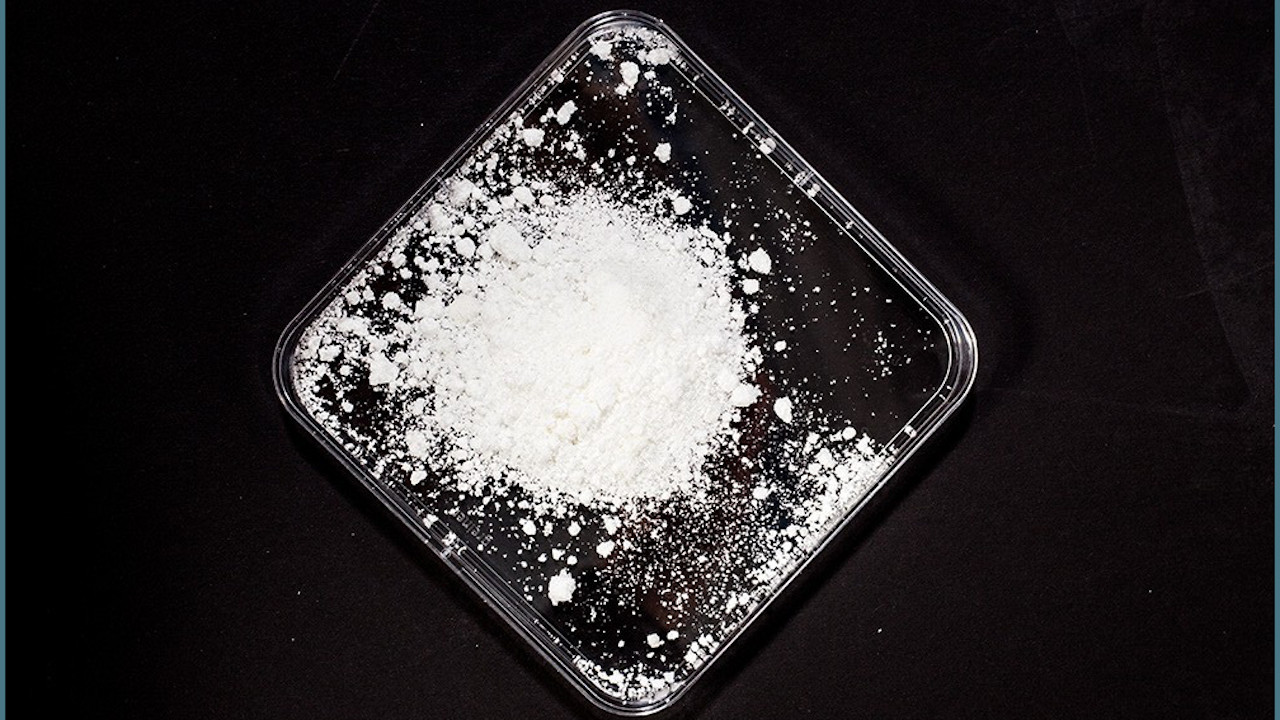
Kunststoffe sind vielseitig einsetzbar und langlebig. Doch gerade die lange Haltbarkeit ist das Problem: Erdölbasierte Kunststoffe verrotten nicht und belasten die Umwelt. Biobasierte Alternativen aus nachwachsenden Rohstoffen gibt es durchaus. Doch sie sind nicht per se umweltschonend, wenn sie nicht auch nachhaltig produziert, wiederverwertbar oder biologisch abbaubar sind. Hier setzt das Projekt PHABIO APP an. Unter der Leitung des Fraunhofer-Instituts für Produktionsanlagen und Konstruktionstechnik (IPK) in Berlin entwickelten Forschende aus Deutschland, Malaysia und den USA in den vergangenen Jahren einen biotechnologischen Prozess, mit dem ein Kunststoff aus tierischen Abfallstoffen hergestellt werden kann, der in der Natur vollständig biologisch abbaubar ist – und das in nur wenigen Monaten.
Das Vorhaben wurde im Rahmen der Fördermaßnahme „Bioökonomie International“ vom Bundesministerium für Bildung und Forschung von 2015 bis 2018 mit insgesamt 1,28 Mio. Euro gefördert. „Das große Ziel war, dass wir die gesamte Prozesskette vom Abfallstoff bis hin zum fertigen Kunststoffbauteil in allen Aspekten erforschen und am Ende eine geschlossene Prozesskette zur Herstellung von Kunststoffbauteilen zur Verfügung stellen“, erklärt Projektkoordinator Christoph Hein vom Fraunhofer IPK.
Tierische Abfallfette als Nährstoffquelle für Bakterien
Bei dem so gefertigten Biokunststoff handelt es sich um Polyhydroxybuttersäure – kurz PHB. Zur Herstellung wird das Bakterium Cupriavidus necator genutzt. Als Nährstoffquelle für die bakteriellen Kunststoffproduzenten dienten Abfallfette aus Schlachthöfen, für die es bisher keinerlei industrielle Verwendung gab. Um Cupriavidus necator in effektive Kunststofffabriken zu verwandeln, musste das IPK-Team um Hein jedoch einige Hürden meistern. „Ein Aspekt war die Modifizierung des Bakterienstammes. Der Wildtyp kann zwar auch Abfallstoffe zu Kunststoff synthetisieren, aber da bekommt man nur sehr wenig Kunststoff heraus, und der ist auch sehr spröde“, erläutert Hein. Für die Kultivierung der Bakterien sowie die Produktion des Kunststoffes waren Forschende der TU Berlin verantwortlich. Sie fütterten die Bakterien in riesigen Fermentern mit den flüssigen Abfallfetten.
Eine weitere Herausforderung war, den Kunststoff aus den Zellen der Bakterien herauszulösen. „Da haben wir auch mit den internationalen Partnern viel gearbeitet. So haben wir versucht, über biologische Extraktionsverfahren die Bakterien von Ratten trennen zu lassen, die den bakteriellen Kunststoff verstoffwechseln und dann wieder ausscheiden. Doch hier war die Geruchsbelastung des Kunststoffs zu immens.“ Ähnliche Versuche mit Mehlwürmern scheiterten Hein zufolge an der Skalierbarkeit. „Am Ende haben wird dann doch ein chemisches Verfahren genutzt, wo wir alle Lösungsmittel wiederverwerten können und danach einen qualitativ hochwertigen Kunststoff bekommen.“
Auch die Qualität der Abfallfette – vor allem deren Kohlenstoffgehalte – war für die Produktion der neuen Biopolymere entscheidend. Dafür analysierten die Forschenden die Fettqualität während des gesamten Fleischverarbeitungsprozesses. Das Ergebnis: „Wir können im Prinzip alles verarbeiten, was aus den Schlachthöfen herauskommt. Es ist auch nicht auf ein bestimmtes Tier beschränkt.“ Nicht nur Abfallfette von Rind, Schwein und Geflügel sind Hein zufolge als Bakterienfutter geeignet, sondern auch Fischabfälle.
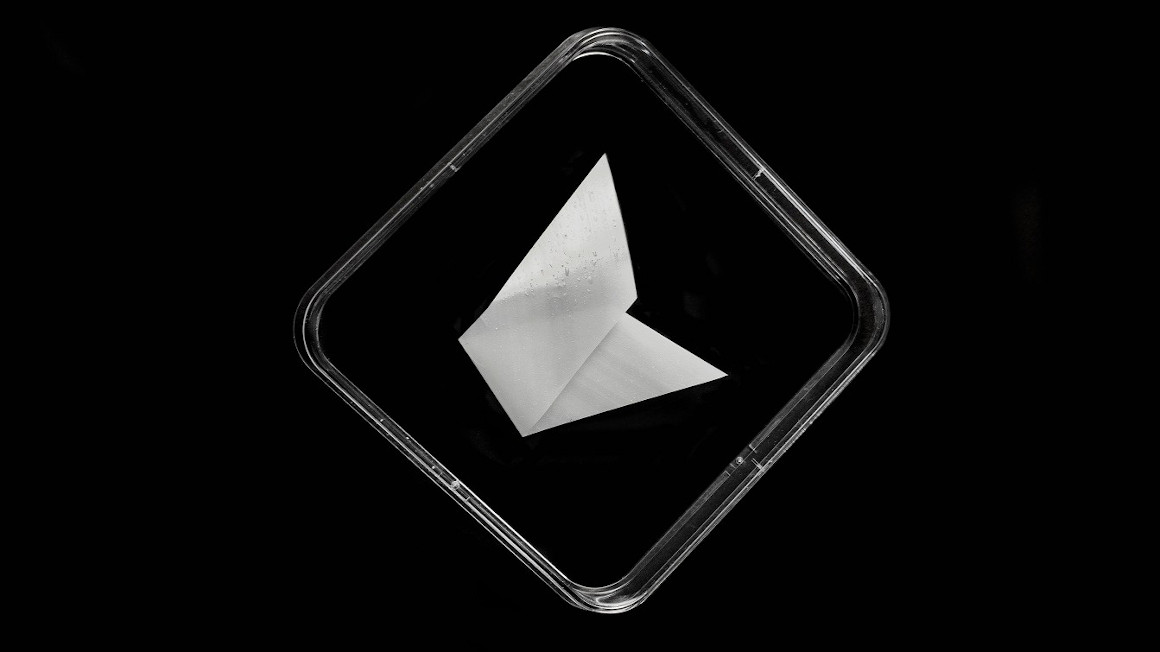
Neues PHB für Spitzgussverfahren geeignet
Neben der umweltschonenden Herstellung des Bio-Kunststoffes war auch die Weiterverarbeitung zu Produkten mithilfe etablierter Verfahren ein Hauptanliegen der Projektpartner. Anhand des Spitzgussverfahrens wurde daher getestet, ob sich der neue PHB-Kunststoff zur Produktherstellung eignet. Auch hier musste das Team nachjustieren, denn die Kristallisierung des Kunststoffes dauerte ursprünglich viel zu lange. Bis das Biopolymer ausgehärtet war und weiterverarbeitet werden konnte, musste der Spritzgusszyklus pausieren.
Doch auch dieses Problem wurde gelöst: „Wir haben spezielle Zusatzstoffe entwickelt, die dem Rohkunststoff zugesetzt wurden, sodass er schneller kristallisiert und weiterverarbeiten werden kann“, so Hein. Dabei handelte es sich zwar um chemische Zusatzstoffe. Ihr Anteil im PHB-Kunststoff ist mit maximal 0,07% jedoch sehr gering und wird auch komplett mit abgebaut. Weitere Prozessparameter wie Verarbeitungstemperatur und -geschwindigkeit mussten ebenfalls optimiert werden, um den Kunststoff im Spritzguss weiterverarbeiten zu können. Im Ergebnis des Projekts wurden bereits erste Probekörper sowie ein faltbarer Würfel als Demonstrator hergestellt.
In der Natur komplett abbaubar
Was die Eigenschaften des neuen Biopolymers betrifft, so ist es Hein zufolge mit dem bekannten Kunststoff Polypropylen (PP) vergleichbar und daher vor allem für kurzlebige Produkte wie Einweggeschirr oder die derzeit allgegenwärtigen Corona-Schnelltests geeignet. Anders als viele Biokunststoffe kann das neue PHB tatsächlich in der Natur biologisch abgebaut werden. „Egal in welchem Umfeld, im Kompost oder im Meer: der Kunststoff wird sehr zügig abbaut. Je nachdem, wie der Kunststoff verarbeitet wurde, ist er in 6 bis 18 Monaten komplett in der Natur abgebaut“, resümiert Hein.
PHABIO APP
Projektpartner:
Fraunhofer IPK: Projektkoordination, Optimierung des Bakterienstammes, Compoundierung und Verarbeitung des Kunststoffes
TU Berlin: Kultivierung und Produktion des Kunststoffes
Animox Gmbh: Aufreinigung des Kunststoffes
Internationale Partner:
University of Science Malaysia: biologische Aufreinigung des Kunststoffes
University of Massachusetts Dartmouth/ Boston: Anpassung und Optimierung des Bakteriums
Im Folgeprojekt PHABIO UP will das Team um Hein bis 2022 die Produktion des neuartigen Biokunststoffes nun für die industrielle Großproduktion fit machen. „Bisher waren die Materialmengen, die wir erzeugen konnten, stark limitiert. Und auch die Prozesse der Kunststoffherstellung waren aus biologischer Sicht noch zu langsam. Deshalb wollen wir jetzt alle Teilaspekte im Projekt so skalieren, dass es in den Tonnenmaßstab hineingeht und so den industriellen Anwendungen genügt.“ Das Folgeprojekt wird gleichfalls über die Fördermaßnahme „Bioökonomie International“ finanziert.
Autorin: Beatrix Boldt