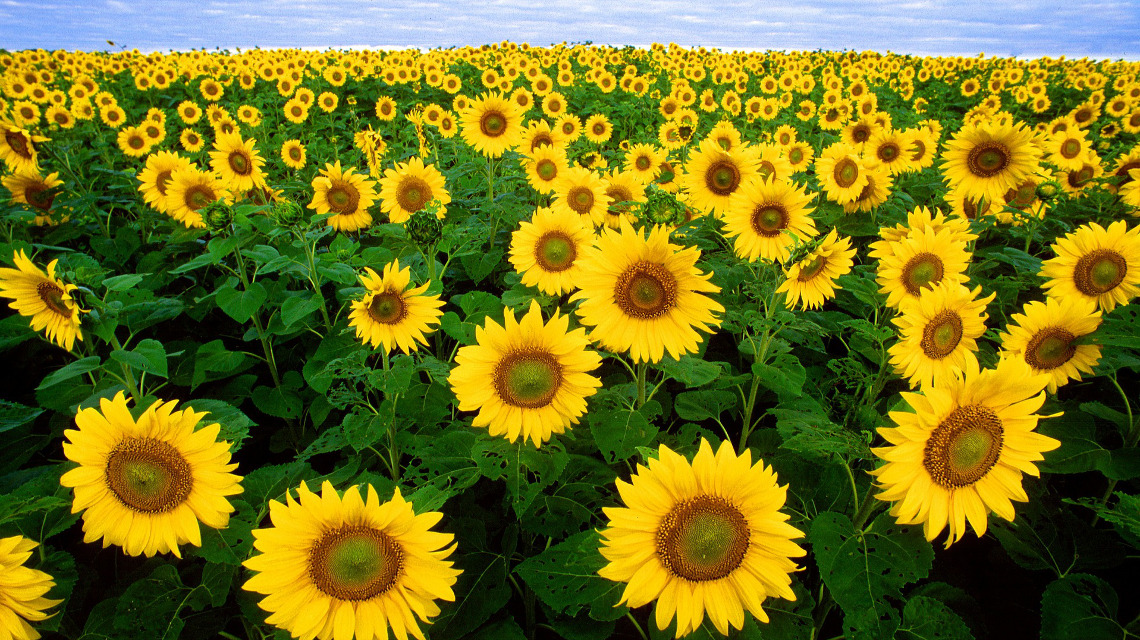
At just under one percent, the share of bio-based plastics on the global market is still very low. However, the global plastics industry is changing. Renewable raw and residual materials are increasingly coming into focus. In the Bio-Polyols project, researchers at Bielefeld University, together with an industrial partner, have now developed a process to produce the important plastic group of polyurethanes from domestic vegetable oils and make them usable for high-performance composites. The project received 78,000 euros in funding from the Federal Ministry of Education and Research (BMBF) from October 2020 to March 2022 during the exploratory phase as part of the "New Products for the Bioeconomy" ideas competition.
Bio-based plastic building blocks for floor coverings
Polyurethane (PUR) is a soft plastic that usually consists of fossil building blocks. These are foamed in combination with moisture and used in a variety of ways, for example in shoe soles, adhesives, but also car seats and flooring. The project focused on the use of bio-based plastic building blocks for floor coverings. To this end, the researchers worked together with Windmöller GmbH from Detmold.
Starting point: high oleic sunflower oil
In order to be able to produce these important PUR plastics from domestic vegetable oils, the Bielefeld team led by project manager Harald Gröger first had to find a suitable vegetable oil. The choice fell on high oleic sunflower oil, which has a high proportion of unsaturated fatty acids. "These unsaturated fatty acids have at least one carbon double bond, which can be chemically functionalized very efficiently," explains Gröger.
For the building blocks produced from the vegetable oil to be suitable for the desired polymer applications, they first had to be functionalized so that these individual modules can be coupled at the ends of the compounds. These modules are molecules, so-called monomers, which are able to form polymers through chemical reactions. "Domestic vegetable oils cannot normally be used as basic building blocks for monomers because they lack a functionalizable group," explains the expert in organic chemistry and biotechnology. According to Gröger, the functional groups required to form the urethane group in the PUR polymers first had to be incorporated for the click reaction needed to build the PUR polymers.
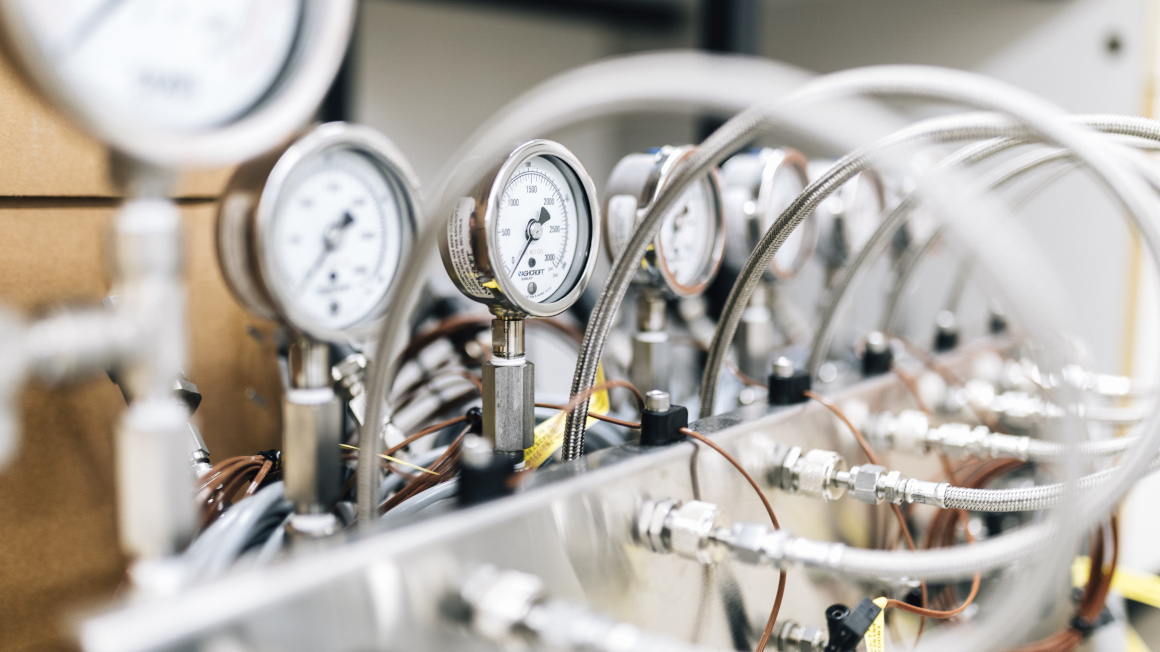
Plant molecules functionalized with hydroxy groups
"The project's idea was to introduce at least two so-called hydroxy groups as such a functional group into the native plant oil molecule. This group can then be linked to the complementary group, the isocyanate group, to obtain the PUR polymers," explains the project manager. Chemical catalysis was used to introduce hydroxyl groups, after which the monomer building blocks were converted into the appropriate PUR foams. "We were able to show that we can use a practicable catalysis technology in two steps - hydroformylation and hydrogenation - to produce a polymer building block from domestic vegetable oil, which proved to be very promising for polymer applications in the flooring sector," summarizes Gröger.
Chemical-catalytic route proved compelling
The key step of this chemical-catalytic route, known as hydroformylation, quickly proved to be very promising. During this process, the unsaturated fatty acids are functionalized with the help of synthesis gas. "Hydroformylation can be carried out without the use of solvents, which is a major advantage. We only have the vegetable oil as a substrate, which we can convert with the metal catalyst and the synthesis gas." It has also been shown that the synthesis process offers attractive economic prospects, as only small quantities of waste are produced. The use of renewable energies in combination with carbon dioxide as the starting compound for producing the synthesis gas would make the process even more sustainable.
According to Gröger, the first samples produced and tested by project partner Windmöller GmbH were also compelling in terms of the required material properties. Both the tensile strength and the speed of curing and shaping of the polymer are promising.
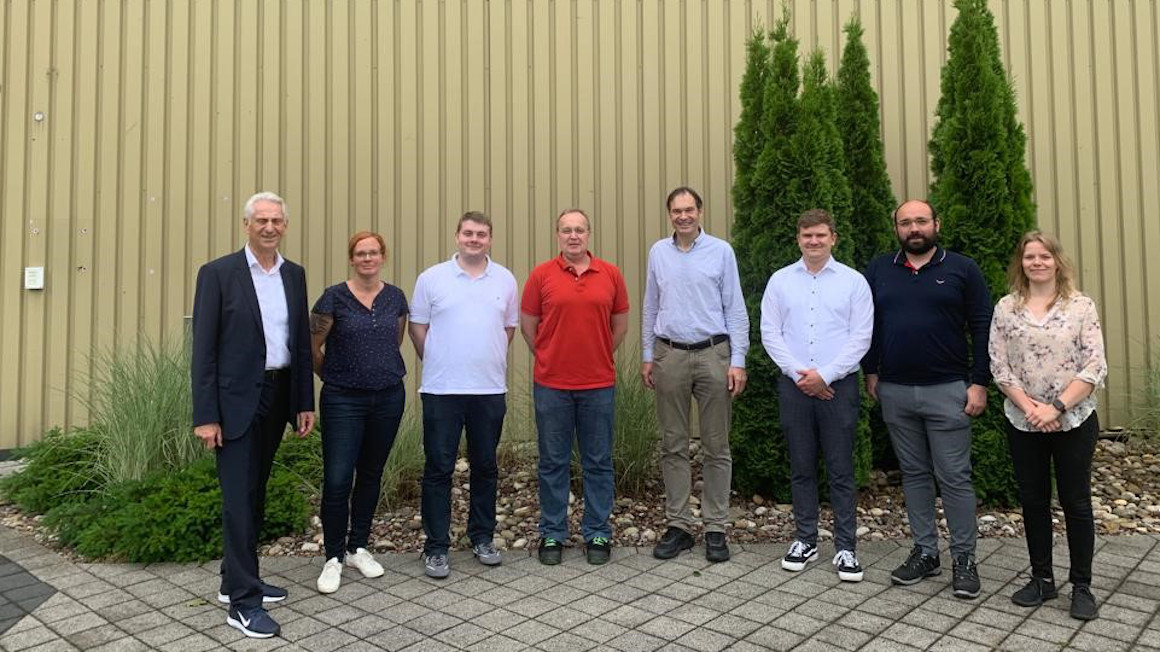
Feasibility phase underway
The two-year feasibility phase started in fall 2022 and is funded by the BMBF with a further total of around 242,000 euros. It will show whether the bio-based polyurethanes are suitable for an insulating layer in floor coverings. According to Gröger, this phase will focus on process optimization and further product development. "We are focusing on how efficiently and sustainably we can manufacture this product - the hydroxy-functionalized vegetable oil - for example by further minimizing catalyst requirements and waste streams. In addition to the scale-up, we also want to further develop the material science aspect so that the product is competitive and can later keep up with conventional PUR polymers based on fossil building blocks."
Author: Beatrix Boldt