Hemp can replace glass fibers in composite materials
Researchers from Zittau provide proof that hemp fibers can be a real alternative to glass fibers in composite materials.
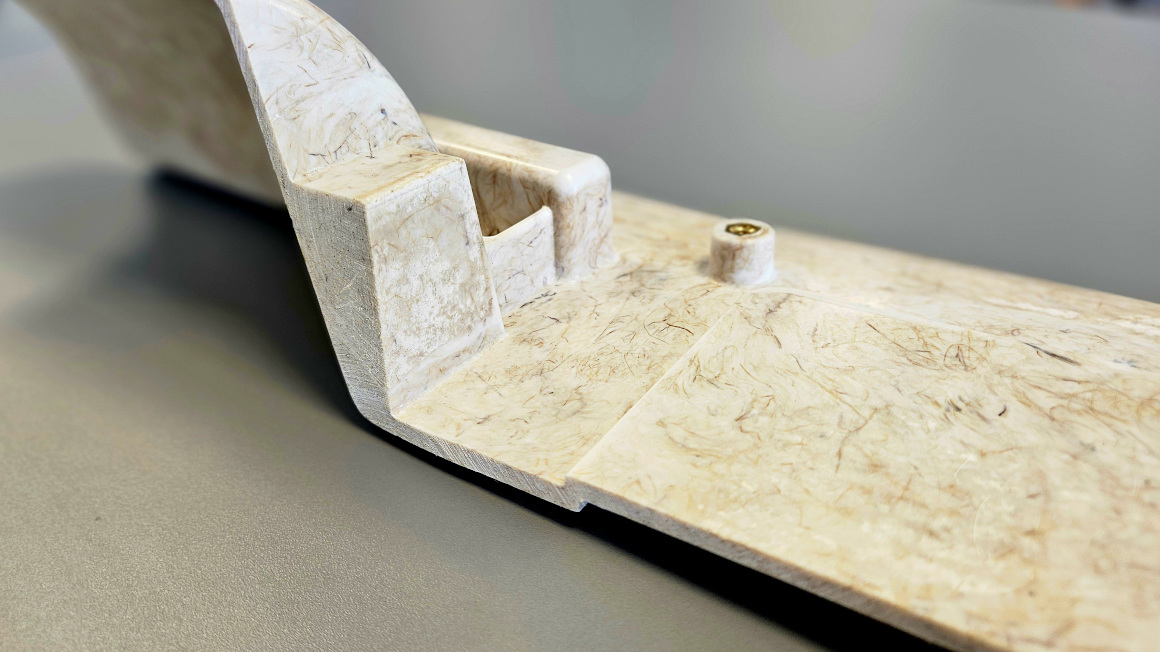
Whether in the home, in sport or in the car: objects made from fiber composites are ubiquitous. By combining several components, such as a plastic matrix with fibers, materials are created that meet the most diverse requirements. Up to now, glass fiber reinforced plastics (GRP) have often been used to produce complex and lightweight molded parts. However, the production of glass fiber releases large quantities of the greenhouse gas carbon dioxide. The recycling and disposal of so-called GRP materials is also problematic. A sustainable alternative to glass fibers could be natural fibers.
Natural fiber SMCs made from hemp for impact extrusion processes
Researchers at the Fraunhofer IWU in Zittau and the Zittau/Görlitz University of Applied Sciences have been working on biological alternatives to glass fibers in composite materials for several years. A team led by Rafael Cordeiro has now shown that glass fibers can be replaced by natural fibers in combination with resin using the example of an interior lining for trains. The new component is a long-fiber-reinforced semi-finished product - so-called sheet moulding compounds (SMCs) - which can be used to produce complex moulded parts with a high surface quality, for example for train interior linings, using an extrusion process.
SMC component with high bio-based content
Only coarse hemp fibers, which are a by-product of textile production using hemp, were used to manufacture the new component. According to the researchers, the weight proportion of natural fibers in the newly developed SMC is around 15%. The use of bio-based resin as a matrix for embedding the hemp fibers should increase the “natural” proportion to up to 38% in the future. A further 55% are natural minerals such as calcium carbonate or aluminum hydroxide hydrate, which occurs naturally as bauxite. 7% of the new SMC consists of fossil-based additives, as there is not yet a bio-based alternative.
“The natural fiber SMC has been developed in such a way that only very small additional plant investments and minimal process parameter changes are required for the production of larger quantities,” says Rafael Cordeiro, research associate at Fraunhofer IWU and in the LaNDER³ project at Zittau/Görlitz University of Applied Sciences. According to the researchers, there are also no significant differences between natural fiber and glass fiber SMCs in the production of semi-finished products and components by impact extrusion in terms of the processes and the energy required.
Another advantage of the natural fiber component: Not only skin and respiratory tract irritation, which can occur on contact with glass fibers, is significantly reduced. Significantly fewer CO2 emissions are released during the production of hemp fibers than during glass fiber production. The usual 30-year service life of hemp fiber-based semi-finished products can also be increased by adjusting the matrix resin.
Longer durability and better ecological balance
The newly developed natural fiber SMCs are still neither recyclable nor fully biodegradable. According to the researchers, however, there are promising attempts to separate the natural fiber from the matrix and the filler so that the natural fiber component can be composted and the filler reused. However, the work of the Zittau team shows that it is possible to produce more sustainable SMC components. “The sustainability balance of natural fiber SMCs is not yet perfect. But it is already much better than that of glass fiber-reinforced composite materials. The material costs are also right. This means that the alternatives we have developed to classic glass fiber SMCs are definitely marketable,” says Cordeiro.
The work of the researchers at the Fraunhofer IWU in Zittau and the Zittau/Görlitz University of Applied Sciences is funded by the Federal Ministry of Education and Research as part of the LaNDER3 strategic partnership via the FH-Impuls funding measure. This provides targeted support for research and innovation partnerships in order to strengthen networking between science and industry in the region.
bb