Plastics - the ubiquitous material
With its sheer endless variety and functionality, plastic is considered the material of the 21st century. Besides its variable technical properties, the carbon-based class of materials also impresses with its high availability and efficient processing methods. Many innovations across all industries succeed only thanks to modern high-performance plastics, which have therefore become indispensable, particularly in transportation, construction, the food industry, healthcare and the energy sector.
Plastics can also contribute to greater sustainability: lightweight materials made from polymers reduce the fuel consumption of cars and aircraft, insulating materials help to reduce energy losses, and packaging helps to increase the shelf life of food. The use of plastics should therefore not be universally condemned. Rather, where their use brings benefits, it is important to drive the transformation from linear to circular value creation.
The three major groups of plastics
Plastics are materials consisting of carbon-containing macromolecules known as polymers. The molecular chains of polymers are made up of repeating basic units, the monomers. The polymers can have linear, branched or cross-linked structures.
Polymers can be obtained from natural substances or produced by synthetic chemical processes. The main raw material for synthetic production was and is petroleum, which is utilized in classic chemical processes such as chain polymerization, polyaddition or polycondensation. In contrast, the bioeconomy relies on renewable natural materials and biogenic residues as a resource. Bioplastics are generally produced with the aid of biotechnological processes.
According to the industry association Plastics Europe, around 390 million tons of plastics were produced worldwide in 2021. 90% of this was based on fossil resources, 1.5% was bio-based and 8.3% of production recycled plastics. In Europe, 57.2 million tons were produced, of which around 10% were recycled plastics.
There are three major groups of plastics: Thermoplastics, Thermosets and Elastomers. They differ in their technical properties:
- Thermoplastics or plastomers can be reversibly formed within a certain temperature range and are also weldable. Typical processing methods are injection molding and extrusion. Important thermoplastics are polyamides (PA), polylactide (PLA), polyethylene terephthalate (PET), polyethylene (PE), polypropylene (PP), polystyrene (PS), polyvinyl chloride (PVC) and celluloid. Thermoplastics are generally recyclable because they can be remelted. However, as with many plastics, additives such as plasticizers, stabilizers or dyes make recycling difficult. Even PET, which is readily recyclable, is still largely thermally processed, i.e. incinerated.
- Thermosets or duromers contain hard, insoluble polymers and are no longer moldable after curing. They exhibit high strength with low weight. However, they decompose when exposed to excessive heat, and they can form cracks under strong mechanical stress. Starting materials are usually synthetic resins with certain additives, which are cured. Further processing is carried out by compression molding, injection molding or layer molding. Important representatives are polyurethane (PU), melamine resin and epoxy resin. Due to the particularly strong molecular bonds, thermosets are considered to be difficult to recycle.
- Elastomers are deformable plastics that return to their original shape after deformation. The best-known examples are the vulcanizates of natural rubber and silicone rubber. They are used, among other things, in tires or rubber bands. Recycling is just as difficult here, but downcycling is already taking place on a large scale, i.e., the recycled product loses quality.
There are also composite materials in which plastics are combined with metallic, ceramic or organic fibers. Here, too, the close connection of the components makes recycling difficult.
Global plastics production by material type in 2021
Source: Plastics Europe 2022 (according to Conversio Market & Strategy GmbH and nova-Institut)
Page 2 of 7
The plastic problem
The special technical properties of plastics become a problem when they are disposed of in the environment after use and pollute natural areas.
In Europe, 29.5 million tons of plastic waste were generated in 2020, according to the European Plastics association. Of this, 35% was recycled, 42% was incinerated and 23% ended up in landfills.
In Germany, there was a total of 5.4 million tons of plastic waste in 2020, of which 42% was recycled, 57 % was incinerated and about 1% of plastic waste ended up in landfills. Just over 2 million tons of plastic recyclate (recycled plastic) was processed.
Packaging materials are the largest source of plastic waste. They often have an exceptionally short life cycle - in fact, sometimes only a few minutes pass before they are disposed of again. During the Corona pandemic, the use of single-use plastics in medicine (such as in masks, visors, gloves and rapid tests) also increased enormously.
The Great Pacific Garbage Vortex between California and Hawaii has also achieved sad notoriety: at 1.6 million square kilometers, it is three times the size of France and weighs an estimated 80,000 tons.
There are microplastics that come loose when textiles are washed (dealt with in the TextileMission research project), and abrasion from car tires (studied in the RAU research project). Such plastic residues can now be found everywhere: They enter sewage treatment plants via wastewater and even reach the Alps with the wind. The quantity and composition of microplastics on agricultural land, for example, has been investigated by the BMBF-funded µPlastic research project. The PLAWES research project analyzes the microplastic problem in the Weser and Wadden Sea. In total, the Ministry of Education and Research (BMBF) is funding 20 collaborative projects on the topic of "Plastics in the Environment".
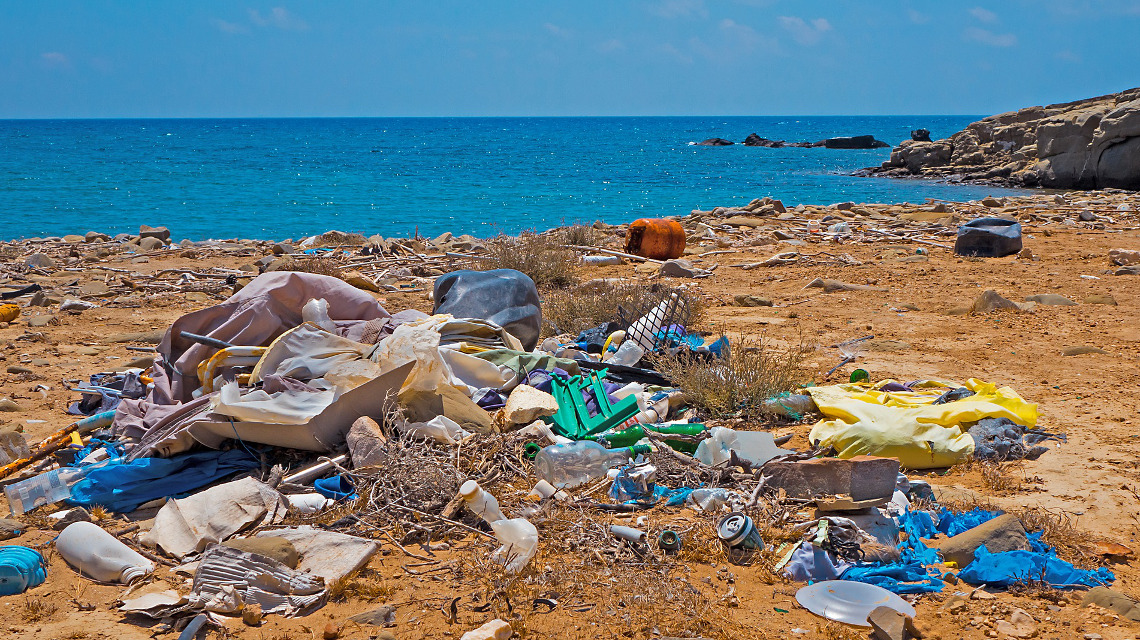
Why plastics last so long
The fact that so many plastics accumulate in the environment is due not only to improper disposal but also to the fact that most types of plastic are poorly biodegradable, if at all: Naturally occurring microorganisms generally do not have the appropriate enzymes to break down the bonds between polymers. This is especially true for the C-C compounds in hydrocarbons. Most polymers cannot even pass through the cell membrane of living microorganisms. However, researchers are increasingly detecting microorganisms that have developed the ability to degrade and digest plastics (see Chapter 4).
Wind and weather break down plastic pieces that have entered the environment, but microplastics remain. Only UV radiation from the sun can break the bonds of the polymers to a certain extent, causing the material to become brittle and yellowish. This has consequences for nature and health: while the polymers have so far been considered harmless to health, the situation is different for some additives: bisphenols, which are used as hardeners, increase the risk of obesity, diabetes, infertility, several types of cancer and lead to developmental damage in children. The same applies to phthalates, which are used as plasticizers. In addition, so-called endocrine disruptors, i.e. hormonally active substances, are already used in the manufacture of plastics and can now be detected in the blood, urine or fatty tissue of virtually everyone. The World Health Organization (WHO) considers it proven that endocrine disruptors are involved in the development of breast and prostate cancer, infertility, diabetes mellitus, cardiovascular diseases, thyroid disorders, and neurological, neurodegenerative and psychological diseases in humans, among others.
Animals too suffer from these effects when they ingest such substances. In their case, however, they also mistake small plastic parts for food and then starve to death with a full stomach or die from internal injuries. Large pieces of plastic in waters also cover coral reefs, sponges or mussel beds and prevent them from colonizing. Research has even shown that microplastics affect the growth of plants because they change the structure of the soil.
Page 3 of 7
On the way to a circular plastics economy
Traditionally, the plastics industry has been linear. In a circular economy, however, the aim is to minimize the use of non-renewable resources and the generation of waste. The service life and life cycle of materials is determined by reuse and recycling.
The European Union's plastics strategy published in January 2018 ("A European Strategy for Plastics in a Circular Economy") is leading the way in establishing a plastics circular economy. Among other things, it formulates the following goals:
- Plastic recycling is to be improved economically and qualitatively by 2030: All plastic packaging is to be reusable or recyclable.
- Plastic waste as well as environmental pollution caused by plastics are to be curbed.
- A more effective circular economy is to be established along the entire value chain.
To reduce the problem of plastic waste, the European Union has also introduced a ban on numerous disposable products, which has been in force since July 3, 2021. In Germany, for example, this affects 320,000 disposable cups for hot drinks per hour. The German government has also taken other measures: since 2022, there is a mandatory deposit on single-use plastic beverage bottles, which is to be extended to plastic bottles containing milk beverages in 2024. From 2025, single-use PET beverage bottles must contain at least 25% recycled material. A ban on exports of hard-to-recycle plastic waste has been in place since January 1, 2021.
Apart from avoiding the use of plastics, the overarching goal is to transform plastics production into a closed loop and to develop ways of biodegrading plastics. This includes replacing petroleum with bio-based raw materials and developing new bio-based, biodegradable plastics.
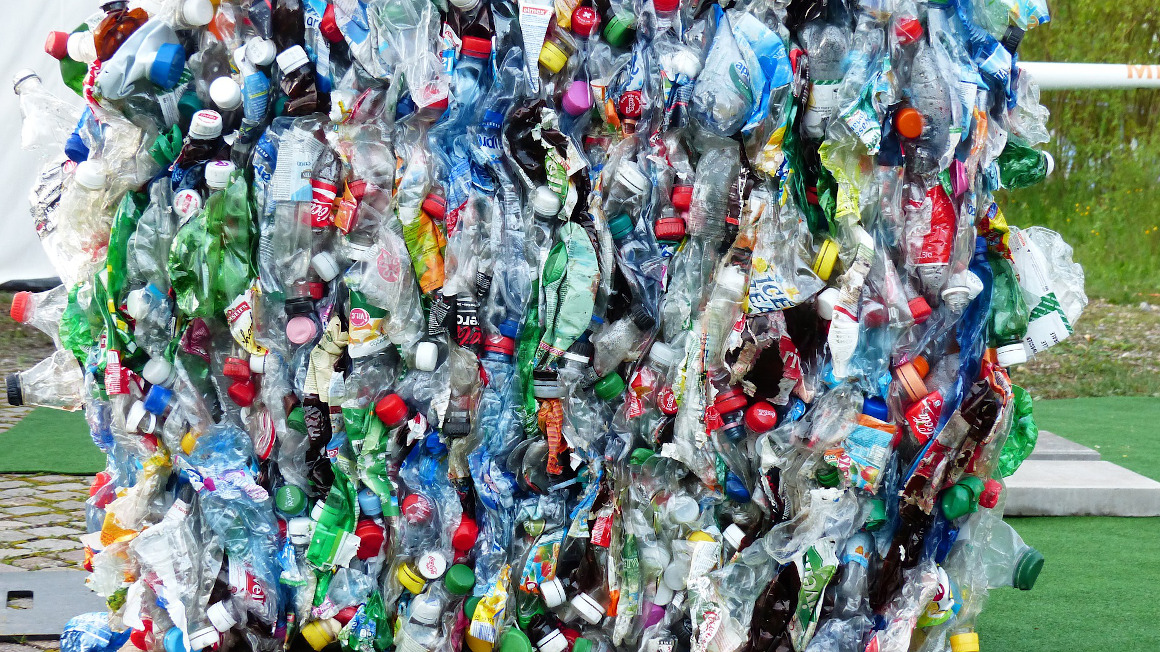
Mechanical and chemical recycling technologies
The following technologies are relevant for plastics recycling:
Mechanical recycling, in which plastics are shredded into small pieces and treated with heat, is well suited if single-variety materials are available. These include single-variety thermoplastics such as PE, PP, PVC, PET and PS. The recyclability reaches its limits with heterogeneous products. With the proprietary revolPET process, which emerged from a research project, even complex composites and mixtures can be prepared in such a way that the different PET monomers have the same quality as newly synthesized monomers. At the same time, the process does not alter other plastics such as PE, PP and PA, so that these could be recycled in further steps.
In chemical recycling, plastics are broken down into their basic chemical building blocks, which then serve again as the starting material for a wide variety of products. Thermochemical recycling processes include solvolysis, pyrolysis and gasification. Today, the processes often still tend to deliver a mixture of hydrocarbons and CO2, and are also very energy-intensive. In combination with mechanical recycling, however, they hold great potential, which is currently being intensively developed by industry players.
A recycling process also exists for polystyrene by means of depolymerization and subsequent re-polymerization. Progress in this area was made by the ResolVe research project funded under FONA. The international ISOPREP research project has developed a process for recycling PP. The solvent-based approach delivers a recyclate that is qualitatively equivalent to new PP.
Studies of plastics recycling in Germany have shown that inadequate sorting makes recycling more difficult. Additives of different plastics that mix during recycling also reduce the quality of the recyclate. If plastics are sorted by type, the industry already achieves high recycling rates, for example 94% for PET bottles in Germany.
Tracers, fluorescent markers that support the sorting machines, could create greater grade purity. The BMBF research project MaReK is an example of this. There are also several free tools that advise companies on how to optimize their packaging for recycling. With the EcoCircle initiative, for example, industry is also pursuing the goal of transforming plastics production into a circular economy and, to this end, specifically developing plastics for recycling.
Biotechnological recycling processes can not only simplify sorting, but also replace existing mechanical or chemical processes. The prerequisite for this is to tap enzymes that can decompose the plastic in question. Numerous examples will be presented in the next chapters. Last but not least, biotechnological processes sometimes even enable upcycling, i.e. reprocessing creates a higher-value product compared to the starting product.
Page 4 of 7
Biological recycling: Bacterial enzymes crack polymer chains
Microorganisms have existed on earth for billions of years and have developed enormously diverse metabolic pathways in the course of their evolution. Fascinatingly, some bacteria possess enzymes with the help of which they can also break down the molecular chains of plastics.
In 2016, the bacterium Ideonella sakaiensis 201-F6 was discovered in a recycling yard for PET bottles in Japan. It is able to grow on PET and feed on it. The key enzyme for PET degradation is a hydrolase that has been named PETase. It breaks down PET into so-called MHET - and the bacterium also has an enzyme for its degradation, MHETase. This process produces ethylene glycol and terephthalic acid - the very building blocks from which PET is made. A few years ago, a team of researchers from Greifswald and the Helmholtz Center Berlin elucidated the structural biology of how these two enzymes work. On this basis, researchers have now not only further optimized PETase, but have also merged PETase and MHETase into a single enzyme that works six times as efficiently as the two enzymes on their own.
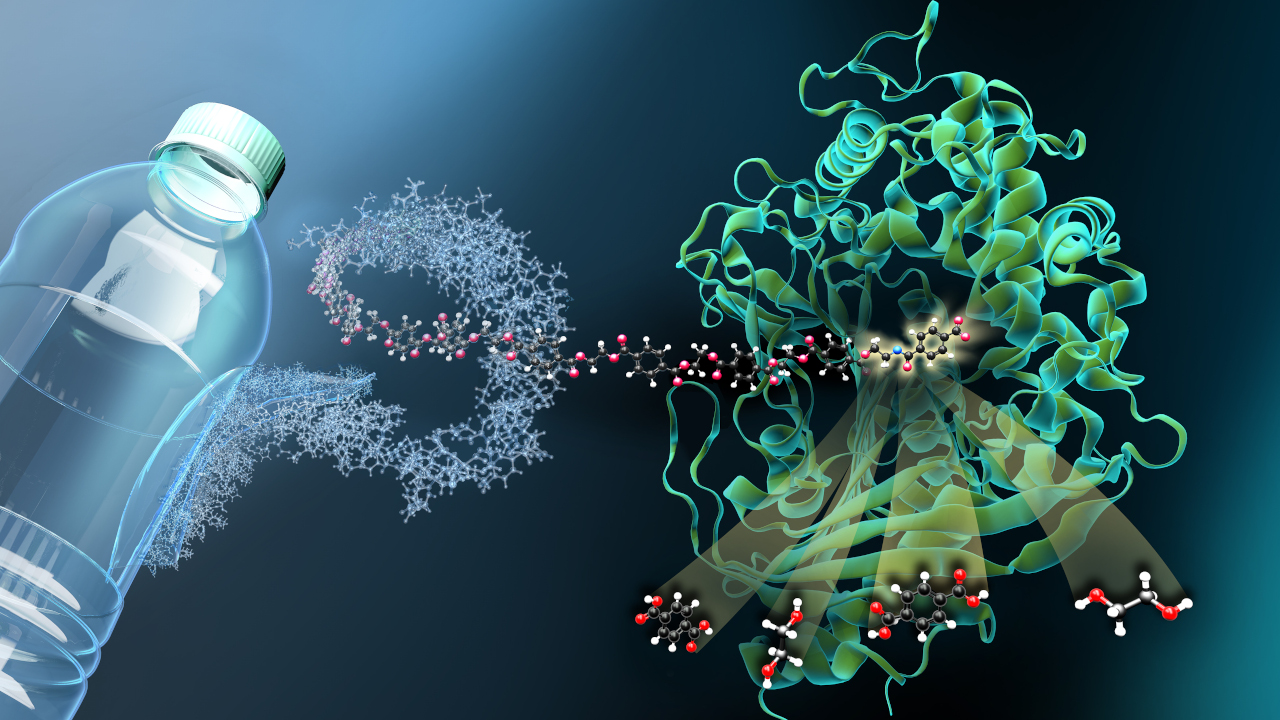
The groundbreaking discovery from Japan spurred numerous international and national research activities. The EU consortium P4SB, coordinated by RWTH Aachen University, used representatives of the bacterium Pseudomonas putida optimized by means of synthetic biology for PET degradation. The project was very successful. To do this, the researchers heated the plastic to 70 degrees, causing it to lose its crystalline structure. However, the enzyme esterase tolerates this temperature. The bacteria not only decomposed PET, the team also made progress in PU degradation. This is particularly challenging because PU hides a whole group of plastics.
Ultimately, the researchers in the project succeeded in producing the bioplastic PHA from the degradation products. Another advantage of the optimized microorganisms is that they can select suitable substrates from a mix of plastic waste and metabolize up to four different monomers simultaneously. Contaminants such as food residues do not interfere with this process - unlike in a chemical recycling process - but are simply additional food for the bacteria.
In the follow-up project MIX-UP, a European-Chinese cooperation, the researchers want to fully exploit the advantages of biotechnological recycling and develop solutions to bacterially degrade mixed plastic waste without prior sorting. A process is planned that can process fossil-based plastics (PP, PE, PUR, PET and PS) as well as the biodegradable plastics PLA and PHA. The degradation products can then be used to produce bioplastics by fermentation.
PET-degrading enzymes are also being researched in Leipzig: A team at the university has spent many years studying the bacterium Thermobifida cellulosilytica, which possesses enzymes known as cutinases that can break PET down into its building blocks.
Initially with the aim of cleaning up water bodies, the PlastiSea research project is screening seawater for bacteria that can degrade one of the plastics PET, PU, PE, PA or PEF. This search could also lead to new approaches for recycling other plastics. One promising find is the bacterium Pseudomonas aestusnigiri, which can degrade plastics. Saltwater bacteria are difficult to cultivate, but their enzymes can be genetically transferred into other microorganisms that are better suited for industrial processes. The research team has already been able to break down polyester and PET into their basic building blocks.
Page 5 of 7
Industrial application for biological PET recycling
One approach to biotechnological PET recycling has already made it into industrial application:
The French biotechnology company Carbios, together with the Toulouse Biotechnology Institute (TBI), has developed a process in which PET is broken down into its two basic building blocks - ethylene glycol and terephthalic acid - with the help of enzymes. In a second step, the recovered monomers are then used to produce PET for bottles again. The cycle is thus closed.
Carbios' team reported on the approach in the scientific journal Nature, causing a worldwide sensation. In the metagenome of a compost heap, the researchers discovered a hydrolase called LLC (leaf compost cutinase). The bacterial enzyme already naturally breaks down PET much more efficiently than other known PET hydrolases. Using protein engineering, the French researchers have further increased the enzyme's activity. Carbios has also developed a process that allows the two monomers to be recovered in a quality that makes it possible to produce PET from them again.
In 2021, an industrial demonstration plant was commissioned in Clermont-Ferrand, where Carbios is testing its technology. All process steps from the pretreatment of PET waste to monomer production are linked here. In collaboration with Indorama Ventures - the world's largest producer of recycled PET - a commercial biorecycling plant is currently being built in Longlaville near Luxembourg: 50,000 tons of PET waste per year will be processed and recycled here. The plant is scheduled for completion by 2025.
Biotech recycling also opens up new possibilities for textile recycling: A consortium founded in 2022 with On, Patagonia, PUMA and Salomon is testing how textiles made from polyester can be recycled using Carbios technology.
Page 6 of 7
Degrading biobased plastics PLA and PHA with enzymes
Microbial degradation processes also exist for the naturally biodegradable plastics PLA and PHA. It has been known for at least 25 years that bacteria from the actinomycete group in particular can use PLA as food and break it down into lactic acid monomers with the aid of enzymes from the lipase group. However, the biological process is very slow at normal ambient temperatures, which is why chemical processes such as the proprietary CreaSolv process have dominated recycling to date. Another part of PLA waste is composted industrially.
However, a collaboration with researchers from FZ Jülich, RWTH Aachen University and the University of Leipzig has developed a potentially competitive alternative: Their strain of Pseudomonas putida can digest PLA as well as PET, provided the unsorted plastic mix has already been enzymatically pretreated. In just four days, the bacteria then decompose pieces of plastic that would not have decomposed in nature after 400 years.
The French company Carbios has also developed an enzymatic technology for the biodegradation of PLA-based single-use plastics.
The term PHA covers a wide range of polyesters that are naturally formed by a number of bacteria as energy and carbon stores. Since PHA is completely biodegraded by the enzyme PHA depolymerase in a comparatively short time, not only during industrial composting but also under environmental conditions, biotechnological recycling has so far attracted little interest. In contrast, the microbial degradation of PET and PU by bacteria that produce PHA directly from them is being studied more intensively.
Page 7 of 7
Optimizing plastics for biodegradation
Another approach to promoting biotechnological plastics recycling is to modify established plastics so that they become amenable to enzymatic degradation, or to develop completely new plastics. What most developments in this field have in common, however, is that they initially aim to help degrade plastics in nature in a short time. As soon as the economic conditions are right, however, this automatically lays the foundation for recycling processes.
Tapping the properties of PHA and PHB
Polyhydroxyalkanoates (PHA), which can form such diverse structures that they can be used to produce both thermoplastic and elastomeric materials, have great potential for plastics recycling. In the BMBF SusPackaging project, for example, researchers have developed a new PHA structure and an optimized production process, making the biodegradable material well suited for small disposable packaging.
The plastic polyhydroxybutyric acid (PHB) is a different case: The material is bio-based and readily biodegradable - but its technical properties can still be improved. In the BMBF research project PHB2Market, the participants have therefore developed composite materials that are less brittle and stable for longer. Since it is a thermoplastic and the additives are also biobased, the researchers assume that the PHB composite is also biodegradable and recyclable. The PHB optimized in the PHABIO project is also considered fully biodegradable, according to those involved. However, the focus here was on producing the plastic from animal waste fats with the help of the bacterium Cupriavidus necator - a somewhat different form of recycling.
DIE BIOPIONEERS - Portrait: Marieluise Lang - The Bioplasticist
The researchers in the EU project Glaukos are also thinking in product-oriented terms: Here, biodegradable plastics are to be developed for use in textile fibers and coatings for clothing, but also for fishing nets. If these products get into nature, they will biodegrade. The goal, however, is to recycle the fibers in a targeted manner, which is why microbial processes are also being developed for this purpose. The BMBF's Ensure research project is similarly specific: Here, the researchers want to help the plastics PE, PET and PBAT achieve better biodegradability with the help of suitable additives.
In the EU project UPLIFT, the participants want to optimize plastics for upcycling. The depolymerization of plastics - i.e. their decomposition into their individual components - is to be combined directly with other biobased components in order to produce new plastics microbially. If possible, this process should be able to be integrated into existing recycling and fermentation processes.
Because even biodegradable plastics such as PLA and PCL do not always undergo satisfactory microbial decomposition, a research team in the USA has integrated enzymes that degrade these plastics directly into the plastics in the form of nanometer-sized particles. If the plastics are moist and heated to at least 40 degrees - as in industrial composting - this activates the enzymes and they completely decompose the plastic. The process aims to prevent microplastics from remaining in industrial compost. However, in principle it would be possible to produce plastics again from the decomposition products.