New bioglues from vegetable oil
Fraunhofer researchers are developing new biobased adhesives that consist almost entirely of vegetable oils - including resins and hardeners.
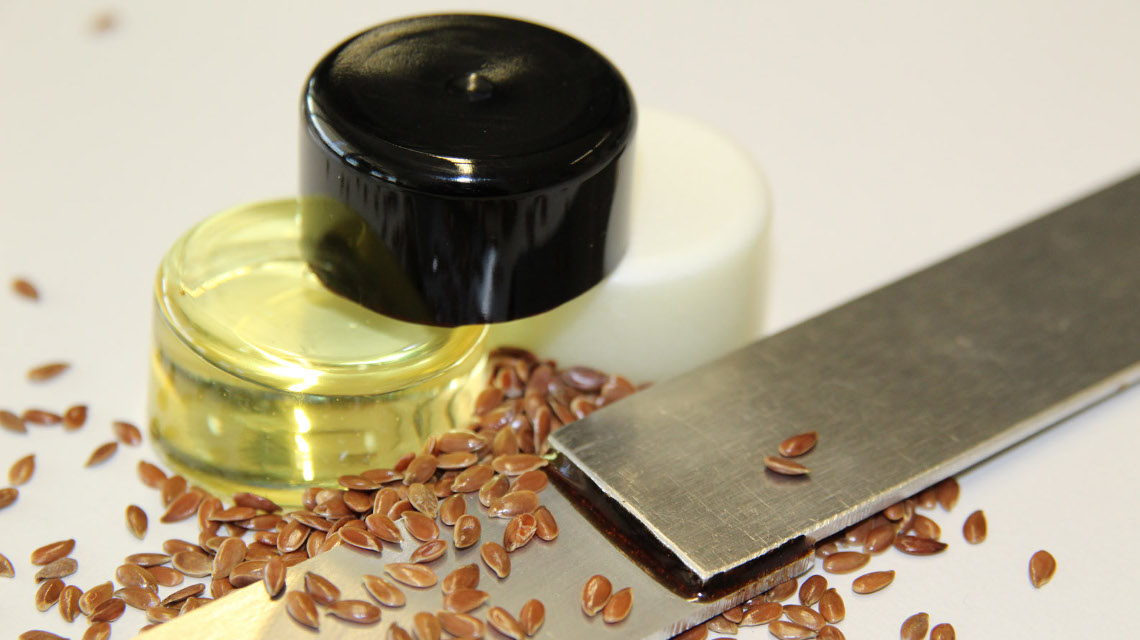
Children's toys, food boxes or shopping bags: many products already consist of bio-based feedstocks and are therefore considered sustainable. In order to be classified as sustainable, however, the organic content of the material must account for at least 35%. Fraunhofer researchers have been working for years to increase the biogenic content of materials such as plastics. At the Fraunhofer Institute for Microstructures of Materials and Systems IMWS in Halle (Saale), scientists are therefore focusing on the development of bioglues, including the associated resins and hardeners.
Using resins from vegetable oils to produce highly resilient plastics
Until now, adhesives have mostly consisted of petroleum-based thermosetting resins, also known as epoxy resins. Once heated, these can no longer be deformed. Combined with a hardener, the resins can be functionalized, i.e. they can be easier to process, dyed or fireproofed. A bio-based alternative could be resins from vegetable oils such as scorpion fish oil. In combination with appropriate hardeners, they can also be used to produce highly resilient plastics.
Antibacterial effect with thyme oil
The IMWS researchers still have a few hurdles to overcome before the bio-adhesives from the Fraunhofer laboratory are launched on the market: Since the resin is extracted from the seeds of oil plants, the chemical composition can vary, which is common for natural raw materials. The researchers therefore first have to find out how the varying ingredients affect the resins. "We are investigating these resins from the micro to the macro level," explains Andreas Krombholz, group leader at IMWS. In addition, research is being carried out into which fillers and functional materials have which benefits, for example whether they have a high electrical conductivity or even an antibacterial effect. The latter effect can be achieved by adding modified thyme oil, for example.
Conversion from epoxidation to enzyme treatment
The IMWS team also uses vegetable oil epoxides for adhesive development. Since not only the material itself but also the hardener has been replaced by more ecological substances, the bio-based proportion of the new organic glue is now 86 percent. Krombholz reports that the Fraunhofer researchers are also taking a more sustainable approach to epoxidation. "Together with the Fraunhofer Institute for Interfacial Engineering and Biotechnology IGB, we switched from epoxidation to a novel enzyme-based process. This means we can process vegetable oils without using petrochemicals. The treatment with enzymes takes place at 40 degrees Celsius rather than 100 degrees Celsius as in the past, so we are also conserving energy." The researchers were also able to significantly improve delivery routes and thus the environmental balance by using indigenous vegetable oils for the production of organic adhesives.
bb/um