Saatgut vor Ort keimfrei machen
Elektronenstrahlen könnten chemische Beizmittel bei der Saatgutbehandlung bald ablösen. Fraunhofer-Forscher bieten nun eine mobile Variante der schonenden Desinfektion an.
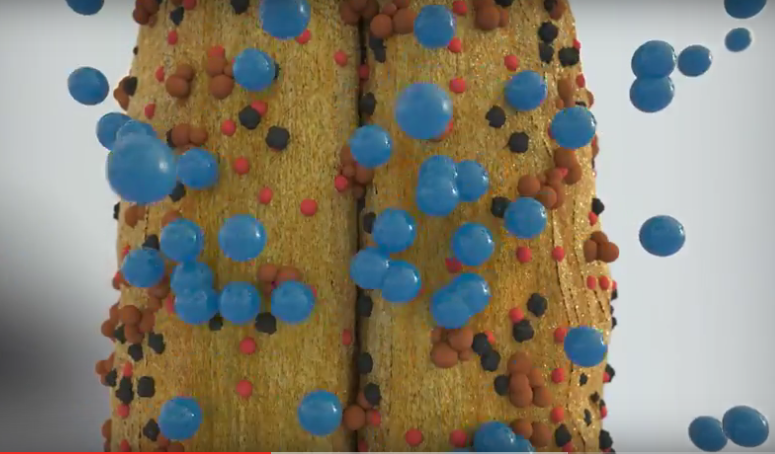
Jungpflanzen sind besonders krankheitsanfällig. Um die Sprösslinge vor schädlichen Bakterien oder Pilzen zu schützen, wird das Saatgut in der Regel mit chemischen Beizmitteln wie Fungiziden desinfiziert. Das Pflanzenschutzmittel tötet zwar die Keimlinge ab und schützt den Samen somit vor Infektionen. Es ist aber auch für Mensch und Tier nicht ungefährlich. Fungizide können beispielsweise das menschliche Immunsystem nachhaltig schwächen. Eine chemiefreie und somit Mensch und Umwelt schonende Technik, haben Forscher vom Fraunhofer-Institut für Organische Elektronik, Elektronenstrahl- und Plasmatechnik FEP in Dresden gemeinsam mit Partnern aus der Industrie jetzt auf den Weg gebracht.
Elektronenstrahlen statt Chemikalien
Dabei haben die Wissenschaftler ein in der Praxis bereits bewährtes und einst von dem Naturwissenschaftler Manfred von Ardenne entwickeltes Verfahren weiterentwickelt. Dabei handelt es sich um die sogenannte Elektronenkanone, die mittels beschleunigter Elektronenstrahlen hier Bakterien, Viren und Pilzspuren an der Oberfläche des Samens abtötet. Dabei wird sichergestellt, dass die Elektronen nur so tief in die Schale eindringen, dass das innere des Saatkorns, also der Keimling und die DNA, unberührt bleiben. Diese schonende Technologie ist zwar nicht neu, war aber bisher nur für Großsaatproduzenten konzipiert.
Saatgutbehandlung im Kleintransporter
Im Rahmen des Projektes „Ressourcenschonende Saatgutbehandlung mit neuen, preiswerten Elektronenbehandlungsmodulen“ haben die Fraunhofer-Forscher aus der Großanlage eine mobile und effektive Variante entwickelt, die auch für kleine Saatgutproduzenten rentabel ist. Die Anlage ist so kompakt, dass sie auch in einem Kleintransporter montiert und betrieben werden kann. Der neu entwickelte Elektronenbeschleuniger schafft bis zu 7 Tonnen Getreide pro Stunde.
Das Herzstück des mobilen Elektronenbeschleunigers: die Elektronen-Ringquelle.
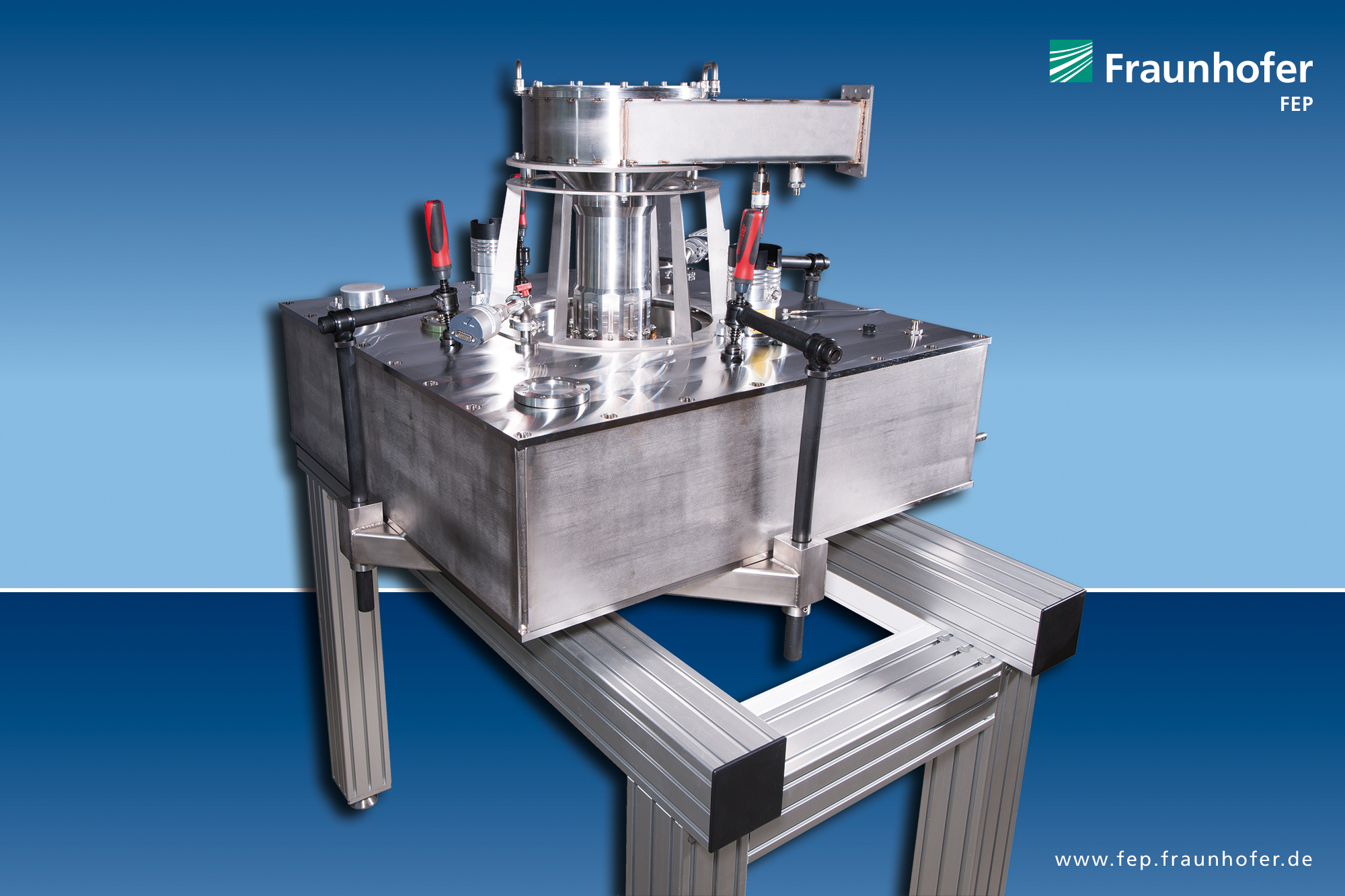
Diese Ressourceneffizienz wird durch die Formung der Kaltkathodenquelle in Ringform erreicht, die das Herzstück der Anlage bildet. „Das Besondere an dieser Quelle ist, der Verzicht auf thermische Emitter, was eine freie Formung der Quelle erlaubt. Dadurch kann eine Anlage mit nur einer einzigen Elektronenquelle für die gleichmäßige und allseitige Behandlung genutzt werden“, erklärt Projektleiter André Weidauer.
Gleiche Wirkung bei weniger Energie
Das vom Fraunhofer FEP einst weiterentwickelte Verfahren wird bereits seit mehreren Jahren zur Saatgutproduktion eingesetzt. Der Projektpartner, die Nordkorn Saaten GmbH in Güstrow, bietet seit 2012 unter der Marke E-VITA in Fraunhofer-Anlagen Elektronen-behandeltes Saatgut an. Diese chemiefreie und nachhaltige Saatgutbehandlungs-Anlage war bisher allerdings nur für Großsaatproduzenten wie Nordkorn Saaten mit einer Behandlung von bis zu 25 t/h Saatgut rentabel. „Die neue Anlage ist eine konsequente Weiterführung der bisherigen Technologie zur Elektronenbehandlung von Saatgut. Durch die kompakte Form benötigt die Anlage weniger Energie bei gleicher Wirkung gegen die im und am Samen haftenden Erreger“, sagt der Geschäftsführer der Firma Nordkorn Saaten GmbH, Andreas Prelwitz. Prelwitz zufolge ist das Interesse der Landwirtschaft an der chemiefreien Saatgutbehandlung sehr groß. Der Chef des Güstrower-Unternehmens ist überzeugt: „Die Elektronenbehandlung von Saatgut liefert einen großen Beitrag zur umweltschonenden Produktion in der Landwirtschaft“.
Millionenförderung durch den Bund
Die Entwicklung der mobilen Saatgutbehandlungsanlage mittels Elektronenstrahlen wurde vom Bundesministerium für Ernährung und Landwirtschaft (BMEL) mit rund 2,9 Mio. Euro gefördert. Am Projekt waren auch die BayWa AG und Glatt Ingenieurtechnik GmbH beteiligt.
bb