Pharmaceuticals
For thousands of years, medicinal herbs have helped to relieve illnesses. Nature, in addition, offers a huge selection of therapeutic agents that serve as basis for advanced medications. Increasingly, biotechnological processes are employed in the production of medication. These biopharmaceuticals have become indispensable in the therapy of widespread diseases such as cancer and diabetes.
FACTS & FIGURES
No. of companies:
1.032 (2014)
643 Pharma (BPI)
389 medical biotechnology (BCG)
Employees:
112.475 (2014)
(Source: BPI)
Sales:
€36,2 billion (2014)
(Source: Pharma Fakten 2014)
Examples of bioeconomy:
Biopharmaceuticals, medicinal plants
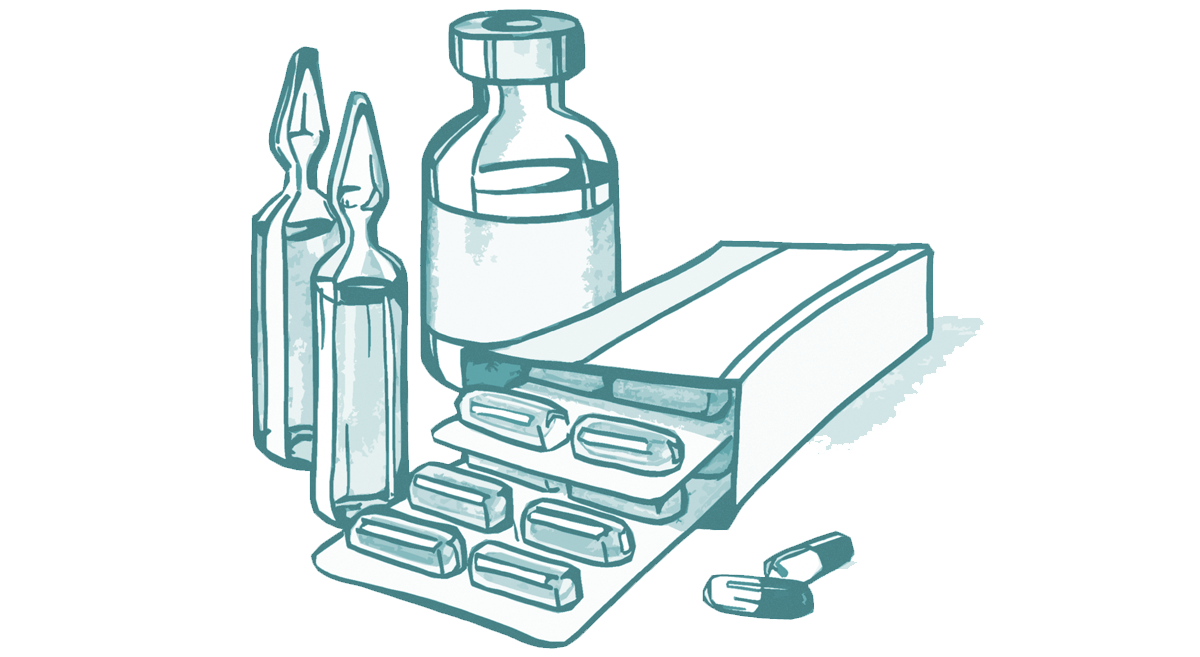
Especially with respect to production of medicinal preparations, pharmaceutical companies are increasingly resorting to biological insights. Although chemically produced medicine still represents the largest share on the German pharma market, so-called biopharmaceuticals are increasingly gaining ground. Their sales of 5.6 billion euros are currently 21% of the market, with a rising trend. These drugs consist of biomolecules that are so large that they cannot be manufactured by man – or only at prohibitive cost. These medications include antibodies against cancer and against auto-immune diseases such as multiple sclerosis, hormones such as insulin for treatment of diabetes and enzymes against metabolic diseases. Techniques from advanced biotechnology developed in the 1980s are applied for their production: living microorganisms and cells can thereby be re-programmed as mini-factories.
The development of biopharmaceuticals began in the late 1970s. US researchers from the company Genetech succeeded in 1978 in isolating for the first time the genetic information for the hormone insulin gained from human cells and in inserting them by gene transfer into bacteria cells. Previously, patients were forced to use insulin from pigs or cattle. Production was not only tedious and expensive, but the therapy was also not tolerated by all patients. Ultimately, the human body reacts against animal hormones as it does against pathogens. In 1979 Frankfurt researchers at the Hoechst pharmaceutical complex likewise developed a biotechnological process for production of human insulin with the aid of genetically modified microorganisms. In 1987 the Eli Lilly pharmaceutical group in Germany obtained licencing for human insulin developed on the basis of the Genentech principle. It was originally produced in Strasbourg, France, and exported to Germany. In 1984 the Hoechst company attempted to obtain a licence for its experimental plant in Frankfurt, but Joschka Fisher, the Environment Minister in the state of Hesse, refused an operating licence. It was only in 1994 that Hoechst obtained the licence, and in 1996 approval followed for production of human insulin. In 1998 biotechnological production officially began. It would not be possible to supply the present number of insulin patients without insulin produced by genetic engineering.
Despite these initial reservations, medication for man and animal manufactured by genetic engineering is generally accepted. Today, more than 200 medications available in Germany are produced in this way. In 2013 an additional 14 were approved – the largest yearly number until then. In addition to the Frankfurt location – which now belongs to the French company Sanofi - the Swiss pharmaceutical group Roche at its plant in Penzberg has implemented comprehensive production capacities for biotech medications. Additional German companies with significant production facilities include Bayer in Leverkusen, Merck in Darmstadt and Boehringer Ingelheim in Biberach. A number of small and medium-sized biotechnology companies have furthermore specialized as service providers to carry out bio-based production, or to support the development and market-dedicated implementation of the relevant processes.
Germany leads European countries in this field. In 2008 the production volume for biopharma was assessed at 675,000 litres. At that point in time, Germany was the second largest producer in the world, after the USA. Several expansion processes have taken place since: Sanofi has continuously expanded its production facilities in Frankfurt, with addition of a cell culture plant for 30 million euros, for production of antibodies used in clinical development. In 2013 Roche in Penzberg announced investment of 280 million euros for further expansion of its pharma plants. The Bayer Group in March of 2014 announced investments of 500 million euros for its complex in Wuppertal, to offer more protein-based drugs for haemophiliacs.
In production of biopharmaceuticals, experts decide between upstream and downstream procedures. For upstream, it is essential to tailor a biological production system – such as microorganisms and mammalian cells – such that the desired proteins are eventually produced. This process must also be designed so that it can take place on an industrial scale in fermenters with capacities of 500 to several thousand litres. In the downstream process, the active substances must be purified to the extent that they are suitable for therapeutic application. This is because the microorganisms or mammalian cells initially create a kind of brew in which – apart from the desired substances – numerous other by-products are contained. Mechanical and thermal techniques such as centrifugation and crystallisation are therefore essential for assuring fast and successful purification.
During recent years, a certain class of biotechnologically produced medicines has especially moved increasingly to the focus of interest: antibodies. A number of white blood cells in the human body produce these molecules. They are seen as tracers and as guided missiles of the human immune system, because each of them bonds to only a certain individual other molecule – the surface protein of a virus, for example, or the toxin from a bacterium. By this bond, an antibody renders its target molecule harmless and prepares its degradation. Since the mid-1970s, processes have been developed by which human antibodies can also be produced with the aid of cell cultures. Today, immune molecules are not only an indispensable medical tool: they also represent an increasingly important medication class. With many diseases such as cancer and autoimmune disorders, they help not only to relieve symptoms, but also to attack the cause of disease – especially by significantly improving the struggle against cancer and autoimmune disease. By now there are more than ten different officially approved antibody-based medications, with many others in advanced stages of development. In Germany, research is taking place for many innovative forms of antibody molecules, in order to further improve their action. Other classes of medication – for example, antibiotics and vaccines – are currently as a rule being produced by biotechnological technologies. Globally, pharma companies produce approximately 4.7 billion vaccine doses (EVM). In Germany, they produce vaccines against influenza and avian flu, tick-borne encephalitis (TBE), diphtheria, whooping cough and rabies – in addition to adjuvants for vaccine production around the world. These companies are continuously expanding their production capacities: the British group GlaxoSmithKline, for example, has invested 100 million euros in production of influenza vaccine in Dresden. In Marburg, Novartis has built an innovative plant for production of flu vaccines and vaccines against TBE and rabies.
Intelligent process control
Intelligent process control is indispensable for producing all these medications in the required amounts. With its technical know-how in bioprocesses, Germany is leading in the world. Work funded by the BMBF is additionally taking place on meeting current and future challenges in this field. These efforts include optimized process control based on intelligent sensor technology. For biotechnologically produced medication, ongoing enhancement of purification processes is a key task – which is why the BMBF has funded further targeted development here. Current research efforts are also focused on effective production organisms. In the initial years of biotechnology – as for insulin – these organisms were initially bacteria; currently, mammalian cells are primarily being used. An example is human cell lines and CHO cells that initially originated from hamsters. In contrast to bacteria, these cells are capable of producing certain molecules that are essential for the efficacy of medications.
Unconventional sources are also being used now as biological producers of medicine. For example, attention has focused on plants that produce innovative active pharmaceutical agents. In 2012 the regulatory agency US Food and Drug Administration (FDA) approved an enzyme produced by carrot cells for treatment of Gaucher’s disease. Work is also being carried out in Germany on such plant-made pharmaceuticals. Scientists at the Fraunhofer Institute for Molecular Biology and Applied Ecology (IME) in Aachen, for example, have succeeded in producing an HIV vaccine in tobacco plants. Bayer, the pharmaceuticals group, is also conducting tests with tobacco plants in special plant facilities and under controlled conditions. This work, based on a process developed by Icon Genetics, a biotech company in Halle, Germany, is intended to enable production by plants of a new vaccine against cancer of the lymph nodes. These plants are by no means found in normal agriculture. Intensive research work here has resulted in the required production and purification processes, and the new active agents must pass clinical studies. On the basis of research work carried out by plant researchers at Freiburg University, the biotech company Greenovation is likewise working on a production method for medicine based on the moss Physcomitrella patens. Plans are for the first active agent to go into clinical testing in 2014.
There are also plants whose constituent substances are interesting as active medicinal agents. The substance paclitaxel, found in the Pacific yew (Taxus brevifolia), for example, is employed as a cancer drug. The restricted habitat of this plant, and its low content of active agent, however, means that it is not possible to meet worldwide demand for this drug by conventional means alone. For some good time, this drug has therefore been partly manufactured synthetically from certain plant/herbal active-agent precursors. In 2002 the British pharma group Bristol-Myers Squibb developed a process for cultivation of isolated yew cells on culture media in fermenters, for the purpose of obtaining this active agent. Biotechnological production takes place in the state of Schleswig-Holstein, in Ahrensburg, at the company Phyton Biotech GmbH, which offers one of the world’s largest fermenter capacities based on plant cells.
In addition to the advanced biotechnological processes that have appreciably improved medical possibilities in recent years, traditional medicinal plants continue to play an important role. Cultivation of medicinal herbs has a long history in Germany. A total of 440 medicinal plants are indigenous to Germany, with about 75 of them commercially cultivated on an area of about 12,000 hectares. Most of this area is in the states of Thuringia, Bavaria, Hesse and Lower Saxony, which together cover more than 70 % of domestic demand for medicinal plants. Chamomile represents the greatest share of all plants cultivated (more than 1,000 hectares), followed by plants such as flax, lady’s thistle, peppermint and buckthorn (each from 500 to 1,000 hectares). Domestic cultivation, however, represents only a niche: 90 % of processed medicinal plants are imported. Medicine from nature enjoys great and growing respect in Germany: in the early 1970s, only 52 % of the population used such products, and in 2002 it had increased to 73 %. The use of natural remedies has proved especially effective in treatment of minor disorders such as colds.
Some medicinal plants today are still harvested in the wild: these especially include plants that are used only in small amounts, or that cannot be cultivated domestically. In comparison to commercial agriculture, however, the quality and the quantitative composition of their constituents fluctuate. As a result, attempts are being made in Germany to cultivate such new or not yet cultivated medicinal plants. These efforts, however, are difficult: for herbs it can take at least five years to render these plants suitable for commercial cultivation, and for trees and shrubs even longer. For this reason, the BMEL funds research work in this field. Throughout Europe, companies established in Germany are market leaders in the production of plant-based drugs. Nevertheless, domestic pharmacy sales of phytopharmaceuticals are declining. With 2012 sales of almost 750 million euros, though, it is still the third-most important sub-segment on the German pharma market. In addition to applications in medicine, medicinal plants are gaining importance for cosmetics and dietary food supplements.
To enable German agriculture to profit more from the market for medicinal plants, the BMEL has funded the demonstration project KAMEL.
The attempt has been made – for example, with chamomile, valerian and melissa – to improve the profitability and the product quality for these species by research and development work and thereby to intensify their cultivation in Germany. Emphasis has been placed on optimization of breeding and on improved drying, cultivation, harvesting and after-crop techniques.
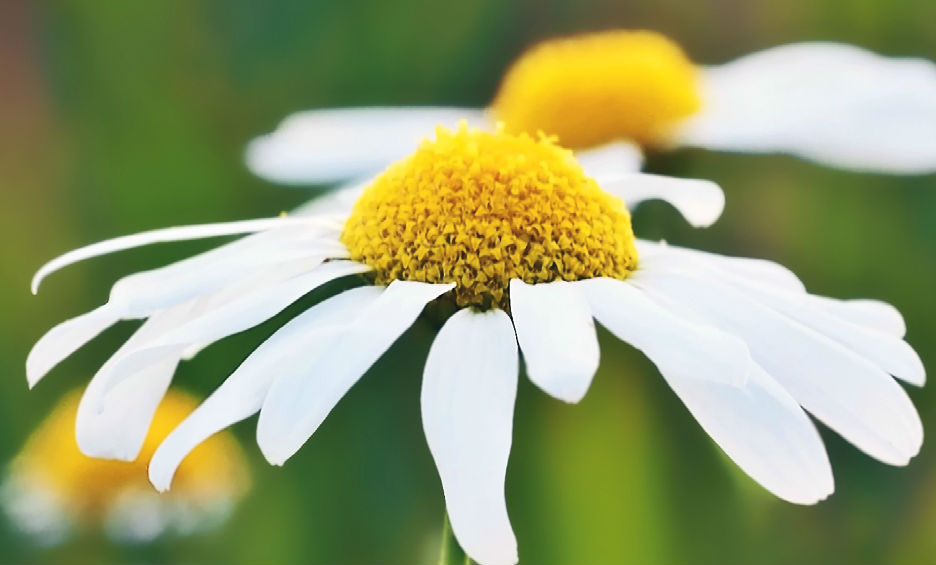