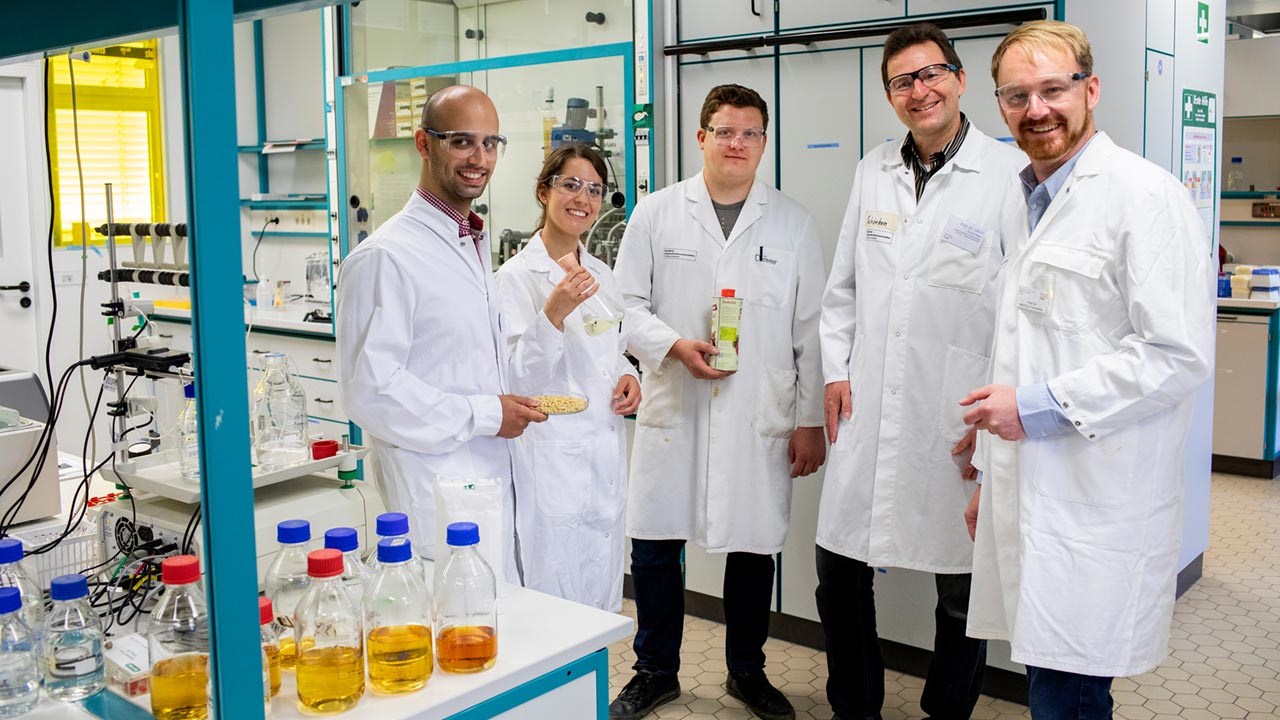
Can two manufacturing methods be combined into a single and at the same time more sustainable process? This was the question the Linopol project set out to answer four years ago. On the one hand, the team led by project manager Ulrich Schörken from the Technical University of Cologne aimed to replace the previously petroleum-based production of polyamide 12 with a biobased alternative. On the other hand, they were looking to avoid waste products in the production of fragrances and flavorings and turn them into recyclable materials. Last year, the team succeeded in proving the proof of concept.
Fragrance and plastic in one process
In fragrance production, linoleic acid is separated to yield hexanal. The smaller part, with six carbon atoms, is the fragrance. However, the larger part, based on twelve carbon atoms, is discarded. "We asked ourselves: Can we use the whole fatty acid?" Schörken explains, recalling the genesis of the project idea. The larger cleavage product could eventually be a starting compound for polymers such as the plastic polyamide, which is used to make nylon, for example. The idea also convinced the German Federal Ministry of Education and Research, which funded the project with 538,000 euros from March 2019 to July 2022 as part of the "Biorefineries Technology Initiative" funding program under the "National Research Strategy Bioeconomy 2030."
The team relied on thistles as a source of linoleic acid. As native plants that also grow on poor soils, thistles are an attractive species for new bioeconomy uses. The researchers pursued two approaches in parallel: synthesis using enzymes and chemocatalysis.
Suitable enzymes needed for the biotechnological process
For the biotechnological route, the project participants first had to identify suitable enzymes. In the first step, a lipoxygenase was to peroxidize linoleic acid. It turned out that commercially available lipoxygenase from soy works better than the recombinant, i.e. biotechnologically self-generated enzymes. In the second step, a hydroperoxide lyase would convert the intermediate to oxocarboxylic acid. Hydroperoxide lyases are so sensitive that they are not commercially available and thus the researchers had to produce them themselves. The most promising results were obtained with a new hydroperoxide lyase from papaya, produced recombinantly in E. coli. Finally, a transaminase produces the aminocarboxylic acid - the polyamide building block. Several omega transaminases are described in the literature that can convert long-chain hydrophobic substrates. The research team found as many as seven different enzymes, which they tried out successfully.
Hydroperoxide lyase in particular proved to be a bottleneck. "The enzyme is difficult to produce, very sensitive and both substrate- and product-inhibited," Schörken reports. In addition, the oxo acids produced are very reactive. "The substances therefore disappear quickly, and we initially had difficulties identifying our products," recalls the project manager. The third challenge was that the end product of the enzyme cascade, 12-amino oxododecenoic acid, is both zwitterionic and hydrophobic and cannot be easily extracted both in water solution and in organic solvents.
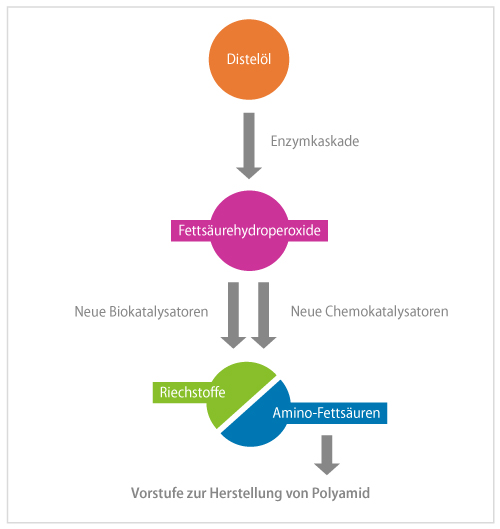
Konti process posed too many difficulties as a four-phase system
To solve some of these challenges, the team had temporarily tried to use a continuous process in which the enzymes are immobilized in a reactor column instead of a batch process. "But then, we had an aqueous phase, a lipid phase, a gas phase and the solid phase with the enzymes," Schörken says. "A four-phase system like that needs a lot of optimization." In addition, oxygen saturation caused problems. In the end, therefore, they stuck with the original approach.
Nevertheless, the project was very successful: "After just over two years, we were able to demonstrate for the first time that the complete cascade works and that we can thus achieve a bifunctional building block for polyamide 12 synthesis," says the project manager with satisfaction. At the outset of the project, it was by no means certain that this proof of concept would actually be achieved within the next three years.
Successful chemical approach with new catalysts
The chemical approach was also unexpectedly successful. The team first tested it in the closely related synthesis of phenol. Up to now, the industry has relied primarily on Lewis acids as catalysts. However, the researchers at TH Köln were able to show that heterogeneous catalysts are also suitable - so suitable that this process was patented. The same catalysts could eventually be used to separate hydroperoxides along the way to polyamide. Of course, further optimization is still required for industrial application.
Nevertheless, Schörken is far from dissatisfied, after all, all of the project's goals were achieved. With the phenol synthesis, an unexpected by-product emerged. The transaminases used in the project are also so efficient that the researcher would like to continue working with them in other projects. Last but not least, three project members were able to earn doctorates and publish seven scientific papers. The project leader concludes: "Scientifically, the project was a great success."
Autor: Björn Lohmann