Thread made of crab shell
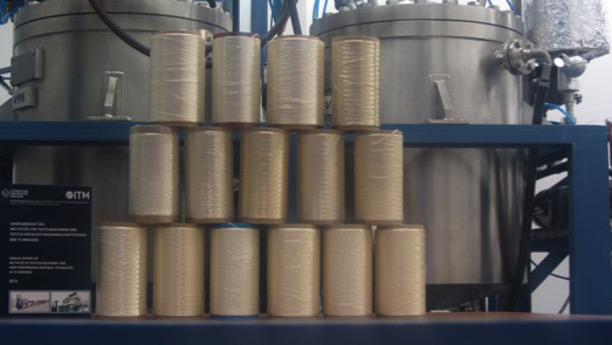
The Chitosan is mixed with an industrial polyester producing a hybrid fibre that combines the biologically qualities of Chitosan with the mechanical strength of the synthetic polymer. The new fibre is particularly suitable for medical applications such as implants or surgical yarns.
Sea creatures such as crabs or shrimps are not only tasty, but because of the high chitin content in their shells, they are extremely sought after. However, huge quantities of these shells still end up as waste in the bin. Because of its structure-building properties, in addition to cellulose, chitin belongs to the most widespread polysaccharides and is the starting material for the technical production of Chitosan. The biopolymer is again an important raw material for the production of fibres, foams or foils, and because of its biocompatible properties is especially well-suited for medical products.
Utilising waste products
“To find such a great use for a waste product, is a great thing,” enthuses Rolf-Dieter Hund, research group leader at the Institute of Textile Chemistry Textile Machinery and High Performance Materials (ITM) at the TU Dresden. In cooperation with the Halle-based company Heppe Medical Chitosam GmbH, which supplies the world’s pharmaceutical companies with Chitosan, the Dresden research group has now developed a thread that is made of 100 percent Chitosan.
A lot of yarn from a small amount of powder
Using the wet spinning process, the white powder, which was obtained in cleanroom conditions, was then processed into garn by Rolf-Dieter Hund in the laboratory. To do achieve this, the white powder was first dissolved, filtered, freed of air bubbles and then forced through a nozzle with 600 individual holes, each hole 90-microns in diameter. This is how the wafer thin fibres originated for medicine. Lastly, they are washed, dried and provided with a protective layer. The system can spin between 30 and 40 metres of thread per minute. According to Hund, around one and a half kilos of Chitosan powder are needed to produce 7,000 metres of yarn.
Chitosan is bio-compatible but expensive
According to the researchers, the natural spun material from the shells of crustaceans is biocompatible and non-allergenic, and is broken down in the body by the body’s normal enzymes. In light of the above, the range of applications is large. The organic yarn is suitable for wound dressings, surgical sutures or artificial skin or as bone implants, transporters for active ingredients, or as a nutrient medium for stem cell research. The bio-yarn is still considerably more expensive than conventional textile yarn, and until it has become standard for biomedical applications, further tests are necessary.