New fiber composite made from biopolymers
A research collaboration has developed a sustainable alternative for the production of organosheets.
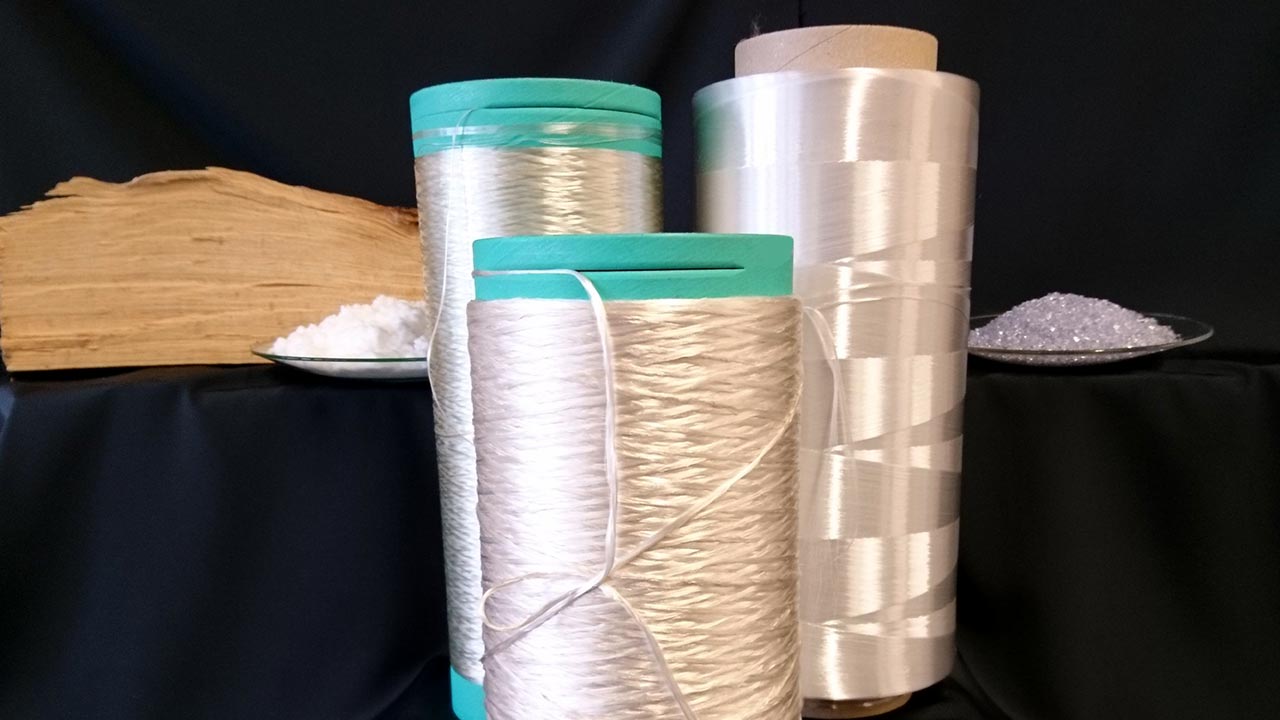
Fiber composites made from bio-based raw materials are increasingly in demand in industry. They are set to replace materials previously based on glass or carbon fibers or even basalt or aramid fibers. The intention is to produce more sustainable products, because the previous variants are very energy-intensive, both in production and in recycling. Yet sustainability is not to be achieved at the expense of processability or material properties. A research association around the German Institutes for Textile and Fiber Research (DITF) has now presented CELLUN, a corresponding fiber composite material.
Further processing using established methods
In lightweight construction, the industry prefers to use organosheets. These are semi-finished sheets made from thermoplastics and reinforcing fibers. They can be processed into molded parts using established processes such as hot pressing, thermoforming, injection molding or pultrusion. The components produced in this way have a uniform quality and are easy to recycle.
Organosheets can also be produced from CELLUN. The composite material consists of non-fusible cellulose fibers and thermoplastic derivatives of cellulose fibers reinforced with regenerated fibers and HighPerCell cellulose fibers developed by the DITF.
Towards industrial maturity
CELLUN is now to be further developed to industrial maturity and optimized for subsequent recycling. The German Federal Ministry of Economics and Technology is funding the joint project. The researchers want to find particularly suitable reinforcing fibers and integrate them into the matrix of cellulose and thermoplastic cellulose derivatives. Finally, several molded parts are to be produced from them in different processes for demonstration purposes.
Full recycling as a goal
Particularly important to the project team is closed-loop recycling: CELLUN should be fully recyclable. The team is pursuing two possible approaches: The molded parts could be thermally reshaped without any loss of quality. Or the material could be chemically separated into its individual components, which could then be used again as raw materials.
DITF hopes to develop a cost-effective, resource-saving as well as climate- and environment-friendly composite material for the lightweight construction and automotive sectors.
bl