Paper and cardboard made of grass
Uwe D'AgnoneProfession:
Industrial clerk
Position:
Managing partner at Creapaper GmbH
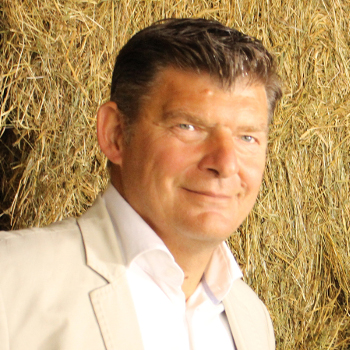
Profession:
Industrial clerk
Position:
Managing partner at Creapaper GmbH
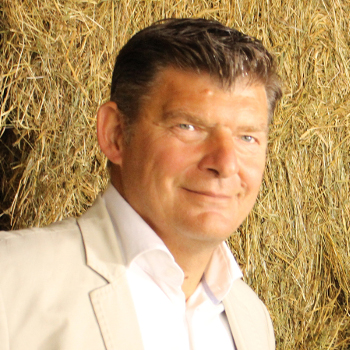
Uwe D'Agnone is committed to a sustainable and resource-efficient industry and is breaking new ground with his grass-based paper and packaging.
Short-sleeved, full of innovative ideas and absolutely convinced of the benefits and necessity of a sustainable and bio-based industry – that is what Uwe D'Agnone in a nutshell. The 53-year-old inventor and CEO of Creapaper is committed to the sustainable, resource-efficient use of raw materials in the paper industry.
For the trained businessman with his office in Hennef near Bonn, a sustainable industry is not only the latest trend, but rather an attitude towards life in general: "My wife and I are enthusiastic hobby divers. Unfortunately, by doing so we are witness to the pollution of the oceans and the destruction of coral reefs," says D'Agnone.
He first came into contact with environment-conscious processes at an early age: "The topic of sustainability has interested and accompanied me already during my training days in a printing company." Shortly after completing his training, he started his own printing consultancy to develop and implement his own ideas on sustainability in the printing and paper industry.
Alternative raw material for paper
About six years ago, he decided to develop and establish an alternative raw material for paper production and founded CREAPAPER. "The most difficult step in conventional papermaking is to separate the wood fibers from the lignin. This requires a great deal of chemistry, energy, and water." The higher a plant grows, the more lignin it contains. So he looked around for low growing material: "We use dried grass, hay, so we can produce year-round," explains D'Agnone.
A ton of wood pulp requires about 6,000 liters of water and 5,000 kilowatt hours of energy, but for the same amount of grass pulp, you only need about two liters of water and 137 kilowatt hours. "To get paper out of grass, a purely mechanical process is sufficient - the air-dried fibers are cleaned, cut to fiber length, ground, and pelletized," says D'Agnone.
This process saves enormous amounts of CO2 emissions in the production of grass paper compared to conventional paper or waste paper. And even the price of grass fiber is more than 40% cheaper. Depending on the product, D'Agnone now uses up to 51% grass pellets for production. And although it would be possible to produce white-painted grass paper, most customers prefer the light brown-green color, so the sustainable origin of their product remains recognizable.
Multi-award winning idea
In fact, neither the product nor its origin need to be hidden: After all, the grass carton was nominated for the German Packaging Award in 2015 because of its sustainability aspect. And in 2016, Creapaper won the StartGreen Award in the Start-up category for the development of the grass-based substitute pulp for papermaking. In 2018, the sustainable packaging approach also received the KfW Award. In addition, the Federal Ministry for the Environment, Nature Conservation and Nuclear Safety (BMU) awarded Creapaper GmbH the German Innovation Award for Climate and Environment (IKU).
The use of graphic papers in offices has decreased significantly, but the demand for packaging material has increased enormously. Therefore D'Agnone and Creapaper are focusing more and more on packaging boards.
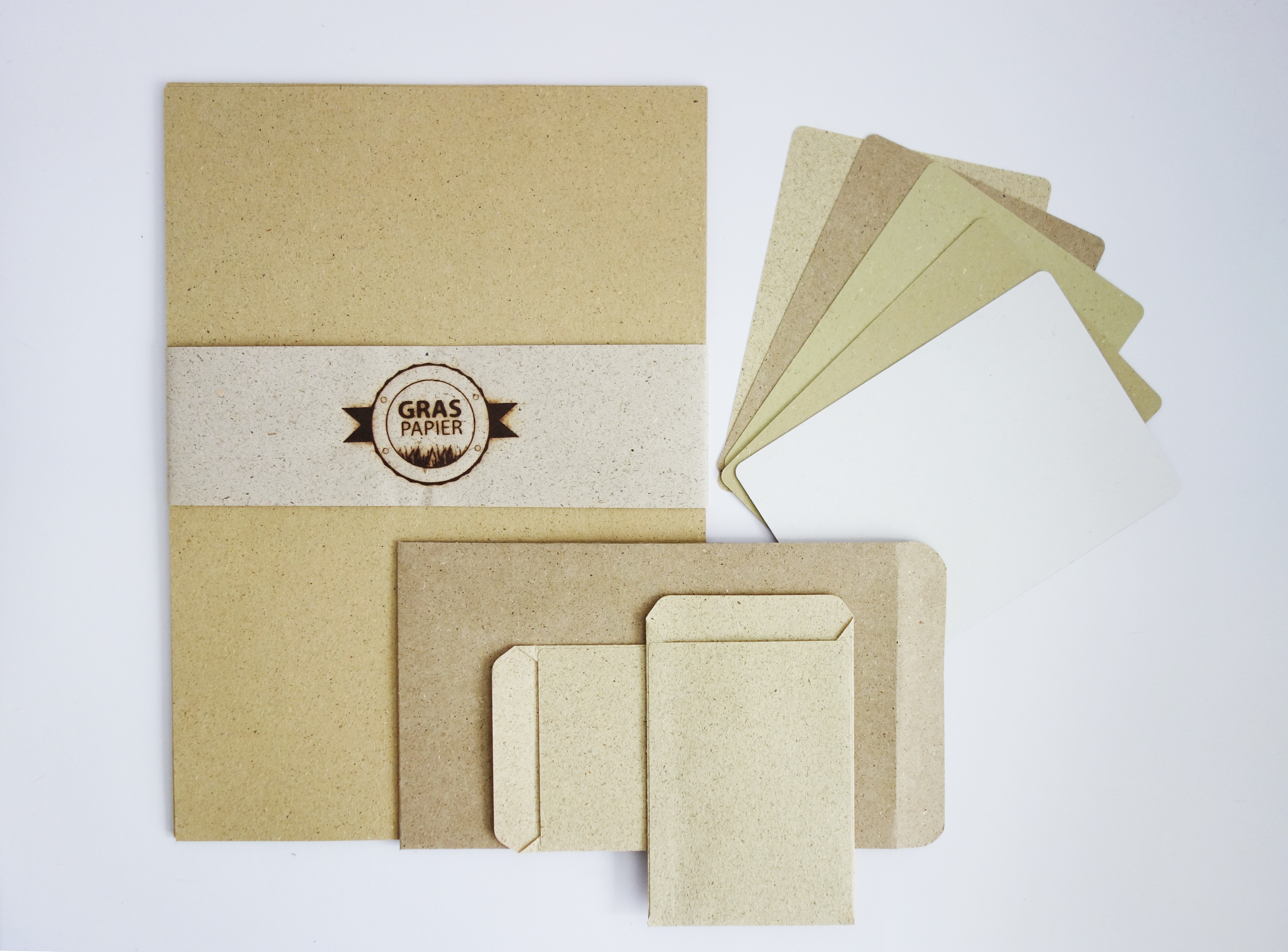
Paper industry initially skeptical
Before those accolades, some difficulties had to be overcome: Despite the eco-friendly and positive energy and price balance for grass paper and the early successes with hand-made grass paper sheets, the paper industry was extremely skeptical about the new material: "The biggest hurdle was the paper industry itself, because there is simply no room for pilot projects with new raw materials" sums up D'Agnone. Only with an interested large customer at hand - the OTTO dispatch - he and his raw material received a production window in a paper mill. In addition, the material had to be tested for possible allergens and tested for a number of other certifications, such as for life cycle assessment or direct food contact, before it could be introduced to the market.
Packaging for online shopping and organic fruits
Although the use of graphic paper in offices has dropped significantly over the last years, the demand for cardboard and packaging material has increased enormously due to the booming online shopping. Accordingly, D'Agnone and his now 16 employees at Creapaper focus more and more on packaging boards. However, his team produces the sustainable packaging material not only for online trade, packaging trays for organic fruit have also been developed for two large supermarket chains. "We are starting to see new ways of thinking and doing the industry. And we are now officially a member of the paper association,” D'Agnone says proudly.
Regional production
In fact, the grass pellets are now suitable for the production of 90% of all currently produced paper products. But D'Agnone doesn’t just want to reduce CO2 emissions in the paper industry by merely replacing wood fibers. He is also committed to local and regional production. His grass pellet production facilities can be supplied with locally mown grass and should in each case be located as close as possible to paper mills. Thereby, delivery routes and chains can be kept as short as possible. So far, 14 paper mills across Germany already work with grass fibers and have produced different types of paper.
And even outside Germany, the new raw material is catching on: D'Agnone has already inspired a Dutch and an Italian paper mill. But despite the awards and the positive international feedback on his product, the ecological value remains his top priority: "If only a fraction of the international paper industry switched to the new raw material, we would see a significant positive effect on the global climate."
Next step: Cascade usage
D'Agnone's next goal is to further increase the sustainability of his product: He wants to remove the proteins from the hay before they are processed into pellets. He hopes for a cascade use of the raw material via an upstream work step. "Our paper needs the fibers, not the proteins. They are basically wasted in the paper. Therefore, we want to isolate them beforehand and put them into the industry, where they could be processed, for example, for pet food," says D'Agnone.
He estimates the chances of success quite optimistic, so far he has received a lot of positive feedback from the industry. "The bio-economy and above all the sustainable use of our raw materials is one of the key issues of our time. No one is exempt from it and we urgently need to do something!”
Author: Judith Reichel