Bio-based lightweight components for vehicle construction
Together with partners, Fraunhofer researchers want to develop material-saving processes for the production of durable components made of fibre-reinforced biopolymers and thus reduce the CO2 content in vehicle components by up to 50%.
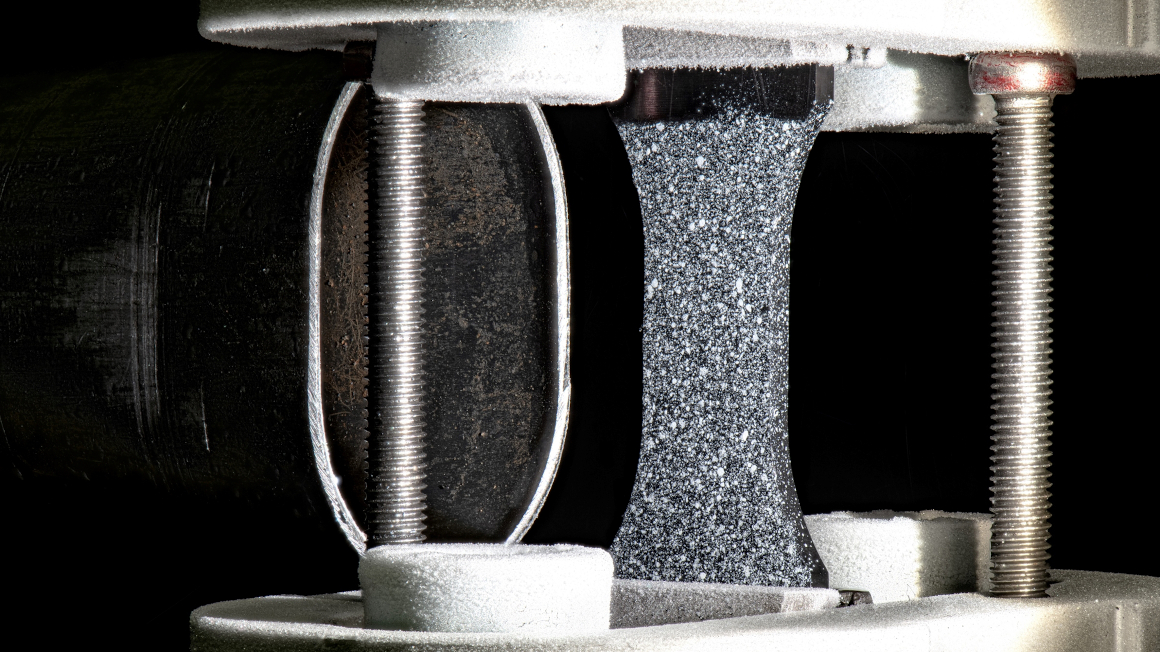
Whether dowels, egg spoons or armature boards: plastics are omnipresent. Because the mostly petroleum-based materials are light, durable and versatile in industry. At the same time, their production from fossil raw materials often releases large quantities of the climate-damaging greenhouse gas CO2. Experts therefore see great potential in the use of bio-based plastics in lightweight construction to reduce CO2 emissions in industry. In the COOPERATE project, researchers from the Fraunhofer LBF, together with partners, now want to replace lightweight construction components made from petroleum-based plastics with bio-based alternatives. At the same time, the team is working on material-saving methods to improve the eco-balance and sustainability of production.
Reducing the CO2 share in vehicle construction
The goal is to reduce the CO2 content in the production of plastic parts in vehicle construction by up to 50%. "We focus on the matrix material in the composite and halve the emissions there compared to conventional plastic with 9 kilograms of CO2 per kilogram to 4.5 kilograms of CO2 per kilogram of product weight," says Georg Stoll, project manager and scientist at the Fraunhofer LBF in Darmstadt. "The weight savings in the vehicle area also allow the consumption of drive energy to be reduced, which in turn reduces the CO2 footprint."
Durable lightweight components made from biopolymers
The project team is pursuing two approaches: On the one hand, conventional plastics are to be replaced by bio-based plastics or fibre-reinforced biopolymers obtained from agricultural residues. Here, the researchers want to optimise a biopolyamide obtained from linseed oil for durable, vibration-loaded lightweight components.
Development of material-saving processes
On the other hand, material-saving processes for the production and design of components are to be developed in order to reduce material use and thus greenhouse gas emissions already in this phase. The aim is to achieve a material saving of 20 to 30%, taking into account the stressability of the material. "We simulate both the manufacturing process and the component behaviour. In this way, we can already see in the virtual design and development process how the component must be optimally designed in order to consume less material," says the project manager.
In addition to the Fraunhofer LBF, the partners involved are BOGE Elastmetall GmbH, a manufacturer of vibration systems and plastic components for the automotive industry, TECNARO GmbH, which develops bioplastics and biocomposites from renewable raw materials, and the Chair of Carbon Composites (LCC) at the Technical University of Munich.
The necessary models to describe the material behaviour in the finished component are being developed at the Fraunhofer LBF and at the LCC of the TU Munich. Sample geometries are currently being produced from the bioplastic by injection moulding and characterised on test benches at the Fraunhofer LBF. In this way, the team wants to gain knowledge about the influence of certain parameters such as temperature or humidity in the component geometry on the stiffness and operational strength of the material.
Wider use of bio-based plastic components in industry
With the new material-saving processes and the improved material properties relevant to lightweight construction, the project team wants to pave the way for the use of bio-based plastics in other fields of technology and application such as mechanical engineering. "Bio-based plastics are becoming increasingly efficient and nowadays achieve almost comparable properties to their fossil counterparts, which have been highly optimised over many decades. Designing a sustainable component that can bear the same loads with less weight than a component made of greenhouse gas-intensive materials is nevertheless a major challenge," says Stoll.
bb