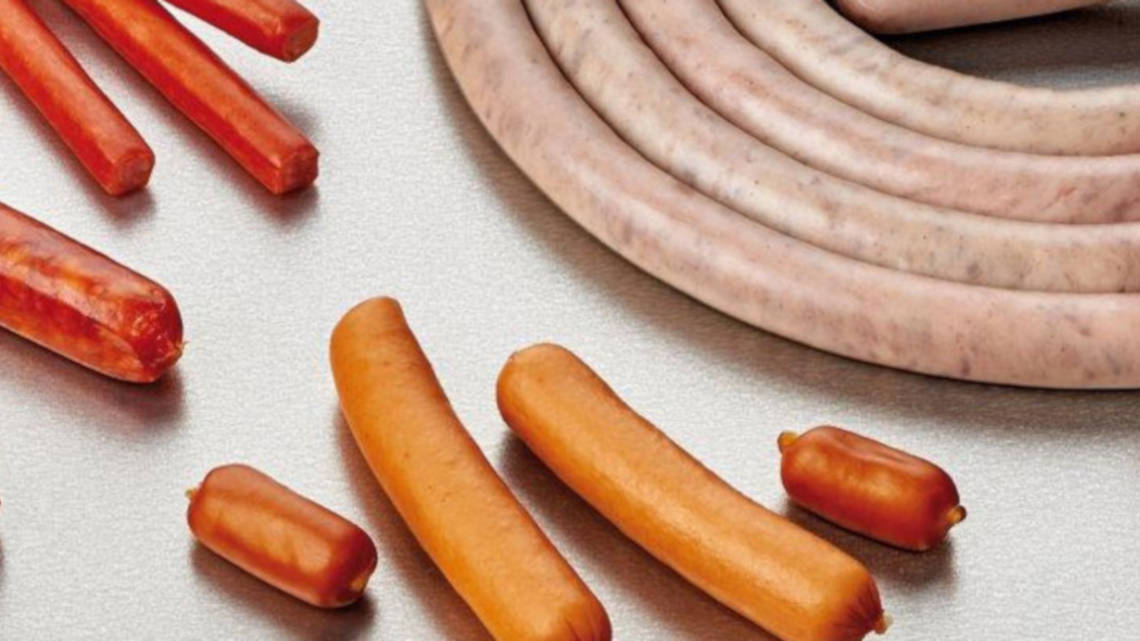
The standard process for producing collagen films has been established for 125 years. Now, a consortium of four partners has been looking for ways to to this a more sustainable and homogeneous way in the project "BioPro: Biotechnological process development for novel collagen-based membranes". The Weinheim-based company NATURIN Viscofan GmbH tested the practical suitability of one of its products: a nature-identical casing for sausages.
Enzymes instead of chemical process steps
"We wanted to optimize the manufacturing process by replacing chemical steps with enzymes in the process sequence," explains Hans-Jörg Menger, who is responsible for Innovation and Diversification at Naturin. The chemical conversion of collagen was to be supported by enzymes. The aim is to extrude collagen from its natural structure into a membrane that can be used by the food industry.
First, suitable enzymes had to be identified. So-called proteases were considered - but not all of them. In order not to impair the tensile strength of the membrane, the enzymes were required not to shorten the fibres. Project partner N-Zyme BioTec GmbH from Darmstadt identified five potentially suitable enzymes that Naturin tested during the course of the project. These enzymes were to "fibrillate" the coarse macrocollagen fibrils and thus expose the fine microcollagen fibrils. As with a carpet, these fibrils were then rewoven to form a membrane with a defined thickness and different permeabilities for water-attracting or water-repellent substances. In addition, the process should drastically reduce the amount of collagen raw material required, as well as the need for water, energy and chemicals. ASA Spezialenzyme GmbH pursued an alternative path within the project. The company was to synthesise the collagen films in the desired thickness from collagen nanofibrils using new enzymes.
Adapting process conditions to enzymes
Until then, Naturin had to adapt the process steps in which enzymes were to be used to their range of action - defined primarily by temperature, pressure and pH value. In order to create the best possible conditions, the researchers had already taken the technically possible framework conditions of the processes into account when selecting the enzymes. "It is not always possible to completely adapt the steps," said Menger. Nevertheless, Menger's team was able to optimize the parameters both on a laboratory and semi-technical scale to such an extent that an economic process using enzymes would ultimately be possible.
In order to evaluate the results of enzyme activities and select the most suitable enzyme, Naturin and the Institute of Biological Process Engineering at the Mannheim University of Applied Sciences have developed a fibre measurement method. Using this special microscopic method, the project partners analyzed the length, thickness and structure of the fibres as they existed after the use of the enzymes. Not all parameters met the requirements, but one enzyme proved to be suitable. "Our theoretical expectations have all been confirmed in practice," said Menger.
This is how the enzymatically produced collagen fibres look under the microscope.
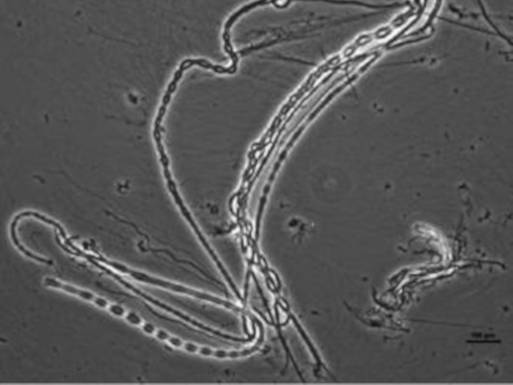
All goals met within the set time frame
The joint project "BioIndustry2021: BioPro Collagen Membrane" was funded by the German Federal Ministry of Education and Research with approximately 972,000 euros from February 2013 to March 2016. Of this amount, approximately 162,000 euros were invested in Naturin's subproject. Approximately 810,000 euros went to the project partners ASA Spezialenzyme GmbH, N-Zyme BioTec GmbH and the Institute of Biological Process Engineering at Mannheim University of Applied Sciences. Project leader Peter Kunz and scientific director of the Bio-Logik-Control consulting office in Mannheim sums up the project: "We can be proud of the fact that, cooperatively, we have achieved all the project goals within the given timeframe."
However, a whole series of optimizations were necessary before the process with one of the five enzymes tested actually produced a collagen membrane that is superior to the existing nature-identical membranes. In this way, Naturin produced prototypes of particularly low thickness that were nevertheless mechanically and thermally more stable than the previous sausage casings. So far, nature-identical membranes have been many times thicker than natural casings. The new approach also made it possible to save raw materials and chemicals.
Large-scale production possible in the future
However, Naturin has not yet transferred the enzymatic process to large-scale production. "We would have had to completely retrofit certain process steps in the existing production plant in order for the enzymes to function optimally. That would not have been economical," said Menger. However, should the production plant one day be redesigned, Naturin intends to integrate the process steps in which enzymes have achieved the greatest effects in the research project into the plant.
Author: B. Lohmann