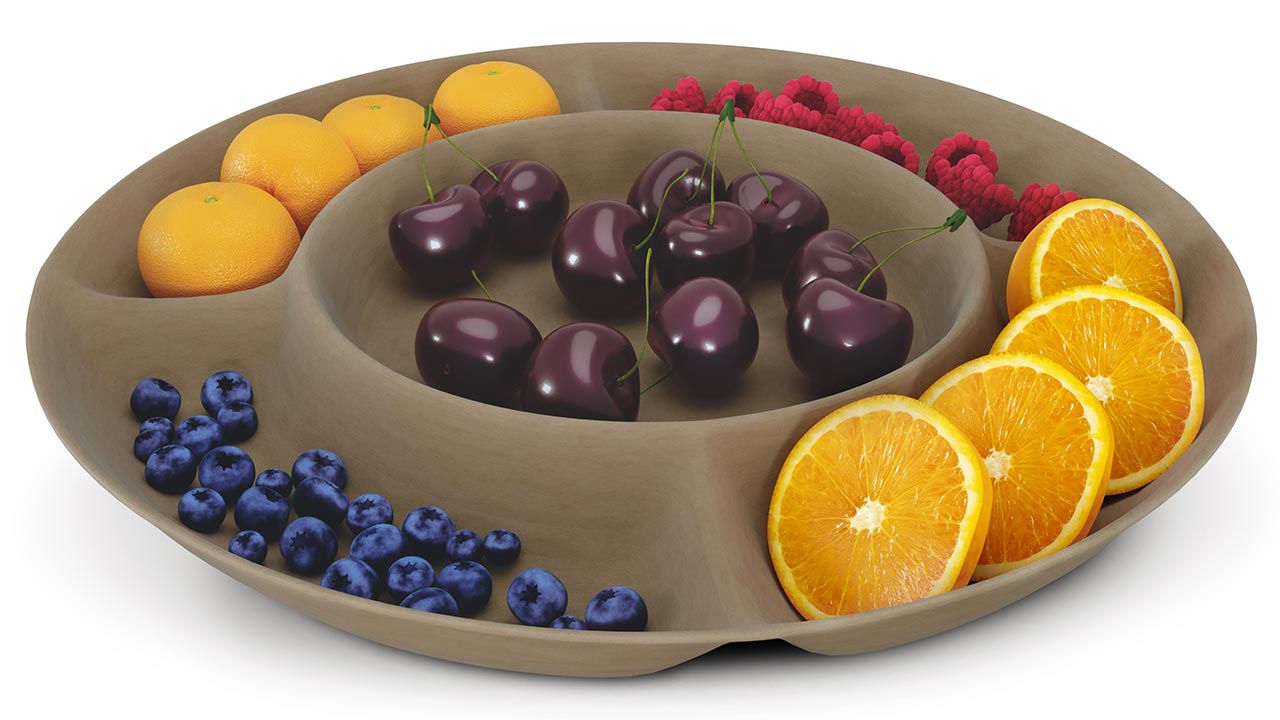
Verpackungen gibt es aus Kunststoff. Es gibt sie aus Papier. Und dort, wo Papier zu empfindlich ist, erfüllt oft beschichtetes Papier seinen Zweck. Doch nur das reine Papier erreicht hohe Sammel- und Recyclingquoten. Kunststoffe scheitern hingegen oft an Sortierproblemen oder fehlenden Verfahren. Beschichtetes Papier müsste von der Beschichtung getrennt werden, bevor es einem Recycling zugeführt werden könnte. Was läge also näher, als auch dort papierbasierte Verpackungen einzusetzen, wo heute noch Kunststoffe oder beschichtete Papiere üblich sind?
Viele Hürden für Papierverpackungen
Doch dabei gibt es offensichtliche Hindernisse: Papier ist nicht nur sehr feuchteempfindlich, auch zu große Hitze kann eine Brandgefahr bedeuten. Wie könnte ein papier- bzw. cellulosebasierter Werkstoff diese Probleme lösen? Diese Frage trieb eine Gruppe von Forschenden unter der Leitung der Dualen Hochschule Baden-Württemberg (DHBW) Karlsruhe um. Gemeinsam mit ihrem Forschungspartner, dem Fraunhofer-Institut für Chemische Technologie in Pfinztal, und den Industriepartnern Tecnaro, Mack Kunststofftechnik sowie der Werbeagentur Mainteam wollen sie darauf im Forschungsprojekt 3D-Thermocell eine Antwort geben. Das Bundesministerium für Bildung und Forschung fördert das Vorhaben mit rund einer Million Euro.
Vier unterschiedliche Lösungsansätze
Wegen der Größe der Herausforderung verfolgen die Projektbeteiligten gleich vier Ansätze, erläutert Monika Korbmann von der DHBW: „Unsere erste Idee war es, kleine Kunststoffkügelchen ins Papier einzubringen und ähnlich wie Polystyrol aufzuschäumen“, berichtet die Forscherin. Das Material hätte dann ein größeres Volumen gehabt und wäre stabiler gewesen als gewöhnliche Pappe. Anschließend hätte es im Thermoformverfahren beispielsweise zu einer Schale geformt werden können. „Das hat nicht funktioniert, weil sich die Kunststoffkügelchen nicht mit dem Papier verbunden haben“, resümiert Korbmann. Darüber hinaus hätte sich ein ähnliches Problem wie bei beschichtetem Papier ergeben: Die Kunststoffkügelchen hätten fürs Recycling zuerst entfernt werden müssen.
Die zweite Idee besteht darin, Papierfasern in Kunststoffpolymere einzubringen, als günstiger Füllstoff. Auch hier gäbe es jedoch am Ende das Trennproblem. Und falls der Kunststoff eh schon biobasiert und biologisch abbaubar wäre, gäbe es auch aus Nachhaltigkeitssicht nicht viel zu gewinnen.
Additive reversibel zusetzen
„Unser dritter Ansatz bringt Papierfasern mit ähnlichen Fasern aus Biopolymeren zusammen“, berichtet Korbmann. Auf 90% Papier kommen idealerweise 10% Biopolymere. Das daraus hergestellte Papier wäre dank des thermoplastischen Kunststoffs nach einem optionalen Aufschäumen thermoformbar. Die Kunststofffasern ließen sich beim Recycling abtrennen, sodass 90% des Produkts recyclingfähig wären und sogar 100% des Materials aus nachwachsenden Rohstoffen stammen würde.
Mit einem Mix aus 80% Papierfasern und 20% des Biokunststoffs PLA hat das Projektteam diesen Ansatz erfolgreich erprobt. „Allerdings ist das Verfahren nur möglich bei Zugabe von Feuchtigkeit“, schränkt Korbmann ein. Das Wasser müsste mit Zeit- und Energieaufwand wieder rausgetrocknet werden – ein zusätzlicher Schritt im Vergleich zum normalen Thermoformen.
Bleibt Idee Nummer vier: „Wir haben das Papier direkt im Herstellungsprozess verändert, indem wir zusätzliche Stoffe beigeben“, erklärt die DHBW-Forscherin. Die Zusätze verbinden sich mit der Cellulose und erzeugen ein festeres Gefüge. Nach mehreren Tests hat sich Polyvinylalkohol als besonders vielversprechend erwiesen. Er geht mit der Cellulose eine reversible chemische Bindung ein, was eine gute Grundlage fürs Recycling ist. Tatsächlich kann der Polyvinylalkohol einfach aus dem Papier ausgewaschen werden. Mit einem Mix aus 92% Papier und 8% Polyvinylalkohol haben die Projektbeteiligten erfolgreich ein thermoformbares Papier mit hoher Festigkeit hergestellt.
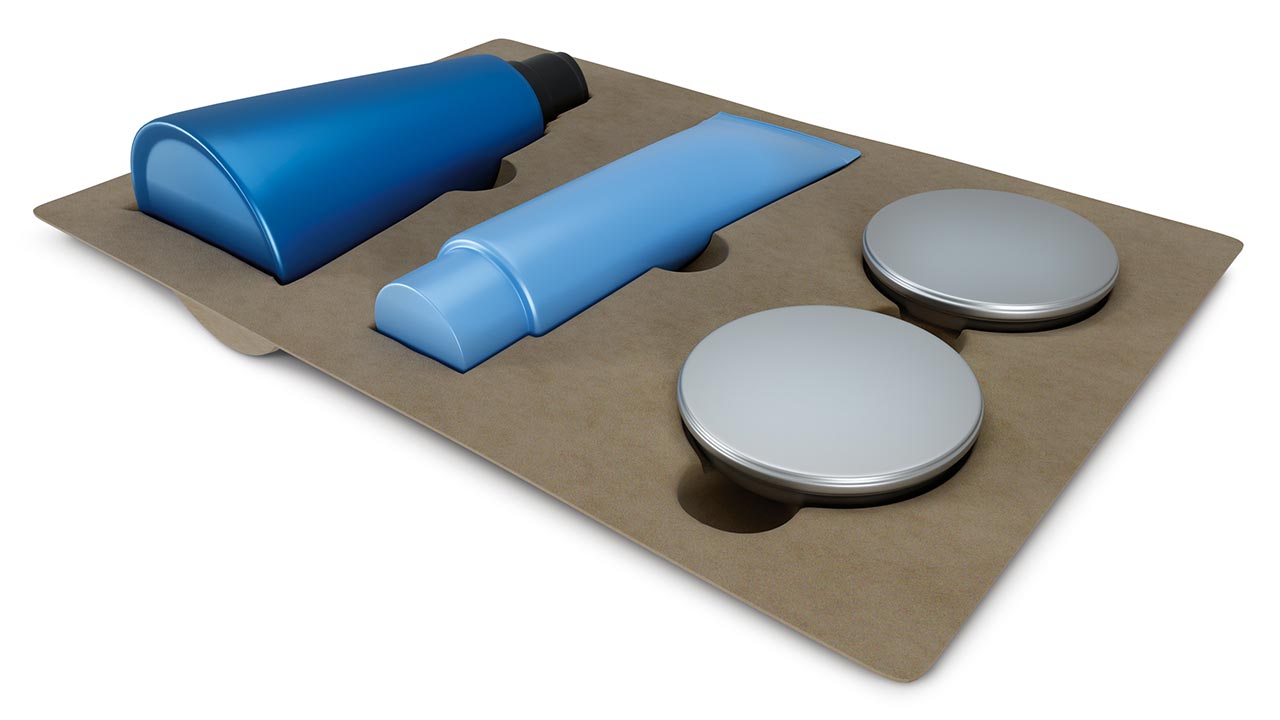
Auf die Prozessdetails kommt es an
Dabei steckte eine Menge Arbeit darin, den richtigen Prozess zu entwickeln. Sprühten die Forschenden die Lösung mit den Additiven auf das Papier, damit es einzieht und nicht wie eine Beschichtung rein oberflächlich wirkt, war es schwierig eine gleichmäßige Verteilung im Papier zu erzielen. „Cellulose ist ein natürliches Material, jede Faser ist einzigartig und reagiert daher nicht vorhersehbar wie ein Kunststoff“, erklärt Korbmann. Brachten die Forschenden die Additive direkt bei der Papierherstellung in den Faserbrei ein, zeigten sich bessere Ergebnisse. „Aber auch hier war die Herausforderung, die richtige Menge Additive einzusetzen, weil wir mit einer relativ großen Wassermenge arbeiten“, erinnert sich die Forscherin.
Am zuverlässigsten war der Prozess, bei dem das Papier in die Lösung getaucht wurde, wobei dann die Weiterverarbeitung keine so guten Ergebnisse lieferte. Jetzt will das Forschungsteam untersuchen, was passiert, wenn die Lösung unmittelbar nach der Papierherstellung aufgesprüht wird, solange das Papier noch feucht ist und keine feste Faser hat.
Machbarkeit für den Non-Food-Bereich zeigen
Was bleibt, ist das naheliegende Problem: Weil der Polyvinylalkohol leicht auszuwaschen ist, ist das Papier sehr feuchtigkeitsanfällig. „Zunächst möchten wir die Machbarkeit für den Non-Food-Bereich nachweisen“, sagt Korbmann. Zusätzliche Funktionalitäten wie eine Feuchtigkeitsbarriere oder eine Versiegelung wären Ziele für ein Nachfolgeprojekt, das dann auch auf den Food-Sektor ausgerichtet wäre.
„Jede der vier Ideen hat ihre Vorteile, aber auch knifflige Punkte zu lösen“, stellt Korbmann fest. Doch noch ist das Projekt nicht abgeschlossen und Zeit, den erfolgversprechendsten Ansatz weiter zu entwickeln. Das Potenzial neuer Cellulose-basierter Verpackungen wäre riesig. Korbmann ist zuversichtlich, bis zum Projektende noch den ein oder anderen Ansatz so weit bringen zu können, dass nicht nur Versuche in der eigenen kleinen Thermoformanlage funktionieren, sondern das neue Papier-basierte Verpackungsmaterial in einer großen Anlage beim Industriepartner erprobt werden kann.
Autor: Björn Lohmann