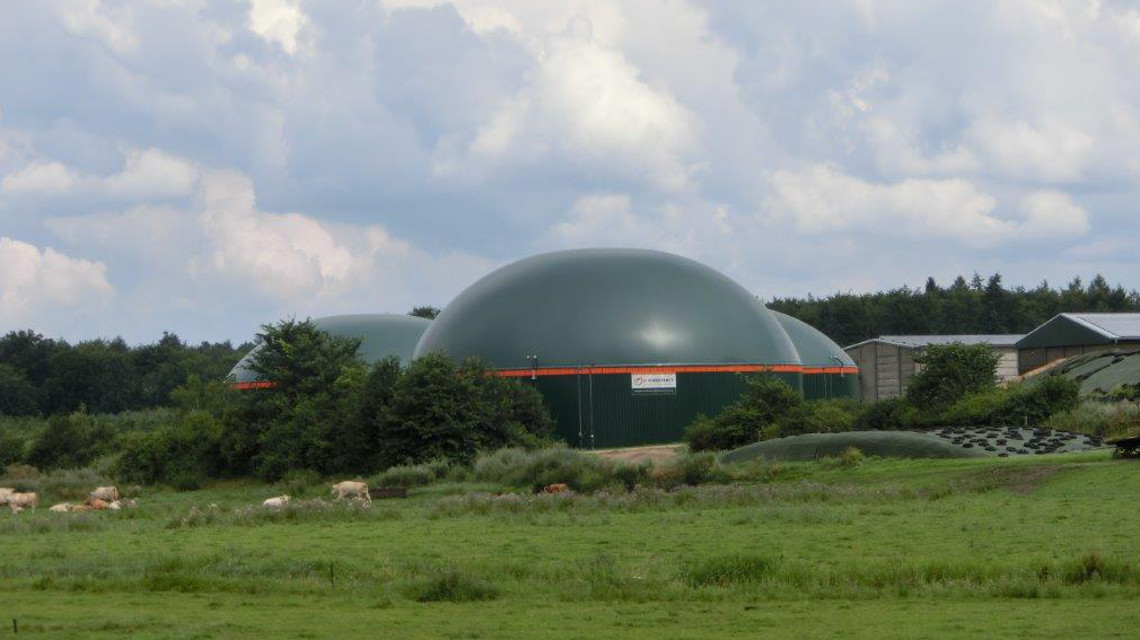
Treibhausgase wie Kohlendioxid (CO2) und Methan (CH4) heizen die Erderwärmung an und sind somit wesentliche Treiber des Klimawandels. Um die Pariser Klimaziele zu erreichen, müssen Emissionen jedoch deutlich reduziert oder im besten Fall vermieden werden. Die Nutzung von Kohlendioxid und Methan als Rohstoff kann dabei einen entscheidenden Beitrag leisten. Hier setzt das Projekt Biogasohol an. Darin wollen Forschende am Leibniz-Institut für Katalyse (LIKAT) in Rostock die beiden Gase aus Biogas in eine wichtige Grundchemikalie, das Synthesegas – ein Gemisch aus Kohlenmonoxid (CO) und Wasserstoff (H2) – umwandeln. Das drei Jahre dauernde Vorhaben wird im Rahmen der Fördermaßnahme „Bioökonomie International“ vom Bundesministerium für Bildung und Forschung (BMBF) bis April 2024 mit rund 518.000 Euro unterstützt. Partner in Vietnam sind an dem Projekt beteiligt.
Neue Katalysatoren und Prozesse für die Synthesegasherstellung
Auch bei der Nutzung nachwachsender Rohstoffe zur Herstellung von Biogas werden klimaschädliche Treibhausgase freigesetzt. Denn Biogas enthält etwa ein Drittel CO2 und zwei Drittel CH4 neben Verunreinigungen – beispielsweise Spurenelemente im Pflanzenmaterial wie Schwefel. Derzeit wird das CO2 in Biogasanlagen abgetrennt und an die Umgebung abgegeben, während Methan in Heizkraftwerken verbrannt wird. Das Team unter Leitung von Udo Armbruster vom LIKAT möchte diese wertvollen Stoffströme in einen geschlossenen Stoffkreislauf zurückführen. Dafür wurden im Projekt neue Katalysatoren und Prozesse etabliert, um Synthesegas herzustellen – und das auf nachhaltige Weise.
Prozess der trockenen Reformierung im Fokus
„Der klassische Weg, Synthesegas aus kohlenstoffhaltigem Material zu erzeugen, besteht darin, es bei sehr hohen Temperaturen mit Wasser zu verdampfen und dann an einem festen Katalysator in Synthesegas umzuwandeln. Das ist jedoch ein energieaufwändiger Prozess“, erläutert Armbruster. Beim herkömmlichen Verfahren der Dampfreformierung werden demnach riesige Mengen Wasser auf extrem hohe Temperaturen von 700 Grad Celsius und mehr erhitzt. Im Rahmen des Projekts wurde daher die Methode der Trockenreformierung bei der Umwandlung von Methan und Kohlendioxid in Synthesegas angewendet. „Bei der trockenen Reformierung ist die Wärmebilanz besser, weil kein Wasser zugeführt wird und auch nur kleine Mengen Wasser im System gebildet werden“, erklärt der Chemiker.
Nickel-Katalysator modifiziert
Die Trockenreformierung läuft zwar bei geringeren, aber dennoch hohen Temperaturen ab und stellt ebenfalls hohe Ansprüche an die im Prozess eingesetzten Materialien. Mit Blick auf eine großtechnische Produktion von Synthesegas aus Biogas musste daher ein geeigneter Katalysator gefunden werden, der unter diesen Temperaturen schnell reagiert und eine hohe Ausbeute ermöglicht. Hier profitierte das Rostocker-Team von der jahrelangen Katalysator-Forschung und konnte einen leistungsfähigen Ersatz für die teuren Edelmetallkatalysatoren etablieren. „Wir haben uns auf Nickel-Katalysatoren fokussiert, weil wir wissen, dass diese unsere Zielreaktion sehr effizient durchführen können. Da man in der Regel einfaches Nickelmetall jedoch nicht nutzen kann, mussten wir noch bestimmte Eigenschaften hinzufügen, damit der Katalysator stabil und aktiv ist“, erklärt Armbruster.
Damit der nickelhaltige Katalysator beim Trockenreformieren funktioniert, musste das Team einige Hürden nehmen. Ein generelles Problem war hierbei die Kohlenstoffbildung, da Nickel sehr schnell und sehr viel Kohlenstoff bindet. Dieser entsteht bei der Trockenreformierung durch die Zersetzung von Methan und Kohlenstoffdioxid. Der Katalysator musste daher so modifiziert werden, dass er so wenig wie möglich Kohlenstoff erzeugt, aber dennoch hochaktiv ist, um Methan und CO2 zu aktivieren. „Durch die Veränderung der Säureeigenschaften wurde der Katalysator basischer, sodass CO2 besonders gut adsorbiert und auch die Kohlenstoffbildung vermieden werden konnte“, berichtet Armbruster.
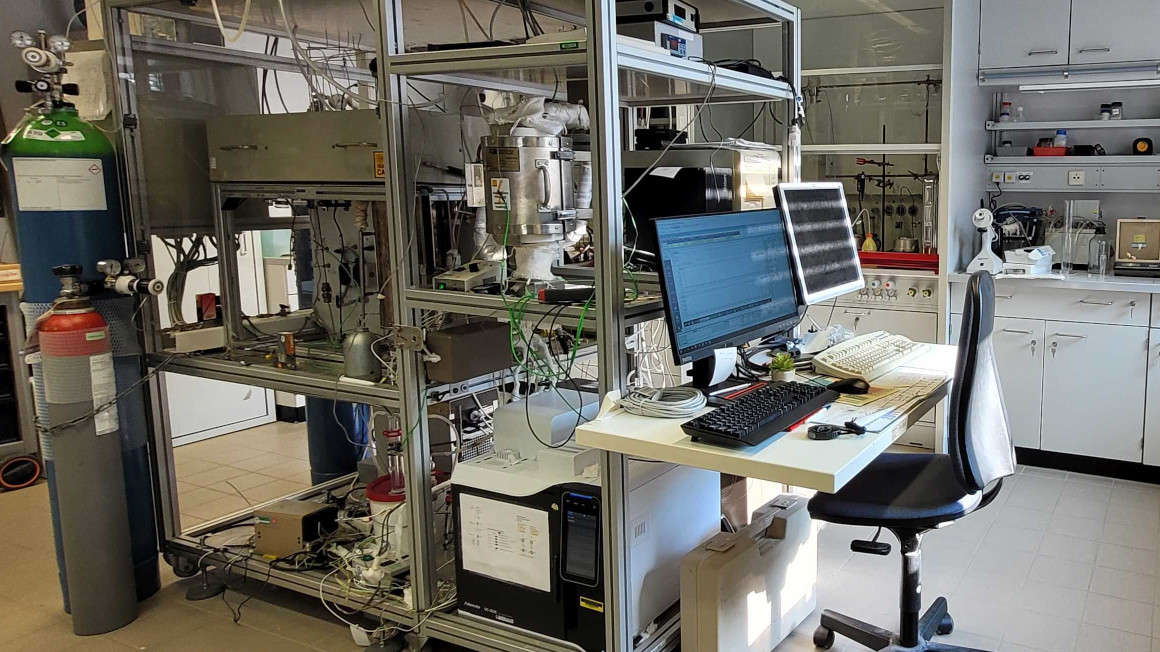
Mit Blick auf eine industrielle Großproduktion werden im Projekt sowohl der Katalysator als auch der Prozess der Trockenreformierung hochskaliert. Hierfür musste unter anderem die Oberfläche des nickelhaltigen Katalysators vergrößert werden. Konkret heißt das: Der pulverförmige Katalysator wurde zu Granulat verarbeitet, das aufgrund seiner porösen Beschaffenheit eine größere Oberfläche bietet. „Das grobkörnige Material hat Zwischenräume zwischen den Körnchen, durch die das Gas hindurchströmen kann. Wir haben jedoch auch schon versucht, das aktive Material auf Monolithen, also Keramikblöcken, aufzubringen“, erklärt Armbruster. Zugleich wurden die Nickelkatalysatoren in Verbindung mit einem Trägermaterial wie Magnesium-Aluminium-Oxid genutzt, das eine größere Oberfläche hat und bei hohen Temperaturen sehr stabil ist.
Nickel-Katalysator kostengünstig und leistungsstark
„Wir sehen ein großes Potenzial in unserem Nickel-Katalysator, da dieser sehr kostengünstig ist. Auch arbeiten wir mit nur 2,5 % Metallgehalt, haben aber eine so hohe Aktivität, dass sie vergleichbar ist mit Katalysatoren, die zehnmal mehr Nickel enthalten. Damit ist der Katalysator sehr leistungsstark und stabil. Wir können in derselben Zeit mehr Einsatzmaterial am Katalysator umsetzen als andere Katalysatoren“, resümiert der Projektleiter.
Umsatz von Synthesegas liegt bei 90 %
Entsprechende Tests im LIKAT-Labor mit simuliertem Biogas zeigen, dass der Nickel-Katalysator beim Trockenreformieren – bei einem Verhältnis von 1:1 für CO2 und CH4 – etwa 90 % zu Synthesegas umsetzt. Noch sind die Arbeiten aber nicht abgeschlossen. Eine Projektverlängerung wurde beantragt. „Als Nächstes wollen wir schauen, wie schnell Störkomponenten wie Ammoniak und Schwefelwasserstoff unsere Katalysatoren vergiften. Wenn das abgeschlossen ist, würden die Partner in Vietnam mit unserem Katalysator in größerem Maßstab weiterarbeiten“, so Armbruster.
Neue Einnahmequelle für Biogasbetreiber
In Vietnam wird die neue Technologie der LIKAT-Forschenden abschließend in einer Pilotanlage mit richtigem Biogas erprobt, und auch die anvisierte Umwandlung von Synthesegas in Methanol realisiert. Zugleich wird auch die gesamte Prozesskette auf ihre Wirtschaftlichkeit bewertet. Armbruster ist überzeugt: Die Umwandlung von Biogas in Synthesegas würde Biogasbetreibern neue Absatz- und Verdienstmöglichkeiten bieten. Hinsichtlich der Weiterverarbeitung zu Methanol könnten demnach dezentrale Anlagen in der Nähe von Biogasanlagen ein Lösungsansatz sein.
Autorin: Beatrix Boldt