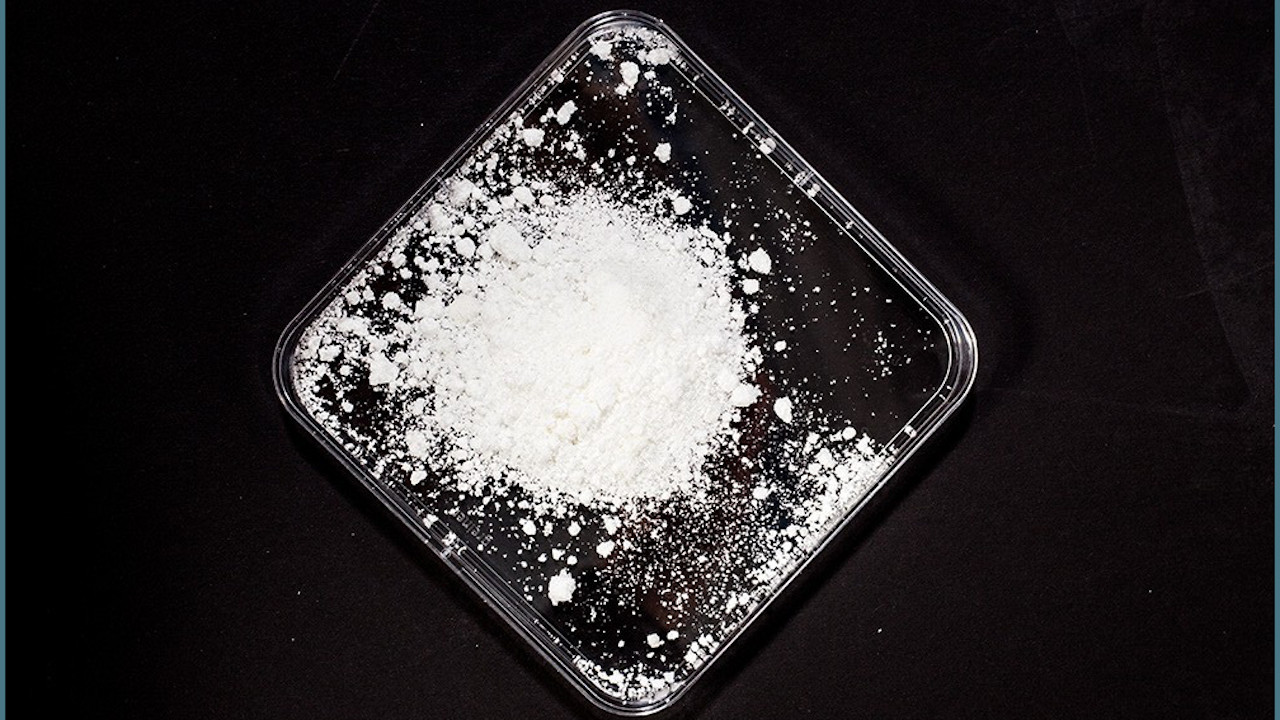
Plastics are versatile and durable, but it is precisely their long durability that is the problem: petroleum-based plastics do not decompose and pollute the environment. Bio-based alternatives made from renewable raw materials do exist. But they are not environmentally friendly per se unless they are also sustainably produced, recyclable or biodegradable. This is the approach taken by the PHABIO APP project. Under the direction of the Fraunhofer Institute for Production Systems and Design Technology (IPK) in Berlin, researchers from Germany, Malaysia and the USA have spent the past few years developing a biotechnological process that can be used to produce a plastic from animal waste that is completely biodegradable in nature - in just a few months.
The project received a total of 1.28 million euros in funding from the German Federal Ministry of Education and Research from 2015 to 2018 as part of the "Bioeconomy International" funding measure. "The big goal was to explore all aspects of the process chain from waste material to the finished plastic component. In the end, we wanted to provide a closed process chain for the production of plastic components." explains project coordinator Christoph Hein from Fraunhofer IPK.
Animal waste fats as a source of nutrients for bacteria
Using the bacterium Cupriavidus necator the bioplastic polyhydroxybutyrate (PHB) is produced. Waste fats from slaughterhouses, for which there was previously no industrial use, serve as a nutrient source for the bacterial plastic producers. However, in order to turn Cupriavidus necator into effective plastic factories, Hein's IPK team had to overcome a number of hurdles. "One challenge was modifying the bacterial strain. The wild type can also synthesize waste materials into plastic, but you only get very little plastic out of that, and it's also very brittle," Hein explains. Researchers at the TU Berlin were responsible for cultivating the bacteria and producing the plastic. To do this, they fed the bacteria in huge fermenters with the liquid waste fats.
Another challenge was to dissolve the plastic out of the bacteria's cells. "That's where we collaborated a lot with the international partners. For example, we tried to use biological extraction processes to have rats separate the bacteria, which metabolize the bacterial plastic and then excrete it again. However, the odor of the plastic was too strong." Similar experiments with mealworms failed because of scalability, according to Hein. "In the end, we ended up using a chemical process where we can recycle all the solvents and then get a high-quality plastic."
The quality of the waste fats - especially their carbon content - is also crucial for the production of the new biopolymers. To investigate this, the researchers analyzed the fat quality throughout the meat processing chain. The result: "In principle, we can process everything that comes out of the slaughterhouses. It's not limited to a specific animal, either." According to Hein, not only waste fats from beef, pork and poultry are suitable as bacterial feed, but also fish waste.
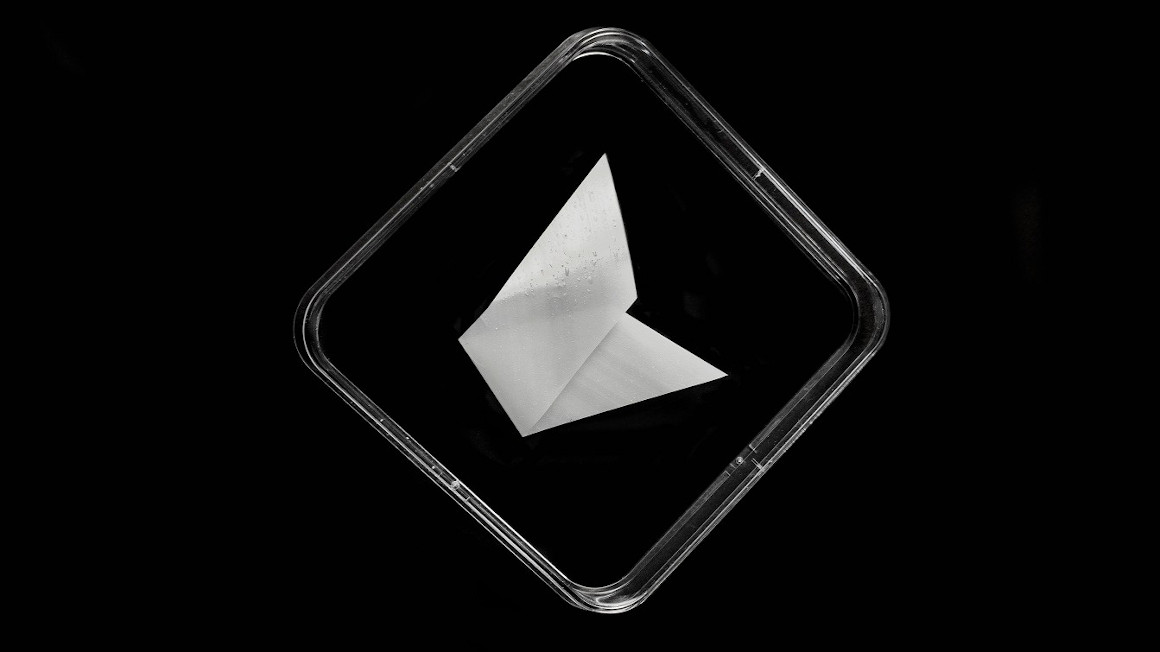
New PHB suitable for injection molding
In addition to the environmentally friendly production of the bioplastic, further processing using established methods was also a major concern of the project partners. The injection molding process was therefore used to test whether the new PHB plastic was suitable for product manufacture. Here, too, the team had to make adjustments, because the crystallization of the plastic originally took far too long. Until the biopolymer had cured and could be further processed, the injection molding cycle had to be paused.
Yet this problem was also solved: "We developed special additives for the raw plastic so that it crystallizes faster and can be processed further," says Hein. Although these were chemical additives, their proportion in the PHB plastic is very low at a maximum of 0.07%, and they are also completely degradable.
Other parameters such as processing temperature and speed also had to be optimized in order to be able to further process the plastic in injection molding. As a result of the project, first test samples and a foldable cube have already been produced as prototypes.
Completely degradable in nature
As far as the properties of the new biopolymer are concerned, Hein says it is comparable to the well-known plastic polypropylene (PP) and is therefore particularly suitable for short-lived products such as disposable tableware or the currently omnipresent Corona rapid tests. Unlike many bioplastics, the new PHB can actually biodegrade in nature. "Regardless of the environment, in compost or in the ocean, the plastic degrades very rapidly. Depending on how the plastic was processed, it is completely degraded in nature in 6 to 18 months," Hein sums up.
PHABIO APP
Project partners:
Fraunhofer IPK: Project coordination, optimization of the bacterial strain, compounding and processing of the plastic material
TU Berlin: Cultivation and production of the plastic
Animox Gmbh: Purification of the plastic
International partners:
University of Science Malaysia: biological purification of the plastic
University of Massachusetts Dartmouth/ Boston: adaptation and optimization of the bacterium
In the follow-up project PHABIO UP, Hein's team aims to make the production of the novel bioplastic fit for large-scale industrial production by 2022. "Until now, the quantities of material we could produce were very limited. And the processes of plastic production were still too slow from a biological point of view. That's why we now want to scale up all the sub-aspects in the project so that industrial applications are possible." The follow-up project is also funded by the "Bioeconomy International" funding measure.
Author: Beatrix Boldt