Durable bioplastics for the automotive industry
Researchers at the Institute for Bioplastics and Biocomposites (IfBB) at Hannover University of Applied Sciences want to develop bioplastics for the automotive industry that can withstand high temperatures and stresses.
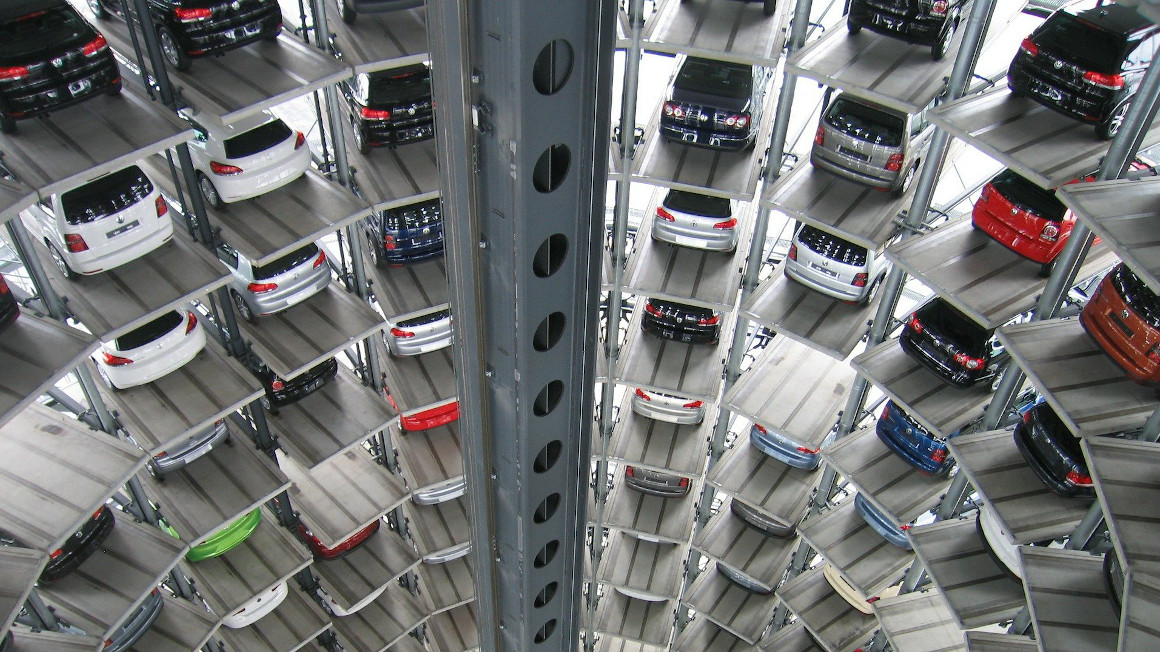
Bioplastics such as PLA (polylactide) are now used in many areas - from food packaging to dowels or children's toys. Nevertheless, their share is still low compared to conventional plastics based on fossil raw materials. The same applies to composites, which have to exhibit certain properties and therefore consist of different plastics. Here, too, there are now partially or completely bio-based materials. Researchers at the IfBB at Hannover University of Applied Sciences now want to prove that bioplastics can also withstand high temperatures and stresses.
Charge air tubes and filter modules made from bioplastics
In the "Bioplastics for high-temperature applications (HoT-BRo 2)" project, a team led by Andrea Siebert-Raths is working with industrial partners to develop and modify materials specifically for use in the automotive sector. The focus is on thermoplastics made from biobased or partially biobased and recycled polyamides. The new materials will be used to manufacture products for the engine compartment: a turbocharger charge air pipe, a commercial vehicle liquid filter module, a thermal management module and a cable gland as reference components.
Suitability for high-temperature applications proven
The aim of the project is to establish the bio-based formulations as high-performance plastics in various areas - not only in the automotive industry - and thus replace conventional plastics. The project is funded by the German Federal Ministry of Food and Agriculture. In the run-up to the project, a feasibility stage has already shown that bio-based composites are also suitable for demanding high-temperature applications with appropriate processing and refinement.
bb