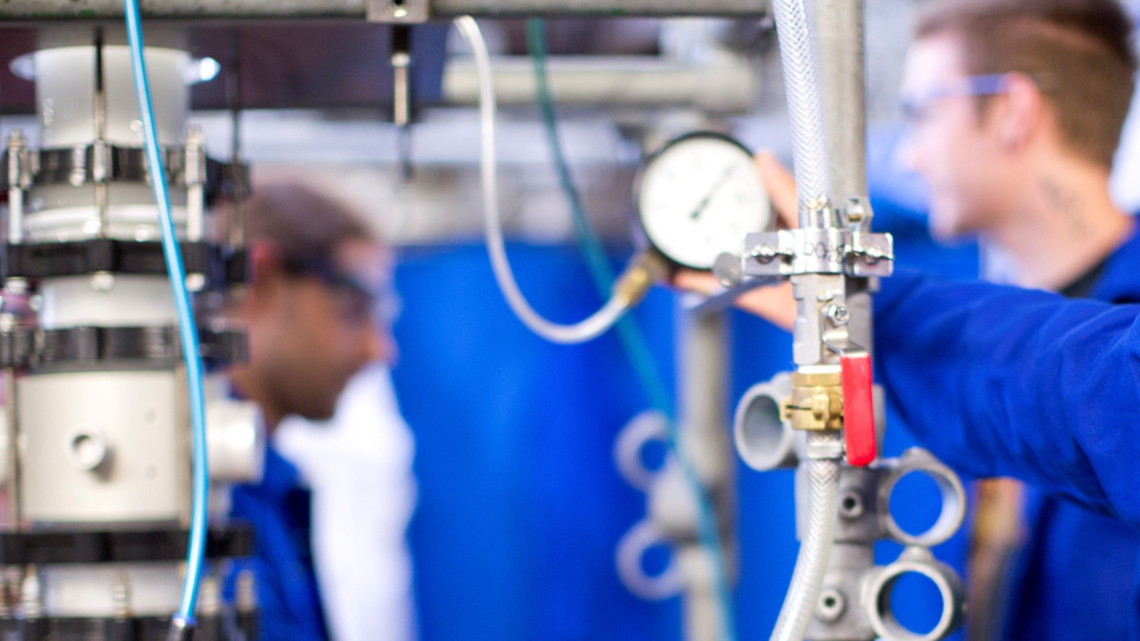
Methanol is one of the chemical industry’s most important source materials. It is colourless, flammable and smells of alcohol, and the starting point for manufacturing paints and varnishes as well as fuel. In 2015, the global demand for methanol was about 65 million tonnes. However, this compound of carbon monoxide, water and oxygen is produced mainly from finite resources such as mineral oil, natural gas or coal. To reduce the consumption of fossil raw materials for methanol production, researchers under the supervision of the Karlsruhe Institute for Technology (KIT) intend to develop a sustainable technique in the next few years.
Use of organic industrial by-products
The joint project is called 'OptiMeOH', which stands for 'Optimized process chain for resource-efficient Methanol synthesis'. Its aim is to render biomass usable as a sustainable source of carbon. The researchers also have another by-product of industrial manufacturing in mind: carbon dioxide. In the main, the organic residual materials to be used will come from industry and municipal waste disposal.
The research project's remit is to develop an innovative process chain for synthesizing methanol that either renders the use of fossil raw materials completely unnecessary, or that uses carbon dioxide from fossil sources in a variety of ways. "This significantly improves resource efficiency and the degree of exploitation of carbon," says Siegfried Bajohr, who heads the Catalytic Fuel Conversion research area at the KIT's Engler-Bunte Institute.
Fermenting biomass under high pressure
The theoretical and experimental investigations focus on the following areas, amongst other things: energy-saving biogas production by means of pressure fermentation (i.e. the fermentation of biomass at high pressures of 30 bar or more), a new reactor design for methanol synthesis and an innovative technique for treating industrial gases by means of chemical gas scrubbing with ionic fluids. "One of our main tasks is to investigate how much greenhouse gas can be saved by improving technological processes," says Nike Trudel, a chemical engineer from KIT.
Practical testing in an industrial park
The technique developed under the auspices of OptiMeOH is then to be compared with conventional processes and evaluated from economic and ecological perspectives. To this end, the technology is to be integrated for appraisal in two different industrial contexts – in a large industrial park and in a decentralized plant. "The process will be subjected to assessment that covers all aspects; its efficiency rating and its eco-balance will be compared with the methanol production methods that are based on coal, mineral oil and natural gas," explains Bajohr.
The joint project, scheduled to run until the end of 2019, involves the KIT researchers as well as a research team from the German Technical and Scientific Association for Gas and Water (Deutscher Verein des Gas- und Wasserfaches), the University of Stuttgart, the University of Kaiserslautern and three industrial partners including Höchst KG. The project is being funded by the German Ministry for Education and Research as part of the "CO2Plus – material use of CO2 to broaden the raw material base" funding programme with 1.4 million euros. The industrial partners are providing a further 300,000 euros.