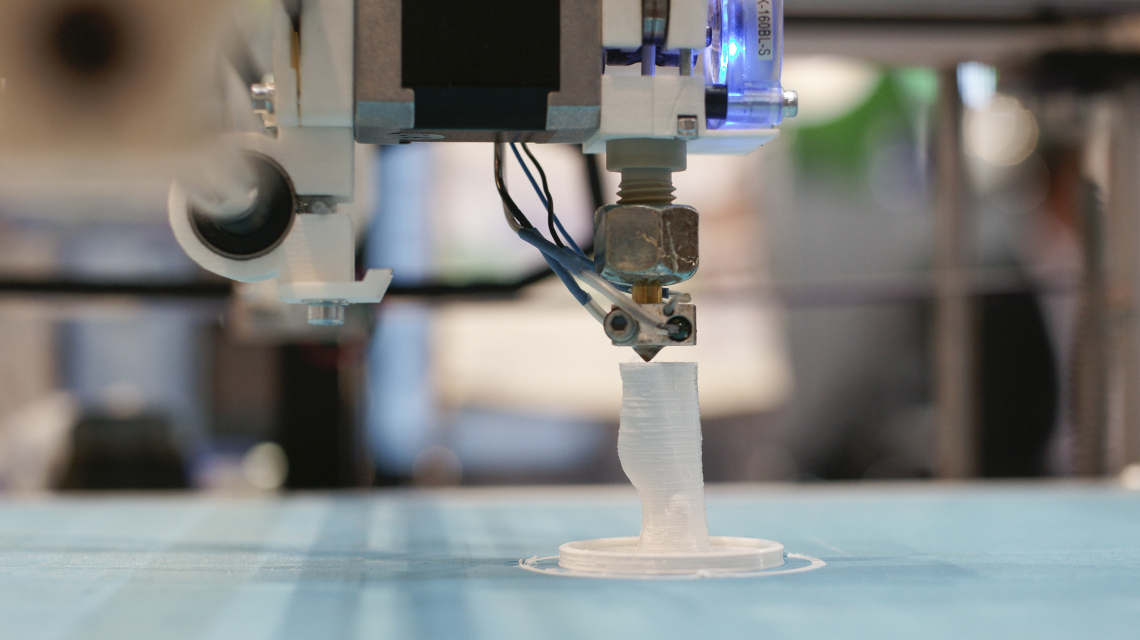
In privaten Haushalten sind 3D-Drucker zwar noch nicht Standard. Doch Industrie und Forschung setzen schon seit Langem auf das Werkzeug. Die dreidimensionale Fertigungstechnik wurde in den vergangenen Jahren vor allem für biobasierte Kunststoffe zu einem bevorzugten Anwendungsfeld. Immer neue nachhaltige Materialien wurden entwickelt und erweiterten so die 3D-Druck-Palette. Ob für Prothesen oder Kinderspielzeug, Autoteile oder Sportartikel: Die Einsatzmöglichkeiten für den 3D-Druck scheinen heute grenzenlos und zeigen, wie populär die Technik geworden ist.
Bioökonomie neu kommunizieren
Als das Projekt „BioFabNet – Biobased Fabrication Network“ im August 2013 an den Start ging, war die Technologie von einer breiten Anwendung zwar noch weit entfernt, aber handelsübliche Drucker kamen in eine Preisspanne, in der sich Privatpersonen, Tüftler und Technikinteressierte dafür zu interessieren begannen. Damals waren gerade zwei Materialien für den 3D-Druck auf dem Markt. „Das war biobasiertes PLA oder erdölbasiertes ABS“, erinnert sich Projektleiter Ralf Kindervater. Er ist Geschäftsführer der BIOPRO Baden-Württemberg, einer Landesgesellschaft, die Themen zur Umsetzung der Bioökonomie und Unterstüzung der Gesundheitsindustrie in Baden-Württemberg vorantreibt. Ziel des Projektes BioFabNet war es, neue Kommunikationsmethoden zu biobasierten Werkstoffen zu entwickeln, um so die breite Öffentlichkeit auf die Möglichkeiten der Bioökonomie aufmerksam zu machen. Das Projekt „BioFabNet“ wurde im Rahmen der Förderinitiative „BioIndustrie 2021“ vom Bundesministerium für Bildung und Forschung (BMBF) über zweieinhalb Jahre mit insgesamt 118.950 Euro gefördert.
3D-Drucker als Zugpferd der Bioökonomie
„Der 3D-Drucker und in Aussicht gestellte neue Materialien, die jeder testen konnte, waren das Zugpferd, um das Interesse für die Bioökonomie zu wecken. Wir wollten den Nutzern von 3D-Druckern zeigen, dass man in Zukunft vielleicht auch selbst eigene Kunststoffe entwickeln kann“, erklärt Kindervater. Der BIOPRO-Chef erinnert sich noch gut daran, wie interessiert aber dennoch distanziert Messebesucher auf neue biobasierte Produkte wie den „grünen Dübel“ reagierten, die die Landesgesellschaft mit Partnern entwickelt hatte. „Was das Selbermachen betrifft, sind wir weitestgehend entfremdet. Aber über das 3D-Drucken kommt man wieder an Menschen ran, weil es ihnen gestalterische Möglichkeiten eröffnet.“
3D-Druck-Nutzer für Praxistest gewonnen
Von den gestalterischen Möglichkeiten des 3D-Drucks konnten sich rund einhundert Tester überzeugen. Dafür wurde eine junge Community von Anwendern der 3D-Technik angesprochen. Profis, Semi-Professionelle und Laien erhielten so die Chance, auf ihren eigenen 3D-Druckern die im Projekt speziell dafür entwickelten neuen biobasierten Kunststoffmischungen auf Basis von Polymilchsäure (PLA) zu testen.
Für manche 3D-Drucker waren diese Puzzelteile eine harte Nuss.
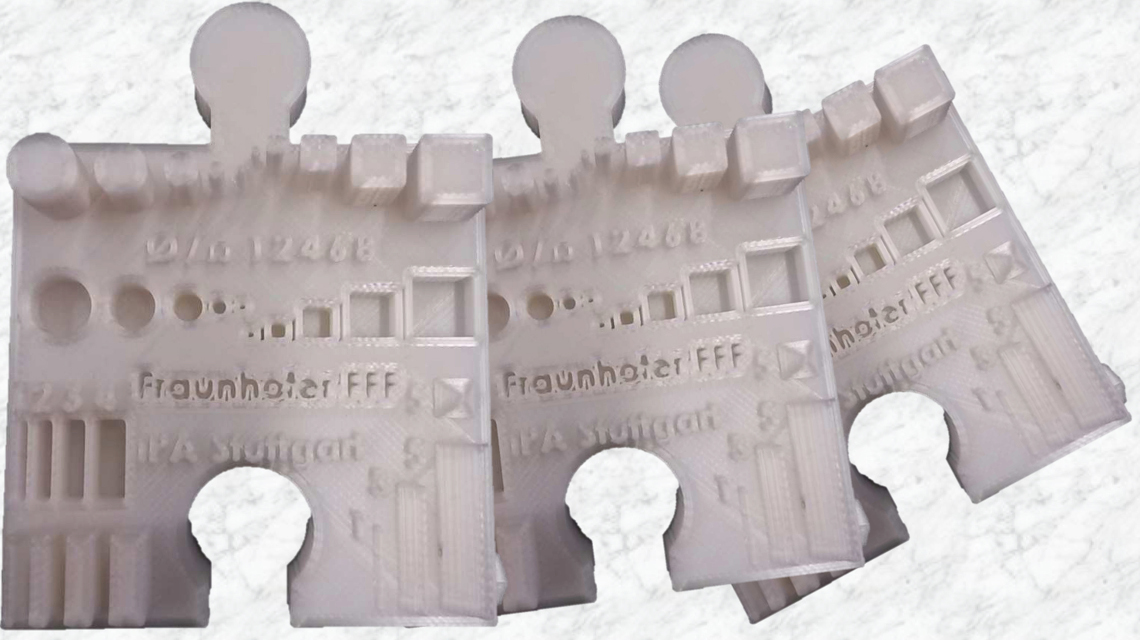
Probekörper aus neuen PLA-Materialen gedruckt
Das Institut für Kunststofftechnik der Universität Stuttgart (IKT) entwickelte als Projektpartner hierfür die geeigneten Druckfilamente, suchte nach Zusatzstoffen für PLA, um das Material für den Druck z.B. geschmeidiger zu machen. Bevor die neuen Druckfilamente an die Tester gingen, wurden diese am Fraunhofer-Institut für Produktionstechnik und Automatisierung (IPA) auf ihre grundsätzliche Eignung und Verarbeitbarkeit in den 3D-Druckern geprüft. Erst dann wurden sie über BIOPRO einschließlich einer elektronischen Bauanleitung für Probekörper, die dafür vom IPA ausgedacht wurde, an die Tester versendet. Neben freiwählbaren Objekten, bei denen die Tester ihrer Fantasie freien Lauf lassen konnten, wurden von den Materialtestern spatelähnliche Prüfkörper sowie Puzzleteile gedruckt und an die BIOPRO zurück geschickt. „Die IPA-Kollegen hatten ein Puzzelstück entworfen, auf dem sie all das, was ein 3D-Drucker können muss, abgebildet haben. Also ganz feine Erhebungen oder Vertiefungen, Buchstaben, Schriften“, sagt Kindervater.
Dabei erwies sich die Entwicklung neuer gebrauchfähiger Druckfilamente als nicht ganz unproblematisch. „Es ist einige Tüftelarbeit nötig, bis das Material auch gleichförmig aus der Maschine kommt. Denn der PLA-Draht muss bis auf den hundertstel Millimeter gleichmäßig sein, weil sonst das Druckergebnis negativ beeinflusst wird“, berichtet Kindervater.
Druckergebnisse offen diskutiert
Die Projektergebnisse wurden auf der BioFabNet-Webseite publiziert. Anhand einer Grafikwolke konnte jeder Tester sehen, wie gut das an seinem Gerät gedruckte Produkt tatsächlich ist. „Mit unserem Projekt haben wir gezeigt, dass man die Zahl der biobasierten Werkstoffe erweitern kann und das mit relativ einfachen Mitteln“, so Kindervater. Drei verschiedene Druckfilamente auf PLA-Basis mit verschiedenen Zusatzkomponenten wurden innerhalb der zweieinhalb Jahre entwickelt, getestet und zwischenzeitlich auch von Industriepartnern übernommen. Derweil war die Vermarktung der neuen Biokunststoffe nicht das eigentliche Projektziel, sondern die bessere Kommunikation derartiger Innovationen. Die größte Herausforderung sieht Kindervater in dem Schritt, sich mit den Themen 3D-Druck und biobasierte Werkstoffe überhaupt der Community zu stellen.
Über Problemlösungen Bioökonomie vermitteln
Die Erfahrung der Tester zum Druck mit den jeweiligen Materialien wurde auch in einem speziell dafür eingerichteten Blog sowie auf zahlreichen Veranstaltungen auf breiter Ebene diskutiert. „Und das ist super angenommen worden. Die Leute haben sehr fachlich und offen diskutiert“, betont Kindervater. BioFabNet konnte somit zeigen: Bioökonomische Innovationen – richtig verpackt – kommen an. „Früher sind wir immer mit einem Problembewusstsein bezüglich Klimaschutz gekommen, um Bioökonomie zu vermitteln. Über BioFabNet haben wir uns getraut, offensiv in einem völlig neuen Themenkreis über biobasierte Werkstoffe mit Bürgern zu sprechen.“ Man müsse das Interesse wecken, in dem man Problemlösungen für Bürger schaffe, so Kindervater. „Und dann kann man am Ende sagen: übrigens – das war Bioökonomie!“
Autorin: Beatrix Boldt