3D printing with bioplastics
Thorsten PerlProfession:
Researcher
Position:
Co-founder and Technical Director of BioInspiration GbR in Eberswalde
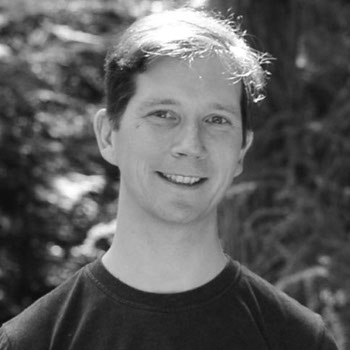
Profession:
Researcher
Position:
Co-founder and Technical Director of BioInspiration GbR in Eberswalde
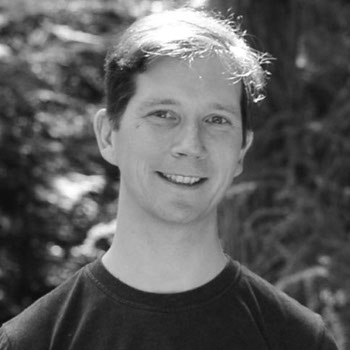
Thorsten Perl has the head behind the start-up Bioinspiration. Its focus is on 3D printing with bioplastics.
Simply dispose of cups, toys or shoes by throwing them onto the compost heap: That is what Thorsten Perl had in mind when developing his new 3D printer material. Together with his business partner Brian Cotty and their BioInspirations start-up based in the German city Eberswalde, the inventor of this sustainable printing filament is gaining enthusiasts for 'WillowFlex', and not just amongst 3D printer fans.
What contribution can your company make towards generating a bio-based economy?
We are predominantly introducing bio-based alternative materials and innovative recycling techniques with a view to their implementation in trade and industry. We want to simplify the decentralized production chain from field / fermenter to high-quality raw material in order to stabilize local economic cycles. To this end, and together with our colleagues, we combine bio-inspired materials with bionic design so as to be able to make future-oriented, easily recyclable products by means of organic manufacturing techniques (3D printing).
How did you come upon the idea of making compostable material for 3D printing?
What led us to this idea was the desolate situation regarding materials used for toys. As fathers with 3D printing experience, we asked ourselves whether there may not be more natural development potential in plastics. And we found a biodegradable elastomer in the USA. As there was no other bio-based, compostable 3D printer filament to be had, we mounted a kickstarter crowdfunding campaign to launch it on the young and very receptive global 3D printing market. It proved to be astonishingly easy.
What was or is the biggest challenge to be faced?
One thing led to another, really. We have good connections to our supplier who has his own laboratory, we found a plastics processor in Berlin who markets the filament together with ourselves, and the response grew steadily. The biggest challenge seems to be getting people from industry interested, and being able to demonstrate to them that compostability and recycling are possible.
What do you personally find most intriguing about this topic?
I find it just great to learn from nature and then join forces with her and others to create something worthwhile for this and future generations. The Biomimicry Institute, Werner Nachtigall's work on bionics, biology in general and the works of the natural scientist Raoul Francé all fuelled my enthusiasm and gave me that fantastic feeling of making contact with new materials, playing with them, combining them, developing them further and discovering new potential applications.
What are your next targets?
The next thing is to emancipate WilloFlex from the world of 3D printing. We are currently looking at compostable shoes and outdoor clothing. Further ahead, we shall be considering biodegradable hard plastic made of 3D filament and CO2 nanotubes / nanofibres to supplement high-end 3D printer materials.
Interview: Beatrix Boldt