gut für die Umwelt sind.“ Der Nachhaltigkeitsaspekt müsse positiv in den Köpfen ankommen und wertvoll erscheinen.
Know-how fließt in Fahrradsitze und Spielzeug
Während dieses BioWPC-Projektes lag der Fokus jedoch nicht auf Marketing und Marktplatzierung, sodass es trotz der vorhandenen technischen Möglichkeiten noch kein Produkt aus dem Forschungsvorhaben auf den freien Markt geschafft hat. Hirsch und Kollegen nutzen jedoch ihr gewonnenes Know-how für bereits gestartete Nachfolgeprojekte. „Wir arbeiten inzwischen an sogenannten Add-on-Lösungen wie Kindersitzen aus biobasiertem Material sowohl für das Fahrrad als auch das Auto. Zudem entwickeln wir auch noch nachhaltiges, biobasiertes Kinderspielzeug“, berichtet Hirsch. Sein Fazit: „Wir konnten in unserem Teilprojekt zeigen, dass alles, was bisher aus thermoplastischen Kunststoffen hergestellt wurde, jetzt aus Biopolymeren produziert werden könnte und die Technologie bereits dafür bereitsteht.“ Nun müsse nur noch das Verständnis und die Akzeptanz in der Bevölkerung weiter wachsen, damit sich solche Produkte für den Auftraggeber in Zukunft auch wirtschaftlich lohnen.
Autorin: Judith Reichel