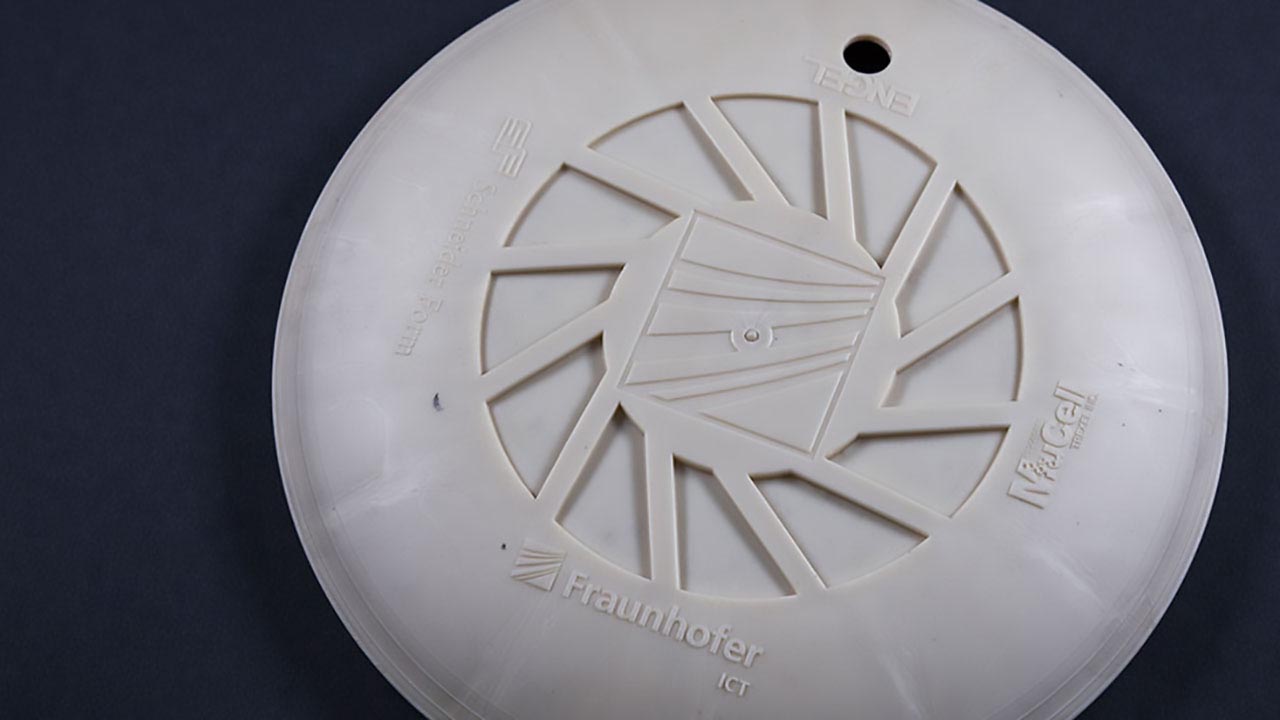
At the latest since the discovery of the Great Atlantic Garbage Patch, the topic of plastic waste has been back in the public debate. Since then, it has become clear that it is not enough to replace petroleum with bio-based resources in the production of plastics: That may protect the climate, but not nature. For the latter, the bio-based plastics must also be biodegradable under environmental conditions. The only plastic produced on an industrial scale to date that is heading in this direction is polyactide (PLA). But even it only decomposes in industrial composting plants in a reasonable time.The search for new, more suitable plastics therefore continues, and the PHB2Market research project has tested and optimized a promising candidate for its marketability.
Two PHB composites developed
At first glance, polyhydroxybutyrate (PHB) is a potential candidate, but not a convincing one: the polymer is biobased and readily biodegradable. It also has very good heat resistance of more than 100 degrees Celsius, which is important for beverage cups, for example, or for surfaces that are exposed to the sun for long periods of time. However, PHB has low impact strength in its unmodified state - i.e., it is relatively brittle - and changes its mechanical properties over time. With around 360,000 euros in funding from the German Federal Ministry of Education and Research (BMBF), a team led by the Fraunhofer Institute for Chemical Technology (ICT) has therefore set out to develop a PHB composite that addresses PHB's weaknesses without losing its strengths. The project ran from January 2017 to April 2020 and resulted in two practical composite formulations.
"We focused on two main objectives in the project," explains project manager Kevin Moser from ICT: "The incorporation of in-house developed plasticizer systems to increase impact strength and the optimization of long-term stability." PHB already outperforms polypropylene (PP) in other industrially important properties such as strength and Young's modulus. So if the research team achieved its two goals, it would have a sustainable, generally usable plastic that can be further individually modified depending on the target application - so the vision.
3D printing filaments and a frisbee
The functionality of the PHB composite was to be tested on two practical applications: the production of a Frisbee disc and filaments for the 3D printing of cubes or gear wheels. "The Frisbee is an injection-molded product, must be sufficiently flexible, not too brittle and look visually appealing," says Moser, explaining the choice.
Of course, compounders know the different additives that can be used to influence the properties of a plastic. But this is still a long way from finding the right formulation: "If you add a plasticizer to increase impact strength, this also influences all the other properties. You then have to balance that out and add other additives if necessary." Such a development process involves many years of experience, but also a great deal of testing.
Die Projektbeteiligten
- Fraunhofer - Institut für Chemische Technologie ICT
- Biotrend
- IBWCH - Instytut Biopolimerów i Włókien Chemicznych
- ICSO - Instytut Ciężkiej Syntezy Organicznej "Blachownia
- Silesian Polymers
30 different plasticizers tested
The team developed and tested more than 30 plasticizers until the desired impact strength was achieved. The experts then produced more than a hundred composites and tested them for long-term stability. For this, the stability is tested right after manufacturing and then again after a month to see how the properties have changed. "With PHB, the changes in mechanical properties are most pronounced during this time," Moser explains. "If nothing much has changed by then, the signs are quite good for sufficient stability and thus later use.
Thanks to many years of experience with PHB, the team was able to master some of the processing challenges well. On the contrary, it proved difficult to correctly dose the modified fatty acids used as plasticizers, which are often located precisely at the transition between their solid and liquid state at room temperature. "We were also surprised that we could incorporate some plasticizers into the polymer matrix at high concentrations, while others separated at low concentrations." The team had not expected such large differences, given the similar polarity of the substances.
High organic share maintained
In the end, however, there was success: The project was able to present a formulation that is suitable for higher-value applications in injection molding and, in addition to high impact strength, has sufficiently high strength and Young's modulus - while retaining these properties over time. For 3D printing, a formulation was found that is easy to print despite the high crystallinity of PHB and has high accuracy in printing. Whether these two composites are still fully biodegradable was not tested again in the project. "But we made a point of ensuring that the additives we used were of bio-based origin," emphasizes the project manager. "The organic content ended up being very high." Moreover, he says, the additives used had no negative impact on the environment. "Therefore, the material is probably further biodegradable and, as a thermoplastic, also recyclable," Moser expects.
The composites developed have not yet made it into practice. "But we were able to arouse the curiosity of some companies and then developed PHB composites for their requirements," reports Moser. These are not yet on the market, but "the companies are working on it".
Author: Björn Lohmann