Better recycling of rotor blades
Researchers want to optimize existing recycling concepts for the efficient reuse of raw materials from rotor blades of old wind turbines.
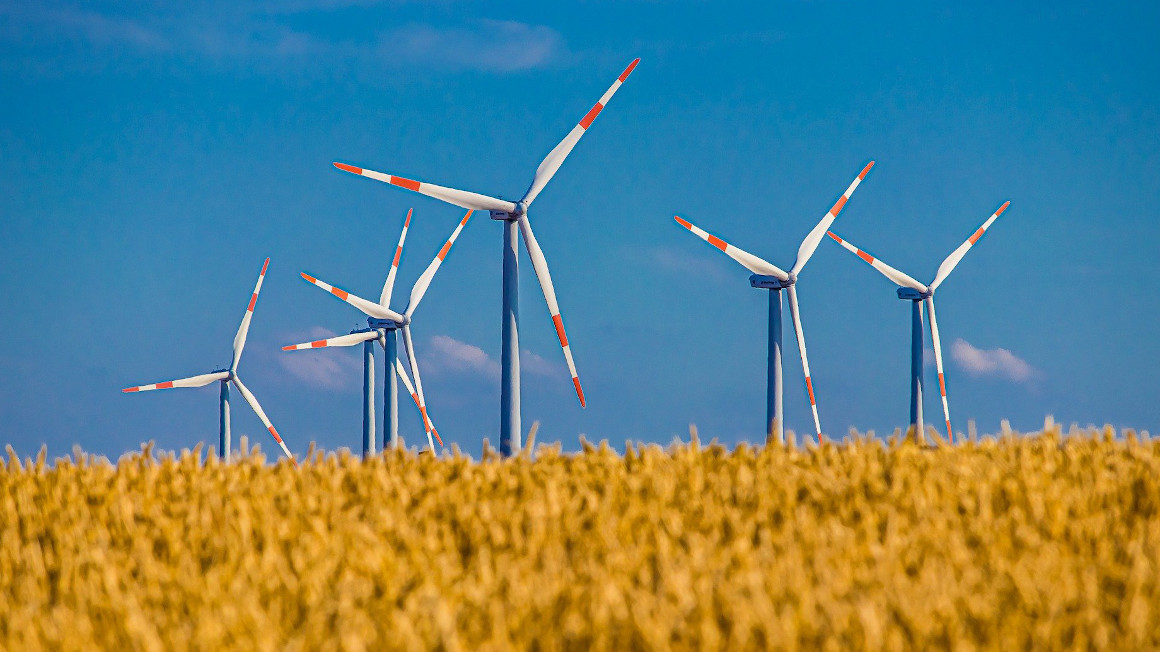
By 2045, Germany wants to become climate-neutral. This means that no more CO2 is to be emitted than can be absorbed by forests or other means. To achieve this goal, the German government is relying, among other things, on the expansion of renewable energies, and this includes wind turbines (WT). With the discontinuation of EEG subsidies last year, the first wind turbines have already been taken out of operation after 20 years. However, wind turbines contain valuable raw materials that have so far been insufficiently recycled. Researchers from the Fraunhofer Institute for Wind Energy Systems IWES, together with the Institute for Energy and Circular Economy (IEkrW) at Bremen University of Applied Sciences, therefore want to develop a new concept that will make it possible to better recycle and reuse rotor blades in the future. The project is being funded with 150,000 euros as part of the "Research for Sustainable Development - FONA3" program of the German Federal Ministry of Education and Research (BMBF).
Sustainable recycling concept for rotor blades
"Holistic conceptualization is essential to create a sustainable recycling concept for rotor blades that gives the wind industry a clear framework to create a competitive market for secondary products and disposal. For this, we need concrete implementation strategies," explains project coordinator Steffen Czichon, head of the rotor blades department at Fraunhofer IWES.
Concrete and steel make up the lion's share of a wind turbine at around 97%. These materials are already easy to recycle. But the rotor blades also contain valuable raw materials - such as fiber-reinforced plastics (FRP) with carbon and glass fibers. When the wind turbines are dismantled, these are currently shredded and transported away directly at the site. The carbon-containing materials are separated from the other materials for recycling, as are the thick-walled flange areas with the metal bolts or metal sleeves.
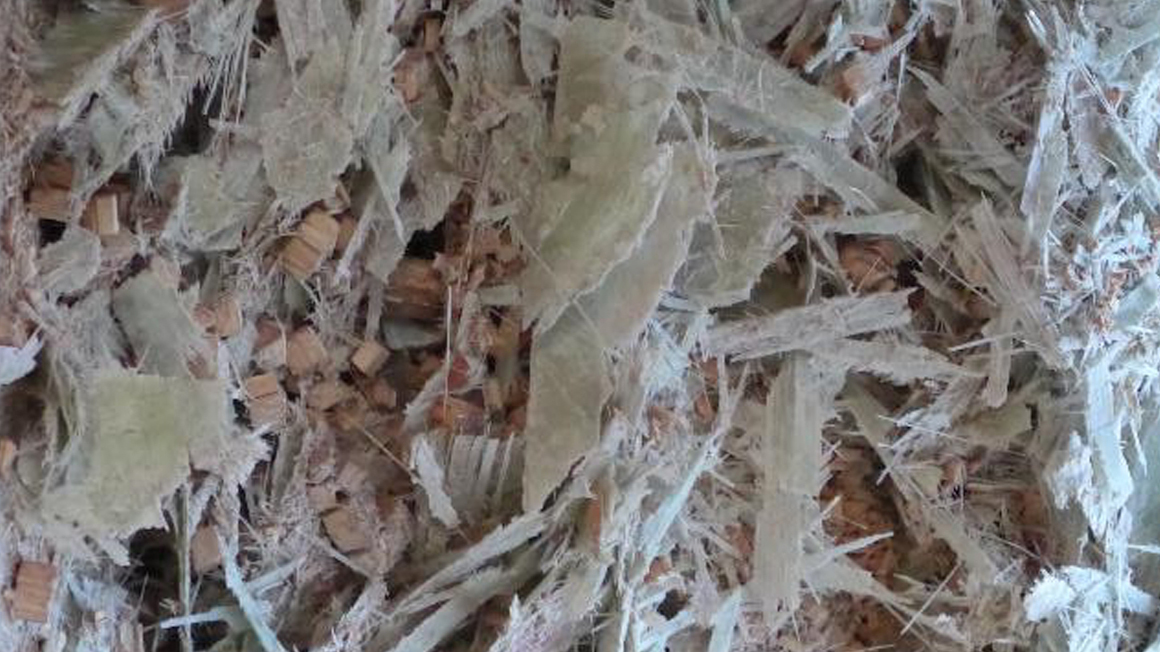
Better recycling rate also for secondary raw materials
The main part of the rotor blades with a matrix of glass-fiber-reinforced plastic resins (GRP), including the so-called sandwich materials such as balsa wood or plastic foams built into them, is shredded and used in the cement industry as a substitute for sand and chalk. The CFRP components are then recycled by means of large-scale pyrolysis. In this process, the plastic contained is thermally decomposed so that the fibers can be recovered and processed into new nonwovens or even reused ground in injection molding. The researchers in the KoReNaRo project now want to optimize and further develop the existing recycling concepts for the decommissioned end-of-life wind turbines. The aim is to achieve the highest possible recycling rate in terms of the circular economy and to develop and open up a market for newly recoverable secondary products.
Demonstration plant planned in Bremerhaven
There are also plans to design a demonstration plant for recycling rotor blades. Bremerhaven is targeted as the location. To this end, a concept for automated initial treatment is to be developed first, in which the rotor blade can be more effectively cut up and separated into its components. The researchers also aim to further utilize and recycle the main chords that give the rotor blade its stability. In addition, the recycling of the balsa wood as wood foam is now to be initiated on an industrial scale.
bb