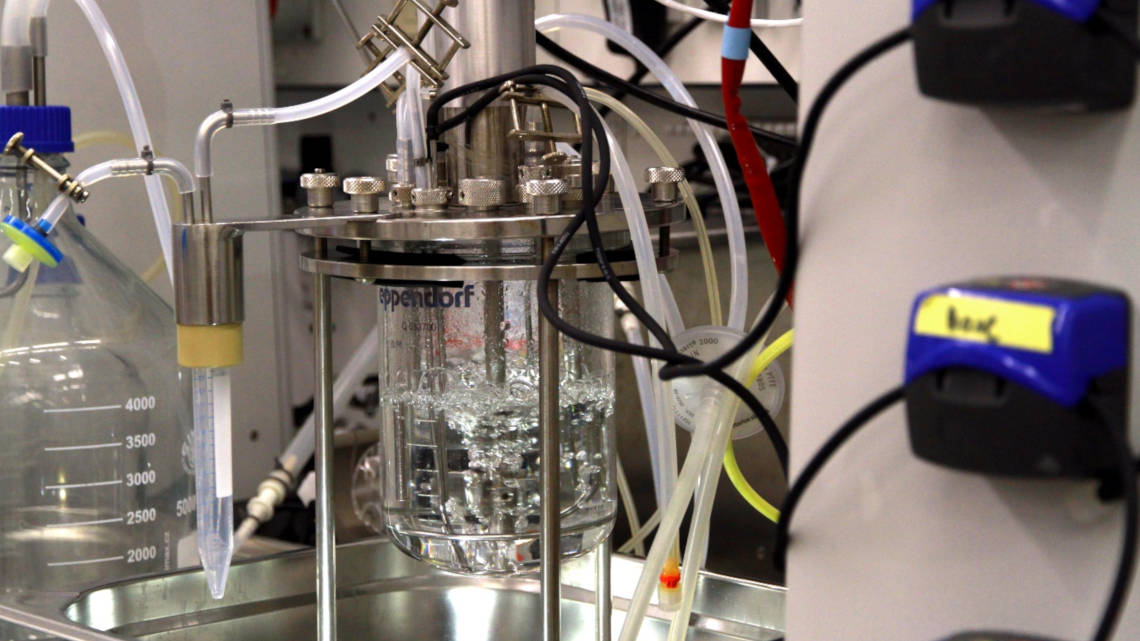
Germany has a recycling problem, even if it appears to be different at first glance. While the Federal Environment Agency reported a recycling rate of 99.4% for 2017, slightly more than half of the 6.15 million tonnes of collected plastic waste was thermally recycled, i.e. used to generate heat in waste incineration plants, cement works or power stations. Material recycling amounted to only 2.87 million tonnes (46.7%). This process conserves around three times as much of the energy contained in the plastic as can be used thermally by burning it. High material recycling rates are therefore desirable as part of a circular-flow economy.
However, while thermal use is also a form of recycling, there is also plastic waste that is not recycled. The German industry processed 12.6 million tonnes of plastics in 2017, more than twice as much as was recycled in total. The "Plastic Scoreboard" of the Heinrich Böll Foundation criticizes that only 16% of German plastic waste is effectively reused for products. The joint research project "P4SB" (From Plastic waste to Plastic value using Pseudomonas putida Synthetic Biology), funded by the European Union under the "Horizon 2020" program, aims to change this situation.
Recycled plastics more expensive than petroleum equivalents
Project manager Lars Blank of RWTH Aachen University considers two causes to be the main reasons for the low level of material recycling: "Recycled plastics are usually more expensive than the original from crude oil," reports the researcher, and: "There are some plastic components that we are not yet able to recycle". There are a few exceptions, such as PET bottles made from PET recyclate, where the waste is well pre-sorted and can therefore be easily recycled. In addition, the prices for recycled plastic are high at the moment: "Recycled plastic is more expensive than new plastic because outdoor manufacturers are driving up demand for their sustainability labels," says Blank. These exceptions do not solve the problem, but for him they point the way to the solution: "Instead of the conventional downcycling in recycling, we want to recycle the plastics so that they can make more money - and pay for the logistics of the waste collection." In addition, the researchers want to pursue this approach not only for PET, but also for polyurethane (PU), which has been difficult to recycle in the past.
The approach of the project is biotechnological in nature: In the first step, special enzymes break down a specific plastic fraction within the plastic waste into its monomers, i.e. its individual building blocks. In a second step, selected microorganisms use these monomers to produce more complex - and more expensive - plastics.
Microorganisms solve the problem of sorting
"This approach has the advantage that auxiliary materials or paints do not interfere with recycling," explains Blank. "The microbe can pick and choose from the mixed monomers and tolerates the rest". This is the reason why established processes consisting of mechanical and chemical steps fail: " A chemist cannot be this flexible when it comes to substrates; he needs monomers with a purity of 99.9% for this."
The enzymes used for PET degradation, known as esterases, have the advantage that they come from an organism that still thrives at 70 °C. "Plastic is partly crystalline, enzymes cannot attack it in this form," explains Blank. However, the glass–liquid transition temperature at which the plastics lose their crystalline structure is 70 °C. Because the enzymes are still in working order at this temperature, they can break down the entire fraction into monomers. To ensure that the esterases do this with the required efficiency, the P4SB partners of the University of Leipzig have further optimized them.
The "P4SB" project was funded by the European Union with around 7 million euros from April 2015 to March 2019. Coordinated by RWTH Aachen University, a total of ten project partners from Germany, Spain, Ireland, Great Britain and France were involved. A follow-up project has already started.
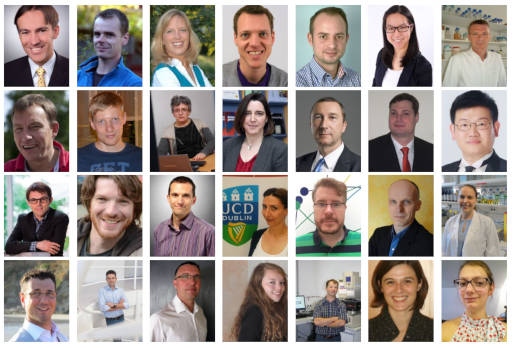
Bacteria produce plastics
The bacteria involved, of the genus Pseudomonas putida, use polyester as a storage molecule, comparable to lipids in humans. If the researchers feed them with the monomers produced by the esterases, the microorganisms form polyester in their cells. However, the cells then have to be destroyed and the substance purified - a costly and time-consuming step. "For this reason, we have also produced other molecules that are secreted by the bacteria and can thus be obtained more easily," explains Blank. In this way, detergents can be synthesized from plastic monomers.
For example, P. putida naturally metabolizes polyethylene glycol. The researchers only had to train the bacteria to be more efficient by means of adaptive laboratory evolution. The team also used recombinant genetic engineering to teach the microorganisms how to accept phthalates as nourishment. The same applies to the use of PU monomers: the bacteria can naturally absorb the monomer butanediol and the researchers taught them recombinantly how to metabolize adipic acid. Overall, the work on PET went very well. As expected, PU proved to be more difficult because it involved an entire group of substances, summarized Blank. Nevertheless: "Up to four different monomers can now be metabolized simultaneously in a microorganism" - a big advantage over chemical reactions, which are always tailored to a single starting monomer. And impurities - for example food residues - that would interfere with a chemical reaction are simply used by the microorganisms as an additional source of carbon.
Project goal achieved, profitability within sight
The project has thus achieved its goal: "We have developed an established strain that produces a valuable substance from plastic monomers and also tools for synthetic biology," summarizes the project leader. Bioplastic manufacturers could now use the new substrate to reduce their costs compared to the resource vegetable oil. Although the new process has not yet been fully optimized and scaled up to industrial scale, this would only be a matter of time: "An enzyme manufacturer would need another one to three years to further optimize the P4SB enzyme and reduce production costs," said Blank. A project partner has already developed two applications for one of the microorganisms' products - polyhydroxyalkanoate (PHA): Print adhesives such as Post-it labels and adhesives for hot glue guns. However, the adhesives cannot yet compete in terms of price with manufacturers of established adhesives who produce on a ton scale instead of in kilograms.
However, it will be some time before the microorganism itself is used in recycling plants: Profit margins in the recycling industry are low, and the industry is taking a correspondingly conservative approach. "However, if they see a cost advantage, they are on board immediately," says Blank. It will take four to five years for the microorganism to reach this stage. The next steps in this direction are already being taken successfully in the follow-up project.
Author: Björn Lohmann