What is 3D printing?
3D printing is the computer-aided production of three-dimensional products by applying materials layer by layer. Digital design templates form the basis of the production process, which is also known as "additive manufacturing".
In 1981, Chuck Hull invented the first 3D printing process, stereolithography. Laser sintering, developed by Carl Deckard, followed in 1987. A year later, the first commercial 3D printer was on the market. Successively, other 3D printing processes emerged, including fused layer modeling, on which most consumer 3D printers are based today, as well as polyjet technology and 3D screen printing as an extension of screen printing. The most recent development is Direct Sound Printing, which is still in the research stage and is based on sound waves giving objects their shape.
So-called filaments are used as 3D printing materials in the industries. The range of materials that can be printed is continuously growing. The most important are plastics such as polyactides, acrylonitrile-butadiene-styrene copolymers or polyetheretherketones, synthetic resins such as polyacrylates, silicones, ceramics and metals. But even proteins or whole cells can be processed in 3D printing (so-called bioprinting).
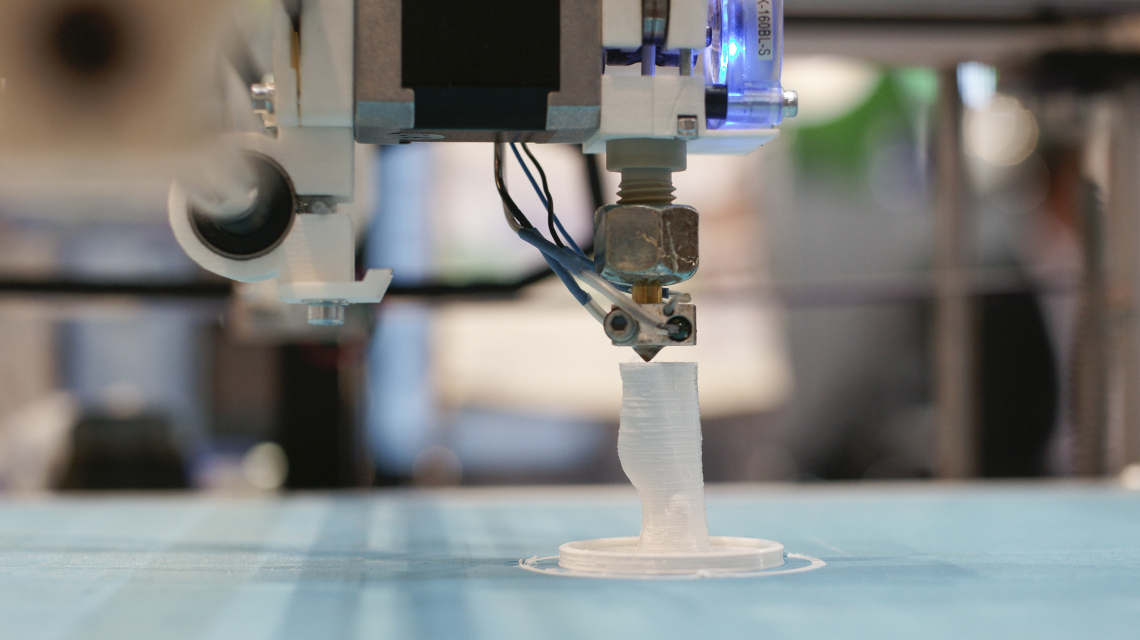
While 3D printing processes were initially valuable for the production of prototypes without casting templates or similar, additive manufacturing processes are increasingly being used in series production as well. Market researchers expect the market volume for 3D printers in this country to reach 400 million euros by 2024. In a survey conducted in Germany, one in three companies also stated that they intend to use additive manufacturing processes by 2030 at the latest. Many experts see additive manufacturing as a disruptive technology that is also an essential component of the Industry 4.0 concept. This refers to digitalized production and manufacturing with intelligently networked machines, systems and products.
Page 2 of 5
Food from the 3D printer
In 2007, researchers used 3D printing to create food structures for the first time. This was initiated by the U.S. space agency NASA, which was looking for new ways to produce astronaut food. The personalized production of particularly compatible and healthy foods is considered a major future market. 3D printing makes it possible to choose texture, taste and shape almost at will, imitating products that would naturally contain allergens or unhealthy fats. 3D printing, however, could be used to create products without these ingredients. Likewise, it is possible to incorporate valuable nutrients into a food product that does not naturally have them.
Texture for meat and fish alternatives
Manufacturers of meat and fish alternatives are placing particularly high hopes in additive manufacturing processes. Until now, it has been difficult to replicate the texture and taste of meat and fish with vegetarian or even vegan components. In 3D printing, for example, muscle fibers could be imitated exactly in their structures with plant proteins.
Most experts today assume that additive manufacturing methods are primarily suitable for individualizing food, but are not the means of choice for mass production, as the printing processes are too slow for this. Nevertheless, the market research provider Research and Markets expects the market volume for printed food to reach $500 million as early as 2023.
Market research sees great potential in 3D printers for the home, with which people can produce their own food tailored to their nutritional needs. People would then no longer buy ready-made food, but recipes and print ingredients. In this way, food could be produced in quantities to meet demand, which would drastically reduce the amount of food thrown away in stores and households.
Video: 3D printer cake art (in German)
Resource-efficient printing
3D printing generates hardly any waste products. What's more, for the bioeconomy, cascade utilization of biogenic raw materials is important in order to operate as efficiently, sustainably and with as little waste as possible. Extracting plant proteins and nutrients to print food fits perfectly into this and even allows biogenic residues to be recycled.
Decentralized food production would also be beneficial on a large scale. Here we come full circle to the origins at NASA: Companies could print food regardless of the season and regional fertility - even in the desert. Remote villages could produce food in this way, like potential lunar colonies.
So far, food printing is still associated with high costs and a low supply of suitable materials. Nevertheless, there are already some food manufacturers who use additive manufacturing processes on a more or less large scale. In Japan, the sushi restaurant "Singularity" is also set to open in the medium term, with plans to produce all its dishes using 3D printing.
3D printer food at a glance
Product |
Manufacturer/Brand |
Chocolate | Hershey (USA) began developing a chocolate printer back in 2014. In the company's "Chocolate Worlds," visitors can print their own designed chocolate bars. The development of a chocolate printer for professional chefs followed at the end of 2017. |
Potato chips | In 2012, PepsiCo wanted to create a new potato chip design for its Ruffles (USA) brand that would appeal to specific target groups, but was difficult to produce using the conventional process. The company therefore used 3D printing to create different plastic prototypes to test customer response and decide which direction to take the development. |
Cookies | At the South by Southwest 2014 technology fair, Oreo (USA) presented a 3D printer that could produce customizable Oreo cookies. |
Pasta | Barilla (Italy) debuted a printer capable of producing fresh pasta in 2016. Now, the spin-off BluRhapsody offers chefs the opportunity to buy individually designed pasta from 3D printing. A seven-gram pasta costs between two and five euros. |
Salmon substitute | The company Revo Foods (Germany) has been marketing salmon made from pea and algae protein, produced using 3D printing, in at least 14 countries since November 2021. |
Meat substitute | Redefine Meat (Israel/Netherlands/UK) markets a variety of plant-based meat alternatives, for which the company also uses 3D printing processes. Start-up Novameat (Spain), founded in 2018, has been selling 3D-printed steaks made from pea protein, beetroot juice and other ingredients since 2022, as well as other printed meat alternatives. |
Meat from cells from the bioreactor | Aleph Farms (Israel) claims to be the first company to grow and 3D print steaks from non-GMO animal cells. Meatech (Israel/Belgium) printed its first 100-gram steak from real fat and muscle cells in 2021. Other meat and fish products are to follow. |
Page 3 of 5
Applications in materials engineering
Materials technology is struggling with the fact that many of its raw materials are finite and/or unsustainable. Therefore, alternatives made from renewable, bio-based raw materials are becoming increasingly important. In combination with modern additive manufacturing processes, these biogenic raw materials result in numerous large and small applications. The focus is particularly on cellulose and lignin, but also on other biopolymers that can be processed into plastics. In addition, there are highly specialized printing materials, for example spider silk proteins.
Constructing houses
Probably the most impressive example of the dimensions in which additive manufacturing processes are used today is the 3D printing of entire buildings. In 2020, a residential building was built in Bavaria whose walls were created using 3D printing. As of 2022, the largest printed building in Europe is a five-family house with a full basement in Wallenhausen, Bavaria. Its printing took six weeks. In both cases, concrete was used as the raw material.
Prototypes such as the facade elements from the 3DNaturDruck research project funded by the German Federal Ministry of Agriculture show that it doesn't always have to be concrete in house construction. In this project, the University of Stuttgart, together with partners such as the Fraunhofer WKI and the Laser Zentrum Hannover e.V. (LZH), is developing natural fiber-reinforced biopolymers that can be produced using the 3D printing process. The aim is to combine good stability with low weight with the geometric flexibility of additive manufacturing. As a demonstrator, those involved in the project initially want to build a pavilion on the university campus consisting of such facade elements. In 2021, an Italian architecture firm also printed the "Tecla Eco House" from a mixture of clay, earth and rice husk fibers, which significantly reduces CO2 emissions compared to concrete.
In general, there are two main approaches to printing in the construction industry: Either the printer is a fully automated gantry robot, larger than the house to be built. It prints layer by layer in the space it encloses. Or it is a mobile robot with 3D printing nozzle moves on a mobile chassis. According to many experts, 3D printing is particularly useful when complex geometries are to be produced.
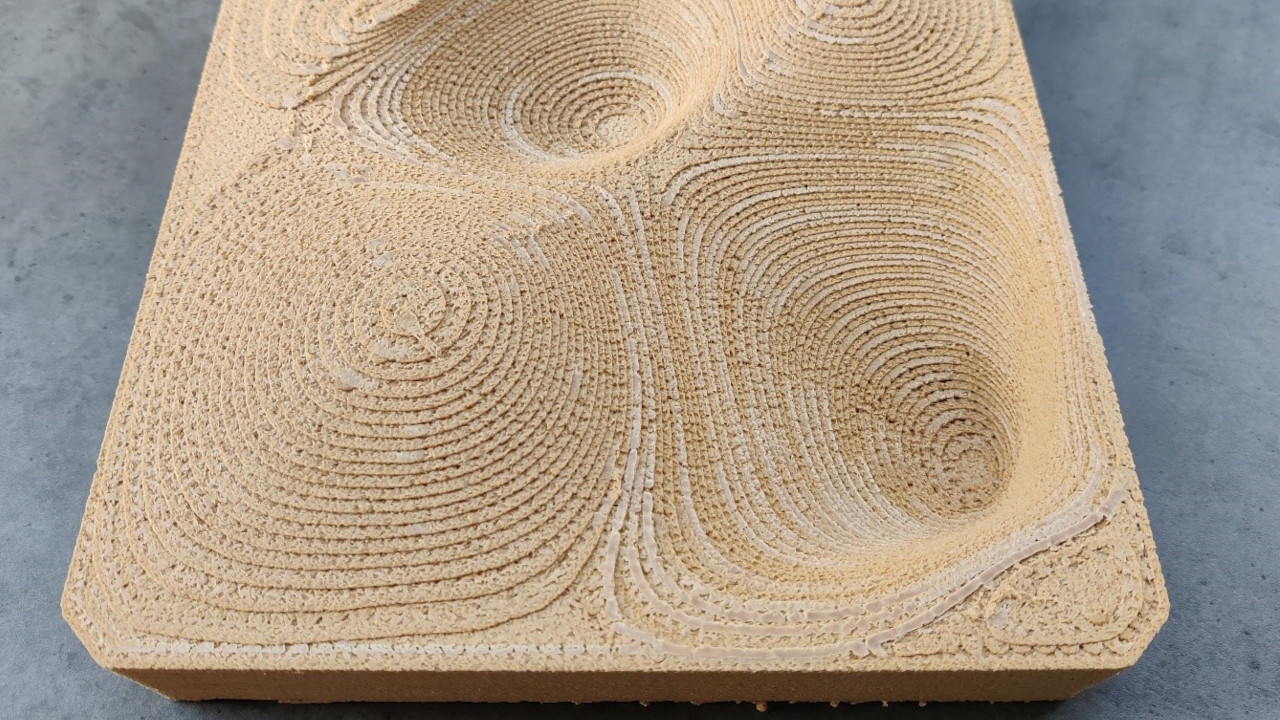
Manufacturing with bio-based plastics
An important area of application of additive manufacturing in the bioeconomy is the replacement of petroleum-based plastics with bioplastics as printing materials. The BMBF-funded BioFabNet project was already running from 2013 to 2015. The participants developed (partially) biobased plastics for 3D printing using the melt-layer process, which were subsequently tested and further improved with various users. Today, polyactides (PLA) are standard in 3D printing. Great hopes rest on polyhydroxyalkanoates (PHA), which are much faster to biodegrade, but are still under development due to poorer mechanical properties or are only used in combination with other plastics. Fungal-like additive material (FLAM) also has great potential, but this too is still rather the subject of research.
A final example illustrates the versatility of biobased applications in materials technology: researchers at the University of Halle have produced a ring using 3D printing. This is not used as jewelry, however, but consists of a biodegradable polymer into which an insect repellent has been incorporated that is also available as a spray or lotion to repel mosquitoes. The ring continuously evaporates small amounts of the active ingredient and protects the wearer from bites for about a week.
Page 4 of 5
3D Printing for Regenerative Medicine
Because 3D printing can process biocompatible materials such as cellulose, collagen, alginate or even PEG and certain metals, the process is booming in medicine and medical research.
Here, too, a major advantage is geometric flexibility. It is possible, for example, to print scaffolds on and in which cells can grow into the right shape to replace destroyed body tissue. If a piece of the esophagus had to be removed from a patient due to cancer, a perfectly fitting replacement could be created in this way. Bone implants can also grow on scaffolds made of calcium phosphate ceramics. These scaffolds are bioresorbable and are broken down by the body once the healing bone has replaced the implant. In some cases, the new tissue can be printed directly without a scaffold. An example of this is a corneal substitute for the eye.
In the long term, medicine hopes to be able to print entire organs with bioprinting. Liver tissue can already be printed and used to strengthen a damaged organ to bridge the wait for a donor organ. Researchers have even printed hearts from human cells - though not yet at their original size. Recently, 3D Systems and United Therapeutics reached a milestone: they succeeded in printing a lung with more than 4,000 kilometers of capillaries and 200 million alveoli. In an animal model, the companies were able to show that this enables gas exchange and that the lung tissue thus functions. 3D printing thus also opens up completely new possibilities for regenerative medicine.
Page 5 of 5
Further examples from research
In biological research in particular, other creative applications of additive manufacturing have already become established. So-called lab-on-a-chip systems and microfluid systems, which are used to analyze biochemical and cell-biological interactions, can be produced quickly, precisely and individually. The BMBF-funded research project Mono-cy-clone uses 3D printing for single cell analysis: The printer can select cells with desired properties, such as specific size and roundness, and then deposit them as individual droplets in microtiter plates, where researchers can continue working with them.
The approach of printing tissue, familiar from medicine, already makes it possible to produce artificial skin and other tissues on which pharmaceutical tests are carried out. In this way, the compatibility of active ingredients or entire creams can be tested without resorting to animal testing. Even researchers from the field of synthetic biology are considering 3D printing: they hope to be able to produce entire, individually designed microorganisms using this process in the future.