Neuer Katalysator für die grüne Chemie
Bochumer Chemiker haben einen edelmetallfreien Katalysator entwickelt, der Bioraffinerieprozesse effizienter und die Herstellung von Biokunststoffen kostengünstiger macht.
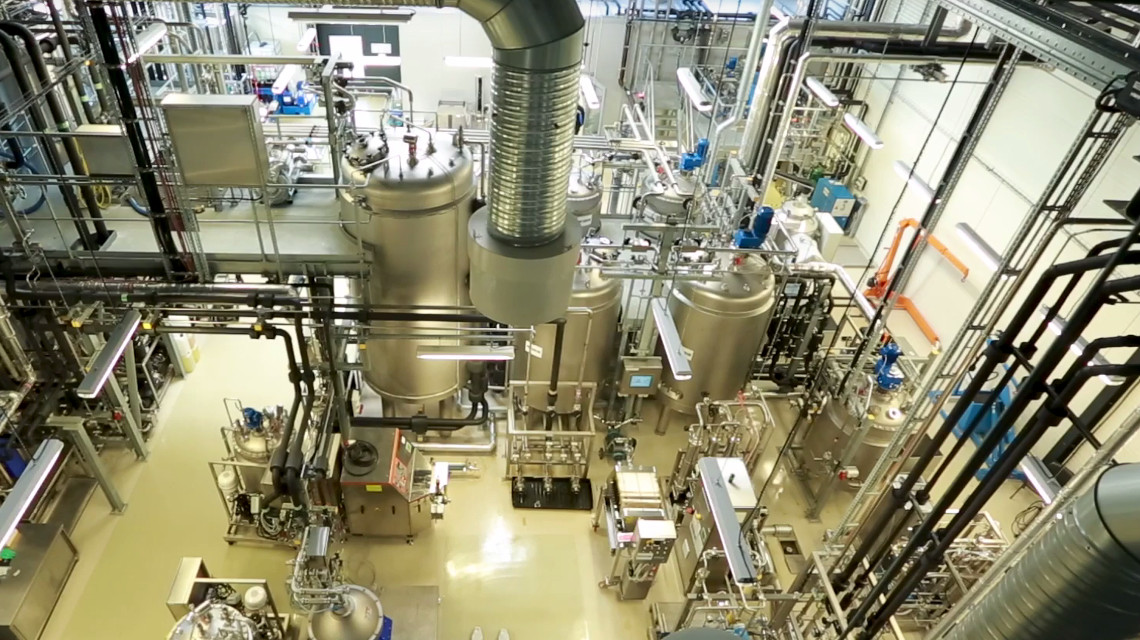
In Bioraffinerien wird pflanzliche Biomasse wie Holz oder Stroh oder andere Abfall- und Reststoffe effizient und nachhaltig zur Erzeugung von Strom und Wärme aber auch für die Herstellung neuer Plattformchemikalien genutzt. Die Umsetzung erfolgt jeweils in Bioreaktoren, deren Prozesse von Katalysatoren angetrieben werden. Katalysatoren bestehen jedoch häufig aus kostspieligen und seltenen Edelmetallen. Chemiker der Ruhr-Universität Bochum (RUB) haben nun einen neuen kostengünstigen Katalysator ohne Edelmetalle entwickelt, der zugleich auch die Herstellung von Biokunststoffen nachhaltiger macht.
Biobasiertes Polymer als Alternative zu PET
Der neuartige Katalysator besteht aus Nickelborid, einem edelmetallfreiem Material das leichter verfügbar und kostengünstiger als Edelmetall ist. Wie die Forscher im Fachjournal „Angewandte Chemie“ berichten, überzeugte der neuartige Katalysator bei der Umsetzung wichtiger Bioraffinerieprodukte. Dabei handelt es sich um die organische Verbindung 5-Hydroxymethyl-furfural, kurz HMF, die in die Plattformchemikalie 2,5-Furandicarbonsäure (FDCA) umgewandelt werden konnte. „FDCA ist für die Industrie interessant, weil es zu Polyestern verarbeitet werden kann. So kann PEF, eine Alternative zu PET, hergestellt werden – und das alles basierend auf nachwachsenden Rohstoffen, nämlich Pflanzen“, erklärt Stefan Barwe.
Umsetzung in Echtzeit
In den Versuchen der Forscher erwies sich der Nickelboridkatalysator als äußerst effektiv. Innerhalb einer halben Stunde setzte er 98,5% des Ausgangsstoffs HMF in FDCA um. Abfallprodukte entstanden keine. Mithilfe elektrochemischer Methoden und Infrarot-Spektroskopie konnten die Bochumer Forscher außerdem erstmals in Echtzeit nachvollziehen, über welche Zwischenprodukte HMF in FDCA umgesetzt wird.
Kopplung von FDCA- und Wasserstoffproduktion
Neben der Umsetzung von FDCA wurde gleichzeitig Wasserstoff erzeugt. „Wir haben den Katalysator außerdem so designt, dass er unter den gleichen Bedingungen effektiv ist, unter denen auch die Wasserstofferzeugung gelingt“, erklärt Stefan Barwe. So war es möglich in einem Schritt sowohl den Ausgangsstoff für die Kunststoffproduktion als auch den potenziellen Energieträger Wasserstoff zu synthetisieren, der normalerweise durch Elektrolyse aus Wasser gewonnen wird, wobei auch Sauerstoff entsteht. Dieser energiezehrende Prozess entfällt durch die Koppelung.
Das Projekt wurde von der Deutschen Forschungsgemeinschaft im Rahmen des Exzellenzclusters Ruhr Explores Solvation (EXC 1069) und vom Sonderforschungsbereich/Transregio 247 gefördert.
bb