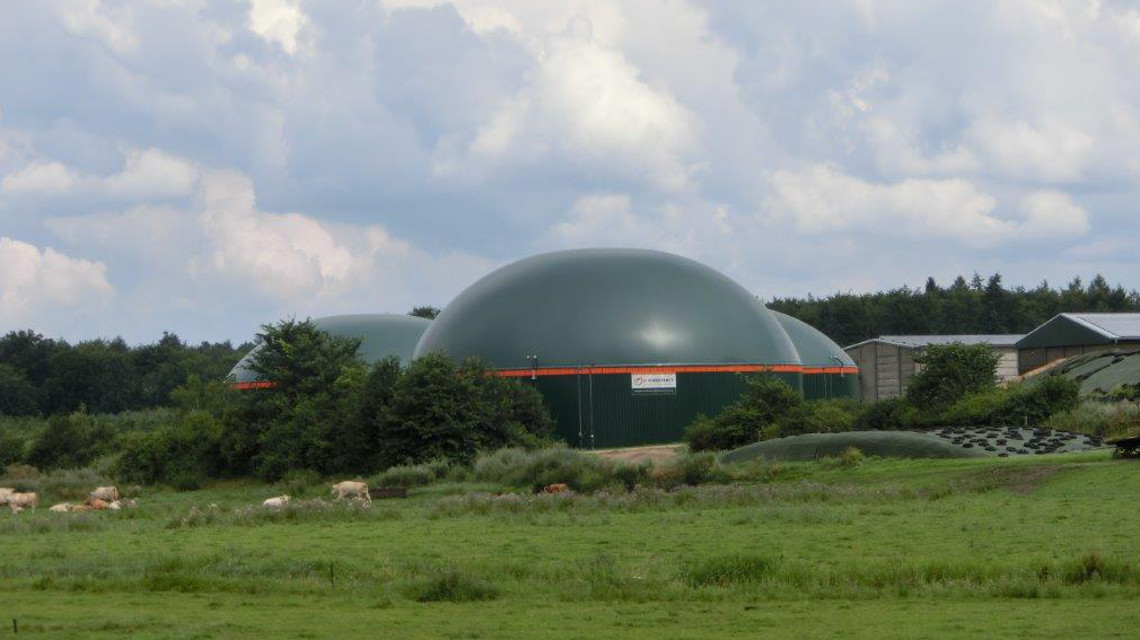
Greenhouse gases such as carbon dioxide (CO2) and methane (CH4) fuel global warming and are major drivers of climate change. However, in order to achieve the Paris climate targets, emissions will need to be significantly reduced or, ideally, avoided. The use of carbon dioxide and methane as a raw material can make a significant contribution to this. This is where the Biogasohol project comes in. Researchers at the Leibniz Institute for Catalysis (LIKAT) in Rostock want to convert the two gases from biogas into an important basic chemical, synthesis gas. Synthesis gas is a mixture of carbon monoxide (CO) and hydrogen (H2). The three-year project is being funded by the Federal Ministry of Education and Research (BMBF) with around 518,000 euros until April 2024 as part of the "Bioeconomy International" funding initiative. Partners in Vietnam are also participating in the project.
New catalysts and processes for synthesis gas production
Even when using renewable raw materials to produce biogas, environmentally harmful greenhouse gases are released. This is because biogas contains around one third CO2 and two thirds CH4 as well as impurities, for example trace elements in the plant material such as sulphur. Currently, the CO2 is isolated in biogas plants and released into the environment, while methane is burned in combined heat and power plants. The research team led by Udo Armbruster from LIKAT wants to return these valuable material flows to a closed material cycle. To this end, new catalysts and processes have been established in the project to produce synthesis gas sustainably.
Focus on the dry reforming process
"The classic way to produce synthesis gas from carbon-containing material is to vaporize it with water at very high temperatures and then convert it into synthesis gas on a solid catalyst. However, this is an energy-intensive process," explains Armbruster. In the conventional process of steam reforming, huge quantities of water are heated to extremely high temperatures of more than 700 degrees Celsius. The project therefore used the dry reforming method to convert methane and carbon dioxide into synthesis gas. "With dry reforming, there is a better heat balance because no water is added and only small amounts of water are formed in the system," explains the chemist.
Nickel catalyst modified
Dry reforming takes place at lower, but still high temperatures. Just like dry reforming, it places high demands on the materials used in the process. With a view to large-scale production of synthesis gas from biogas, the scientists therefore had to find a suitable catalyst that reacts quickly at these temperatures and enables a high yield. Benefiting from years of catalyst research, the Rostock team was able to establish an efficient replacement for the expensive precious metal catalysts. "We focused on nickel catalysts because we know that they can carry out our target reaction very efficiently. However, as it is not usually possible to use simple nickel metal, we had to add specific properties to make the catalyst stable and active," explains Armbruster.
In order for the nickel-containing catalyst to work in dry reforming, the team had to overcome a number of hurdles.One general problem was carbon formation. Nickel binds a lot of carbon very quickly, which is produced during dry reforming through the degradation of methane and carbon dioxide. The catalyst therefore had to be modified so that it produces as little carbon as possible but remains highly active in order to activate methane and CO2. "By changing the acid properties, the catalyst became more alkaline so that CO2 could be adsorbed particularly well and carbon formation could also be avoided," explains Armbruster.
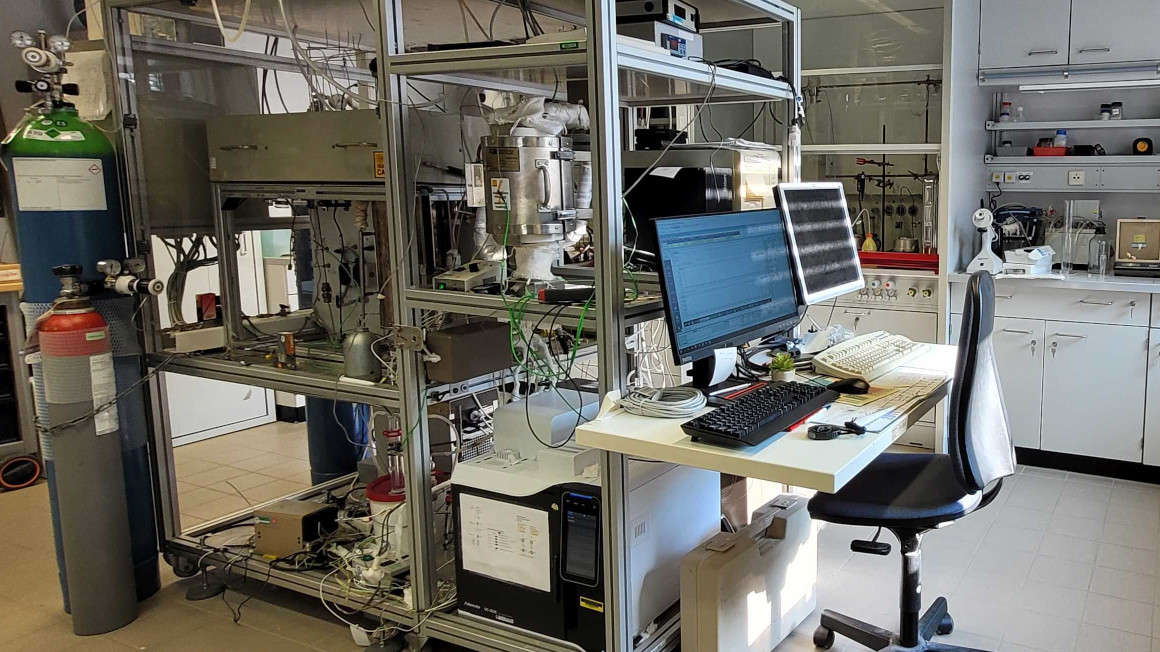
With a view to large-scale industrial production, both the catalyst and the dry reforming process are being scaled up as part of the project. Among other things, the surface area of the nickel-containing catalyst had to be increased for this purpose. Specifically, the powdered catalyst was processed into granulate, which offers a larger surface area due to its porous nature. "The coarse-grained material has gaps between the granules through which the gas can flow. However, we have also tried to apply the active material to monoliths, or in other words ceramic blocks," adds Armbruster. At the same time, the nickel catalysts have been used in combination with a carrier material such as magnesium-aluminum oxide, which has a larger surface area and is very stable at high temperatures.
Nickel catalyst cost-effective and powerful
"We see great potential in our nickel catalyst as it is very cost-effective. Furthermore, we work with a metal content of only 2.5%, but the activity is so high that it is comparable to catalysts containing ten times as much nickel. This makes the catalyst very powerful and stable. We can convert more feedstock on the catalyst in the same time as other catalysts," summarizes the project manager.
Synthesis gas conversion at 90%
Corresponding tests in the LIKAT laboratory with simulated biogas show that the nickel catalyst converts around 90% to synthesis gas during dry reforming - at a ratio of 1:1 for CO2 and CH4. However, the research is still ongoing. The team has applied for a project extension. "Next, we want to see how quickly interfering components such as ammonia and hydrogen sulphide contaminate our catalysts. Once this has been completed, the partners in Vietnam will continue to work with our catalyst on a larger scale," says Armbruster.
New source of income for biogas operators
As a final step, the LIKAT researchers' new technology will be tested in Vietnam in a pilot plant with real biogas, and the planned conversion of synthesis gas into methanol will also be realized. At the same time, the entire process chain will be evaluated for its economic viability. Armbruster is convinced that the conversion of biogas into synthesis gas would offer biogas operators new revenue streams. With regard to further processing into methanol, he believes that decentralized plants in the vicinity of biogas plants could be a solution.
Author: Beatrix Boldt