Coral antibiotic from the cell factory
Biotechnologists at the TU Munich have succeeded in producing an antibiotic agent from horn corals using bacteria.
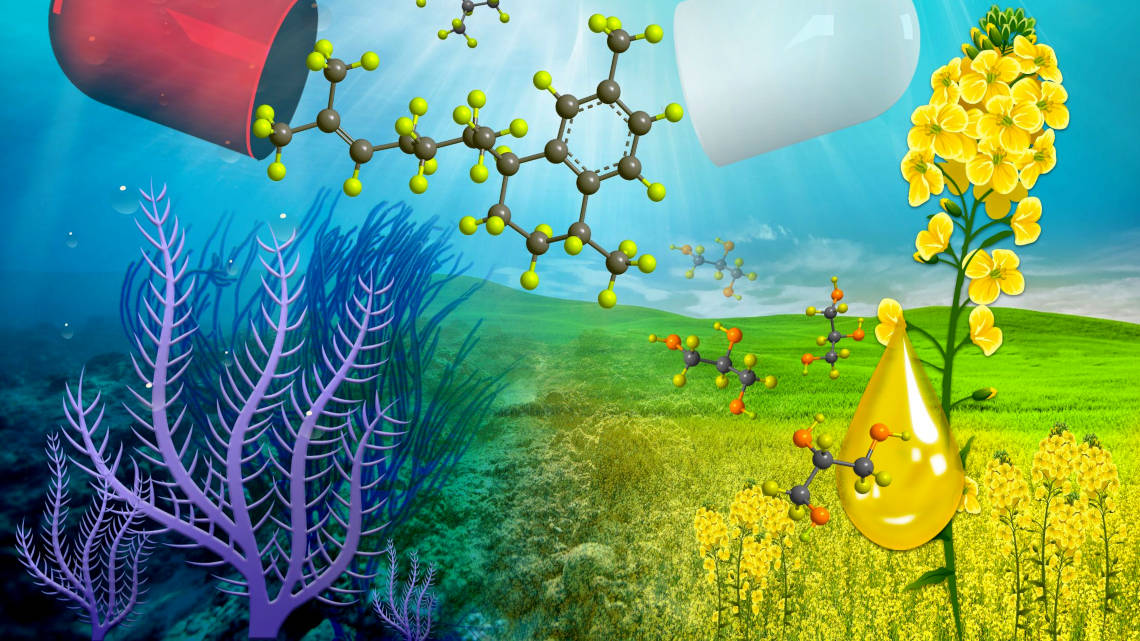
Nature's biodiversity harbors an almost immeasurable treasure of biologically active substances that can be of benefit to humans. A well-known example is the antibiotic penicillin, which is extracted from the mold Penicillium chrysogenum. Less known is the antibiotic Erogorgiaene. It is produced in small quantities by the horn coral Antillogorgia elisabethae. A team from the TU Munich has now succeeded with international partners in producing this active ingredient in bacteria.
Discovered during the dive
For the TU-researcher Thomas Brück the horn coral is no unknown. Already 17 years ago, the reef inhabitant fascinated him during a dive in the Bahamas. Since then the scientist has been interested in Antillogorgia elisabethae and the numerous biologically active substances it produces.
However, it is not possible to simply harvest the corals to extract their active ingredients. Because although the corals are under protection, their existence is already endangered. The anti-inflammatory molecule pseudopterosin produced by them is sought after in the cosmetics industry and the sale of the horn coral is correspondingly lucrative. "Coral reefs store the climate gas carbon dioxide and create a very high biodiversity," warns Brück. "If we want to protect the world's reefs, we have to produce such biologically active natural substances, which have medically useful activities, in a sustainable way".
Environmentally friendly and cheaper
In principle, this would be possible by a chemical-synthetic route, but then one kilogram of the antibiotic Erogorgiaene, which is effective against multi-resistant tuberculosis pathogens, would cost 21,000 euros. On top of this would be the toxic waste produced in the process. The scientists have therefore transferred the metabolic pathway by which a precursor of the antibiotic is formed in the corals to E. coli bacteria. These even use glycerine as a substrate and thus a residue from biodiesel production. With the help of further enzymes, the finished antibiotic is then produced in a second step in the preliminary stage - without any waste and at low cost: "The production costs per kilo would only be around 9,000 euros with this process," emphasizes Brück. The researchers report details in the journal "Green Chemistry".
Further molecules in sight
A patent application has been filed for the process, and the researchers have already set their sights on the next task: They want to further convert the molecule Erogorgiaene into the anti-inflammatory active substance pseudopteropsin.
The previous research project was funded by the German Federal Ministry of Education and Research (BMBF) in the project "Optimized microbial conversion of biomass residues for sustainable production of high value diterpene bio-actives" (OMCBP) as well as by the Werner-Siemens-Stiftung.