Bio-Acrylsäure aus Milchsäure
Mithilfe eines neuen Verfahrens ist es Nürnberger Forschern gelungen, aus fermentativ hergestellter Milchsäure Acrylsäure zu gewinnen.
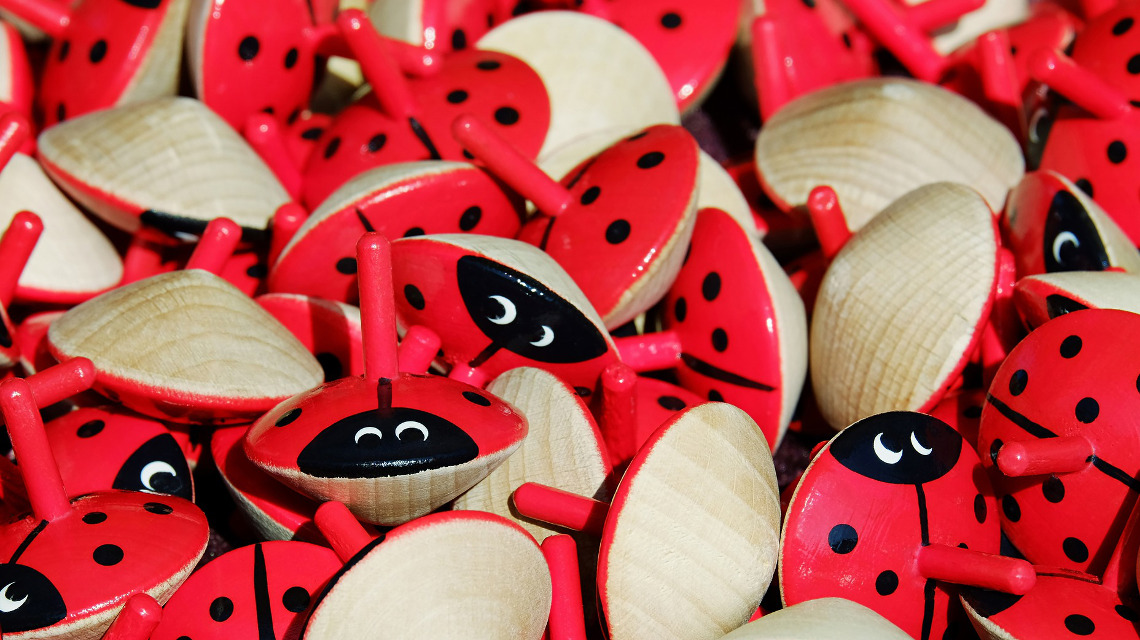
Etwa 5 Millionen Tonnen Acrylsäure werden jährlich von der chemischen Industrie zur Herstellung zahlreicher Produkte genutzt. Die aus dem fossilen Propen gewonnene farblose Flüssigkeit ist ein Hauptbestandteil von Lacken, Beschichtungen und Klebern. Acrylsäure wird aber auch als sogenannter Flüssigkeitsabsorber in Hygieneprodukten wie Windeln verwendet. Forscher der Friedrich-Alexander-Universität Erlangen-Nürnberg haben nun einen Weg gefunden, diese für die chemische Industrie wichtige Verbindung aus Biomasse herstellen zu können.
Bio-Acrylsäure durch Dehydration von Milchsäure
Bei dem Verfahren handelt es sich um ein katalytisches Reaktionssystem, das mittels Flüssigphasen-Dehydratisierung fermentativ hergestellte Milchsäure umsetzt. Beim sogenannten NADA-System (Nucleophile Assisted Dehydration to Acrylates) werden durch Wasserabspaltung Milchsäure und deren Derivate mittels Bromwasserstoff-Katalyse erzeugt. Auf diese Weise konnten etwa 80% Acrylsäure aus dem biobasierten Reststoff gewonnen werden.
Kostenersparnis durch niedrigere Reaktionstemperaturen
Im Rahmen der Verfahrensentwicklung konnte das Team zugleich neuartige Milchsäurederivate wie 2-Brompropionsäure identifizieren, die sich aus Milchsäure aber auch dem Derivat Dilactid synthetisieren und zu Bio-Acrylsäure umwandeln lassen. Das neue Verfahren ist nicht nur umweltfreundlicher sondern auch effizienter. Im Vergleich zur bisher aufwendigen Acrylsäure-Produktion aus Propen wird der Herstellungsprozess durch die Nutzung von Reststoffen, mildere Reaktionsbedingungen und eine einfachere Reaktortechnologie kostengünstiger. So ist die Reaktionstemperatur des NADA-Systems mit etwa 200 °C niedriger als die 250 bis 400 °C, die für die Acrylsäuregewinnung aus Propen benötigt wird.
Mini-Laboranlage im Test
Auf Grundlage dieser Technologie entstand auch eine neuartige Miniplant-Laboranlage, die derzeit vom Industriepartner Procter & Gamble Manufacturing Berlin GmbH (P&G) technisch und ökonomisch validiert wird. Das Verfahren wurde von den Nürnberger Forschern gemeinsam mit der P&G entwickelt und vom Bundesministerium für Ernährung und Landwirtschaft (BMEL) gefördert.
bb