Technische Fasern aus Milchsäure
Eine neue Prozessführung ermöglicht es, den biologisch abbaubaren Kunststoff PLA für mechanisch anspruchsvolle Anwendungen einzusetzen.
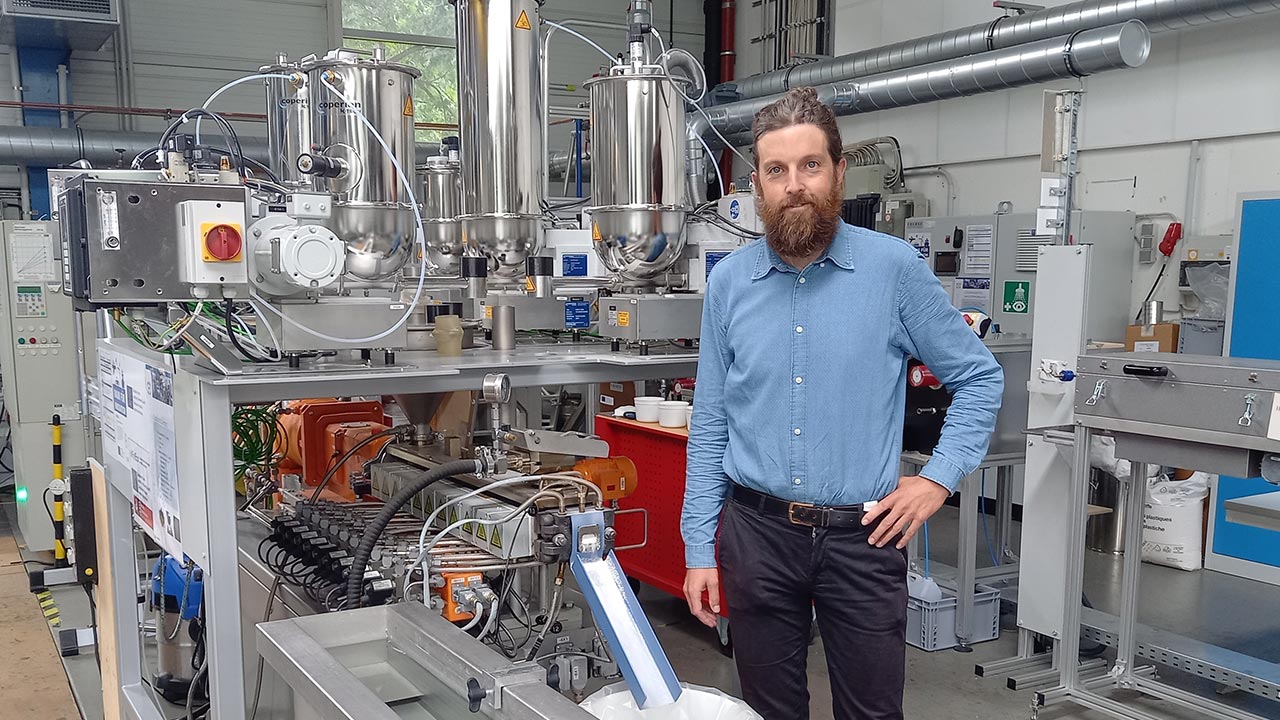
Der biobasierte und biologisch abbaubare Kunststoff PLA – Polylactid oder Polymilchsäure – könnte in Zukunft noch breiter eingesetzt werden: Boris Marx vom Faserinstitut Bremen e.V. hat einen Prozess entwickelt, der dem Material mehr Festigkeit verleiht. Damit schaffte der Forscher es ins Finale des Otto-von-Guericke-Preises 2022, den das Forschungs- und Transfernetzwerk Mittelstand AiF Arbeitsgemeinschaft industrieller Forschungsvereinigungen Otto von Guericke e.V. jährlich für besondere Innovationsleistungen auf dem Gebiet der vorwettbewerblichen industriellen Gemeinschaftsforschung (IGF) vergibt.
Von Medizingarnen bis zu Kinderschaukelseilen
Polylactid ist ein synthetisches Polymer, das zu den Polyestern zählt und auf nachwachsenden Rohstoffen wie Zuckerrohr oder Mais basiert. Zwar verrottet das Material in der Natur nicht gut, doch in der industriellen Kompostierung ist es biologisch abbaubar. Deshalb ersetzt es bereits in einigen Anwendungen erdölbasierte Kunststoffe. Technische Fasern waren davon bislang ausgenommen, weil sie zu hohe Festigkeiten erfordern. Genutzt werden derartige Fasern beispielsweise bei medizinischen Operationen, aber auch für die Seile von Kinderschaukeln.
Marx hat nun einen Prozess entwickelt, der zwei PLA-Komponenten bei einer ganz bestimmten Temperaturführung vermischt. Dadurch entsteht ein PLA-Pulver mit einer sogenannten Stereokomplex-Kristallstruktur. Daraus hergestellte Garne weisen Festigkeiten und Steifigkeiten auf dem Niveau etablierter Kunststoffe auf.
Schnell auf Industriedimensionen übertragbar
„Für die Medizintechnik und speziell für uns als Entwickler und Produzent von innovativen textilen Implantaten sind die im Projekt erzielten Forschungsergebnisse von hoher Bedeutung. Denn bislang gibt es auf dem Markt keine Produkte auf PLA-Basis in stereokomplexer Form“, erläutert Sven Oberhoffner von der ITV Denkendorf Produktservice GmbH. Der jetzt verfügbare PLA-Blend ermögliche beispielsweise, verbesserte Osteosyntheseplatten zur Behandlung von Frakturen zu entwickeln.
Axel S. Hermann, Institutsleiter des Faserinstituts Bremen e.V., zeigt sich optimistisch, dass das neue Verfahren schnell Einzug in den Industriealltag finden wird: „Ergebnis dieses IGF-Projektes ist ein innovativer, sehr nachhaltiger Werkstoff, der für Hochtechnologiebranchen wie die Luft- und Raumfahrtechnik, die Medizintechnik oder für den Automobilbau vorgesehen ist. Da der Werkstoff auf einer industrienahen Technikumsanlage entwickelt worden ist, sind die Parameter, die erforscht wurden, sehr leicht in die Industrie übertragbar.“
bl