Upcycling startup receives Innovation Award
The Hamburg-based startup Bio-lutions uses fibres from agricultural plant waste to manufacture packaging materials. They won the award at a conference on bio-based materials in Cologne.
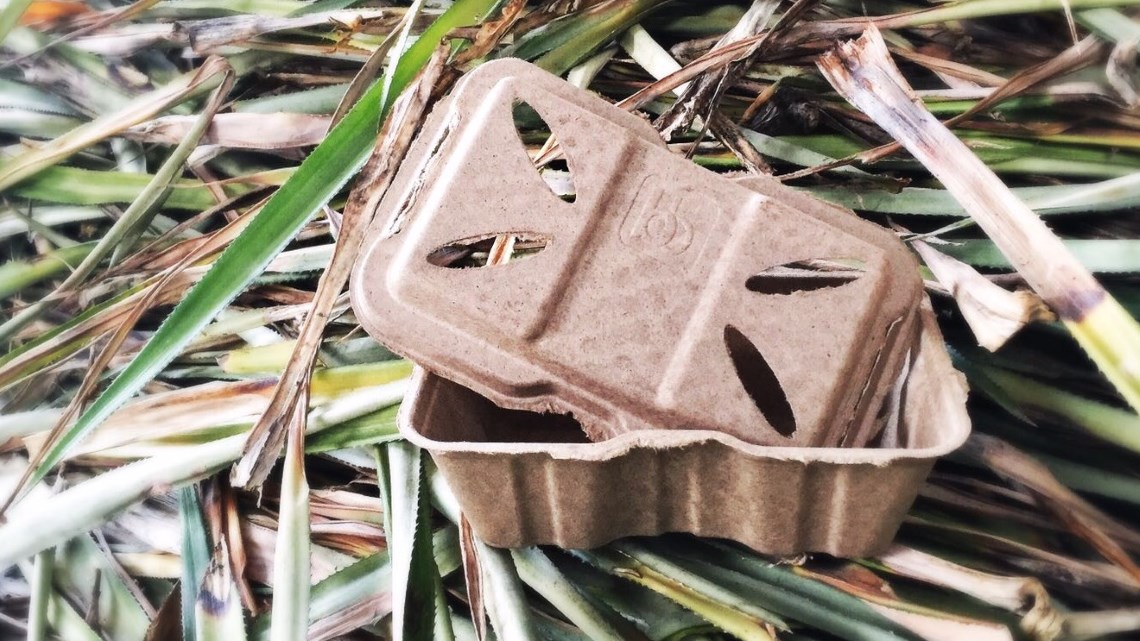
The “International Conference on Bio-based Materials” is a well-established meeting point for companies working in the field of bio-based chemicals and materials. For the tenth year in a row the conference was held this year on May 10 and 11 in Cologne. Almost 200 participants, particularly experts from the chemical and plastics industry met at the event organized by Nova institute.
The competition awarded current developments relating to bio-based economy that have had or will have a market launch in 2016 or 2017. The awardees of the prestigious – albeit without monetary value – Innovation Award "bio-based material of the year" are representative for a new generation of bio-based products with exceptional functionality and properties.
This year six companies were nominated by the conference’s advisory board and experts of Nova institute. Each nominee introduced its innovation in a short 10-minute presentation to the audience in Cologne. The participants of the conference were asked to vote for their favourites and the winners were announced at the traditional gala dinner.
Using banana trunks and tomato leaves
The clear winner was the Hamburg-based Bio-lutions GmbH, which were able to convince the audience with their technology. The startup uses agricultural plant residues as raw material to produce high performance ecologically sustainable packaging and disposable tableware. No matter the material – rice straw, banana trunks, or tomato leaves – the up-cycling procedure turns waste into innovative products.
“Together with our technology partner Zelfo we've developed a mechanical process that turns plant residues into nano and microfibres”, said founder and CEO of Bio-lutions, Eduardo Gordillo. After this procedure the fibres self-binding when adding water. This results in a fiber mash that can be molded into diverse forms – similar to the prodcedure that is currently used to manufacture egg cartons. In contrast to the cellulose-based industry this process requires far less water and energy and no chemicals. The final products can either decompose under normal conditions, be used for biogas production and can be recycled or burned with a nearly CO2 neutral carbon footprint.
Bio-lutions aims to conquer the world with their innovative technology and already started several international cooperations. Funded by the Bundesministerium für Wirtschaftliche Zusammenarbeit und Entwicklung (BMZ) Bio-lutions recently built a production facility in Bangalore, India. Here, they work with small farmers and have already established a smalll ocal team of four. “Since we use local raw material and produce locally, our procedure is both ecologicaly- as well as economicaly-sound”, says Gordillo. Due to the recent plastic ban across a number of federal Indian states, the entrepreneur is hoping for an ever-more increasing demand of sustainable packaging materials.
Second to Bio-lutions at the Innovation Awards was the Finish start up Paptic Ltd. They employ novel wood fibres for a bioplastic composite paper combining the benefits of paper, plastics and textiles. The first application that has already been introduced to the markets is carrier bags, which are addressing the EU directive target for 55% reduction of plastic bag use by 2019. Their innovative technology is based on a foam forming technology, which is using 30% less energy and recyclable.
Manufacturing raspberry flavours
The third place was awarded to a biotechnologically produced raspberry fragrance that was developed by Cologne-based Phytowelt GreenTechnologies GmbH. During her presentation Janin Wascinski was handing out candies that were manufactured using the natural raspberry fragrance.
Extracting the raspberry flavour not from fruits but synthesizing it artificially has been difficult to say the least. Because this procedures does not only generate (R)-alpha-Ionone but also the enantiomer (S)-alpha-Ionone. The (S)-form has a woody and musty flavour which gives the chemical racemate a different and impure fragrance. However, it is complex and uneconomic to separate the two molecules. “Our procedure enables us for the first time to produce only the desired (R)-alpha-Ione”, says Wascinski. The (R)-alpha-Ionone is of high intensity and purity. “Approximately 1 gram of our rasberry fragrance replaces 111 tonnes of raspberry and erases the need for up to 20 hectare of farm land”, sayd Wascinski in Cologne.
Car tires and wet suits made of caoutchouc
Even though they didin’t make it to the top three, the bio-based innovation of the other participants were very impressive as well. For instance, the US company Cooper Tire Ltd. presented a car tire made of natural rubber from guayule. This flowering shrub originates from Mexico and can be farmed on soil that could not be used for other types of farming. The California-based company Patagonia manufactures wet suits not from conventional neoprene but from natural rubber as well. Finally, the Belgian company Hexpol presented bio-based plastics that are extremely elastic and thus especially well-suited for handles, toys, or as slatted bed frames.
pg/jmr