Vehicle underbody made from new biocomposite material
Together with industrial partners, Fraunhofer researchers have developed a new biocomposite material for the production of vehicle underbodies, thereby significantly improving the carbon footprint of the entire production cycle.
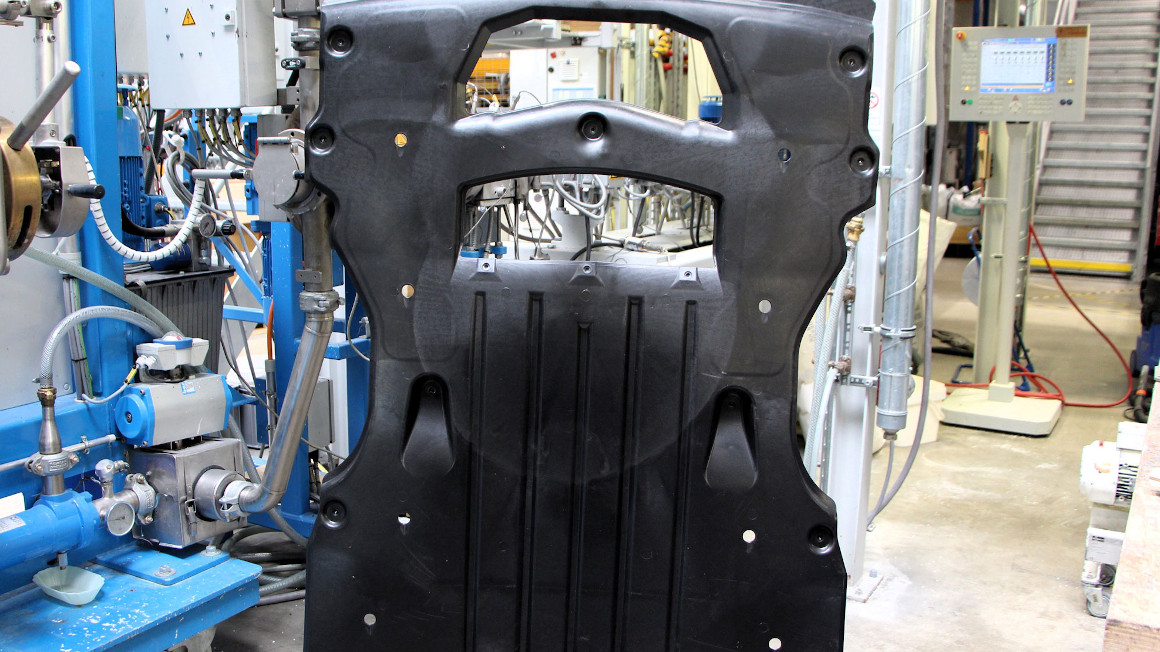
Dashboards made of sisal, door panels made of flax fibres or seat foams made of soya: in the automotive industry, petroleum-based materials are increasingly being replaced by bio-based materials such as natural fibre-reinforced plastics. These are mostly trim parts that are not exposed to high mechanical loads. Components such as vehicle underbodies, on the other hand, have to withstand every crash and are therefore often made of glass fibre-reinforced plastics. A research team has now succeeded in replacing these so-called high-performance materials with high-performance bio-based materials in automotive engineering.
Subfloor made from natural fibres and recycled plastic
Together with industrial partners, researchers from the Fraunhofer Institute for Wood Research – Wilhelm-Klauditz-Institut (WKI) have developed a vehicle underbody made from natural fibres and recycled plastics. By using flax, hemp and cellulose fibres, the vehicle part consists of up to 45% natural fibres. In addition, new polymers such as polypropylene were completely avoided in the production of the natural fibre-plastic compound and only recycled materials were used.
The development of the new component was funded by the German Federal Ministry for Economic Affairs and Climate Protection. In addition to the Fraunhofer researchers, the Thuringian Institute for Textile and Plastics Technology (TITK), Röchling Automotive SE & Co. KG, BBP Kunststoffwerk Marbach Baier GmbH and Audi AG. The WKI team was responsible for developing the bio-based materials for injection moulding. The right combination of compounds was particularly important here.
No loss of rigidity and strength
"Natural fibre injection-moulded compounds are known primarily for their increased strength and stiffness compared to unreinforced polymers. In the development of the vehicle underbody, an innovative combination of selected post-consumer recyclates (PCR) as a matrix and natural fibres of varying degrees of purity has also made it possible to meet the high requirements for cold impact strength without sacrificing the required stiffness and strength," explains Moritz Micke-Camuz, project manager at the Fraunhofer WKI.
The project partners at the TITK and at Röchling finally produced the first fibre composite components (Lightweight Reinforced Thermoplastic, LWRT) from the natural fibre-reinforced mixed fibre nonwoven. The flax and hemp fibres had to be waterproofed so that the subfloor was also protected against moisture. For this purpose, the Fraunhofer WKI developed a furfurylation process for LWRT components, which reduced the moisture absorption of the fibres by up to 35% without impairing the flexural strength of the subsequent components.
Bio-lightweight material suitable for series production
Component tests and road tests with the first prototype components produced were very promising. The test results achieved during series testing in the VW Group's new "Premium Platform Electric" were encouraging. Accordingly, the newly developed biocomposites met all technical requirements for underbody components and proved to be absolutely suitable for series production. Neither the use of natural fibres nor of (post-consumer) recyclates led to any significant impairment of the properties. According to the researchers, from a technical point of view, vehicle underbodies could be made entirely from the new, high-performance lightweight bio-construction material in the future.
CO2 emissions reduced by 40 %
In addition, the carbon footprint of the new vehicle part is also significantly more favourable. By using natural fibres and recycled material, CO2 emissions can be reduced by up to 40 % during production, use and product life, the researchers write.
bb