Innovative bioplastic film made from PLA
Fraunhofer researchers have developed a flexible film material from the bioplastic PLA that does not require plasticisers and is recyclable.
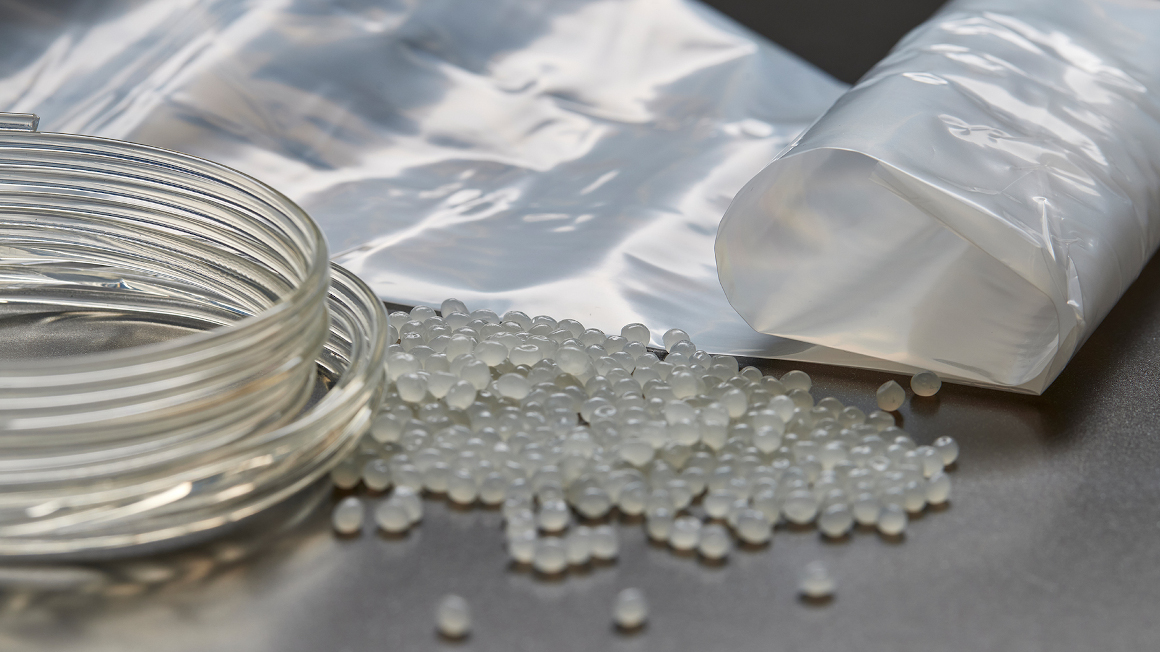
Polylactic acid – PLA for short – is a bioplastic that is particularly valued for its high rigidity. The range of applications for the bio-based and biodegradable polymers extends from children's toys to dowels and disposable cups to food packaging. Fraunhofer researchers have now expanded the range of applications for PLA with the development of a new type of film material.
Until now, the biopolymer was not suitable for flexible disposable packaging such as plastic bags or bin liners. These bags still consist of fossil raw materials and additives such as plasticisers, which ensure a long shelf life and flexibility, but make recycling more difficult. "For an increasingly circular economy, these must be offset by non-fossil raw materials," explains Antje Lieske, head of the Polymer Synthesis department at the Fraunhofer IAP in the Potsdam Science Park. "However, this is not easy, as there are usually no bio-based analogues for fossil plastics with the same material properties."
Plasticiser anchored in polymer chain
Antje Lieske and her research team have now solved this problem. They have developed a new, flexible PLA material that does not require the use of migrating plasticisers and is at least 80% bio-based. The problem is that the plasticiser molecules that are added to the PLA material will leak out of the material over time, making it stiff and hard again. The researchers have therefore "inserted the plasticisers, known as polyethers, directly into the polymer chain to make the material permanently more flexible". "To prevent this migration, we anchored the polyether directly in the polymer. To do this, we synthesised PLA-based block copolymers in which the polyether chain segment is covalently linked to PLA chain segments at both ends," explains Benjamín Rodríguez.
Innovative PLA can be used on standard systems
According to the researchers, these polyethers are non-toxic, commercially available and can also be produced biobased. "In addition, our material can be produced cost-effectively from commercial raw materials in a simple synthesis process. This does not require large-volume synthesis plants, but can also be implemented locally by medium-sized companies as a continuously operated process," explains André Gomoll. This means that the new material can also be processed into films on conventional processing plants in a similar way to petroleum-based low-density polyethylene (LDPE) and chemically recycled with considerably less energy input than LDPE.
Production of innovative bioplastic started
A first plant for the production of the novel bioplastic called Plactid was commissioned last year by SoBiCo GmbH, a subsidiary of the Polymer Group, in Pferdsfeld in Rhineland-Palatinate. Initially, 2,000 tonnes of the new bioplastics were produced here. In the long term, up to 10,000 tonnes are to be processed there annually.
bb